5 Cherry Picker Operator Interview Questions and Answers
Cherry Picker Operators are responsible for operating specialized forklifts, known as cherry pickers, to retrieve and place items stored at elevated heights in warehouses or storage facilities. They ensure safety, efficiency, and accuracy in handling inventory. Entry-level operators focus on learning equipment operation and safety protocols, while senior and lead operators may oversee teams, train new employees, and handle more complex tasks. Need to practice for an interview? Try our AI interview practice for free then unlock unlimited access for just $9/month.
Unlimited interview practice for $9 / month
Improve your confidence with an AI mock interviewer.
No credit card required
1. Entry-Level Cherry Picker Operator Interview Questions and Answers
1.1. What safety protocols would you follow while operating a cherry picker?
Introduction
This question is crucial for understanding your awareness of safety procedures, which is paramount in operating heavy machinery like cherry pickers.
How to answer
- Mention the importance of personal protective equipment (PPE) like helmets and harnesses
- Discuss the need for pre-operation inspections of the equipment
- Explain the significance of understanding the worksite and potential hazards
- Include the importance of following manufacturer's guidelines and safety regulations
- Highlight the necessity of communication with team members while operating
What not to say
- Ignoring the importance of safety and just focusing on operating the machine
- Providing vague responses without specific protocols
- Suggesting that safety protocols can be overlooked for efficiency
- Failing to mention teamwork or communication in a safety context
Example answer
“As a cherry picker operator, my first priority would be safety. I would ensure I'm wearing the appropriate PPE, conduct a thorough inspection of the cherry picker before use, and familiarize myself with the worksite to identify any potential hazards. I would also communicate clearly with my team members to ensure everyone is aware of my movements, and adhere strictly to the manufacturer's guidelines and safety regulations.”
Skills tested
Question type
1.2. Can you describe a time when you had to work as part of a team to complete a task?
Introduction
Teamwork is essential in many roles, especially in environments where heavy machinery is operated. This question assesses your ability to collaborate effectively.
How to answer
- Use the STAR method to structure your response (Situation, Task, Action, Result)
- Describe the context and the specific task you were working on
- Highlight your role in the team and how you contributed
- Discuss the outcome of the teamwork and any lessons learned
- Emphasize the importance of communication and collaboration
What not to say
- Focusing on individual achievements without acknowledging the team
- Describing a negative experience without showing how you contributed positively
- Failing to mention specific actions you took as part of the team
- Being vague about the outcome of the teamwork
Example answer
“In my previous job at a warehouse, we had to prepare for a large shipment on short notice. As part of a team of five, I coordinated with my colleagues to delegate tasks efficiently. I was responsible for ensuring that all items were correctly labeled and packed. By working together and communicating effectively, we completed the task ahead of schedule, which improved our team's efficiency and helped maintain client satisfaction.”
Skills tested
Question type
2. Cherry Picker Operator Interview Questions and Answers
2.1. Can you describe a time when you had to operate a cherry picker in challenging weather conditions?
Introduction
This question assesses your ability to maintain safety and efficiency while operating heavy machinery under less-than-ideal conditions, which is crucial for a Cherry Picker Operator.
How to answer
- Start by explaining the specific weather conditions you faced.
- Detail your approach to ensuring safety for yourself and your team.
- Describe any adjustments you made to your operation techniques.
- Highlight the importance of following safety protocols and regulations.
- Share the outcome of your actions and any lessons learned.
What not to say
- Downplaying the importance of safety protocols.
- Blaming the weather for any mistakes or accidents.
- Focusing solely on the technical aspects without mentioning safety.
- Failing to provide a specific example or situation.
Example answer
“While working for a construction company in Toronto, I had to operate the cherry picker during a heavy rainfall. I ensured I was familiar with the equipment’s limitations in wet conditions and adjusted my operation to avoid slippery surfaces. I communicated closely with my team to ensure everyone was aware of the potential hazards. Ultimately, we completed the task without incident, and I learned the importance of adherence to safety guidelines in adverse conditions.”
Skills tested
Question type
2.2. What safety procedures do you follow when operating a cherry picker?
Introduction
This question evaluates your knowledge of safety protocols, which are vital for preventing accidents and ensuring a safe work environment.
How to answer
- List specific safety procedures you adhere to before, during, and after operation.
- Discuss the importance of personal protective equipment (PPE).
