4 Lumber Stacker Operator Interview Questions and Answers
Lumber Stacker Operators are responsible for operating machinery to stack and organize lumber in a safe and efficient manner. They ensure the proper handling and arrangement of lumber for storage or transportation. Junior operators focus on basic machine operation and safety, while senior and lead operators may oversee workflows, troubleshoot equipment issues, and train team members. Supervisory roles involve managing teams and ensuring operational efficiency in lumber stacking processes. Need to practice for an interview? Try our AI interview practice for free then unlock unlimited access for just $9/month.
Unlimited interview practice for $9 / month
Improve your confidence with an AI mock interviewer.
No credit card required
1. Lumber Stacker Operator Interview Questions and Answers
1.1. Can you describe a situation where you had to optimize the stacking process to improve efficiency?
Introduction
This question is important because it assesses your ability to identify inefficiencies and implement improvements, which is crucial in a lumber stacking role to maximize productivity.
How to answer
- Use the STAR method (Situation, Task, Action, Result) to structure your response.
- Clearly explain the specific inefficiencies you noticed in the stacking process.
- Detail the actions you took to resolve these inefficiencies, including any tools or techniques used.
- Discuss the measurable outcomes of your improvements, such as increased output or reduced waste.
- Highlight any collaboration with team members to achieve these improvements.
What not to say
- Avoid vague responses that don't specify the actions taken.
- Refrain from taking sole credit; emphasize teamwork where applicable.
- Don't focus only on the problems without discussing solutions.
- Steer clear of examples that lack measurable results.
Example answer
“In my previous role at a lumber yard, I noticed that our stacking process was slowing down due to inefficient use of space in the warehouse. I analyzed the layout and proposed a new stacking pattern that utilized vertical space better. After implementing this change, we were able to increase our stacking efficiency by 30%, allowing us to process more lumber within the same timeframe. This experience reinforced the value of continuous improvement in operations.”
Skills tested
Question type
1.2. How do you ensure safety while operating stacking machinery?
Introduction
This question evaluates your understanding of safety protocols and your commitment to maintaining a safe working environment, which is critical in any industrial role.
How to answer
- Detail the safety procedures you follow when operating machinery.
- Mention any training or certifications you have related to safety.
- Discuss how you stay vigilant and aware of your surroundings while working.
- Explain how you promote safety among your colleagues.
- Describe any past incidents and how you learned from them to improve safety practices.
What not to say
- Avoid suggesting that safety procedures are optional.
- Refrain from dismissing the importance of safety training.
- Don't provide examples that indicate negligence or lack of awareness.
- Steer clear of blaming others for safety incidents without taking responsibility.
Example answer
“I prioritize safety by strictly adhering to the safety protocols outlined during my training. I always conduct a pre-operation safety check on the machinery and wear the necessary protective gear. Additionally, I remind my colleagues to stay alert and report any unsafe conditions immediately. After witnessing a minor incident due to equipment malfunction, I advocated for regular maintenance checks, which significantly reduced risks in our operations. Safety is a collective responsibility, and I take it very seriously.”
Skills tested
Question type
2. Senior Lumber Stacker Operator Interview Questions and Answers
2.1. Can you describe a time when you had to manage multiple tasks on the production line? How did you ensure efficiency?
Introduction
This question assesses your ability to multitask and manage workflow, which is crucial in a fast-paced lumber stacking environment.
How to answer
- Use the STAR method to structure your answer: Situation, Task, Action, Result.
- Clearly explain the context of the production line scenario.
- Detail the specific tasks you had to manage and why they were important.
- Explain the actions you took to prioritize and delegate tasks if necessary.
- Quantify the results in terms of productivity or efficiency improvements.
What not to say
- Claiming you can handle everything alone without teamwork.
- Failing to provide concrete examples or metrics.
- Downplaying the importance of efficiency in the production process.
- Neglecting to mention any challenges faced during multitasking.
Example answer
“At Boral, during a peak production period, we faced delays due to equipment maintenance. I coordinated with the maintenance team while simultaneously managing stackers and loaders. I prioritized the most critical tasks, ensuring that we met our daily quota. As a result, we maintained a 95% efficiency rate despite the challenges, and my proactive approach helped prevent further delays.”
Skills tested
Question type
2.2. What safety protocols do you follow while operating machinery, and how do you ensure team compliance?
Introduction
Safety is paramount in any industrial setting, especially when operating heavy machinery. This question evaluates your knowledge of safety protocols and your leadership in enforcing them.
How to answer
- List specific safety protocols you are familiar with in lumber stacking.
- Explain how you personally adhere to these protocols while operating.
- Describe how you communicate the importance of safety to your team.
