4 Header Setup Operator Interview Questions and Answers
Header Setup Operators are responsible for setting up and operating header machines used in manufacturing processes, often in the production of fasteners or similar components. They ensure machines are calibrated correctly, troubleshoot issues, and maintain quality standards. Junior operators focus on learning machine operations and basic setups, while senior and lead operators oversee complex setups, mentor team members, and ensure efficient production workflows. Need to practice for an interview? Try our AI interview practice for free then unlock unlimited access for just $9/month.
Unlimited interview practice for $9 / month
Improve your confidence with an AI mock interviewer.
No credit card required
1. Junior Header Setup Operator Interview Questions and Answers
1.1. Can you describe a time when you encountered a technical issue during a header setup, and how you resolved it?
Introduction
This question is crucial as it assesses your problem-solving skills and technical knowledge, which are essential for a Junior Header Setup Operator role.
How to answer
- Use the STAR method (Situation, Task, Action, Result) to structure your response.
- Clearly outline the technical issue and the context in which it occurred.
- Explain the steps you took to diagnose and resolve the problem.
- Highlight any collaboration or communication with team members to fix the issue.
- Share the outcome and how it improved the overall setup process.
What not to say
- Avoid vague descriptions of the issue without specifics.
- Do not take sole credit if it was a team effort.
- Refrain from mentioning a failure without discussing the learning experience.
- Steer clear of technical jargon that may confuse the interviewer.
Example answer
“During my internship at a local printing company, I encountered a problem with the header alignment on a project. The headers were misaligned due to a software glitch. I quickly communicated with my supervisor and we checked the settings together. I adjusted the parameters based on our discussion, and we ran a test print, which resulted in the headers being perfectly aligned. This experience taught me the importance of teamwork and effective communication in solving technical problems.”
Skills tested
Question type
1.2. How do you ensure quality and accuracy in your header setups?
Introduction
This question evaluates your attention to detail and commitment to quality, which are critical in this role.
How to answer
- Discuss your standard procedures for checking your work.
- Mention any tools or software you use to assist in maintaining quality.
- Explain how you handle feedback and implement it to improve accuracy.
- Provide examples of quality control measures you have followed in previous work.
- Share how you prioritize tasks to ensure accuracy under tight deadlines.
What not to say
- Claiming you do not make mistakes or need checks.
- Providing a generic answer without mentioning specific techniques.
- Focusing solely on speed at the expense of quality.
- Ignoring the importance of feedback mechanisms.
Example answer
“To ensure quality in my header setups, I follow a strict checklist that includes verifying dimensions and ensuring all specifications match the project brief. I use software tools that highlight discrepancies, and I conduct a peer review process to catch any potential errors. For example, in my last project at a student printing service, these methods allowed us to achieve a 99% accuracy rate, minimizing reprints and saving time.”
Skills tested
Question type
2. Header Setup Operator Interview Questions and Answers
2.1. Can you describe your process for setting up headers for a new job order? What key elements do you focus on?
Introduction
This question assesses your technical expertise and attention to detail in header setup, which is crucial for ensuring product quality and operational efficiency.
How to answer
- Outline the step-by-step process you follow for header setup
- Emphasize the importance of accuracy and consistency in your work
- Discuss any tools or software you use to assist with the setup
- Mention how you verify your setups before production begins
- Highlight any past experiences that illustrate your attention to detail
What not to say
- Providing a vague or generic response without a clear process
- Failing to mention the importance of accuracy or quality controls
- Overlooking the need for verification before production
- Ignoring the role of teamwork or communication with other departments
Example answer
“When setting up headers for a new job order, I follow a structured process: I start by reviewing the job specifications and ensuring I understand the requirements. I use our header setup software to input the necessary parameters, focusing on accuracy and consistency. After the initial setup, I conduct a thorough review and cross-check with the production team to confirm everything aligns with their needs. This meticulous approach helped reduce errors by 30% in my previous position at a printing company.”
Skills tested
Question type
2.2. Describe a time when you encountered a problem during the header setup process. How did you resolve it?
Introduction
This question evaluates your problem-solving abilities and how you handle challenges in a technical environment, which is important for maintaining workflow.