- Explain how you perform equipment checks and maintenance.
- Mention how you communicate with ground crew and other team members.
- Share your experience with safety training or certifications.
What not to say
- Neglecting to mention specific PPE or equipment checks.
- Suggesting that safety procedures can be skipped if you're experienced.
- Failing to acknowledge the importance of teamwork in safety.
- Providing vague answers without specific protocols.
Example answer
“I always start by conducting a pre-operation inspection of the cherry picker, checking fluid levels, brakes, and emergency systems. I ensure my harness and other PPE are in place. Throughout the operation, I maintain communication with my ground crew to ensure everyone is aware of my movements. I also participate in regular safety training to stay updated on best practices. This systematic approach has helped me operate safely and effectively.”
Skills tested
Question type
3. Senior Cherry Picker Operator Interview Questions and Answers
3.1. Can you describe a situation where you had to quickly adapt to changing conditions while operating a cherry picker?
Introduction
This question assesses your adaptability and quick decision-making skills, both of which are crucial for safely operating equipment in dynamic environments.
How to answer
- Start by outlining the specific situation that required adaptation.
- Describe the unexpected changes that occurred (e.g., weather, equipment issues, changes in task priorities).
- Explain the steps you took to ensure safety and continue operations effectively.
- Highlight any communication with team members or supervisors during this time.
- Conclude with the outcome and any lessons learned from the experience.
What not to say
- Failing to provide a specific example and speaking in generalities.
- Not emphasizing safety protocols you followed during the situation.
- Ignoring the role of teamwork or communication in your response.
- Dismissing the importance of adaptability in your role.
Example answer
“Last season, while operating the cherry picker, an unexpected storm approached, causing strong winds. I immediately halted operations and communicated with my supervisor to assess the situation. We decided to secure the equipment and move to a safer location. By remaining calm and prioritizing safety, we avoided any accidents and were able to resume work quickly once conditions improved. This experience taught me the importance of staying alert and ready to adapt in the field.”
Skills tested
Question type
3.2. How do you ensure safety compliance while operating a cherry picker?
Introduction
This question is important as it measures your understanding of safety regulations and practices critical to operating heavy machinery.
How to answer
- Discuss your knowledge of relevant safety regulations (e.g., OSHA standards).
- Explain the pre-operation checks you perform before using the cherry picker.
- Detail any training or certifications you possess related to equipment operation and safety.
- Describe how you stay updated on safety practices and regulations.
- Mention any experiences where you identified and mitigated potential safety hazards.
What not to say
- Claiming safety is someone else's responsibility.
- Providing vague or generic answers without specific practices.
- Ignoring the importance of regular training or refreshers.
- Not mentioning the consequences of safety violations.
Example answer
“I prioritize safety compliance by conducting thorough pre-operation checks, ensuring the cherry picker is functioning correctly before use. I am OSHA certified and stay updated on safety practices through ongoing training and workshops. Last season, I identified a potential hazard when a colleague bypassed safety protocols, and I promptly addressed it with management, ensuring we reinforced the importance of compliance across the team. Safety is always my top priority.”
Skills tested
Question type
4. Lead Cherry Picker Operator Interview Questions and Answers
4.1. Can you describe a time when you had to troubleshoot a mechanical issue with the cherry picker during operation?
Introduction
This question assesses your technical knowledge and problem-solving skills, which are critical for ensuring safety and efficiency in your role as a lead cherry picker operator.
How to answer
- Begin with a brief description of the situation and the mechanical issue encountered
- Explain the steps you took to identify the root cause of the problem
- Detail how you resolved the issue and the outcome of your actions
- Highlight any safety measures you implemented during the troubleshooting process
- Mention any lessons learned or improvements made to prevent future issues
What not to say
- Avoid being vague about the mechanical issue or your role in resolving it
- Do not focus solely on technical jargon without explaining the context
- Refrain from taking sole credit if the resolution was a team effort
- Do not ignore the importance of safety in your response
Example answer
“While operating a cherry picker at a construction site in Paris, I noticed that the lift was not responding properly to controls. I quickly assessed the situation and realized the hydraulic fluid levels were low. I informed my supervisor and added the necessary fluid, which restored functionality. The experience reinforced my understanding of routine maintenance checks, and I now emphasize these checks with my team to prevent future problems.”
