6 Hard Chrome Plater Interview Questions and Answers
Hard Chrome Platers specialize in applying a durable chrome coating to metal surfaces to enhance wear resistance, reduce friction, and improve corrosion protection. They work with precision equipment and chemical processes to ensure high-quality plating results. Entry-level roles focus on learning the plating process and equipment operation, while senior roles involve overseeing plating projects, ensuring quality standards, and mentoring junior team members. Need to practice for an interview? Try our AI interview practice for free then unlock unlimited access for just $9/month.
Unlimited interview practice for $9 / month
Improve your confidence with an AI mock interviewer.
No credit card required
1. Apprentice Hard Chrome Plater Interview Questions and Answers
1.1. Can you explain the hard chrome plating process and its applications?
Introduction
Understanding the hard chrome plating process is fundamental for an apprentice in this field. This question assesses your technical knowledge and ability to articulate complex processes clearly.
How to answer
- Start with a brief definition of hard chrome plating
- Outline the key steps involved in the plating process, including preparation, plating, and finishing
- Discuss the materials and equipment used during the process
- Explain the applications of hard chrome plating in various industries, such as automotive and aerospace
- Mention any safety protocols or environmental considerations relevant to the process
What not to say
- Providing vague or incomplete descriptions of the plating process
- Neglecting to mention applications or industry relevance
- Ignoring safety and environmental concerns
- Showing a lack of familiarity with equipment used in chrome plating
Example answer
“Hard chrome plating is an electroplating process used to deposit a layer of chromium onto a substrate for enhanced wear resistance and reduced friction. The process starts with cleaning the substrate, followed by a pre-treatment like acid etching. We then immerse the part in a chrome solution and use an electric current to deposit the chromium. This technique is critical in industries like automotive for components like pistons, where durability is essential. It's also important to follow safety protocols due to the hazardous materials involved.”
Skills tested
Question type
1.2. Describe a time when you encountered a problem during a plating job. How did you resolve it?
Introduction
This question evaluates your problem-solving skills and ability to handle challenges in a hands-on environment, which is vital for an apprentice in this trade.
How to answer
- Use the STAR (Situation, Task, Action, Result) method to structure your answer
- Clearly describe the problem you faced and its implications
- Explain the steps you took to diagnose and address the issue
- Highlight any teamwork or collaboration involved in resolving the problem
- Share the outcome and what you learned from the experience
What not to say
- Blaming others for the problem without taking responsibility
- Failing to explain the specific actions taken to resolve the issue
- Describing a lack of effort to seek help when needed
- Neglecting to mention the learning experience from the situation
Example answer
“During my internship at a local plating shop, I noticed that a batch of parts was coming out with a rough surface finish, which was not acceptable. I first analyzed the plating solution and found that the temperature was lower than required. I communicated with my supervisor and suggested recalibrating the heating system. After making the adjustments, the next batch met our quality standards. This experience taught me the importance of attention to detail and proactive problem-solving.”
Skills tested
Question type
2. Hard Chrome Plater Interview Questions and Answers
2.1. Can you describe your experience with hard chrome plating and the specific techniques you employ?
Introduction
This question is crucial for assessing your technical expertise and practical knowledge in hard chrome plating, which is essential for ensuring high-quality finishes and durability in various applications.
How to answer
- Start by detailing your hands-on experience with hard chrome plating processes.
- Explain the specific techniques and equipment you use, such as rectifiers and plating baths.
- Discuss the types of substrates you have worked with and any unique challenges you faced.
- Mention any relevant safety protocols you follow while operating plating equipment.
- Highlight any certifications or training you have received related to plating.
What not to say
- Providing vague answers without mentioning specific techniques or experiences.
- Downplaying the importance of safety and environmental regulations.
- Failing to mention the types of materials you’ve worked with.
- Not acknowledging the importance of quality control in the plating process.
Example answer
“I have over five years of experience in hard chrome plating, primarily working on automotive components. I utilize advanced rectifiers to ensure consistent current flow and maintain optimal bath chemistry. I've successfully plated steel and aluminum substrates, overcoming challenges like adhesion issues through proper surface preparation. I strictly adhere to safety protocols and have completed a certification in hazardous materials handling.”
Skills tested
Question type
2.2. Describe a challenging project you worked on that required precision in hard chrome plating. How did you ensure quality?
Introduction
This question helps evaluate your problem-solving skills and attention to detail, which are critical in hard chrome plating to achieve the necessary specifications and durability.
How to answer
- Use the STAR method to frame your response: Situation, Task, Action, and Result.
- Clearly outline the project and the specific challenges you encountered.
- Describe the steps you took to ensure precision, such as thorough inspections and adjustments.
