4 Eyeglass Assembler Interview Questions and Answers
Eyeglass Assemblers are responsible for constructing and assembling eyeglasses, ensuring precision and quality in the final product. They work with lenses, frames, and other components, often using specialized tools and machinery. Junior roles focus on basic assembly tasks, while senior and lead positions involve overseeing production, quality control, and mentoring team members. Need to practice for an interview? Try our AI interview practice for free then unlock unlimited access for just $9/month.
Unlimited interview practice for $9 / month
Improve your confidence with an AI mock interviewer.
No credit card required
1. Eyeglass Assembler Interview Questions and Answers
1.1. Can you describe a time when you faced a quality control issue during assembly? How did you address it?
Introduction
This question is important because quality control is critical in eyeglass assembly to ensure product safety and customer satisfaction. It evaluates your attention to detail and problem-solving skills.
How to answer
- Use the STAR method (Situation, Task, Action, Result) to structure your response.
- Clearly describe the quality control issue you encountered, including specifics about the assembly process.
- Explain the steps you took to investigate the issue and identify the root cause.
- Detail the corrective actions you implemented to resolve the problem and prevent future occurrences.
- Quantify the results to demonstrate the impact of your actions on product quality.
What not to say
- Blaming others or external factors without taking responsibility.
- Describing a situation where you ignored the issue.
- Failing to mention any specific metrics or results.
- Not showing a proactive approach to quality control.
Example answer
“In my previous role at Luxottica, I noticed a consistent defect in the lens fitting process, which resulted in a 5% return rate. I initiated a quality review to analyze the assembly procedures. After identifying that improper alignment during assembly was the cause, I implemented a new training session for the team and adjusted our assembly jigs. As a result, we reduced the return rate to 1% within three months.”
Skills tested
Question type
1.2. How do you ensure precision when assembling eyeglasses?
Introduction
This question assesses your technical skills and understanding of the precision required in eyeglass assembly, which is vital for both functionality and customer satisfaction.
How to answer
- Discuss the tools and techniques you use to ensure accuracy.
- Explain your process for checking measurements and alignment.
- Describe any quality assurance protocols you follow.
- Mention any training or experience that has helped you develop precision in your work.
- Highlight the importance of attention to detail in preventing defects.
What not to say
- Implying that precision isn't important.
- Describing a lack of processes or tools to ensure quality.
- Failing to provide specific examples of how you achieve precision.
- Neglecting to mention the significance of meticulous work in assembly.
Example answer
“To ensure precision, I always use calibrated tools for measurement and alignment, such as calipers and alignment jigs. I double-check each measurement before proceeding with assembly. At my last job, I developed a checklist that included critical steps for each assembly phase. This helped maintain high quality and reduced errors significantly, leading to fewer returns and higher customer satisfaction.”
Skills tested
Question type
1.3. What steps would you take if you were assigned to assemble a new type of eyeglasses with unfamiliar components?
Introduction
This question evaluates your adaptability and willingness to learn, which are essential traits for a position that may require working with various products and technologies.
How to answer
- Describe your approach to researching and understanding new components.
- Explain how you would seek guidance or training from experienced colleagues or supervisors.
- Discuss the importance of following assembly instructions and guidelines.
- Mention any strategies you would use to test and validate the assembly process.
- Highlight your proactive attitude towards learning and adapting to new technologies.
What not to say
- Expressing reluctance or resistance to learning new skills.
- Suggesting you would proceed without proper knowledge or guidance.
- Failing to acknowledge the importance of research and training.
- Indicating a lack of interest in understanding new technologies.
Example answer
“If tasked with assembling a new type of eyeglasses, I would first review any available assembly guides and technical specifications. I would also reach out to colleagues who have experience with the new components for insights. If necessary, I'd attend training sessions to get hands-on experience. After assembling a few units, I would conduct tests to ensure everything functions correctly before full-scale production. This approach not only helps me adapt quickly but also contributes to overall product quality.”
Skills tested
Question type
2. Senior Eyeglass Assembler Interview Questions and Answers
2.1. Describe a time when you had to troubleshoot a complex assembly issue with eyeglasses.
Introduction
This question assesses your problem-solving skills and technical knowledge in eyeglass assembly, which are critical for ensuring product quality and customer satisfaction.
How to answer
- Use the STAR method to structure your response: Situation, Task, Action, Result.
- Clearly define the assembly issue and its impact on production or quality.
- Detail the steps you took to identify the root cause of the problem.
- Describe the specific actions you implemented to resolve the issue.
- Share the results, including any improvements in efficiency or quality metrics.
What not to say
- Providing vague descriptions without specifics on the issue or resolution.
- Failing to highlight your role in the troubleshooting process.
- Overlooking the importance of quality standards in the assembly process.
- Not mentioning how the experience informed your future approaches.
