7 Industrial Maintenance Mechanic Interview Questions and Answers
Industrial Maintenance Mechanics are responsible for ensuring the proper functioning of machinery and equipment in industrial settings. They perform routine maintenance, troubleshoot issues, and repair or replace defective components to minimize downtime. Junior mechanics focus on learning and assisting with basic tasks, while senior mechanics handle complex repairs, mentor junior staff, and may oversee maintenance operations. At higher levels, such as supervisors or managers, responsibilities expand to include planning maintenance schedules, managing teams, and ensuring compliance with safety and operational standards. Need to practice for an interview? Try our AI interview practice for free then unlock unlimited access for just $9/month.
Unlimited interview practice for $9 / month
Improve your confidence with an AI mock interviewer.
No credit card required
1. Apprentice Industrial Maintenance Mechanic Interview Questions and Answers
1.1. Can you describe a time when you identified a mechanical issue before it became a serious problem?
Introduction
This question assesses your ability to recognize and address mechanical issues proactively, which is critical in industrial maintenance to prevent costly downtime.
How to answer
- Use the STAR method to structure your response
- Clearly outline the situation and the mechanical issue you encountered
- Explain the steps you took to identify the problem and your thought process
- Detail the actions you implemented to resolve the issue
- Highlight the outcome and how it benefited the team or company
What not to say
- Failing to provide a specific example and speaking in generalities
- Not emphasizing your proactive approach
- Focusing only on the problem without discussing your solution
- Neglecting to mention the positive impact of your actions
Example answer
“During my internship at a manufacturing plant, I noticed unusual vibrations coming from a conveyor belt. I initiated a quick inspection and discovered a misalignment in the bearings. I reported it to my supervisor and, with her permission, adjusted the alignment. This proactive measure prevented a potential breakdown and saved the company from losing several hours of production time.”
Skills tested
Question type
1.2. How do you prioritize tasks when faced with multiple maintenance requests?
Introduction
This question evaluates your time management and organizational skills, which are vital for maintaining efficiency in an industrial environment.
How to answer
- Explain your approach to assessing the urgency and impact of each request
- Discuss how you would communicate with team members or supervisors for prioritization
- Mention any tools or methods you use for task management
- Provide an example of how you successfully managed multiple requests in the past
- Highlight the importance of flexibility and adaptability in your approach
What not to say
- Indicating that you would handle tasks in a random order
- Failing to acknowledge the importance of communication with others
- Not providing a structured method for prioritization
- Ignoring the need for adaptability in a fast-paced environment
Example answer
“When faced with multiple maintenance requests, I first assess each one for urgency and potential impact on production. For instance, if a machine is down, that takes priority over routine maintenance. I often use a simple checklist to track requests and their status, which I share with my team to keep everyone informed. In my last role, this method helped us reduce response time by 30% while ensuring critical issues were addressed promptly.”
Skills tested
Question type
2. Junior Industrial Maintenance Mechanic Interview Questions and Answers
2.1. Can you describe a time when you had to troubleshoot a malfunctioning piece of machinery?
Introduction
This question assesses your problem-solving skills and technical knowledge, which are crucial for a Junior Industrial Maintenance Mechanic.
How to answer
- Use the STAR method to structure your response (Situation, Task, Action, Result)
- Clearly describe the machinery involved and the specific malfunction
- Detail the steps you took to diagnose the issue
- Explain how you resolved the problem and any tools or techniques used
- Share the outcome and any lessons learned from the experience
What not to say
- Providing vague details without specifying the machinery or the problem
- Neglecting to mention how you diagnosed the issue
- Taking sole credit without acknowledging team support or resources
- Failing to discuss what you learned from the troubleshooting process
Example answer
“During my internship at a manufacturing facility, I encountered a conveyor belt that had stopped working. I identified the issue by checking the electrical connections and found a blown fuse. After replacing the fuse, I tested the system and ensured it was functioning properly. This experience taught me the importance of thorough diagnostics and attention to detail.”
Skills tested
Question type
2.2. How do you prioritize maintenance tasks when you have multiple issues reported?
Introduction
This question evaluates your time management and organizational skills, essential for managing the workload of a Junior Industrial Maintenance Mechanic.
