6 Fabrication Manager Interview Questions and Answers
Fabrication Managers oversee the manufacturing and assembly processes of products, ensuring efficiency, quality, and adherence to safety standards. They coordinate teams, manage resources, and implement production schedules to meet project deadlines. Junior roles may assist in operations and reporting, while senior roles involve strategic planning, team leadership, and optimizing production workflows. Need to practice for an interview? Try our AI interview practice for free then unlock unlimited access for just $9/month.
Unlimited interview practice for $9 / month
Improve your confidence with an AI mock interviewer.
No credit card required
1. Assistant Fabrication Manager Interview Questions and Answers
1.1. Can you describe a time when you had to manage a conflict between team members on the fabrication floor?
Introduction
This question assesses your conflict resolution skills and ability to maintain a productive work environment, which is crucial in a fabrication role where teamwork is key.
How to answer
- Provide context about the conflict and the parties involved
- Explain your approach to addressing the conflict, including communication strategies
- Detail the steps you took to mediate and resolve the issue
- Share the outcome and any lessons learned from the experience
- Highlight how your actions improved team dynamics or productivity
What not to say
- Avoid blaming one party without taking responsibility for your role in the situation
- Do not provide vague answers without specifics about the resolution process
- Refrain from suggesting that conflicts should be ignored or avoided
- Avoid focusing solely on the negative aspects without mentioning positive outcomes
Example answer
“At my previous job at Acciona, I encountered a conflict between two team members over differing fabrication techniques. I facilitated a meeting where both could present their viewpoints. By encouraging open communication, we discovered a compromise that combined the best of both techniques. This not only resolved the conflict but also led to a more efficient process that improved our output by 15%.”
Skills tested
Question type
1.2. How do you ensure quality control in the fabrication process?
Introduction
This question evaluates your understanding of quality assurance practices and your ability to implement them effectively in a fabrication setting.
How to answer
- Outline your approach to quality control, including tools and methods used
- Describe how you educate and train team members on quality standards
- Discuss how you monitor compliance with quality procedures
- Provide examples of specific measures you've implemented to improve quality
- Mention any relevant metrics that demonstrate the effectiveness of your quality control efforts
What not to say
- Avoid generic statements without specific examples or methodologies
- Do not suggest that quality control is the sole responsibility of one individual
- Refrain from overlooking the importance of team involvement in quality processes
- Avoid stating that quality control is not a priority in fabrication
Example answer
“In my role at Ferrovial, I implemented a comprehensive quality control plan that included regular inspections at each stage of the fabrication process. I trained my team on best practices and established a feedback loop for continuous improvement. As a result, we reduced defects by 20% over six months, ensuring our projects were delivered on time and met client standards.”
Skills tested
Question type
2. Fabrication Manager Interview Questions and Answers
2.1. Can you describe a situation where you had to manage a significant change in the fabrication process? What steps did you take to ensure a smooth transition?
Introduction
This question evaluates your change management skills and ability to adapt to new processes, which are critical for a Fabrication Manager overseeing complex manufacturing environments.
How to answer
- Use the STAR method to structure your response: Situation, Task, Action, Result.
- Clearly outline the change in the fabrication process and why it was necessary.
- Describe your approach to communicating the change to your team and stakeholders.
- Detail the training and resources you provided to support the transition.
- Share measurable outcomes that resulted from the change, such as improved efficiency or reduced costs.
What not to say
- Focusing solely on the technical aspects without discussing team dynamics.
- Neglecting to mention any resistance faced and how you addressed it.
- Failing to provide concrete metrics or results.
- Not acknowledging the importance of communication during the change.
Example answer
“At Volkswagen, we needed to shift from traditional welding methods to advanced robotic welding. I organized workshops to explain the benefits and collaborated with our HR to provide training sessions. Through clear communication and hands-on support, we transitioned smoothly, reducing production time by 20% and improving weld quality by 15%. This experience underscored the importance of managing both the technical and human aspects of change.”
Skills tested
Question type
2.2. How do you ensure quality control in the fabrication process? Can you provide an example of a quality issue you faced and how you resolved it?
Introduction
This question assesses your attention to detail and commitment to quality assurance, which are vital for maintaining high standards in fabrication.
How to answer
- Outline your quality control processes and methodologies, such as Six Sigma or Lean manufacturing.
- Provide a specific example of a quality issue, including the context and impact.
- Describe the steps you took to investigate and resolve the issue.
- Highlight any improvements made to prevent similar issues in the future.
- Mention the collaboration with other departments, like quality assurance and engineering.
What not to say
- Ignoring the importance of teamwork in resolving quality issues.