- Mention any tools or techniques you used for quality assurance.
- Conclude with the positive outcome of your efforts, including any feedback from stakeholders.
What not to say
- Focusing solely on the problems without discussing your solutions.
- Neglecting to mention the importance of quality control measures.
- Being vague about your role in the project.
- Not addressing the outcome or results of your actions.
Example answer
“In a project for a heavy machinery manufacturer, we faced issues with thickness variation in our chrome plating. By implementing a rigorous inspection process and using a micrometer for precise measurements, I ensured we met the client's specifications. This resulted in a 100% pass rate on quality checks and positive feedback from the client, leading to repeat business.”
Skills tested
Question type
3. Senior Hard Chrome Plater Interview Questions and Answers
3.1. Can you describe a challenging hard chrome plating project you worked on and how you overcame the difficulties?
Introduction
This question assesses your technical expertise and problem-solving skills in the hard chrome plating process, which is crucial for ensuring quality and efficiency.
How to answer
- Use the STAR method to structure your response: Situation, Task, Action, Result.
- Begin by describing the specific project and the challenges faced, such as equipment failures, quality issues, or tight deadlines.
- Explain the steps you took to address these challenges, including any innovative techniques or adjustments to processes.
- Quantify the results, such as improved quality, reduced downtime, or customer satisfaction.
- Reflect on lessons learned and how they apply to future projects.
What not to say
- Avoid vague descriptions without specific challenges or solutions.
- Do not focus solely on technical details without discussing the impact on the project.
- Steering clear of blame on others; instead, emphasize personal contributions.
- Neglecting to show how you adapted or learned from the experience.
Example answer
“At a previous job, we had an urgent order for hydraulic cylinders that needed hard chrome plating, but our main plating tank malfunctioned. I quickly organized a temporary setup using a smaller tank and adjusted the plating parameters to maintain quality. We completed the order on time, and the cylinders met all quality standards, leading to a 20% increase in customer satisfaction. This taught me the importance of flexibility and quick thinking under pressure.”
Skills tested
Question type
3.2. How do you ensure safety and compliance in the hard chrome plating process?
Introduction
This question evaluates your knowledge of safety standards and regulatory compliance, which are paramount in the hard chrome plating industry.
How to answer
- Discuss specific safety regulations and standards relevant to hard chrome plating.
- Explain your process for ensuring compliance, including training, regular audits, and monitoring.
- Share experiences where you implemented safety measures or improved protocols.
- Emphasize the importance of a safety culture in the workplace.
- Mention any certifications or training you have in safety and compliance.
What not to say
- Ignoring the importance of safety and compliance in the industry.
- Providing generic responses that lack specific examples.
- Downplaying the role of teamwork in achieving safety goals.
- Failing to acknowledge past safety incidents and how they were addressed.
Example answer
“In my previous role, I ensured compliance with local and EU regulations by conducting monthly safety audits and providing training sessions for the team. When we identified a potential chemical handling issue, I developed a new protocol, which resulted in zero accidents for six months. I believe fostering a strong safety culture is essential for both employee well-being and operational efficiency.”
Skills tested
Question type
4. Lead Hard Chrome Plater Interview Questions and Answers
4.1. Can you explain your process for ensuring quality control during the hard chrome plating process?
Introduction
This question is crucial for understanding your knowledge of quality standards and your ability to maintain high production quality, which is vital in the manufacturing industry.
How to answer
- Start with an overview of the quality control measures you implement
- Detail specific tests or inspections you conduct during and after the plating process
- Explain how you monitor the plating thickness and ensure it meets specifications
- Discuss your approach to documenting quality checks and addressing any non-conformities
- Highlight any relevant standards or certifications you adhere to in your process
What not to say
- Vague references to quality without specifics
- Failing to mention the importance of documentation and traceability
- Overlooking the need for continuous improvement
- Ignoring safety and environmental regulations
Example answer
“In my previous role at a manufacturing plant, I implemented a multi-step quality control process for hard chrome plating. This included pre-plating inspections to ensure surface cleanliness, real-time monitoring of plating thickness using micrometers, and post-plating tests for adhesion and hardness. I maintained detailed logs to trace any defects back to their root cause, which helped reduce rework by 20%. Ensuring quality is essential to maintain our client's trust and meet industry standards.”
Skills tested
Question type
4.2. Describe a challenging situation you faced in your plating operations and how you resolved it.
Introduction
This question evaluates your problem-solving abilities and resilience in the face of operational challenges, which is essential for a lead position.