Skills tested
Question type
4.2. How do you ensure the safety of your team while working with cherry pickers?
Introduction
This question evaluates your leadership and safety management skills, which are essential for maintaining a safe working environment for your crew.
How to answer
- Discuss your approach to safety training and how you ensure all team members are properly trained
- Describe how you conduct regular safety inspections and risk assessments
- Explain your methods for communicating safety protocols to the team
- Share examples of how you foster a culture of safety among your crew
- Mention the importance of reporting near misses and learning from incidents
What not to say
- Avoid downplaying the importance of safety or suggesting it’s solely the responsibility of the safety officer
- Do not give generic answers without specific examples
- Refrain from ignoring the role of personal protective equipment (PPE) in safety
- Avoid stating that accidents are unavoidable without discussing prevention measures
Example answer
“I prioritize safety by conducting weekly safety briefings with my team where we discuss proper use of cherry pickers and review any incidents. I also ensure all crew members complete their safety training before operating equipment. Recently, I implemented a buddy system where team members check each other's safety gear before starting work, which has significantly reduced our incident rate. This proactive approach fosters a culture of safety within the team.”
Skills tested
Question type
5. Warehouse Equipment Specialist Interview Questions and Answers
5.1. Describe a time when you identified a safety hazard in the warehouse and how you addressed it.
Introduction
This question is important because it assesses your ability to prioritize safety and proactively manage risks in a warehouse environment, which is critical for a Warehouse Equipment Specialist.
How to answer
- Use the STAR method (Situation, Task, Action, Result) to structure your response.
- Clearly describe the safety hazard you encountered and the potential risks it posed.
- Detail the steps you took to address the hazard, including any communication with team members or management.
- Discuss any training or changes in procedure you implemented as a result.
- Share the outcomes, such as improved safety metrics or feedback from your team.
What not to say
- Ignoring the importance of safety protocols.
- Providing vague responses without specific actions taken.
- Downplaying the severity of the hazard.
- Failing to mention collaboration with others.
Example answer
“While working at Amazon, I noticed that a section of the loading area was cluttered with unused equipment, creating a tripping hazard. I immediately reported it to my supervisor, and we organized a team to clear the area and implement a new storage solution. This not only improved safety but also increased efficiency in our loading process by 15%.”
Skills tested
Question type
5.2. How do you ensure that all warehouse equipment is maintained and in good working condition?
Introduction
This question evaluates your knowledge of equipment maintenance protocols and your ability to prevent downtime, which is essential for maintaining operational efficiency in a warehouse.
How to answer
- Explain your routine maintenance schedule and the importance of regular inspections.
- Discuss how you track equipment performance and maintenance history.
- Mention any specific tools or software you use for equipment management.
- Describe how you communicate maintenance needs to your team or management.
- Highlight any past experiences where your maintenance practices improved equipment reliability.
What not to say
- Suggesting that maintenance is not a priority.
- Failing to mention systematic approaches or tools used.
- Ignoring the importance of team collaboration in maintenance tasks.
- Providing an unclear or overly complex maintenance process.
Example answer
“At DHL, I implemented a weekly inspection schedule for all equipment, using a maintenance tracking software to log issues and schedule repairs. This proactive approach reduced equipment downtime by 20% and ensured our operations ran smoothly, as the team always had the right tools ready when they needed them.”
Skills tested
Question type
5.3. Imagine a scenario where a critical piece of equipment breaks down during peak hours. How would you handle the situation?
Introduction
This situational question assesses your crisis management and problem-solving skills under pressure, which are vital in a fast-paced warehouse environment.
How to answer
- Describe your immediate response to assess the situation.
- Discuss how you would communicate with your team and management.
- Explain your approach to finding a quick solution, such as arranging for repairs or finding alternative equipment.
- Mention how you would mitigate the impact on operations and keep the workflow moving.
- Share any lessons learned from past experiences that would guide your actions.
What not to say
- Panic or indecisiveness in the face of equipment failure.
- Failing to communicate with team members or management.
- Ignoring the importance of having contingency plans.
- Providing an unrealistic or overly simplistic response to a complex problem.
Example answer
“During peak season at Walmart, our main forklift broke down unexpectedly. I immediately assessed the situation and informed my supervisor while coordinating the team to safely move items manually. I contacted our maintenance team to expedite repairs and arranged for a backup forklift from another location. This response minimized disruption and we maintained our productivity levels, which was crucial during such a busy time.”