How to answer
- Describe your approach to assessing the urgency and impact of each issue
- Explain how you communicate with your team or supervisor to prioritize tasks
- Mention any tools or systems you use for task management
- Highlight the importance of safety and minimizing downtime in your prioritization
- Provide an example of a situation where you successfully prioritized tasks
What not to say
- Suggesting that all tasks are equally important without differentiation
- Ignoring the importance of communication with your team
- Failing to mention safety considerations
- Giving a generic answer without a specific example
Example answer
“If multiple machinery issues arise, I first assess each problem's urgency based on its impact on production. For instance, if a critical machine fails, I prioritize that over less urgent tasks. I communicate with my supervisor and document tasks using a maintenance log. This approach was effective when I managed several repairs during a shift, ensuring minimal downtime by addressing the most critical issues first.”
Skills tested
Question type
3. Industrial Maintenance Mechanic Interview Questions and Answers
3.1. Can you describe a time when you diagnosed and fixed a malfunctioning machine? What steps did you take?
Introduction
This question evaluates your technical problem-solving skills and ability to work under pressure, which are crucial for an Industrial Maintenance Mechanic.
How to answer
- Use the STAR method to structure your response (Situation, Task, Action, Result)
- Begin with a brief description of the malfunction and its impact on production
- Detail the diagnostic procedures you used to identify the issue
- Explain the repair process, including any tools or techniques used
- Quantify the results, such as reduced downtime or increased efficiency
What not to say
- Vague descriptions that lack specific details about the problem or solution
- Failing to mention the impact of the malfunction on operations
- Taking sole credit without acknowledging teamwork or collaboration
- Neglecting to discuss safety protocols followed during repairs
Example answer
“At a manufacturing plant in Lyon, I encountered a conveyor belt that had stopped working. After assessing the situation, I conducted a thorough diagnostic check, identifying a faulty motor. I swiftly replaced the motor and recalibrated the system, which restored operations within two hours. This repair minimized downtime and prevented a potential backlog in production.”
Skills tested
Question type
3.2. How do you prioritize maintenance tasks when you’re faced with multiple urgent issues?
Introduction
This question assesses your time management skills and ability to prioritize tasks effectively, which is essential in a maintenance role.
How to answer
- Outline your approach to assessing urgency and impact of each task
- Discuss any tools or methods you use to keep track of maintenance schedules
- Explain how you communicate with your team and management about priorities
- Share an example of a time you effectively managed multiple urgent tasks
- Mention any safety considerations that influence your prioritization
What not to say
- Indicating that you handle tasks in a random order without a method
- Failing to consider the importance of communication with the team
- Neglecting to discuss the impact of unresolved issues on operations
- Suggesting that you would prioritize personal preferences over business needs
Example answer
“When faced with multiple urgent tasks, I first assess each issue's impact on production. For example, if a major machine is down, I prioritize that over less critical tasks. I use a maintenance management system to track issues and communicate with my team about our priorities. Once, during a shift, the packaging machine broke down while we had several minor issues. I coordinated with the team to resolve the packaging issue first, which allowed us to avoid production delays and meet our shipping deadlines.”
Skills tested
Question type
4. Senior Industrial Maintenance Mechanic Interview Questions and Answers
4.1. Can you describe a time when you diagnosed and repaired a complex mechanical failure in a production line?
Introduction
This question is crucial for assessing your technical troubleshooting skills and ability to perform under pressure, which are essential for a Senior Industrial Maintenance Mechanic.
How to answer
- Use the STAR method to structure your response: Situation, Task, Action, Result.
- Clearly describe the mechanical failure and its impact on production.
- Detail the diagnostic process you followed, including tools and techniques used.
- Explain the repair process and any challenges faced during the repair.
- Quantify the results to show the impact of your work on production efficiency.
What not to say
- Providing vague descriptions of the problem without specific details.
- Failing to mention the tools or methods used during diagnosis.
- Not discussing the outcome or improvements made post-repair.
- Taking sole credit without acknowledging any teamwork or collaboration.
Example answer
“At a beverage manufacturing plant, we faced a significant bottleneck due to a malfunctioning conveyor system. I diagnosed the issue as a misalignment in the drive motor, which was causing frequent shutdowns. By utilizing laser alignment tools and adjusting the motor placement, I resolved the issue within three hours. This not only minimized downtime by 30% but also improved our overall throughput by 15%. This experience underscored the importance of precise diagnostics and quick action in maintenance roles.”