How to answer
- Use the STAR method: outline the Situation, Task, Action, and Result
- Clearly define the challenge and its impact on production
- Explain the steps you took to analyze and resolve the issue
- Discuss the outcome and what you learned from the experience
- Emphasize teamwork and communication if others were involved
What not to say
- Avoiding the specifics of the challenge
- Taking sole credit without acknowledging team efforts
- Focusing too much on the negative aspects without discussing solutions
- Neglecting to mention any follow-up actions or preventive measures
Example answer
“At my previous job, we experienced a significant increase in defects due to a supplier's inconsistent material quality. I organized a cross-functional team to analyze the plating results and communicate our concerns to the supplier. We developed a temporary workaround by adjusting our process parameters to accommodate the material inconsistencies. Ultimately, we switched suppliers, which reduced our defect rate by 30% and improved our overall production efficiency. This taught me the importance of proactive supplier management.”
Skills tested
Question type
5. Plating Supervisor Interview Questions and Answers
5.1. Describe a time when you had to manage a process improvement in the plating department.
Introduction
This question assesses your ability to identify inefficiencies and implement process improvements, which is critical for a Plating Supervisor to enhance productivity and product quality.
How to answer
- Start by identifying the specific process that required improvement.
- Explain the steps you took to analyze the current process and identify issues.
- Detail the changes you implemented and how you communicated these to your team.
- Quantify the results of the improvement, such as increased efficiency or reduced waste.
- Discuss any challenges faced during the implementation and how you overcame them.
What not to say
- Focusing solely on technical aspects without mentioning team involvement.
- Not providing measurable outcomes or results from the improvement.
- Avoiding discussion on challenges faced during the process.
- Claiming credit without acknowledging team contributions.
Example answer
“At a previous position with ElectroPlating Inc., I noticed that our plating throughput was below target. I conducted a root cause analysis and found that our rinse cycle was inefficient. I collaborated with my team to redesign the rinse process, implementing a new filtration system. This change improved our throughput by 20% and reduced chemical waste by 15%. It taught me the importance of team engagement in process improvements.”
Skills tested
Question type
5.2. How do you ensure compliance with safety and environmental regulations in the plating process?
Introduction
This question evaluates your understanding of safety standards and environmental regulations, which are critical in the plating industry to maintain compliance and protect employees.
How to answer
- Describe your knowledge of relevant safety and environmental regulations.
- Explain your approach to training employees on safety protocols.
- Discuss how you monitor compliance and identify potential hazards.
- Share any initiatives you’ve implemented to improve safety and environmental practices.
- Highlight the importance of a safety-first culture within your team.
What not to say
- Claiming that safety regulations are not a priority.
- Providing vague or generic answers without specifics.
- Not mentioning the role of training and team involvement in compliance.
- Underestimating the importance of documentation and reporting.
Example answer
“In my role at MetalFinish Ltd., I prioritized compliance by staying updated on safety regulations and conducting quarterly training sessions for my team. I implemented a safety audit checklist that helped identify potential hazards, leading to a 30% reduction in incidents over a year. Creating a culture of safety was key; I encouraged open communication about safety concerns, ensuring that everyone felt responsible for maintaining a safe work environment.”
Skills tested
Question type
6. Plating Manager Interview Questions and Answers
6.1. Can you describe a time you implemented a new plating process that improved efficiency in the kitchen?
Introduction
This question assesses your ability to innovate and improve operational processes, which is crucial for a Plating Manager responsible for the presentation and efficiency of food service.
How to answer
- Start by describing the existing plating process and its challenges
- Explain the rationale behind the new plating process you implemented
- Detail the steps you took to implement the change, including team involvement
- Quantify the improvements in efficiency or customer satisfaction
- Reflect on any feedback received from staff or customers post-implementation
What not to say
- Focusing solely on the technical aspects without discussing team collaboration
- Not providing measurable outcomes or improvements
- Avoiding acknowledgment of any challenges faced during implementation
- Neglecting to mention how you communicated the changes to the team
Example answer
“At a high-end restaurant in London, I noticed our plating was slowing down service during peak hours. I introduced a new assembly line method where each team member specialized in specific components of the dish. This change reduced our plating time by 20% and increased our table turnover rate significantly. Feedback from both guests and staff was overwhelmingly positive, showing that efficiency and quality could go hand in hand.”
Skills tested
Question type
6.2. How do you ensure that the plating standards are maintained across different shifts and staff members?
Introduction
This question examines your leadership and training skills, essential for maintaining consistency in food presentation.
