5 Equipment Specialist Interview Questions and Answers
Equipment Specialists are responsible for managing, maintaining, and ensuring the proper functioning of equipment used in various industries. They may handle tasks such as equipment inspections, troubleshooting, repairs, and providing technical support. Junior roles focus on learning and assisting with basic tasks, while senior and lead roles involve overseeing operations, training others, and managing equipment-related strategies and processes. Need to practice for an interview? Try our AI interview practice for free then unlock unlimited access for just $9/month.
Unlimited interview practice for $9 / month
Improve your confidence with an AI mock interviewer.
No credit card required
1. Junior Equipment Specialist Interview Questions and Answers
1.1. Can you describe a time when you had to troubleshoot a piece of equipment? What steps did you take?
Introduction
This question assesses your problem-solving abilities and technical knowledge, both of which are crucial for a Junior Equipment Specialist role.
How to answer
- Use the STAR method (Situation, Task, Action, Result) to structure your answer.
- Clearly describe the equipment issue and its context.
- Detail the troubleshooting steps you took, emphasizing your analytical skills.
- Highlight any tools or techniques you used in the process.
- Mention the outcome and how it benefited the team or organization.
What not to say
- Providing vague answers without specific details.
- Avoiding technical terminology that shows lack of knowledge.
- Focusing too much on the problem rather than the solution.
- Not acknowledging any mistakes or learning experiences.
Example answer
“At a construction site, I encountered a malfunctioning hydraulic lift. I first assessed the situation, identifying a potential hydraulic fluid leak. I checked the fluid levels and inspected the hoses for damage. After tightening some connections and replacing a worn hose, I tested the lift, restoring its function. This not only saved time but also ensured safety on site, reinforcing my troubleshooting skills.”
Skills tested
Question type
1.2. How do you prioritize your tasks when you have multiple equipment issues to address at the same time?
Introduction
This question evaluates your time management and prioritization skills, essential for effectively managing multiple responsibilities.
How to answer
- Describe a systematic approach to assess and prioritize tasks.
- Explain the criteria you use to determine urgency and importance.
- Discuss any tools or methods you utilize to keep track of tasks.
- Provide an example of a time when you successfully managed competing priorities.
- Highlight your communication strategy with team members regarding task statuses.
What not to say
- Claiming you can handle everything at once without a clear strategy.
- Neglecting the importance of collaboration with colleagues.
- Providing a generic answer without personal experience.
- Indicating that you become overwhelmed under pressure.
Example answer
“When faced with multiple equipment issues, I first assess each situation by urgency—prioritizing those that impact safety or operations. For instance, when two machines broke down simultaneously, I addressed the one that was critical for ongoing construction first. I communicated with my team to delegate less urgent tasks, allowing us to resolve the issues efficiently. This method helped maintain workflow and prevent delays.”
Skills tested
Question type
2. Equipment Specialist Interview Questions and Answers
2.1. Describe a time when you identified a significant issue with equipment maintenance and how you addressed it.
Introduction
This question is crucial for assessing your problem-solving skills and attention to detail, which are essential for an Equipment Specialist responsible for maintaining operational efficiency.
How to answer
- Use the STAR method (Situation, Task, Action, Result) to structure your response.
- Clearly outline the specific issue you identified with the equipment.
- Detail the steps you took to investigate and resolve the issue.
- Highlight any collaboration with team members or departments.
- Quantify the results of your actions, such as reduced downtime or cost savings.
What not to say
- Failing to provide a specific example and discussing a generic situation.
- Not mentioning any preventive measures implemented after the incident.
- Blaming others for the issue without taking any responsibility.
- Overlooking the importance of teamwork in resolving the issue.
Example answer
“At a mining site in Queensland, I noticed that a critical piece of equipment was frequently failing during operations. I conducted a thorough inspection and discovered that the maintenance schedule was not being adhered to. I collaborated with the maintenance team to revise the schedule and implemented a more rigorous tracking system. As a result, we reduced equipment downtime by 30%, which significantly improved productivity.”
Skills tested
Question type
2.2. How do you stay updated on the latest equipment technology and industry standards?
Introduction
This question evaluates your commitment to professional development and your ability to adapt to the evolving landscape of equipment technology.
