3 Log Peeler Interview Questions and Answers
Log Peelers are responsible for manually or mechanically removing bark from logs in preparation for further processing in industries such as lumber or paper production. They ensure the logs are properly prepared for downstream operations. Junior roles focus on basic peeling tasks, while senior and lead roles may involve overseeing teams, maintaining equipment, and ensuring quality standards are met. Need to practice for an interview? Try our AI interview practice for free then unlock unlimited access for just $9/month.
Unlimited interview practice for $9 / month
Improve your confidence with an AI mock interviewer.
No credit card required
1. Log Peeler Interview Questions and Answers
1.1. Can you walk us through your experience with different types of logs and their peeling requirements?
Introduction
This question is crucial for understanding your technical knowledge and practical experience in log peeling, which is essential for the quality of the final product.
How to answer
- Describe the types of logs you have worked with and their specific characteristics.
- Explain the peeling techniques you've used for each type of log.
- Share any challenges you faced and how you overcame them.
- Mention any specific machinery or tools you are proficient with.
- Highlight the importance of quality control in the peeling process.
What not to say
- Generalizing your experience without specific examples.
- Failing to mention the importance of safety protocols.
- Neglecting to discuss quality assurance measures.
- Overlooking the environmental impact of log peeling.
Example answer
“In my previous role at a timber processing company in Singapore, I worked with various types of logs, including Teak and Mahogany. Each required different peeling techniques; for instance, I used a lathe for Teak to minimize waste. I faced challenges with log defects, which I addressed by adjusting the peeling angle to ensure uniformity. Understanding these nuances has been vital for maintaining our quality standards.”
Skills tested
Question type
1.2. Describe a situation where you had to ensure safety compliance while operating peeling machinery.
Introduction
This question assesses your understanding of safety regulations and your ability to implement them in the workplace, which is critical in any manufacturing role.
How to answer
- Use the STAR method to structure your response.
- Explain the safety compliance standards relevant to log peeling.
- Detail a specific incident where you ensured compliance.
- Discuss the steps you took to educate others on safety protocols.
- Highlight the positive outcomes of maintaining a safe work environment.
What not to say
- Downplaying the importance of safety protocols.
- Not providing a specific example.
- Failing to mention any collaboration with safety officers.
- Ignoring the consequences of non-compliance.
Example answer
“At my last job, we had a safety audit that revealed potential risks with our peeling machines. I took the initiative to implement a checklist for daily safety inspections and organized training sessions for the team on proper operating procedures. As a result, we achieved a 30% reduction in safety incidents over six months, creating a safer work environment for everyone.”
Skills tested
Question type
1.3. How do you handle tight production schedules while maintaining quality in log peeling?
Introduction
This question helps evaluate your time management skills and your ability to balance efficiency with quality control, which is vital in a production setting.
How to answer
- Describe your approach to planning and prioritizing tasks.
- Explain how you monitor production progress and quality.
- Share specific strategies you employ to maintain high standards despite time pressures.
- Discuss any tools or techniques you use for tracking production metrics.
- Highlight the importance of communication with your team during busy periods.
What not to say
- Suggesting that speed is more important than quality.
- Not providing concrete examples of how you manage production.
- Failing to mention teamwork or collaboration.
- Overlooking the role of feedback in improving processes.
Example answer
“In a previous role, we often faced tight production deadlines. I implemented a daily goals system that allowed us to track our progress against targets while ensuring quality checks at every stage. For example, I introduced peer reviews for the peeling process, which helped catch issues early. This approach not only kept us on schedule but also improved our quality metrics significantly.”
Skills tested
Question type
2. Senior Log Peeler Interview Questions and Answers
2.1. Can you describe a time when you had to deal with a challenging log peeling project? What steps did you take to ensure success?
Introduction
This question is important as it evaluates your problem-solving skills and ability to handle challenges specific to log peeling, which is crucial for maintaining production efficiency.
How to answer
- Use the STAR method (Situation, Task, Action, Result) to structure your response.
- Clearly outline the specific challenge you faced, such as equipment failure or poor log quality.
- Detail the actions you took to address the issue, including any adjustments to techniques or processes.
- Highlight the results of your efforts with specific metrics, like improved yield or reduced waste.
- Reflect on what you learned from the experience and how it can apply to future projects.
What not to say
- Focusing solely on the problem without discussing your role in the solution.
- Avoiding specifics, such as metrics or outcomes.
- Claiming to have never faced challenges in log peeling.
- Not acknowledging the team’s effort if applicable.