Skills tested
Question type
4.2. How do you prioritize maintenance tasks when faced with multiple urgent issues in a plant?
Introduction
This question evaluates your prioritization and time management skills, which are vital for maintaining operational continuity in industrial settings.
How to answer
- Explain your approach to assessing the urgency and impact of each issue.
- Discuss how you communicate with team members and management to align priorities.
- Describe any tools or systems you use for tracking tasks and deadlines.
- Mention any criteria you consider for prioritizing maintenance tasks.
- Provide an example of a time when your prioritization led to successful outcomes.
What not to say
- Suggesting that all tasks are equally urgent without justification.
- Failing to involve team members in the prioritization process.
- Neglecting to mention any follow-up or review mechanisms.
- Describing a chaotic approach without structured criteria.
Example answer
“When faced with multiple urgent maintenance issues, I first assess the impact on production and safety. For instance, if a critical machine is down, I prioritize that over less urgent repairs. I use a digital task management system to track and communicate priorities with my team. Last year, when we had simultaneous failures in two different processes, I coordinated with my team to address the safety issue first, which prevented further complications and allowed us to restore operations swiftly. This structured approach has consistently helped reduce downtime.”
Skills tested
Question type
5. Lead Industrial Maintenance Mechanic Interview Questions and Answers
5.1. Can you describe a time when you diagnosed a complex mechanical failure? What steps did you take to resolve it?
Introduction
This question is crucial for assessing your technical expertise and problem-solving abilities as a Lead Industrial Maintenance Mechanic, where diagnosing and resolving issues quickly is essential to minimize downtime.
How to answer
- Begin by outlining the context of the mechanical failure, including the machinery involved and its importance to operations.
- Detail the diagnostic process you followed, including any tools or techniques used.
- Explain the steps you took to resolve the issue, emphasizing your hands-on skills and teamwork if applicable.
- Discuss any challenges you faced during the resolution process and how you overcame them.
- Conclude with the impact of your actions on production efficiency and any lessons learned.
What not to say
- Failing to provide specifics about the machinery or the failure.
- Only focusing on technical details without mentioning the diagnostic process.
- Taking sole credit for team efforts without acknowledging collaboration.
- Overlooking the importance of safety considerations in the repair process.
Example answer
“At a manufacturing facility in Singapore, we experienced unexpected downtime due to a malfunction in a critical conveyor system. I led the diagnostic effort, using vibration analysis tools to pinpoint a bearing failure. Collaborating with my team, we replaced the bearings and recalibrated the system within 48 hours, resulting in a 20% increase in throughput. This situation reinforced the need for thorough inspections and preventive maintenance, which I later integrated into our routine checks.”
Skills tested
Question type
5.2. How do you prioritize maintenance tasks in a fast-paced industrial environment?
Introduction
This question evaluates your organizational and time management skills, essential for a Lead Industrial Maintenance Mechanic who needs to balance multiple tasks while ensuring operational efficiency.
How to answer
- Explain your prioritization framework, considering factors like safety, production impact, and equipment criticality.
- Share examples of how you assess and categorize tasks based on urgency and importance.
- Discuss how you communicate priorities with your team and manage stakeholder expectations.
- Highlight any software tools or systems you use to track maintenance activities.
- Describe how you adapt to changes in priorities based on new developments or emergencies.
What not to say
- Providing a vague answer without a clear prioritization method.
- Ignoring the importance of safety in task prioritization.
- Failing to mention communication with the team regarding priorities.
- Suggesting that all tasks are equally important.
Example answer
“In my previous role at a semiconductor manufacturing plant, I used a risk-based approach to prioritize maintenance tasks. Critical equipment failures that could halt production were always addressed first, followed by routine maintenance tasks. I implemented a maintenance management system that allowed us to track progress and communicate priorities effectively. This approach reduced unplanned downtime by 30% over six months.”
Skills tested
Question type
6. Maintenance Supervisor Interview Questions and Answers
6.1. Can you describe a time when you had to handle a major equipment failure? What steps did you take to resolve the issue?
Introduction
This question is crucial for a Maintenance Supervisor as it assesses your problem-solving skills and your ability to manage high-pressure situations effectively.