How to answer
- Discuss specific resources you utilize, such as industry journals, webinars, and conferences.
- Mention any professional associations you are a part of.
- Explain how you apply new knowledge to your work.
- Share examples of how staying informed has benefited your team or organization.
- Highlight any certifications or training programs you have completed.
What not to say
- Claiming you do not need to stay updated because you have enough experience.
- Providing vague answers without mentioning specific resources or actions.
- Neglecting to explain how new knowledge impacts your work.
- Overlooking the importance of continuous learning in your field.
Example answer
“I regularly read industry journals like 'Equipment Today' and attend webinars hosted by organizations like the Australian Institute of Mining and Metallurgy. I also participate in local equipment expos to see the latest technology firsthand. Recently, I implemented a new tracking software that I learned about at a conference, which improved our equipment utilization by 20%.”
Skills tested
Question type
3. Senior Equipment Specialist Interview Questions and Answers
3.1. Can you describe a time when you identified a significant equipment issue that affected operations? How did you handle it?
Introduction
This question assesses your technical expertise as well as your problem-solving and communication skills, which are crucial for a Senior Equipment Specialist responsible for maintaining operational efficiency.
How to answer
- Use the STAR method to structure your response: Situation, Task, Action, Result.
- Clearly explain the context of the equipment issue and its impact on operations.
- Detail the steps you took to diagnose the problem and any analysis you performed.
- Describe how you communicated your findings and coordinated with relevant stakeholders.
- Quantify the results of your actions and any improvements made post-resolution.
What not to say
- Focusing solely on technical details without discussing the impact on operations.
- Failing to mention collaboration with other team members or departments.
- Neglecting to discuss the outcome or lessons learned.
- Blaming others for the issue without taking responsibility for resolution.
Example answer
“At Siemens, I noticed recurring downtime in one of our key production machines. I conducted a thorough analysis and discovered that a specific component was prone to failure. I quickly informed the operations team and worked with the maintenance staff to implement a preventative maintenance schedule. As a result, we reduced downtime by 30% and improved overall efficiency significantly. This experience taught me the importance of proactive communication and teamwork in resolving equipment issues.”
Skills tested
Question type
3.2. How do you stay updated with the latest advancements in equipment technology?
Introduction
This question evaluates your commitment to continuous learning and your ability to integrate new technologies into your work, which is essential for a Senior Equipment Specialist.
How to answer
- Discuss specific resources you use to stay informed, such as industry journals or webinars.
- Mention any professional organizations or networks you are part of.
- Explain how you apply new knowledge to your role or share it with your team.
- Highlight any relevant certifications or courses you have completed recently.
- Provide examples of how adopting new technologies has benefited your previous employers.
What not to say
- Indicating a lack of interest in keeping up with industry trends.
- Providing vague responses without specific examples or resources.
- Focusing only on past knowledge without mentioning current practices.
- Neglecting to discuss the application of new knowledge in your work.
Example answer
“I actively subscribe to industry publications like 'Equipment Today' and participate in webinars hosted by professional organizations such as VDMA. Recently, I completed a certification in predictive maintenance technologies. At my last job, I introduced a new monitoring system that improved our predictive maintenance capabilities, reducing equipment failure rates by 25%. Staying informed allows me to bring innovative solutions to the team.”
Skills tested
Question type
4. Lead Equipment Specialist Interview Questions and Answers
4.1. Can you describe a time when you had to troubleshoot a significant equipment failure and how you resolved it?
Introduction
This question is critical for assessing your technical problem-solving skills and ability to handle pressure during equipment failures, which is a common scenario for a Lead Equipment Specialist.
