4 Feed Mixer Operator Interview Questions and Answers
Feed Mixer Operators are responsible for operating and maintaining equipment used to mix and prepare feed for livestock or other agricultural purposes. They ensure the proper blending of ingredients, monitor machinery, and adhere to safety and quality standards. Junior operators focus on learning equipment operation and basic tasks, while senior and lead operators oversee processes, troubleshoot issues, and may supervise other team members. Need to practice for an interview? Try our AI interview practice for free then unlock unlimited access for just $9/month.
Unlimited interview practice for $9 / month
Improve your confidence with an AI mock interviewer.
No credit card required
1. Junior Feed Mixer Operator Interview Questions and Answers
1.1. Can you describe your experience with operating feed mixing equipment and any safety protocols you follow?
Introduction
This question is crucial for assessing your technical skills and understanding of safety practices, both of which are essential for a Junior Feed Mixer Operator role.
How to answer
- Start by detailing your hands-on experience with specific types of feed mixing equipment.
- Discuss any relevant training or certifications you have completed.
- Explain the safety protocols you adhere to while operating the machinery.
- Share a specific instance where you successfully operated the equipment and ensured safety.
- Emphasize the importance of following manufacturer guidelines and standard operating procedures.
What not to say
- Providing vague answers without mentioning specific equipment or protocols.
- Neglecting to mention safety as a priority.
- Claiming to have experience without substantiating it with examples.
- Ignoring the importance of teamwork and communication in a manufacturing environment.
Example answer
“I have over a year of experience operating a Bucher Unipektin feed mixer, where I learned to carefully calibrate the equipment to ensure proper blending ratios. I follow strict safety protocols, including wearing appropriate PPE and conducting pre-operation checks. Last month, I identified a potential equipment malfunction during my shift and promptly reported it, preventing any safety incidents. This experience reinforced my commitment to safety and efficiency in feed production.”
Skills tested
Question type
1.2. Describe a time when you had to troubleshoot a problem during the mixing process. What steps did you take?
Introduction
This question evaluates your problem-solving abilities and your capacity to respond effectively to challenges in the feed mixing process.
How to answer
- Use the STAR method to structure your response (Situation, Task, Action, Result).
- Clearly define the problem you encountered during the mixing process.
- Explain the steps you took to troubleshoot the issue.
- Highlight any teamwork or communication involved in resolving the problem.
- Conclude with the outcome and what you learned from the experience.
What not to say
- Blaming others for the problem without taking personal accountability.
- Providing overly technical jargon that may confuse interviewers.
- Failing to mention the outcome or resolution of the issue.
- Not discussing the importance of teamwork in problem-solving.
Example answer
“During my last shift at a local feed mill, I noticed that the mixer was not achieving the desired consistency. I quickly checked the calibration settings and found them to be off. I consulted with my supervisor, and we adjusted the parameters together. As a result, we improved the mixing quality and met our production targets for the day. This experience taught me the importance of thorough checks and open communication when facing technical issues.”
Skills tested
Question type
2. Feed Mixer Operator Interview Questions and Answers
2.1. Can you describe the process you follow when mixing feed to ensure consistency and quality?
Introduction
This question evaluates your technical knowledge and attention to detail, which are crucial for maintaining the quality of feed products.
How to answer
- Outline the steps you take in the mixing process, from ingredient selection to final product testing
- Emphasize the importance of accurate measurements and monitoring equipment
- Discuss how you handle any potential issues, such as ingredient variability
- Mention the importance of adhering to safety and quality standards
- Share any technology or software you use to assist in the mixing process
What not to say
- Neglecting to mention the importance of quality control
- Focusing solely on the technical aspects without discussing consistency
- Ignoring the role of teamwork in the mixing process
- Failing to acknowledge safety protocols
Example answer
“When mixing feed at Cargill, I start by verifying the quality and specifications of each ingredient. I use a digital scale for precise measurements and regularly calibrate my mixing equipment to ensure uniformity. After mixing, I conduct batch tests to check for consistency before sending it for packaging. This approach minimizes variability and ensures we meet safety standards.”