- Providing vague examples without clear outcomes.
- Failing to mention any follow-up actions taken to ensure quality.
- Downplaying the impact of quality issues on production.
Example answer
“While working at BMW, we encountered a recurring issue with dimensional inaccuracies in parts. I led a root cause analysis and discovered a calibration error in our CNC machines. I coordinated with the engineering team to recalibrate the machines and implemented a new checklist for regular quality checks. This resulted in a 30% reduction in defects and improved overall production quality, reinforcing the need for rigorous quality control processes.”
Skills tested
Question type
3. Senior Fabrication Manager Interview Questions and Answers
3.1. Can you describe a time when you had to implement a new fabrication process that significantly improved efficiency?
Introduction
This question is crucial for assessing your ability to innovate and optimize fabrication processes, which is a key responsibility of a Senior Fabrication Manager.
How to answer
- Use the STAR method to structure your response (Situation, Task, Action, Result)
- Clearly outline the inefficiencies of the previous process and its impact on production
- Describe the new process you implemented, including any technologies or methods used
- Quantify the improvements achieved (e.g., time saved, cost reduction, quality enhancement)
- Share any feedback received from the team or stakeholders about the changes
What not to say
- Focusing solely on technical details without discussing team involvement
- Providing an example without quantifiable outcomes
- Not addressing how you overcame resistance to change
- Neglecting to mention any lessons learned from the implementation
Example answer
“At Siemens, we faced a bottleneck in our metal forming process that was causing delays. I led the initiative to implement a new CNC machining technique, which reduced cycle time by 30% and improved accuracy. This change not only enhanced our production capacity but also boosted team morale as they saw the tangible benefits of their efforts. The process was adopted across all fabrication lines after a successful pilot.”
Skills tested
Question type
3.2. How do you ensure quality control in fabrication processes, especially when leading a diverse team?
Introduction
This question assesses your understanding of quality assurance measures and your ability to maintain high standards while managing a diverse workforce.
How to answer
- Explain your approach to quality control and the specific standards you follow
- Discuss how you communicate quality expectations to your team
- Describe any training or resources you provide to ensure compliance with quality standards
- Share an example of how you handled a quality issue in the past
- Highlight the importance of continuous improvement in quality practices
What not to say
- Implying that quality control is solely the responsibility of the QA team
- Providing vague answers without specific examples
- Ignoring the importance of training and communication in quality assurance
- Neglecting the role of feedback loops in maintaining quality
Example answer
“At ThyssenKrupp, I established a quality control protocol that involved regular audits and real-time feedback from the fabrication team. I implemented a training program focusing on quality standards and encouraged open communication about any quality concerns. When we identified a recurring issue with weld integrity, I facilitated cross-training sessions that improved our overall quality metrics by 20% over six months.”
Skills tested
Question type
4. Fabrication Supervisor Interview Questions and Answers
4.1. Can you describe a time when you had to manage a production issue on the fabrication floor? How did you resolve it?
Introduction
This question is crucial for understanding your problem-solving skills and your ability to handle pressure in a fabrication environment, which is vital for a supervisory role.
How to answer
- Use the STAR method (Situation, Task, Action, Result) to structure your response.
- Clearly outline the production issue and its implications for the operation.
- Detail the steps you took to resolve the issue, including any collaboration with team members.
- Highlight the outcome and any metrics that demonstrate the impact of your resolution.
- Reflect on what you learned from the experience and how it shaped your supervisory approach.
What not to say
- Blaming others for the production issue without taking responsibility.
- Failing to discuss specific actions taken to resolve the issue.
- Neglecting to mention the impact of the resolution on production metrics.
- Being vague about the situation and outcomes.
Example answer
“At XYZ Fabrication, we faced a critical issue when a key machine broke down unexpectedly, halting production. I quickly assessed the situation, coordinated with the maintenance team for immediate repairs, and communicated transparently with my team about the delays. By reallocating resources to other areas, we minimized downtime and managed to meet our production targets for the week. This experience taught me the importance of quick decision-making and cross-functional teamwork.”
Skills tested
Question type
4.2. How do you ensure safety compliance among your team on the fabrication floor?
Introduction
Safety is paramount in fabrication environments. This question assesses your commitment to safety standards and your ability to enforce compliance among team members.
How to answer
- Describe your approach to communicating safety standards and protocols.
- Share specific training or initiatives you have implemented to promote safety.
- Explain how you monitor compliance and address violations.
- Discuss the importance of creating a safety-first culture within your team.
- Mention any safety metrics or improvements achieved under your supervision.
What not to say
- Implying that safety is not a priority in your operations.