Skills tested
Question type
Similar Interview Questions and Sample Answers
Simple pricing, powerful features
Upgrade to Himalayas Plus and turbocharge your job search.
Himalayas
Himalayas Plus
Himalayas Max
Find your dream job
Sign up now and join over 100,000 remote workers who receive personalized job alerts, curated job matches, and more for free!
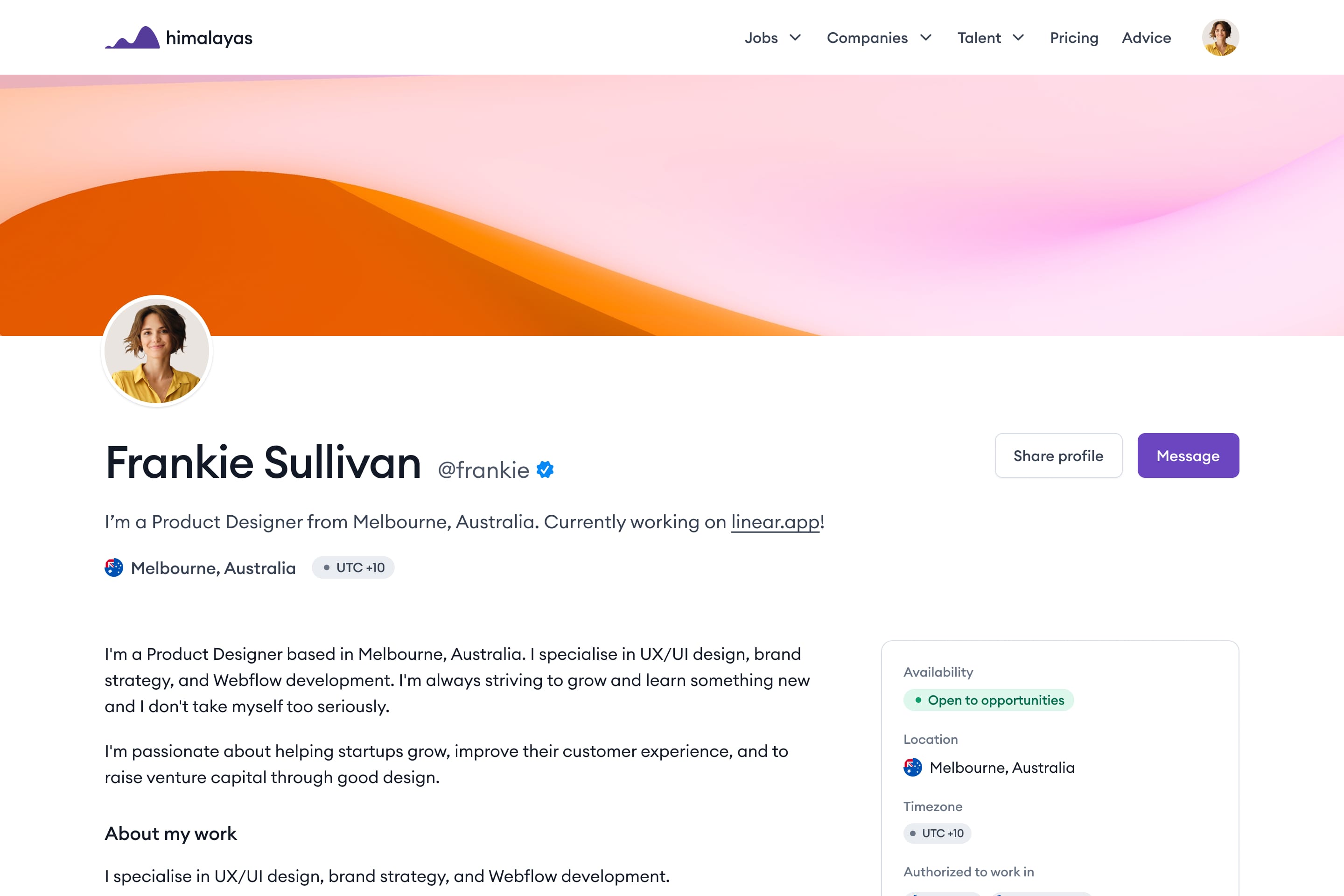