Skills tested
Question type
2.2. Describe a time when you encountered a problem during the mixing process. How did you resolve it?
Introduction
This question assesses your problem-solving skills and ability to work under pressure, both of which are vital in fast-paced mixing operations.
How to answer
- Use the STAR method to structure your response (Situation, Task, Action, Result)
- Clearly define the problem and its impact on production
- Detail the steps you took to investigate and resolve the issue
- Highlight any collaboration with team members or supervisors
- Share the positive outcome and any lessons learned
What not to say
- Blaming others for the problem without taking responsibility
- Providing vague answers without specific actions taken
- Failing to address how you prevented similar issues in the future
- Overlooking the importance of teamwork in problem resolution
Example answer
“At my previous job with Perdue Farms, I noticed inconsistencies in the moisture levels of the feed mix. I immediately stopped production and checked the moisture sensors, which were malfunctioning. After reporting to my supervisor, we recalibrated the sensors and adjusted our ingredient ratios. This prevented a major quality issue, and I learned the importance of proactive monitoring.”
Skills tested
Question type
3. Senior Feed Mixer Operator Interview Questions and Answers
3.1. Can you describe a time when you identified a quality issue with the feed mix? How did you address it?
Introduction
This question is important as it assesses your attention to detail, problem-solving skills, and ability to maintain quality standards in feed production, which are crucial for ensuring animal health and production efficiency.
How to answer
- Use the STAR method (Situation, Task, Action, Result) to structure your response.
- Clearly outline the quality issue you encountered and its implications.
- Explain the steps you took to investigate and resolve the issue.
- Discuss how you communicated with your team and any changes made to prevent future occurrences.
- Include measurable outcomes that demonstrate the effectiveness of your actions.
What not to say
- Avoid vague descriptions of the issue without context.
- Do not take sole credit; acknowledge teamwork where applicable.
- Refrain from focusing on blame instead of solutions.
- Avoid mentioning issues that were not resolved effectively.
Example answer
“At my previous position with Cargill, I noticed inconsistencies in the texture of a specific feed mix. I conducted a thorough analysis and discovered that a supplier had altered the grain type. I immediately informed my supervisor and collaborated with the procurement team to source the correct grain. As a result, we were able to adjust the mix and maintain consistent quality, ultimately improving customer satisfaction by 20%.”
Skills tested
Question type
3.2. What safety protocols do you follow when operating feed mixing equipment?
Introduction
This question evaluates your knowledge of safety standards and practices, which are essential in preventing workplace accidents and ensuring the safety of both staff and products.
How to answer
- List specific safety protocols and procedures you adhere to.
- Explain the importance of each protocol in preventing accidents.
- Discuss any training you have received related to safety in feed mixing.
- Provide examples of how you have implemented or improved safety measures in your past roles.
- Mention the importance of reporting and addressing safety hazards.
What not to say
- Avoid generic responses that lack detail.
- Do not downplay the importance of safety.
- Refrain from sharing experiences that demonstrate negligence.
- Avoid mentioning safety protocols you're unfamiliar with.
Example answer
“In my role at Archer Daniels Midland, I strictly follow protocols such as wearing personal protective equipment (PPE), conducting daily safety checks on the mixing equipment, and ensuring proper training for all team members. I also implemented a safety audit system that led to a 30% reduction in minor accidents over the year. Prioritizing safety not only protects the team but also ensures product quality.”
Skills tested
Question type
3.3. How do you manage your time when faced with multiple feed mixing tasks and deadlines?
Introduction
This question helps assess your time management and prioritization skills, which are vital in a fast-paced environment where meeting production schedules is critical.
How to answer
- Describe your approach to prioritization and time management.
- Share specific tools or methods you use to stay organized.
- Discuss how you handle unexpected challenges or changes in schedule.
- Provide an example of a situation where you successfully managed competing deadlines.
- Emphasize the importance of communication with your team regarding workload.
What not to say
- Avoid saying you work best under pressure without examples.
- Do not imply that you struggle with time management.