- Failing to provide specific examples of safety initiatives.
- Neglecting to mention how you hold team members accountable.
- Being unaware of relevant safety regulations and standards.
Example answer
“At ABC Manufacturing, I initiated a weekly safety briefing where we reviewed protocols and shared best practices. I also implemented a safety observation program where team members could anonymously report concerns. As a result, we saw a 30% decrease in workplace incidents over the past year, reinforcing a culture where everyone feels responsible for safety.”
Skills tested
Question type
5. Director of Fabrication Interview Questions and Answers
5.1. Can you describe a complex fabrication project you managed from conception to completion?
Introduction
This question assesses your project management skills, technical knowledge, and ability to deliver results in a fabrication setting, which are crucial for a Director of Fabrication.
How to answer
- Outline the project's objectives and scope clearly
- Discuss the planning and resource allocation process
- Describe your role in overseeing the fabrication process and managing the team
- Highlight any challenges faced and how you overcame them
- Share the final outcomes, including metrics like time, cost, and quality improvements
What not to say
- Failing to mention specific metrics or outcomes
- Focusing too much on technical details without discussing leadership and management
- Not explaining how you handled challenges or team dynamics
- Overlooking the importance of communication with stakeholders
Example answer
“At Boeing, I managed a project to fabricate a new wing design for a commercial aircraft. I coordinated a cross-functional team, ensuring that we adhered to timelines and budgets. When we encountered material supply issues, I quickly sourced alternatives and negotiated with suppliers to minimize delays. Ultimately, we completed the project 10% under budget and improved structural integrity by 15%, which was critical for safety compliance.”
Skills tested
Question type
5.2. How do you ensure quality control in fabrication processes?
Introduction
This question evaluates your knowledge of quality assurance methodologies and your commitment to maintaining high standards in fabrication, which is essential for a leadership role in this field.
How to answer
- Discuss the quality control processes you have implemented in past roles
- Mention specific tools or methodologies you use, such as Six Sigma or Lean Manufacturing
- Explain how you train your team to adhere to quality standards
- Describe how you handle quality issues when they arise
- Provide examples of how your quality control measures positively impacted the final products
What not to say
- Implying that quality control is someone else's responsibility
- Being vague about the processes or tools you use
- Not providing specific examples or metrics
- Ignoring the importance of team training and engagement in quality assurance
Example answer
“In my role at Lockheed Martin, I implemented a Lean Six Sigma quality control process that reduced defects by 30%. I trained my team on statistical process control and established regular quality audits. When we faced a recurring issue with weld integrity, we conducted root cause analysis and adjusted our training program, leading to a 25% improvement in compliance with quality standards over six months.”
Skills tested
Question type
6. VP of Fabrication Interview Questions and Answers
6.1. Can you describe a significant operational challenge you faced in a fabrication environment and how you overcame it?
Introduction
This question is essential as it assesses your problem-solving abilities, operational knowledge, and leadership skills in managing complex fabrication processes.
How to answer
- Start by clearly defining the challenge and its impact on production or safety.
- Explain the steps you took to analyze the situation and gather data.
- Discuss your decision-making process and the options you considered.
- Detail the implemented solutions and how you involved your team.
- Quantify the results and improvements achieved as a result of your actions.
What not to say
- Avoid vague descriptions of the challenge without specifics.
- Don't take sole credit for the solution; acknowledge team efforts.
- Refrain from focusing too much on technical jargon without clarity.
- Avoid discussing failures without highlighting what you learned from them.
Example answer
“At Thyssenkrupp, we faced a significant delay due to a supplier failing to deliver critical components on time, affecting our production schedule. I organized a cross-functional team to assess alternative suppliers and negotiated expedited delivery terms. We implemented temporary process adjustments and communicated transparently with stakeholders. As a result, we minimized downtime by 30% and maintained our production targets, reinforcing the importance of agility and teamwork in operations.”
Skills tested
Question type
6.2. How do you ensure quality control across different fabrication processes and teams?
Introduction
This question evaluates your understanding of quality management systems and your capability to enforce standards consistently across operations.
How to answer
- Discuss specific quality control methodologies or frameworks you have implemented.
- Explain how you train and empower teams to adhere to quality standards.
- Describe your process for monitoring and measuring quality metrics.
- Share examples of how you have improved quality through feedback loops.
- Highlight your approach to addressing non-conformities and continuous improvement.
What not to say
- Avoid suggesting that quality control is solely the responsibility of a single department.
- Don't provide generic answers without specific examples.
- Refrain from discussing quality issues without outlining how you addressed them.