How to answer
- Use the STAR method to structure your answer
- Clearly define the problem and its impact on the production process
- Explain the steps you took to diagnose and resolve the issue
- Discuss any collaboration with team members or departments to fix the problem
- Share the outcome and what you learned from the experience
What not to say
- Blaming others for the problem without taking responsibility
- Providing a solution that lacks detail or misses key steps
- Failing to highlight the learning experience from the problem
- Neglecting to mention teamwork or communication aspects
Example answer
“While setting up headers for a large print job, I noticed that the dimensions were incorrect, which could have delayed production. I immediately communicated with the design team to verify the specifications. After confirming the error, I quickly adjusted the setup parameters and implemented a double-check system with the production team. The job was completed on time, and the experience taught me the importance of proactive communication and verification.”
Skills tested
Question type
3. Senior Header Setup Operator Interview Questions and Answers
3.1. Can you describe a complex setup you managed and the challenges you faced during the process?
Introduction
This question assesses your technical expertise and problem-solving skills, which are critical for a Senior Header Setup Operator in ensuring precision in production.
How to answer
- Start with a brief overview of the setup process and its significance.
- Identify the specific challenges you encountered during the setup.
- Explain the steps you took to address these challenges, including any technical adjustments or team collaboration.
- Quantify the outcome, such as improvements in efficiency or quality.
- Conclude with any lessons learned that you applied in future setups.
What not to say
- Failing to provide specific details about the challenges faced.
- Overemphasizing technical jargon without explaining its relevance.
- Not mentioning collaboration with team members or stakeholders.
- Neglecting to discuss the impact of your actions on the final output.
Example answer
“At a printing facility in Madrid, I managed a complex header setup for a high-volume client. We faced challenges with alignment and color consistency due to outdated equipment. I collaborated with the maintenance team to recalibrate the machines, resulting in a 30% reduction in waste and a 15% increase in throughput. This experience taught me the importance of proactive communication and equipment maintenance.”
Skills tested
Question type
3.2. How do you ensure quality control during the header setup process?
Introduction
This question is vital to understanding your approach to maintaining quality standards and adhering to protocols in a production environment.
How to answer
- Outline your quality control procedures during the setup.
- Mention specific tools or methods you use to monitor quality.
- Discuss how you train or guide team members in maintaining quality.
- Provide an example of a time when your quality control measures prevented a significant issue.
- Conclude with the importance of quality in the overall production process.
What not to say
- Suggesting that quality control is not a priority.
- Failing to mention specific quality control tools or methods.
- Neglecting the role of teamwork in maintaining quality.
- Providing vague examples without measurable results.
Example answer
“To ensure quality control during header setups, I implement a detailed checklist that includes alignment checks and color calibration tests at various stages. I also conduct regular training sessions for the team on quality standards. For instance, by catching a misalignment early in the process on a project for a local client, we saved over €5,000 in rework costs. Ensuring quality is essential, as it directly impacts customer satisfaction and operational costs.”
Skills tested
Question type
4. Lead Header Setup Operator Interview Questions and Answers
4.1. Can you describe a time when you identified a problem during the header setup process and how you resolved it?
Introduction
This question assesses your problem-solving skills and ability to maintain quality and efficiency in header setup operations, which are crucial for ensuring product consistency.
How to answer
- Use the STAR method (Situation, Task, Action, Result) to structure your answer.
- Clearly describe the specific problem you encountered during the header setup.
- Explain the steps you took to analyze and resolve the issue.
- Highlight any collaboration with team members or other departments.
- Share the positive outcome and any metrics that demonstrate the improvement.
What not to say
- Avoid vague descriptions without specific examples.
- Do not shift blame to others or external factors.
- Refrain from discussing problems without mentioning solutions.
- Avoid focusing solely on the technical aspects without showing teamwork.
Example answer
“At my previous job with a packaging company, I noticed inconsistencies in the header alignment that could lead to production delays. I organized a quick team meeting to identify the root cause, which was a calibration issue with our equipment. After recalibrating, I developed a simple checklist for operators to use during setup, which reduced errors by 30% and improved our output efficiency.”
Skills tested
Question type
4.2. How do you ensure compliance with safety and quality standards in the header setup process?
Introduction
This question evaluates your understanding of safety protocols and quality management, which are essential in header setup operations.
How to answer
- Describe specific safety and quality standards relevant to header setup.
- Explain your process for training team members on these standards.
- Discuss how you monitor compliance and address any discrepancies.
- Provide examples of how you have improved safety or quality in previous roles.
- Mention any relevant certifications or training you have completed.
What not to say
- Avoid stating that compliance is someone else's responsibility.
- Do not provide vague answers without specific standards or examples.
- Refrain from suggesting that safety measures slow down production.
- Do not overlook the importance of ongoing training and monitoring.