Example answer
“In my previous role at Holzwerkstatt GmbH, we faced a significant challenge when a batch of logs arrived with unexpected defects. I quickly assessed the situation and implemented a new peeling technique that minimized waste. By adjusting our approach, we managed to maintain a 95% yield, which ultimately saved us about 10% in costs for that project. This experience taught me the importance of adaptability and thorough quality checks.”
Skills tested
Question type
2.2. What safety protocols do you follow while operating peeling equipment, and how do you ensure compliance within your team?
Introduction
This question assesses your knowledge of safety practices and your leadership in maintaining a safe work environment, which is critical in log peeling operations.
How to answer
- Start by mentioning specific safety protocols relevant to log peeling equipment.
- Discuss how you personally adhere to these protocols in your work.
- Explain how you communicate and enforce safety standards within your team.
- Provide examples of training or safety meetings you've conducted.
- Highlight the importance of safety in preventing accidents and ensuring operational efficiency.
What not to say
- Neglecting to mention specific safety protocols.
- Claiming you don’t worry about safety because you are experienced.
- Failing to explain how you ensure team compliance.
- Downplaying the importance of safety in the workplace.
Example answer
“I strictly follow safety protocols such as wearing personal protective equipment (PPE) and conducting regular equipment checks. I ensure compliance by leading weekly safety briefings and encouraging my team to report any potential hazards. For instance, after noticing some wear on a peeling machine, I organized an inspection that prevented a possible accident, reinforcing a culture of safety first among my colleagues.”
Skills tested
Question type
3. Lead Log Peeler Interview Questions and Answers
3.1. Can you describe a time when you had to troubleshoot a mechanical issue with the peeling equipment?
Introduction
This question assesses your technical skills and problem-solving ability, which are critical for a lead log peeler responsible for maintaining equipment functionality.
How to answer
- Use the STAR method to structure your response: Situation, Task, Action, Result.
- Clearly describe the mechanical issue you encountered and its implications on production.
- Explain the steps you took to diagnose and resolve the issue.
- Highlight any tools or techniques you used in the troubleshooting process.
- Share the outcome and any improvements made to prevent future issues.
What not to say
- Avoid generalizations without specific examples.
- Do not focus solely on the technical details without explaining your thought process.
- Steering clear of blaming others for equipment failure.
- Neglecting to discuss the impact of the issue on operations.
Example answer
“At my previous job with a local timber company, I encountered a malfunction in the log peeling machine that was causing inconsistencies in the peeling quality. I assessed the situation and identified a worn belt that was affecting the feed rate. I replaced the belt and recalibrated the machine, which restored its efficiency. As a result, we increased our output by 20% and minimized waste, reinforcing the importance of regular maintenance checks.”
Skills tested
Question type
3.2. How do you ensure safety and compliance in the log peeling process?
Introduction
This question evaluates your understanding of safety protocols and your ability to lead a team in maintaining a safe work environment, critical for a lead position.
How to answer
- Discuss specific safety regulations relevant to the log peeling industry.
- Describe your approach to training team members on safety practices.
- Explain how you conduct regular safety audits and assessments.
- Share examples of how you've implemented safety improvements.
- Highlight the importance of a safety-first culture within your team.
What not to say
- Avoid vague statements about safety without specific examples.
- Do not imply that safety regulations are optional.
- Steering clear of mentioning safety only after an incident occurs.
- Neglecting to discuss the role of teamwork in maintaining safety.
Example answer
“In my role at a wood processing facility, I prioritized safety by regularly conducting training sessions on equipment operation and emergency procedures. I implemented a safety audit system that involved weekly checks and feedback from team members. This proactive approach led to a 30% reduction in workplace incidents. I believe fostering a culture where safety is everyone's responsibility is key to our success.”
Skills tested
Question type
3.3. What strategies do you use to optimize the efficiency of the peeling process?
Introduction
This question assesses your ability to improve production processes and implement best practices, crucial for maximizing output and reducing waste.
How to answer
- Discuss methods for monitoring and analyzing production metrics.
- Explain how you identify bottlenecks and areas for improvement.
- Describe any tools or technologies you use for process optimization.
- Share examples of successful process changes you've implemented.
- Emphasize the importance of continuous improvement and team involvement.
What not to say
- Avoid generic statements about wanting to improve efficiency without specifics.
- Do not ignore the role of the team in process optimization.
- Steering clear of suggesting changes without data to support them.
- Neglecting to mention the balance between efficiency and quality.