- Avoid overlooking the importance of training and team engagement.
Example answer
“At Siemens, I implemented a Six Sigma approach to ensure quality across our fabrication processes. Each team received training on quality standards and methodologies, empowering them to take ownership of their output. We established regular audits and feedback sessions to identify areas for improvement, which led to a 20% reduction in defects within six months. I believe that quality is a collective responsibility and requires continuous engagement from all team members.”
Skills tested
Question type
Similar Interview Questions and Sample Answers
Simple pricing, powerful features
Upgrade to Himalayas Plus and turbocharge your job search.
Himalayas
Himalayas Plus
Himalayas Max
Find your dream job
Sign up now and join over 100,000 remote workers who receive personalized job alerts, curated job matches, and more for free!
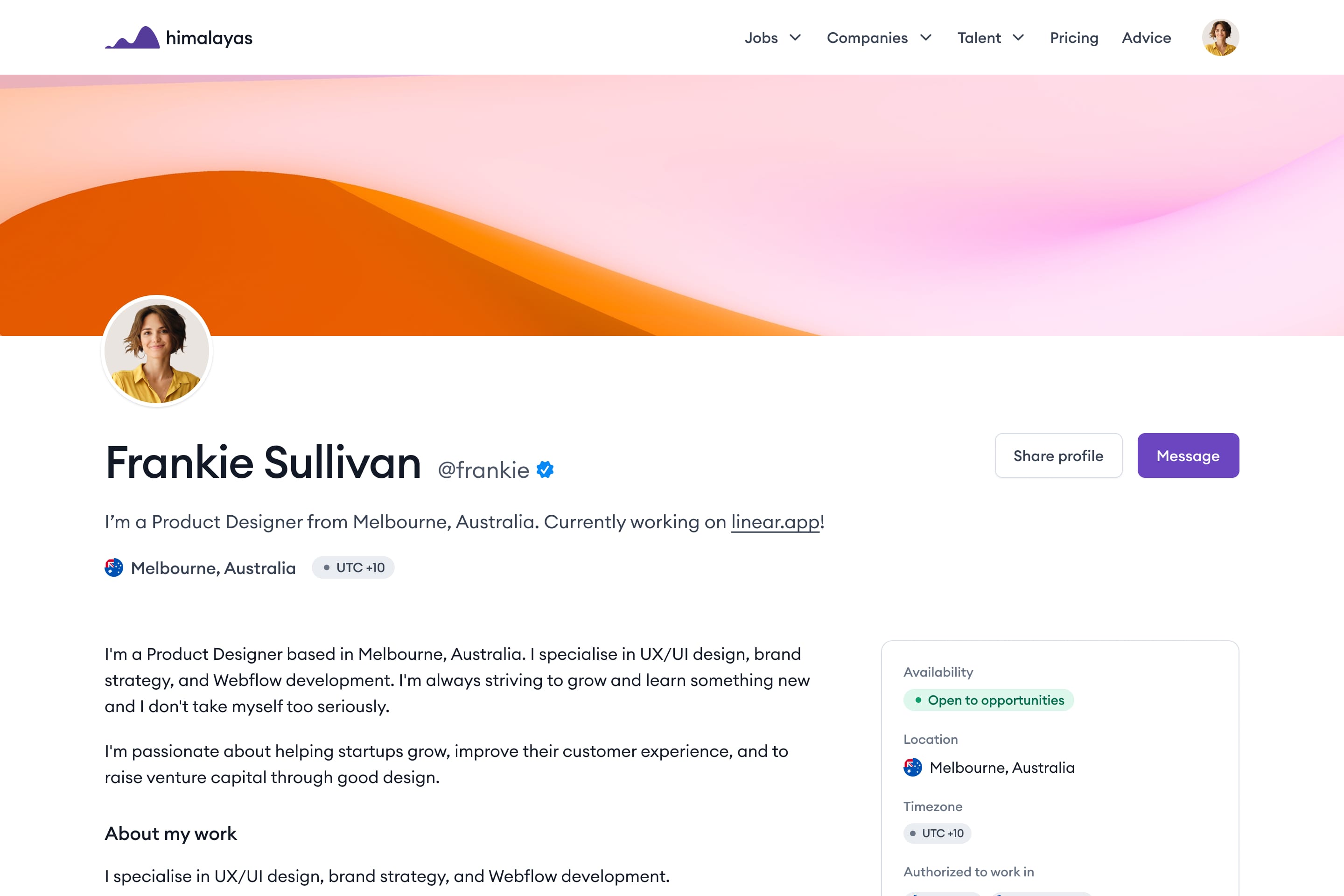