How to answer
- Use the STAR method to clearly outline the Situation, Task, Action, and Result.
- Describe the specific equipment failure and its impact on operations.
- Detail the steps you took to diagnose the issue and implement a solution.
- Highlight any collaboration with your team and other departments.
- Conclude with the outcome and any improvements made to prevent future occurrences.
What not to say
- Blaming team members or external factors without taking personal responsibility.
- Providing vague answers without specific details on actions taken.
- Failing to mention the impact of the issue on safety or productivity.
- Not discussing any lessons learned from the experience.
Example answer
“At Tata Motors, we faced a sudden breakdown of a critical assembly line machine, halting production. I quickly assembled a cross-functional team to diagnose the issue. We identified a malfunctioning sensor and worked collaboratively to replace it. I communicated regularly with the production team about timelines and expectations. Ultimately, we restored operations within four hours, minimizing downtime and reinforcing our preventive maintenance schedule to avoid future breakdowns.”
Skills tested
Question type
6.2. How do you ensure compliance with safety regulations in your maintenance practices?
Introduction
Safety is paramount in maintenance operations. This question evaluates your understanding of safety protocols and your commitment to maintaining a safe work environment.
How to answer
- Discuss your knowledge of relevant safety regulations and standards.
- Explain how you implement these regulations in daily maintenance tasks.
- Share examples of safety training programs you conduct for staff.
- Highlight any past experiences where you improved safety compliance.
- Mention how you monitor and report safety performance metrics.
What not to say
- Indicating that safety regulations are not a priority in maintenance.
- Providing generic answers without specific examples of compliance efforts.
- Neglecting to mention training or staff engagement in safety practices.
- Failing to address how you handle safety violations or incidents.
Example answer
“At Larsen & Toubro, I implemented a comprehensive safety training program that involved regular workshops and drills on equipment handling and emergency procedures. I conduct monthly safety audits to ensure compliance with local regulations and industry standards. After noticing a rise in minor accidents, I revised our safety protocols to include more hands-on training and established a reporting system for unsafe conditions, leading to a 50% decrease in incidents over six months.”
Skills tested
Question type
7. Maintenance Manager Interview Questions and Answers
7.1. Can you describe a time when you implemented a new maintenance strategy that improved operational efficiency?
Introduction
This question is crucial for understanding your ability to innovate and enhance maintenance processes, which directly affect equipment reliability and operational efficiency.
How to answer
- Use the STAR (Situation, Task, Action, Result) method to frame your response
- Clearly describe the maintenance strategy you implemented and the context behind it
- Explain the specific actions you took, including how you involved your team and other stakeholders
- Quantify the improvements, such as reduced downtime, cost savings, or increased productivity
- Reflect on the lessons learned and how they can be applied in future scenarios
What not to say
- Focusing only on the technical aspects without discussing team involvement
- Failing to provide measurable outcomes or results
- Neglecting to mention the challenges faced during implementation
- Taking sole credit without acknowledging team contributions
Example answer
“At a manufacturing plant in Osaka, I noticed frequent equipment failures that led to significant downtime. I implemented a predictive maintenance strategy using IoT sensors to monitor equipment health. This reduced unplanned downtime by 35% and saved the company around ¥5 million annually. By involving the maintenance team and providing training, we ensured a smooth transition and sustained improvements.”
Skills tested
Question type
7.2. How do you prioritize maintenance tasks when faced with multiple urgent requests from different departments?
Introduction
This question assesses your prioritization and decision-making skills, which are essential in a role that often involves juggling competing demands.
How to answer
- Describe your process for assessing the urgency and impact of each maintenance request
- Explain how you communicate with different departments to understand their needs
- Discuss any tools or frameworks you use for prioritization
- Provide an example of how you successfully managed conflicting priorities in the past
- Highlight the importance of balancing immediate needs with long-term maintenance goals
What not to say
- Suggesting you handle requests on a first-come, first-served basis without analysis
- Ignoring the input of other departments in the decision-making process
- Failing to mention specific methods for prioritization
- Overemphasizing one department’s needs at the expense of others
Example answer
“When faced with multiple urgent maintenance requests, I first assess each request’s impact on safety and production. I use a priority matrix to evaluate urgency versus importance. For example, when our production line needed immediate repairs, I communicated with the operations team to understand the implications and allocated resources accordingly, which minimized downtime and met production targets.”