Example answer
“At Luxottica, we faced frequent misalignments in our glasses frames during assembly, which increased return rates. I conducted a thorough analysis, identifying that the issue stemmed from a faulty calibration on our cutting machines. I collaborated with the maintenance team to recalibrate the machines and developed a checklist for daily inspections. As a result, we reduced misalignments by 60% and improved overall customer satisfaction scores.”
Skills tested
Question type
2.2. How do you ensure quality and precision in your eyeglass assembly work?
Introduction
This question evaluates your commitment to quality control and your methods for maintaining high standards in production, which are crucial for customer satisfaction and brand reputation.
How to answer
- Discuss specific quality control processes you follow during assembly.
- Explain how you conduct inspections and what criteria you use.
- Share examples of tools or techniques that help you maintain precision.
- Mention your approach to training and mentoring others on quality standards.
- Highlight any metrics or results that demonstrate your commitment to quality.
What not to say
- Implying that quality control is someone else's responsibility.
- Failing to mention specific practices or tools you use.
- Being overly vague about your quality assurance approach.
- Neglecting to discuss the importance of customer satisfaction.
Example answer
“I implement a rigorous quality control process during assembly. Every pair of eyeglasses is inspected for frame alignment, lens fitting, and overall finish using calibrated tools. I also keep a detailed log of defects to identify patterns and areas for improvement. Through this process, I reduced our defect rate by 30% at my previous job at Fielmann, which significantly enhanced our customer satisfaction ratings.”
Skills tested
Question type
3. Lead Eyeglass Assembler Interview Questions and Answers
3.1. Can you describe a situation where you had to troubleshoot a defect in an eyeglass frame during production?
Introduction
This question assesses your problem-solving skills and attention to detail, which are crucial for ensuring quality in eyeglass assembly.
How to answer
- Start by clearly stating the defect you encountered and its implications on the production line.
- Describe the steps you took to identify the root cause of the defect.
- Explain the solutions you implemented to resolve the issue.
- Highlight any preventive measures you put in place to avoid similar defects in the future.
- Quantify the impact of your actions on production efficiency or quality.
What not to say
- Dismissing defects as minor without addressing their impact.
- Failing to demonstrate a systematic approach to problem-solving.
- Not mentioning collaboration with colleagues or supervisors.
- Describing a situation without a clear resolution or learning outcome.
Example answer
“At Luxottica, I identified a recurring issue with misaligned lenses in our assembly line. I conducted a thorough analysis and discovered that the alignment jig was worn. I replaced the jig and trained the team on proper calibration techniques. This action led to a 30% reduction in defects, significantly improving overall quality control.”
Skills tested
Question type
3.2. How do you ensure that you meet production deadlines while maintaining high-quality standards?
Introduction
This question evaluates your time management and quality assurance practices, which are essential for a lead assembler in a fast-paced environment.
How to answer
- Outline your planning and prioritization methods for daily tasks.
- Discuss how you balance speed with quality checks during the assembly process.
- Provide examples of how you motivate your team to maintain productivity without sacrificing quality.
- Explain any tools or technologies you use to monitor production progress.
- Mention any specific quality assurance protocols you’ve implemented.
What not to say
- Indicating that quality is secondary to meeting deadlines.
- Failing to provide concrete examples of past experiences.
- Suggesting that team motivation is not important.
- Not mentioning any systems or processes for monitoring quality.
Example answer
“In my previous role at Essilor, I implemented a daily production checklist that prioritized high-quality standards alongside deadlines. I held morning briefings to motivate the team and set clear expectations. By streamlining our quality checks and using production tracking software, we consistently met our deadlines while reducing defects by 20%.”
Skills tested
Question type
4. Assembly Supervisor (Eyeglasses) Interview Questions and Answers
4.1. Can you describe a time when you improved the assembly process in your previous role?
Introduction
This question assesses your ability to identify inefficiencies and implement improvements in the assembly line, which is crucial for a supervisory role in manufacturing.
How to answer
- Use the STAR method to structure your response: Situation, Task, Action, Result.
- Clearly describe the specific assembly process you focused on and the challenges it faced.
- Detail the steps you took to analyze the process and propose improvements.
- Explain how you implemented the changes and any training provided to team members.
- Quantify the results, such as improvements in efficiency, reduction in defects, or time saved.
What not to say
- Focusing solely on the problems without discussing solutions.
- Failing to mention teamwork or collaboration with others.
- Providing vague examples that lack specific metrics or outcomes.
- Avoiding responsibility or blaming others for existing issues.
Example answer
“In my previous position at Luxottica, I noticed that our assembly line was experiencing delays due to inefficient layout. I analyzed the workflow and proposed a redesign that reduced unnecessary movement. After implementing a streamlined process and training my team, we improved our assembly speed by 20% and reduced defects by 15%, which significantly boosted our overall productivity.”
Skills tested
Question type
4.2. How do you ensure quality control in the assembly of eyeglasses?
Introduction
This question evaluates your understanding of quality assurance processes and your ability to maintain high standards in production, which is vital in the eyewear industry.
How to answer
- Explain the importance of quality control in the assembly process.