How to answer
- Use the STAR (Situation, Task, Action, Result) method to structure your response
- Clearly outline the equipment failure and its impact on operations
- Detail the steps you took to diagnose the issue
- Explain the solution you implemented and its effectiveness
- Share any follow-up measures you took to prevent future failures
What not to say
- Avoid vague descriptions of the failure without specifics
- Don't focus solely on the technical details without mentioning teamwork or communication
- Refrain from minimizing the impact of the failure or the urgency of the situation
- Avoid taking full credit if others contributed to the resolution
Example answer
“At GE Aviation, we experienced a critical failure in a testing rig that halted production. I quickly assessed the situation, identified a faulty sensor, and led a team to replace it within two hours. After troubleshooting, we implemented a regular maintenance check for all sensors, which led to a 30% reduction in similar failures over the next quarter. This experience reinforced the importance of rapid response and preventive measures.”
Skills tested
Question type
4.2. How do you ensure compliance with safety standards and regulations when working with equipment?
Introduction
This question gauges your understanding of safety protocols and regulatory requirements, which are paramount in the role of Lead Equipment Specialist.
How to answer
- Discuss your familiarity with relevant safety standards (e.g., OSHA, ANSI)
- Explain how you integrate safety training into your team's routine
- Detail your process for conducting safety audits and inspections
- Share examples of how you have addressed safety violations or concerns
- Mention any improvements you've implemented to enhance safety culture
What not to say
- Indicating that safety is solely the responsibility of management
- Failing to provide specific examples of safety initiatives you've led
- Ignoring the importance of continuous training and education
- Downplaying the significance of compliance in daily operations
Example answer
“In my role at Honeywell, I prioritized safety by conducting monthly training sessions on OSHA regulations and integrating safety checks into our equipment maintenance schedules. During a routine audit, I discovered a compliance gap in our equipment usage logs and worked with the team to rectify it, resulting in a 100% compliance rating for the next inspection. Building a culture of safety is essential, and I take that responsibility seriously.”
Skills tested
Question type
5. Equipment Manager Interview Questions and Answers
5.1. Describe a time when you had to manage equipment logistics for a large project.
Introduction
This question evaluates your organizational and logistical skills, which are critical for an Equipment Manager to ensure that all necessary equipment is available and functioning for projects.
How to answer
- Use the STAR method to structure your response, detailing the Situation, Task, Action, and Result.
- Clearly explain the scope of the project and why equipment logistics was critical.
- Discuss specific challenges you faced in managing the equipment logistics.
- Highlight the strategies you implemented to ensure timely delivery and utilization of equipment.
- Quantify your results, including how your actions impacted project efficiency or cost savings.
What not to say
- Providing vague examples without specific details about your role.
- Failing to mention any challenges faced or how they were overcome.
- Taking sole credit for successes without acknowledging team contributions.
- Ignoring the importance of safety and compliance in equipment management.
Example answer
“During a major construction project at BHP Billiton, I was responsible for managing the logistics of over 50 pieces of heavy machinery. We faced a significant challenge when a key piece of equipment broke down just before the project started. I coordinated with suppliers for a quick repair while simultaneously sourcing a backup. As a result, we were able to commence work on schedule, and my efforts contributed to a 15% reduction in project delays compared to previous projects.”
Skills tested
Question type
5.2. How do you ensure that all equipment is properly maintained and compliant with safety regulations?
Introduction
This question assesses your knowledge and approach to equipment maintenance, safety compliance, and risk management, which are vital responsibilities of an Equipment Manager.
How to answer
- Describe your systematic approach to equipment maintenance, including scheduling and tracking.
- Explain how you stay updated with safety regulations and ensure compliance.
- Discuss the importance of training staff on equipment safety and proper usage.
- Provide examples of how you have implemented safety measures and maintenance protocols.
- Highlight any metrics or improvements in safety or equipment uptime you've achieved.
What not to say
- Suggesting that maintenance is not a priority or can be neglected.
- Failing to mention specific safety regulations or compliance standards.
- Offering vague answers about training without specific examples.
- Overlooking the importance of documentation and record-keeping.
Example answer
“At my previous role with Downer EDI, I implemented a comprehensive maintenance schedule for all equipment, ensuring compliance with Australian safety standards. This included regular inspections, training sessions for operators, and maintaining detailed logs of all maintenance actions. As a result, we experienced a 20% reduction in equipment failures and improved safety compliance ratings during audits.”
Skills tested
Question type
Similar Interview Questions and Sample Answers
Simple pricing, powerful features
Upgrade to Himalayas Plus and turbocharge your job search.