Example answer
“At my last position with a beverage manufacturer, I implemented a weekly safety training for our team focused on proper handling of equipment and materials. I also created a quality checklist that aligned with industry standards, which I reviewed with the team every morning. This proactive approach resulted in a 20% reduction in safety incidents and improved product consistency, which was recognized during our last audit.”
Skills tested
Question type
Similar Interview Questions and Sample Answers
Simple pricing, powerful features
Upgrade to Himalayas Plus and turbocharge your job search.
Himalayas
Himalayas Plus
Himalayas Max
Find your dream job
Sign up now and join over 100,000 remote workers who receive personalized job alerts, curated job matches, and more for free!
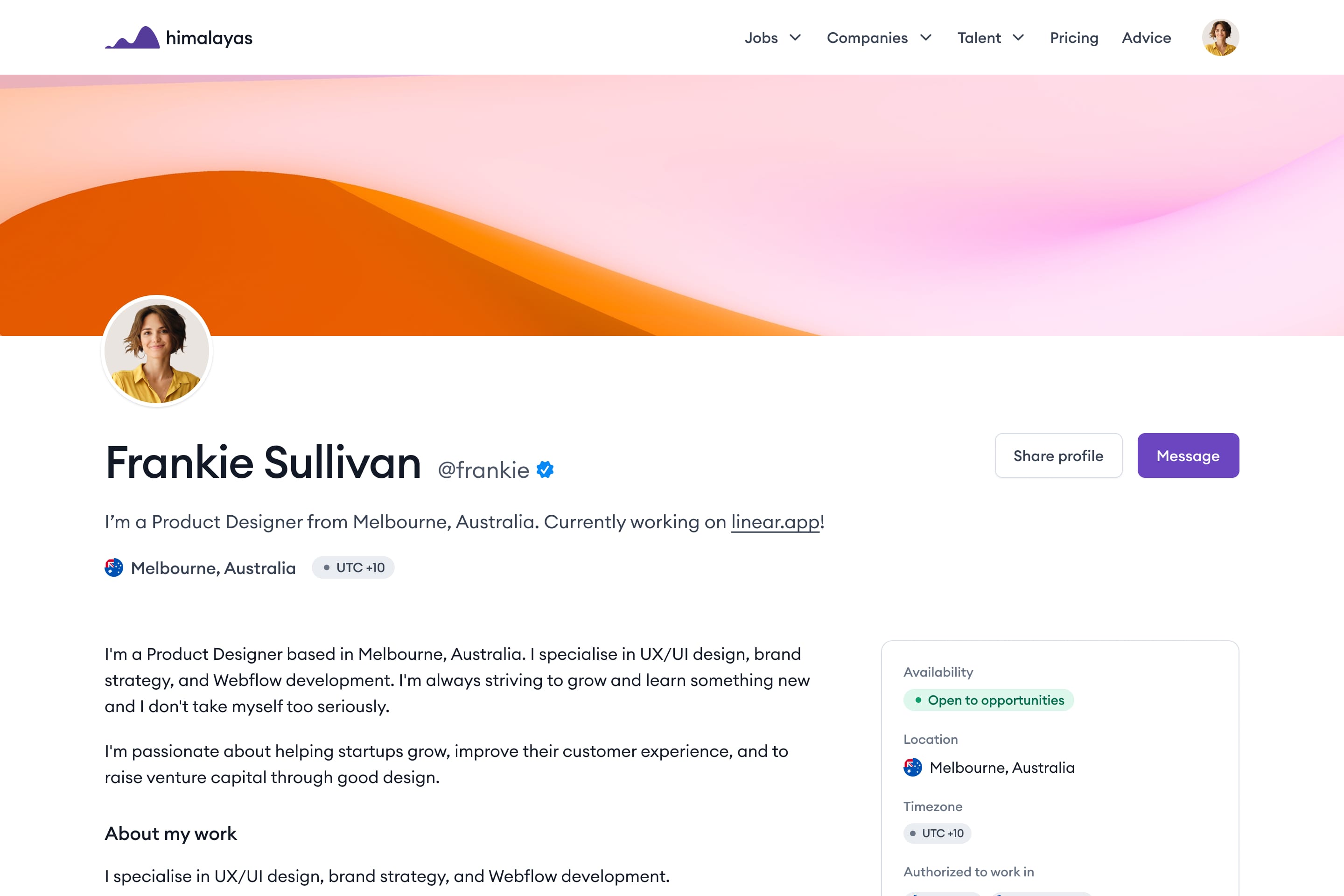