6 Diesel Technician Interview Questions and Answers
Diesel Technicians specialize in diagnosing, repairing, and maintaining diesel-powered vehicles and equipment. They work on engines, transmissions, and other systems to ensure optimal performance and safety. At entry levels, technicians focus on basic maintenance and learning the trade, while senior and master technicians handle complex diagnostics, mentor junior staff, and may oversee shop operations. Need to practice for an interview? Try our AI interview practice for free then unlock unlimited access for just $9/month.
Unlimited interview practice for $9 / month
Improve your confidence with an AI mock interviewer.
No credit card required
1. Apprentice Diesel Technician Interview Questions and Answers
1.1. Can you describe a time when you diagnosed a mechanical issue in a diesel engine?
Introduction
This question assesses your technical knowledge and problem-solving skills, which are crucial for an apprentice diesel technician to effectively contribute to the team.
How to answer
- Use the STAR method to structure your response: Situation, Task, Action, Result.
- Describe the specific diesel engine issue you encountered.
- Explain the diagnostic tools or methods you used to identify the problem.
- Detail the steps you took to resolve the issue and any collaboration with colleagues.
- Share the outcome, including any improvements or lessons learned.
What not to say
- Providing an example unrelated to diesel engines.
- Failing to explain the diagnostic process clearly.
- Taking sole credit without acknowledging teamwork.
- Not discussing the final results or impact of your solution.
Example answer
“During my internship at a local garage, I noticed a diesel engine was experiencing power loss. I used a diagnostic scanner to check for error codes and discovered a fuel delivery issue. I worked with my supervisor to replace the fuel filter and clean the injectors. This restored the engine's performance and taught me the importance of thorough diagnostics.”
Skills tested
Question type
1.2. How do you stay updated on the latest diesel technology and maintenance techniques?
Introduction
This question evaluates your commitment to continuous learning and professional development, which is essential in the rapidly evolving field of diesel mechanics.
How to answer
- Mention specific resources you use, such as online courses, workshops, or technical manuals.
- Discuss any automotive or diesel technician associations you belong to.
- Explain how you apply what you learn to your work or studies.
- Share examples of how staying updated has benefited your skills or work.
- Highlight your enthusiasm for learning and adapting to new technologies.
What not to say
- Claiming you do not need to update your skills.
- Mentioning outdated resources that are no longer relevant.
- Focusing solely on hands-on experience without theoretical knowledge.
- Not providing specific examples of continued education.
Example answer
“I regularly read industry publications and follow blogs dedicated to diesel technology. Additionally, I enrolled in an online course on advanced diesel diagnostics last summer. This not only enhanced my skill set but also improved my understanding of common issues I encounter during my apprenticeship. I’m always eager to learn more through workshops and local trade shows.”
Skills tested
Question type
2. Diesel Technician Interview Questions and Answers
2.1. Can you describe a time when you diagnosed a complex issue in a diesel engine? What steps did you take to resolve it?
Introduction
This question assesses your technical expertise and problem-solving skills, both crucial for a diesel technician who often faces complex mechanical issues.
How to answer
- Use the STAR method to structure your response: Situation, Task, Action, Result.
- Clearly outline the specific symptoms and context of the engine issue.
- Detail the diagnostic tools and methods you used to identify the problem.
- Explain the steps you took to resolve the issue and the rationale behind them.
- Quantify the results, such as improved engine performance or reduced downtime.
What not to say
- Focusing only on the end result without explaining the diagnostic process.
- Neglecting to mention any challenges faced during diagnosis and resolution.
- Providing vague answers without technical details.
- Claiming sole credit without acknowledging teamwork if applicable.
Example answer
“At a fleet maintenance facility, I encountered a diesel engine that was losing power intermittently. I performed a series of tests using a diagnostic scanner and found that the fuel injectors were malfunctioning. After replacing them and recalibrating the engine, the performance improved significantly, resulting in a 20% increase in fuel efficiency and reducing the downtime for the vehicle by two days.”