Example answer
“At my previous position with a timber processing company, I used data analytics to track our peeling rates and identified that a particular machine was underperforming due to idle time. I coordinated with the maintenance team to ensure timely repairs and trained operators on optimal machine use. After implementing these changes, we improved our peeling efficiency by 25%, significantly reducing our overhead costs.”
Skills tested
Question type
Similar Interview Questions and Sample Answers
Simple pricing, powerful features
Upgrade to Himalayas Plus and turbocharge your job search.
Himalayas
Himalayas Plus
Himalayas Max
Find your dream job
Sign up now and join over 100,000 remote workers who receive personalized job alerts, curated job matches, and more for free!
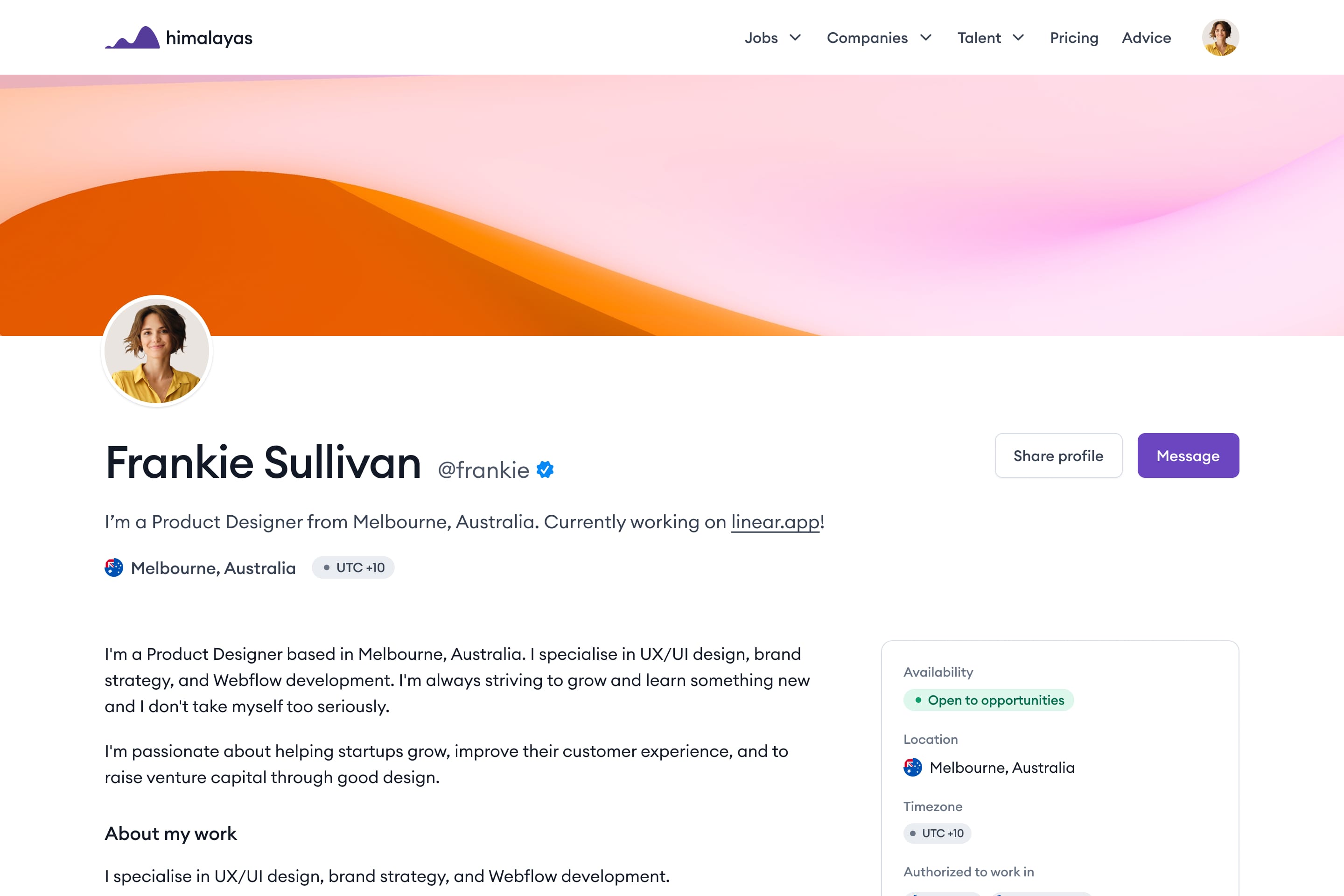