- Provide an example of how you handled a safety issue or ensured compliance among team members.
- Mention any training or certifications you have related to safety.
What not to say
- Indicating that safety protocols are not a priority.
- Failing to mention any specific protocols or training.
- Not having examples of enforcing safety measures.
- Suggesting that safety compliance is solely the responsibility of supervisors.
Example answer
“I strictly follow the Work Health and Safety (WHS) protocols while operating stackers. I always wear the appropriate PPE and conduct a pre-operation inspection of the machinery. I emphasize safety during team meetings, encouraging my colleagues to report any hazards. Last year, I noticed a team member not wearing their safety goggles; I addressed it immediately and organized a refresher training on safety protocols. This proactive approach has led to zero accidents on my watch over the past year.”
Skills tested
Question type
3. Lead Lumber Stacker Operator Interview Questions and Answers
3.1. Can you describe a time when you had to address a safety concern in the lumber stacking process?
Introduction
This question is important as it assesses your commitment to safety protocols, which is crucial in a role that operates heavy machinery and deals with potentially hazardous materials.
How to answer
- Use the STAR method: describe the Situation, Task, Action, and Result
- Clearly outline the safety concern and its potential implications
- Explain the steps you took to address the concern, including communication with your team
- Highlight the outcome, focusing on improved safety or efficiency
- Emphasize your understanding of safety regulations and protocols
What not to say
- Downplaying the importance of safety measures
- Providing vague examples without clear actions or results
- Avoiding responsibility or blaming others for safety issues
- Failing to show proactive behavior in identifying concerns
Example answer
“At a previous job in a lumber mill, I noticed that some stacks were unstable, posing a risk during transport. I immediately identified the issue, gathered the team, and we implemented stricter stacking protocols and regular inspections. As a result, we reduced accidents related to falling stacks by 60% within three months, reinforcing a culture of safety.”
Skills tested
Question type
3.2. What strategies do you utilize to ensure efficiency while operating the lumber stacking machinery?
Introduction
This question evaluates your operational knowledge and ability to maximize productivity without compromising quality and safety.
How to answer
- Discuss specific techniques or processes you have implemented in your previous roles
- Explain how you monitor performance and identify areas for improvement
- Mention any tools or technologies you leverage to enhance efficiency
- Include examples of how you have trained or motivated your team to be more efficient
- Share any metrics or results that demonstrate your impact on efficiency
What not to say
- Suggesting that speed is more important than quality or safety
- Failing to mention teamwork or collaboration
- Providing generic answers without specific examples
- Neglecting to acknowledge the importance of maintenance and care for machinery
Example answer
“I focus on continuous improvement by regularly reviewing our stacking processes and implementing lean principles. For instance, at my last job, I introduced a pre-shift checklist to ensure equipment was in optimal condition, which improved our stacking speed by 15% while maintaining quality. I also encouraged team input for innovative ideas, which fostered a culture of efficiency.”
Skills tested
Question type
4. Lumber Operations Supervisor Interview Questions and Answers
4.1. Can you describe a time when you successfully improved operational efficiency in a lumber processing facility?
Introduction
This question is crucial for understanding your ability to identify inefficiencies and implement solutions that enhance productivity, which is vital in the lumber industry.
How to answer
- Use the STAR method to structure your response: Situation, Task, Action, Result.
- Clearly define the operational challenge you faced.
- Explain the steps you took to analyze the situation and develop a solution.
- Discuss how you engaged your team and gained their support.
- Quantify the results of your actions, such as increased output or reduced waste.
What not to say
- Focusing solely on technical aspects without mentioning team involvement.
- Neglecting to provide specific metrics or outcomes.
- Blaming others for inefficiencies without explaining your role in the solution.
- Vague descriptions that lack clarity on the actions taken.
Example answer
“At a previous job with a lumber mill in São Paulo, we faced significant delays due to outdated machinery. I initiated a project to assess our equipment and proposed a phased upgrade. By securing buy-in from my team and collaborating with maintenance, we reduced processing time by 30% and increased our output by 20% over six months. This experience taught me the importance of blending technical upgrades with team engagement.”
Skills tested
Question type
4.2. How do you ensure compliance with safety regulations in lumber operations?
Introduction
Safety is paramount in the lumber industry. This question assesses your knowledge of safety protocols and your commitment to maintaining a safe work environment.
How to answer
- Discuss your familiarity with local and international safety regulations.
- Explain how you conduct training sessions and safety drills.
- Describe your approach to monitoring compliance and addressing violations.
- Mention any experience with safety audits or incident reporting.
- Highlight the importance of fostering a safety-first culture among employees.
What not to say
- Suggesting that safety regulations are optional or can be overlooked.