Skills tested
Question type
2.2. How do you stay updated with the latest technology and techniques in diesel mechanics?
Introduction
This question evaluates your commitment to professional development and staying current with industry advancements, which is vital in a rapidly evolving field.
How to answer
- Mention specific resources you use, such as technical journals, online courses, or trade shows.
- Discuss any certifications or training programs you have completed recently.
- Explain how you apply new knowledge or techniques in your work.
- Share examples of how staying updated has positively impacted your performance.
- Highlight any professional networks or associations you are part of.
What not to say
- Indicating that you rely solely on your experience without seeking new knowledge.
- Mentioning outdated resources or practices.
- Failing to provide specific examples of professional development efforts.
- Showing a lack of enthusiasm for learning and improving.
Example answer
“I regularly read industry publications like 'Diesel Progress' and attend training workshops. Last year, I completed a certification in advanced diesel diagnostics, which helped me implement new techniques that reduced our diagnostic time by 30%. Networking with other professionals through the Diesel Technicians Association also keeps me informed about the latest trends and technologies.”
Skills tested
Question type
3. Senior Diesel Technician Interview Questions and Answers
3.1. Can you describe a challenging repair you faced with a diesel engine and how you resolved it?
Introduction
This question is important as it evaluates your technical expertise, problem-solving skills, and ability to handle complex repairs, which are crucial for a Senior Diesel Technician.
How to answer
- Provide a brief overview of the diesel engine issue you encountered
- Explain the diagnostic process you used to identify the root cause
- Detail the steps you took to resolve the issue, including any specific techniques or tools used
- Discuss the outcome and any improvements made as a result of your repair
- Reflect on what you learned from the experience and how it has influenced your technical approach since
What not to say
- Describing a simple repair that doesn't showcase your skills
- Failing to mention specific tools or techniques used
- Not quantifying the results or improvements achieved
- Not discussing the learning aspect or growth from the experience
Example answer
“At a trucking company, I faced a significant challenge when a fleet vehicle had recurring fuel injector failures. I used diagnostic software to pinpoint the issue to a faulty injector pump. After replacing it, I also implemented a preventive maintenance schedule to avoid future issues. This led to a 30% decrease in related breakdowns and improved overall fleet performance. The experience taught me the importance of thorough diagnostics and proactive maintenance.”
Skills tested
Question type
3.2. How do you stay updated with the latest diesel technology and repair techniques?
Introduction
This question assesses your commitment to continuous learning and adapting to industry advancements, which is vital for a Senior Diesel Technician.
How to answer
- Mention specific resources you use to keep your knowledge current, such as trade journals, online courses, and workshops
- Discuss any certifications or training programs you have completed recently
- Share how you incorporate new techniques or technologies into your work
- Explain the importance of staying updated in your role
- Highlight any mentorship or training roles you take on to pass knowledge to others
What not to say
- Claiming you rely solely on past experience without seeking new knowledge
- Not providing specific examples of resources or courses
- Indicating a lack of interest in advancing your skills
- Failing to mention how this knowledge translates into your practical work
Example answer
“I regularly read industry publications like 'Diesel Progress' and participate in webinars hosted by the National Institute for Diesel Mechanics. I recently completed a certification in advanced diesel diagnostics, which taught me new techniques that I have already applied to improve troubleshooting efficiency. Staying current is crucial in this field, and I also share insights with my team to enhance our collective skills.”
Skills tested
Question type
4. Lead Diesel Technician Interview Questions and Answers
4.1. Can you describe a complex diesel engine repair you successfully completed and the steps you took?
Introduction
This question assesses your technical expertise and problem-solving abilities, which are critical for a Lead Diesel Technician role.