Himalayas
Himalayas Plus
Himalayas Max
Find your dream job
Sign up now and join over 100,000 remote workers who receive personalized job alerts, curated job matches, and more for free!
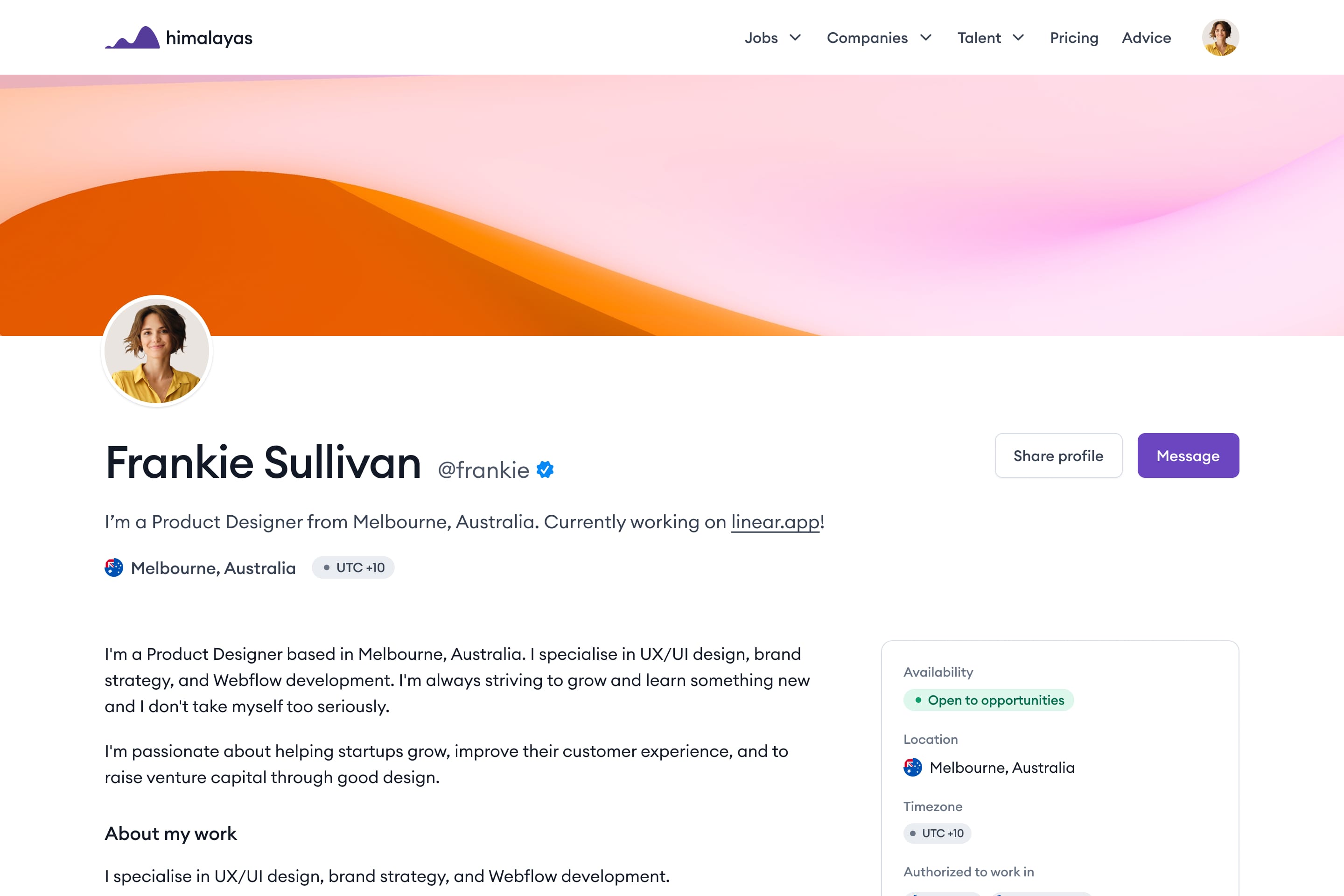