- Refrain from discussing methods that lack structure or organization.
- Avoid neglecting the importance of teamwork in time management.
Example answer
“To manage my time effectively at Purina, I use a daily planner to map out tasks based on urgency and importance. For instance, when faced with simultaneous orders, I prioritize based on delivery deadlines and mix complexity. I also communicate with my team to delegate tasks when necessary. This approach helped us meet all production deadlines last quarter, even while handling a 15% increase in orders.”
Skills tested
Question type
4. Lead Feed Mixer Operator Interview Questions and Answers
4.1. Can you describe a time when you had to troubleshoot a malfunction in the feed mixing equipment?
Introduction
This question is important as it assesses your technical problem-solving skills and your ability to maintain equipment efficiency, which are crucial for a Lead Feed Mixer Operator.
How to answer
- Use the STAR method to structure your response: Situation, Task, Action, Result.
- Begin by describing the specific malfunction and its impact on operations.
- Detail the steps you took to diagnose the issue, including any tools or techniques used.
- Explain how you resolved the problem, emphasizing teamwork if applicable.
- Share the outcome and any improvements made to prevent future malfunctions.
What not to say
- Giving vague descriptions without technical details.
- Blaming others for the malfunction without taking responsibility.
- Failing to mention the importance of safety during troubleshooting.
- Overlooking the learning experience gained from the incident.
Example answer
“At a local feed mill, our mixer suddenly stopped during a critical production run, risking delivery schedules. I quickly assessed the equipment and found a faulty motor relay. I collaborated with my team to replace the relay, ensuring we followed safety protocols. We resumed production within two hours, and since then, I’ve implemented a more rigorous maintenance schedule to catch such issues early, reducing downtime by 20%.”
Skills tested
Question type
4.2. How do you ensure the quality and consistency of feed mixtures?
Introduction
This question evaluates your understanding of quality control processes and your ability to maintain product standards, which are essential in feed production.
How to answer
- Discuss the importance of ingredient selection and sourcing.
- Explain your process for calibrating mixing equipment and monitoring parameters.
- Describe how you conduct quality checks and any testing methods used.
- Highlight your approach to staff training in quality assurance.
- Mention any past experiences where you improved quality control measures.
What not to say
- Suggesting that quality checks are not necessary.
- Failing to mention specific methods or tools you use.
- Overlooking the importance of ingredient sourcing.
- Providing generic answers without personal experience.
Example answer
“To ensure quality, I maintain strong relationships with our suppliers to guarantee high-quality ingredients. I regularly calibrate the mixing equipment and monitor moisture levels during mixing. Additionally, I implement a batch testing system where samples are taken for analysis. At my previous job, these practices led to a 15% reduction in customer complaints about feed consistency, enhancing our reputation in the market.”
Skills tested
Question type
4.3. Describe a time when you had to lead a team through a challenging production schedule. What strategies did you use?
Introduction
This question is crucial as it assesses your leadership skills and ability to manage production workflows under pressure, key responsibilities for a Lead Feed Mixer Operator.
How to answer
- Use the STAR method to outline the situation clearly.
- Describe the challenges the team faced, such as tight deadlines or equipment issues.
- Detail the strategies you implemented to motivate the team and optimize workflows.
- Discuss how you communicated and coordinated with other departments.
- Share the results of your efforts and any feedback received.
What not to say
- Neglecting to provide context about the challenges faced.
- Focusing solely on your actions without mentioning team contributions.
- Ignoring the importance of clear communication.
- Failing to discuss the outcomes or lessons learned.
Example answer
“During a peak season, we faced an unexpected surge in orders, which threatened our production timeline. I organized a team meeting to assess our capacity and suggested splitting shifts to maximize output. I also worked closely with logistics to ensure raw materials were delivered on time. As a result, we met our production targets and received positive feedback from management on our teamwork and efficiency during a challenging period.”
Skills tested
Question type
Similar Interview Questions and Sample Answers
Simple pricing, powerful features
Upgrade to Himalayas Plus and turbocharge your job search.