How to answer
- Use the STAR (Situation, Task, Action, Result) method to structure your response
- Clearly outline the specific diesel engine issue you encountered
- Detail the diagnostic tools and methods you used to identify the problem
- Explain the repair process step-by-step, including any challenges faced
- Quantify the outcome, such as improved performance or reduced downtime
What not to say
- Focusing too much on minor details without explaining the overall impact
- Neglecting to mention collaboration with other team members or departments
- Providing an answer that lacks specific metrics or results
- Avoiding discussion of any challenges faced during the repair
Example answer
“At a local truck service center, I was tasked with diagnosing a recurring issue in a diesel truck's engine that caused significant power loss. After running a series of diagnostics using advanced testing equipment, I identified a faulty fuel injector. I led the team in replacing all the injectors, ensuring we calibrated the engine post-repair. This not only restored the truck's performance but also reduced its fuel consumption by 15%.”
Skills tested
Question type
4.2. How do you prioritize safety and compliance in your daily work as a lead technician?
Introduction
This question evaluates your understanding of safety protocols and compliance regulations, which are essential in the automotive service industry.
How to answer
- Discuss your knowledge of safety regulations specific to diesel mechanics
- Explain how you implement safety measures in your daily tasks
- Share examples of how you have trained or mentored others in safety practices
- Detail any specific compliance standards you have worked with, such as environmental regulations
- Highlight the importance of safety in maintaining team morale and operational efficiency
What not to say
- Suggesting that safety is secondary to completing tasks quickly
- Failing to provide specific examples or experiences related to safety
- Ignoring the importance of compliance with industry standards
- Overlooking the role of safety in team dynamics and performance
Example answer
“In my role at a fleet maintenance facility, I prioritize safety by conducting daily briefings on protective measures and compliance with regulations. I also developed a safety checklist for all maintenance tasks, which has helped reduce workplace accidents by 30% over the past year. Additionally, I lead workshops on proper handling of hazardous materials to ensure that the entire team is aware of best practices.”
Skills tested
Question type
5. Master Diesel Technician Interview Questions and Answers
5.1. Can you describe a complex diesel engine issue you diagnosed and repaired? What steps did you take to resolve it?
Introduction
This question assesses your technical expertise and problem-solving abilities. As a Master Diesel Technician, your capacity to diagnose and fix intricate problems is crucial for maintaining vehicle performance and safety.
How to answer
- Use the STAR method (Situation, Task, Action, Result) to structure your response
- Start by describing the specific issue and its context, including the effects on the vehicle's performance
- Detail the diagnostic tools and techniques you employed to identify the root cause of the problem
- Explain the repair process you undertook, including any challenges faced
- Share the results, focusing on improvements in performance or efficiency and any feedback from the vehicle owner
What not to say
- Providing vague descriptions without specific technical details
- Focusing solely on the final result without explaining the diagnostic process
- Neglecting to mention any mistakes made or lessons learned during the repair
- Avoiding the mention of teamwork or collaboration if applicable
Example answer
“Last year, I worked on a heavy-duty truck that exhibited frequent stalling. After initial checks, I used an advanced diagnostic scanner to reveal a faulty fuel injector. I replaced the injector and cleaned the fuel system, which drastically improved engine performance and eliminated stalling. The owner reported a 15% increase in fuel efficiency post-repair, underscoring the importance of thorough diagnostics.”
Skills tested
Question type
5.2. How do you stay current with the latest diesel technology and repair techniques?
Introduction
This question gauges your commitment to professional development and your ability to adapt to evolving technologies in diesel engineering.
How to answer
- Discuss specific resources you utilize, such as workshops, online courses, and industry publications
- Mention any certifications or training you have pursued to enhance your skills
- Share how you apply new knowledge to your work and improve your repair processes
- Describe your involvement in professional networks or communities
- Emphasize the importance of staying updated in a rapidly changing field
What not to say
- Claiming you do not need to learn new technologies
- Providing generic answers without specifics on resources or actions taken
- Overlooking the importance of continuous learning in your profession
- Failing to mention any proactive steps you’ve taken toward professional development
Example answer
“I subscribe to industry journals like Diesel Progress and attend workshops at local trade schools. Recently, I completed a certification in common rail diesel injection systems, which has helped me handle modern fuel systems more efficiently. I also participate in online forums where technicians share the latest trends and techniques, allowing me to remain proactive in my learning.”