- Failing to mention specific safety training or protocols.
- Not acknowledging the role of employee feedback in safety improvements.
- Being unaware of recent changes in safety legislation.
Example answer
“In my previous role, I led quarterly safety training sessions to educate our staff about compliance with Brazilian safety regulations. I implemented a system for reporting safety hazards anonymously, which increased our incident reporting by 40% and helped us address potential issues proactively. By fostering a culture of safety, we achieved a record year with zero workplace accidents.”
Skills tested
Question type
Similar Interview Questions and Sample Answers
Simple pricing, powerful features
Upgrade to Himalayas Plus and turbocharge your job search.
Himalayas
Himalayas Plus
Himalayas Max
Find your dream job
Sign up now and join over 100,000 remote workers who receive personalized job alerts, curated job matches, and more for free!
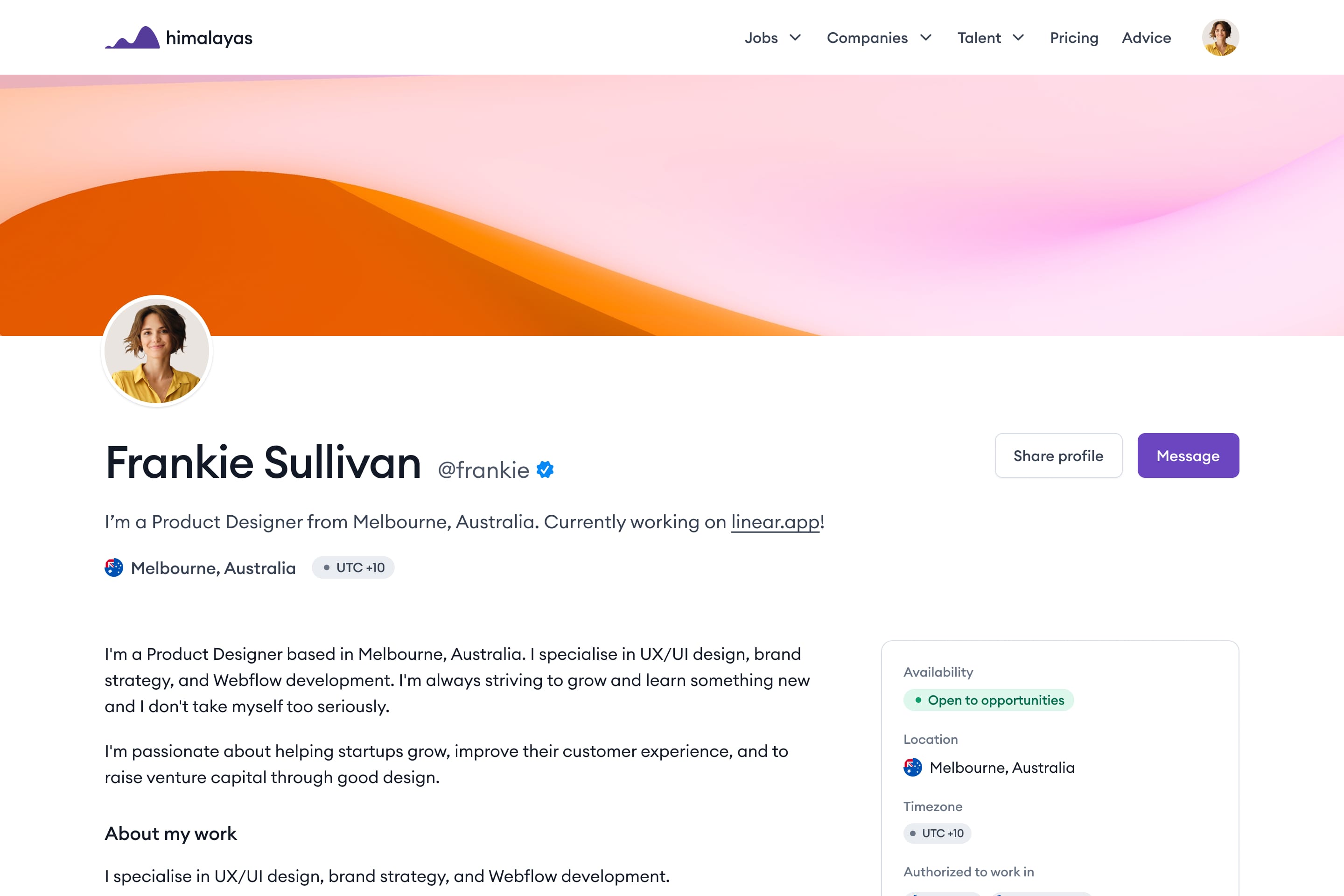