How to answer
- Describe your approach to creating and communicating plating standards
- Explain how you train and support staff to meet these standards
- Share methods you use to monitor compliance and provide feedback
- Discuss how you handle non-compliance or inconsistency issues
- Mention any tools or resources you utilize for training and assessment
What not to say
- Implying that standards are a one-time setup without ongoing training
- Not addressing the importance of communication in maintaining standards
- Failing to acknowledge the role of team morale in compliance
- Overlooking the need for regular evaluations and adjustments to standards
Example answer
“I develop a comprehensive plating manual that includes visuals and detailed descriptions of our standards. I conduct regular training sessions and hands-on workshops to ensure every team member understands these standards. Additionally, I implement a peer review system where staff can provide feedback on each other's plating. This not only fosters a culture of consistency but also encourages teamwork. I regularly review plating during service and provide constructive feedback to maintain high standards.”
Skills tested
Question type
Similar Interview Questions and Sample Answers
Simple pricing, powerful features
Upgrade to Himalayas Plus and turbocharge your job search.
Himalayas
Himalayas Plus
Himalayas Max
Find your dream job
Sign up now and join over 100,000 remote workers who receive personalized job alerts, curated job matches, and more for free!
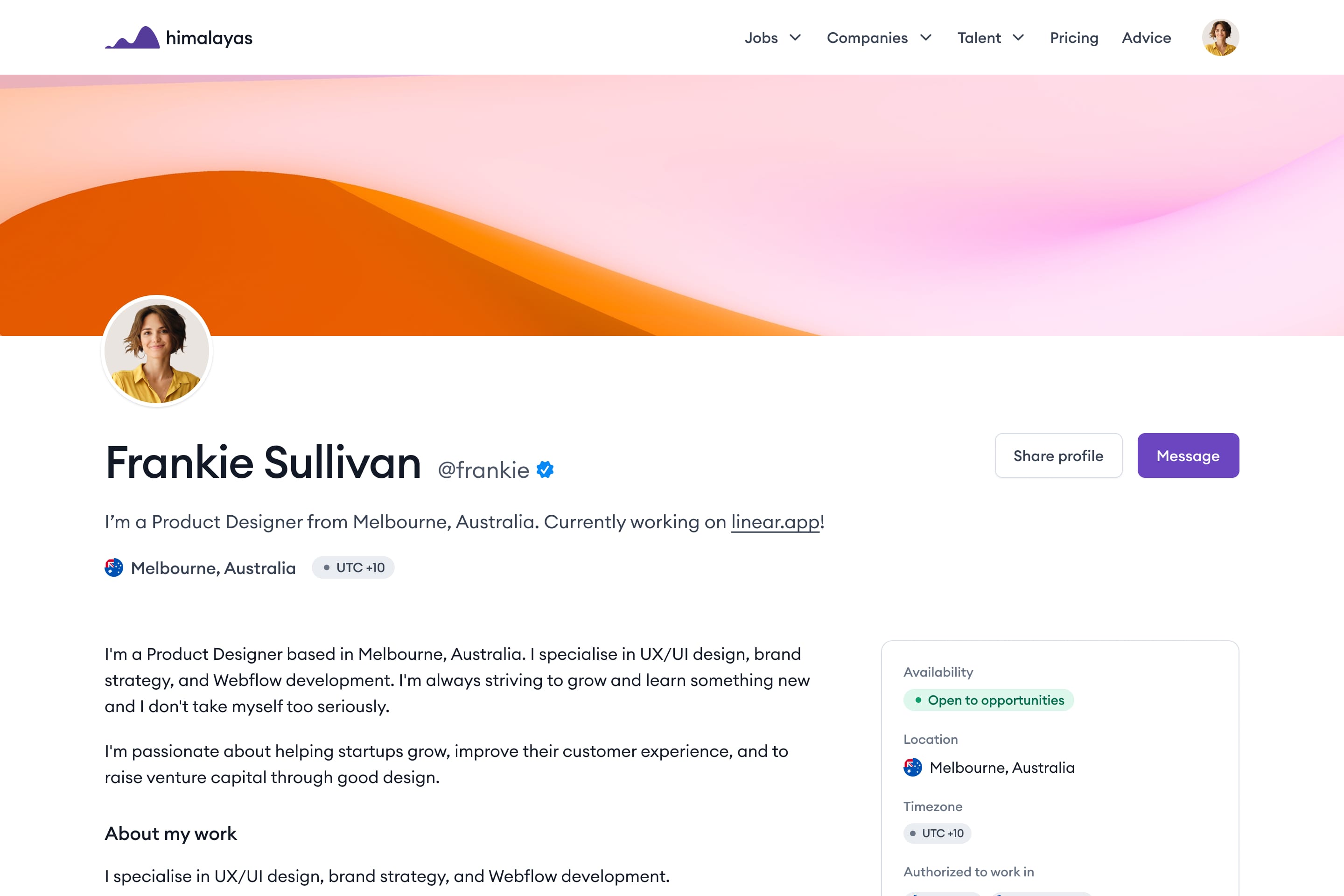