Skills tested
Question type
6. Diesel Shop Supervisor Interview Questions and Answers
6.1. How do you ensure that safety protocols are followed in the shop?
Introduction
This question is crucial for a Diesel Shop Supervisor as safety is paramount in automotive environments, especially when working with heavy machinery.
How to answer
- Start by discussing your understanding of relevant safety regulations and protocols
- Explain how you communicate these protocols to your team
- Detail any training programs or workshops you have implemented
- Share examples of how you monitor compliance and address violations
- Highlight the importance of fostering a safety-first culture within the team
What not to say
- Suggesting that safety protocols are not a priority
- Failing to provide specific examples of safety measures you’ve implemented
- Ignoring the role of team engagement in safety practices
- Mentioning only theoretical knowledge without practical application
Example answer
“In my previous role at a diesel repair shop, I ensured compliance with safety protocols by instituting a comprehensive training program for new hires. We held monthly safety meetings to review procedures, and I established a buddy system for ongoing mentorship. Last year, we had zero safety incidents, which I attribute to this proactive approach and the team's commitment to a safety-first culture.”
Skills tested
Question type
6.2. Can you describe a time you had to resolve a conflict between team members?
Introduction
Conflict resolution is key for a supervisor, as maintaining a harmonious and productive work environment directly impacts shop efficiency.
How to answer
- Use the STAR method to structure your response
- Describe the context of the conflict and the individuals involved
- Explain your approach to mediating the situation
- Discuss the resolution and how you ensured it was lasting
- Highlight any lessons learned or changes made to prevent future conflicts
What not to say
- Avoiding responsibility for handling conflicts
- Describing a situation without focusing on your role
- Not emphasizing the importance of team dynamics
- Failing to mention follow-up actions taken post-resolution
Example answer
“In my previous position at a diesel service center, two technicians were in conflict over tool usage. I first met with each individually to understand their perspectives. Then, I facilitated a meeting where both could express their concerns and collaboratively establish a tool-sharing schedule. This not only resolved the immediate issue but also improved communication, as they agreed to check in weekly. The team atmosphere became more cooperative as a result.”
Skills tested
Question type
6.3. What strategies do you use to manage shop workflow and productivity effectively?
Introduction
Understanding workflow management is essential for a Diesel Shop Supervisor to ensure efficiency and meet customer demands.
How to answer
- Describe any specific tools or software you use for workflow management
- Explain how you prioritize tasks and allocate resources
- Discuss your approach to monitoring progress and addressing bottlenecks
- Share examples of how you have improved shop productivity in the past
- Highlight your ability to adapt strategies based on shop needs and team feedback
What not to say
- Suggesting that workflow management isn’t important
- Providing vague answers without concrete examples
- Ignoring the role of team input in workflow decisions
- Failing to mention any metrics or results from your strategies
Example answer
“At my last job in a diesel repair shop, I implemented a scheduling software that allowed us to track repairs in real-time. I prioritized tasks based on urgency and customer needs, and held daily huddles to update the team on workflow. This approach reduced our turnaround time by 20% and improved our customer satisfaction ratings significantly. Adaptability was key, as I regularly adjusted our strategies based on team feedback.”
Skills tested
Question type
Similar Interview Questions and Sample Answers
Simple pricing, powerful features
Upgrade to Himalayas Plus and turbocharge your job search.
Himalayas
Himalayas Plus
Himalayas Max
Find your dream job
Sign up now and join over 100,000 remote workers who receive personalized job alerts, curated job matches, and more for free!