Himalayas
Himalayas Plus
Himalayas Max
Find your dream job
Sign up now and join over 100,000 remote workers who receive personalized job alerts, curated job matches, and more for free!
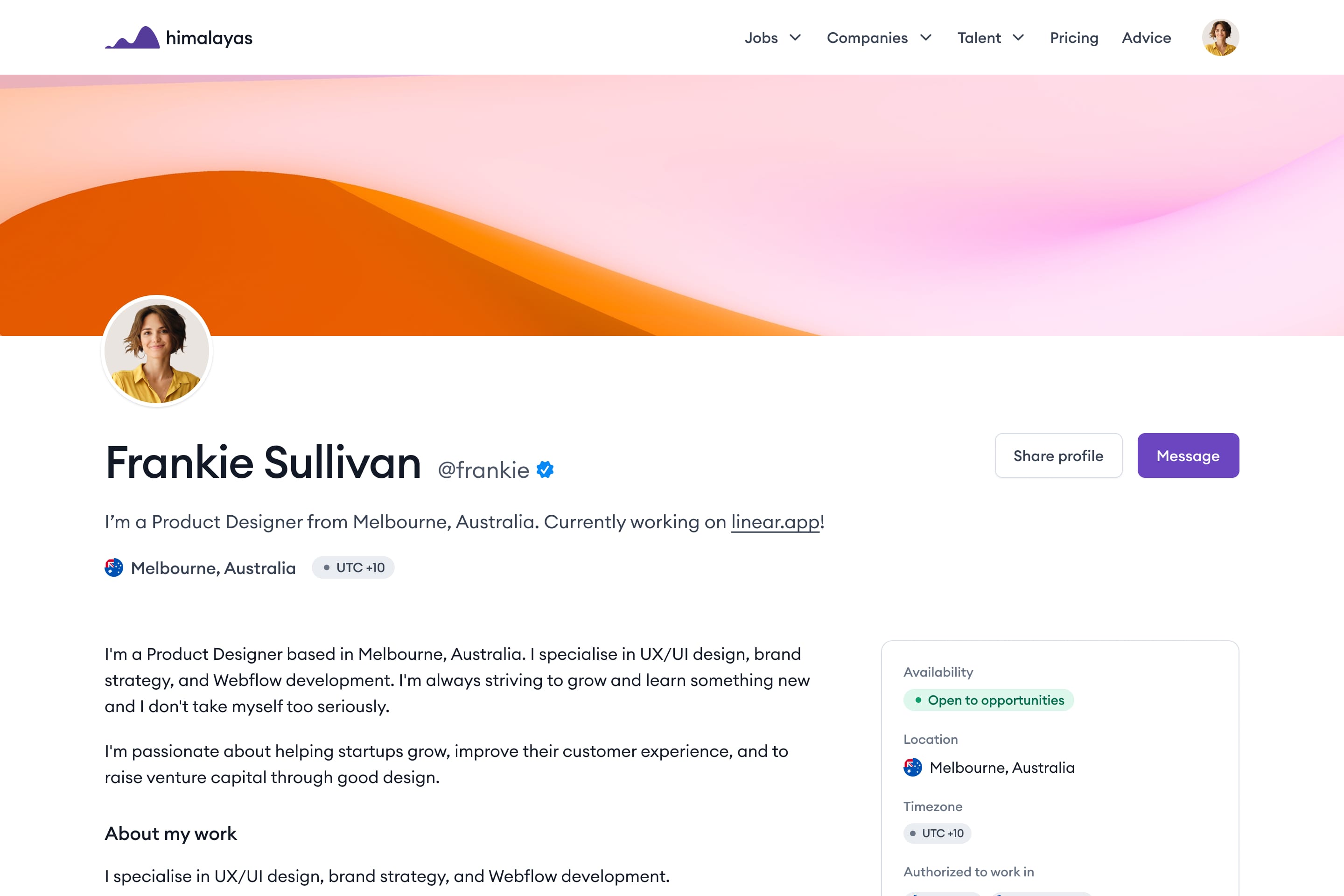