- Describe specific quality control measures you implement, such as inspections and testing.
- Discuss how you train your team to adhere to quality standards.
- Share examples of how you handle defects or quality issues when they arise.
- Mention the metrics you use to measure quality performance.
What not to say
- Neglecting to mention proactive measures for quality control.
- Suggesting that quality checks are solely the responsibility of a separate team.
- Providing examples without clear outcomes or metrics.
- Failing to discuss the importance of continuous improvement in quality processes.
Example answer
“At Safilo, I established a quality control checklist for each assembly station, including visual inspections and functionality tests. I trained my team to identify defects early and encouraged a culture of accountability. We implemented weekly quality reviews, which resulted in a 30% reduction in returns due to quality issues over six months.”
Skills tested
Question type
Similar Interview Questions and Sample Answers
Simple pricing, powerful features
Upgrade to Himalayas Plus and turbocharge your job search.
Himalayas
Himalayas Plus
Himalayas Max
Find your dream job
Sign up now and join over 100,000 remote workers who receive personalized job alerts, curated job matches, and more for free!
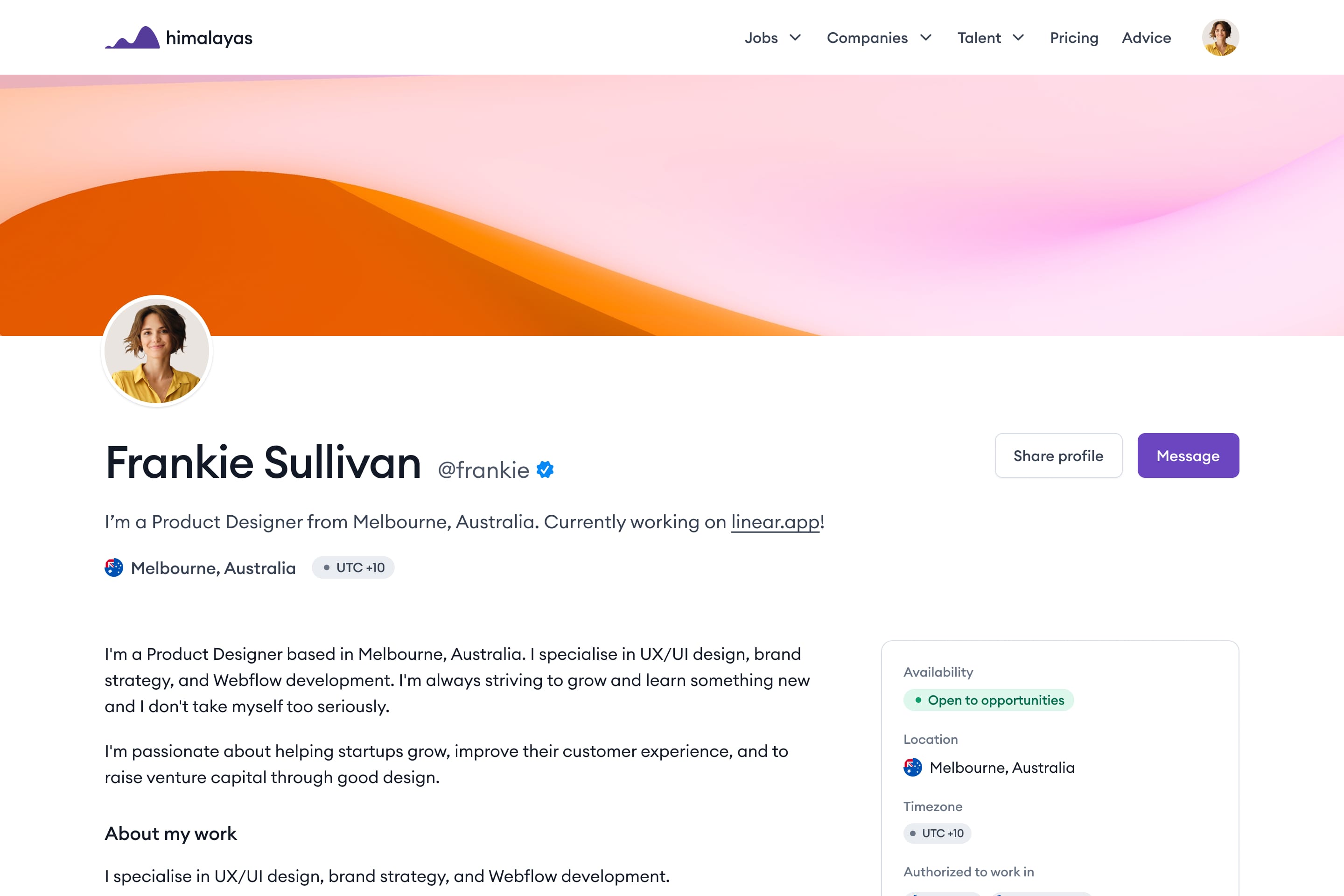