Skills tested
Question type
Similar Interview Questions and Sample Answers
Simple pricing, powerful features
Upgrade to Himalayas Plus and turbocharge your job search.
Himalayas
Himalayas Plus
Himalayas Max
Find your dream job
Sign up now and join over 100,000 remote workers who receive personalized job alerts, curated job matches, and more for free!
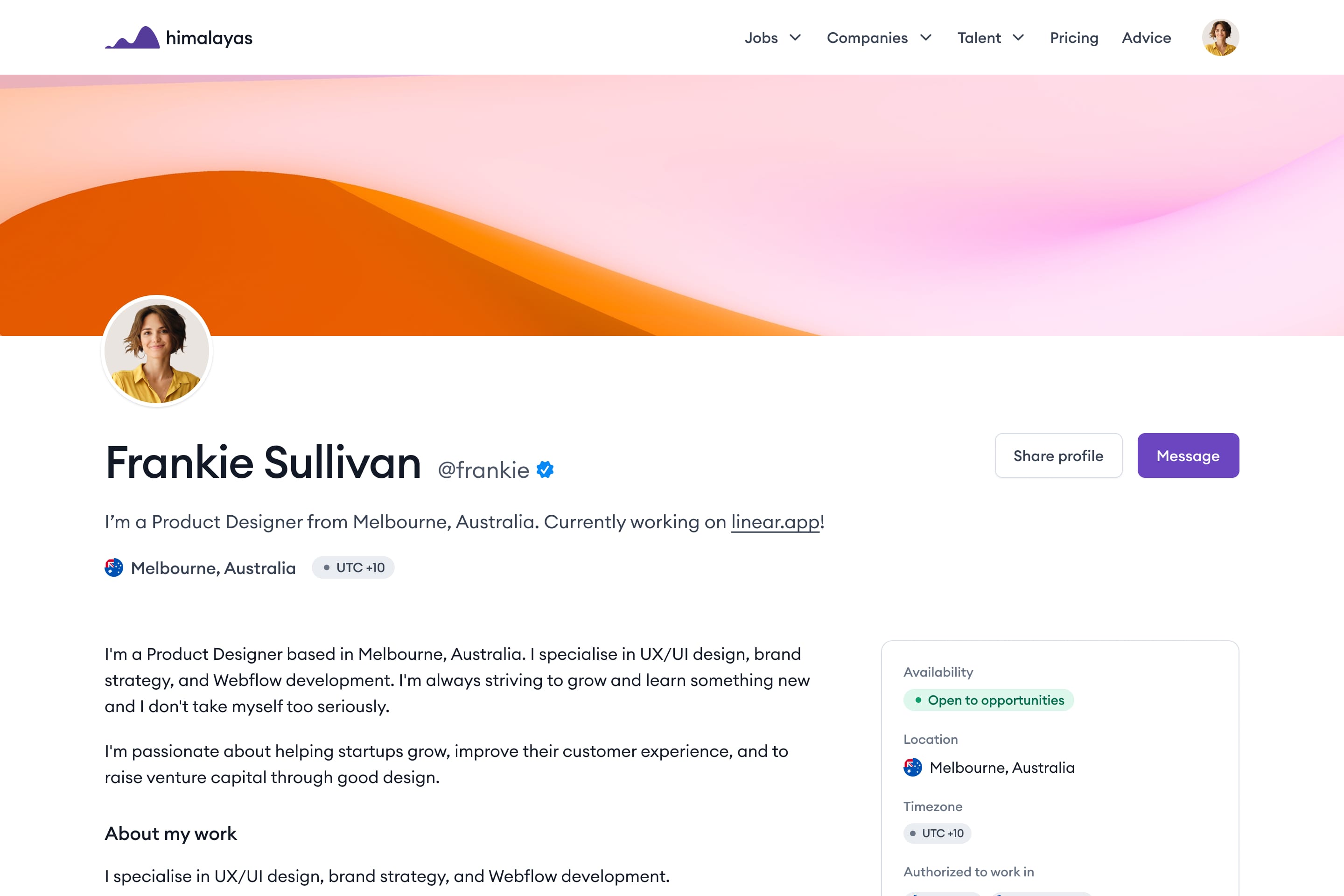