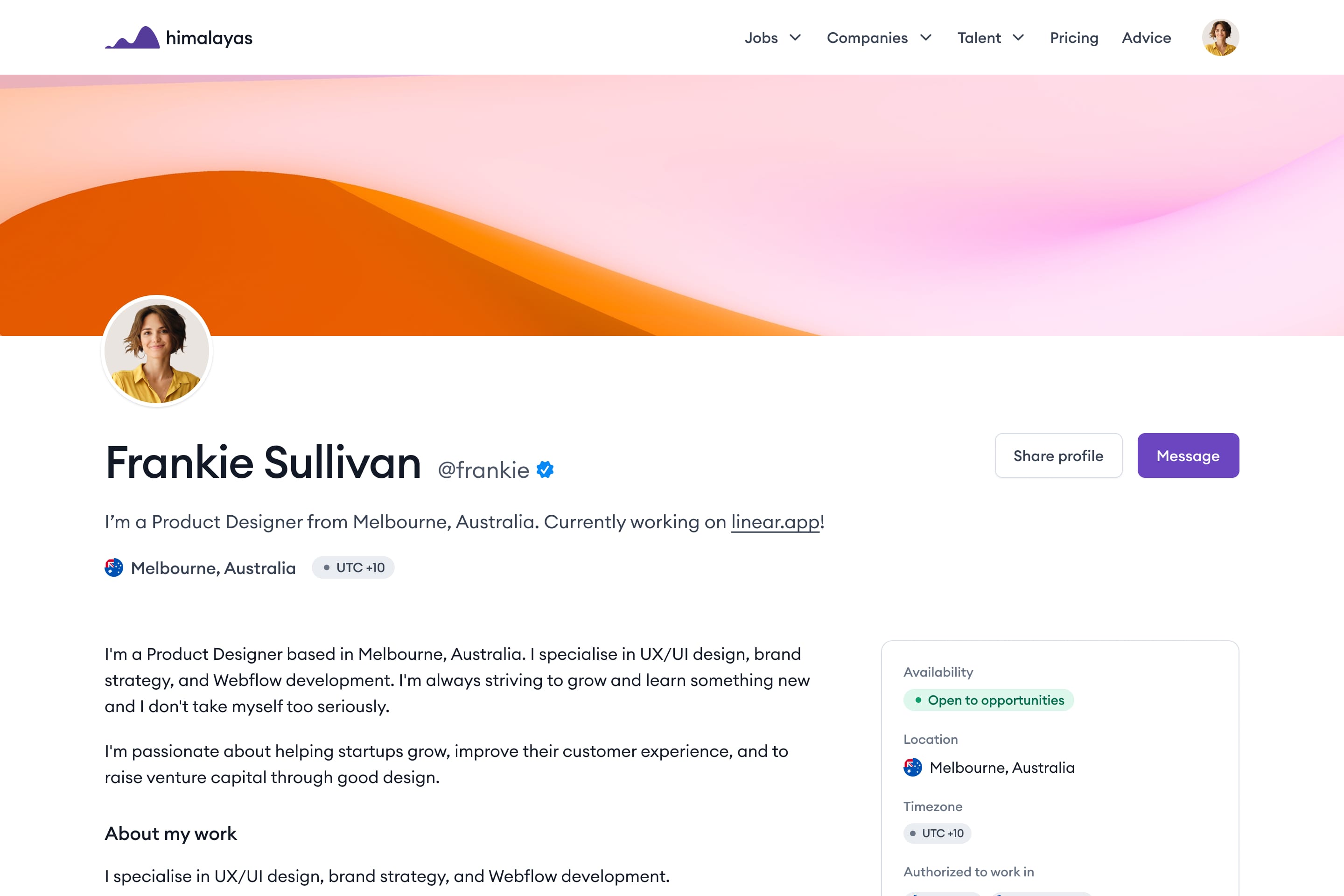