7 Calibration Technician Interview Questions and Answers
Calibration Technicians are responsible for ensuring the accuracy and precision of measurement instruments and equipment. They perform tests, adjustments, and repairs to maintain compliance with industry standards and regulations. Junior technicians typically assist with basic calibration tasks, while senior and lead roles involve overseeing complex calibrations, mentoring team members, and managing calibration processes and documentation. Need to practice for an interview? Try our AI interview practice for free then unlock unlimited access for just $9/month.
Unlimited interview practice for $9 / month
Improve your confidence with an AI mock interviewer.
No credit card required
1. Junior Calibration Technician Interview Questions and Answers
1.1. Can you describe a time when you identified a calibration issue and how you resolved it?
Introduction
This question assesses your problem-solving skills and attention to detail, which are critical for a Junior Calibration Technician role.
How to answer
- Begin by briefly describing the context and the equipment involved.
- Explain how you identified the calibration issue, including any specific tests or observations.
- Detail the steps you took to resolve the issue, emphasizing your methodical approach.
- Discuss any tools or techniques you used to ensure accurate calibration.
- Conclude with the outcome, including any improvements in measurement accuracy.
What not to say
- Failing to provide a specific example or being too vague.
- Blaming others for the calibration issue without taking personal responsibility.
- Neglecting to mention the tools or techniques used.
- Omitting the outcome or results of your actions.
Example answer
“During my internship at Tata Technologies, I noticed that one of the pressure gauges was reading inconsistently. I performed a series of tests to compare its readings against a calibrated standard. Upon identifying the discrepancy, I recalibrated the gauge using the appropriate adjustment procedures and tools. After re-testing, the gauge showed a significant improvement in accuracy, which helped the team maintain compliance with our quality standards.”
Skills tested
Question type
1.2. What steps would you take to ensure compliance with calibration standards in your work?
Introduction
This question evaluates your understanding of calibration standards and your commitment to quality assurance, essential for ensuring accurate measurements.
How to answer
- Mention relevant calibration standards (e.g., ISO 17025) that apply to your role.
- Describe how you would stay updated on these standards and any changes.
- Explain your process for documenting calibration activities and results.
- Discuss the importance of regular training and skills development.
- Highlight your approach to maintaining equipment and ensuring it meets standards.
What not to say
- Not mentioning any specific calibration standards.
- Indicating a lack of awareness of the importance of documentation.
- Suggesting that compliance is not a priority.
- Failing to address the importance of ongoing training.
Example answer
“To ensure compliance with calibration standards, I would familiarize myself with ISO 17025 and any relevant internal procedures. I would keep detailed records of all calibration activities and results to maintain transparency and accountability. Regular training sessions would be essential to stay updated on best practices. Additionally, I would establish a routine maintenance schedule for all calibration equipment, ensuring that they are always in optimal working condition.”
Skills tested
Question type
2. Calibration Technician Interview Questions and Answers
2.1. Can you describe a time when you identified a calibration issue that could have led to significant problems?
Introduction
This question assesses your attention to detail and problem-solving skills, which are crucial for any Calibration Technician. Identifying calibration issues early can prevent costly errors or equipment failures.
How to answer
- Start with a brief overview of the situation and the equipment involved
- Describe how you discovered the calibration issue, including any data analysis or testing methods used
- Explain the steps you took to resolve the issue and any adjustments made to the calibration process
- Quantify the impact of your actions, such as improved accuracy or reduced downtime
- Discuss any follow-up actions or changes to procedures to prevent future issues
What not to say
- Describing a situation where you ignored a calibration issue
- Focusing only on technical aspects without explaining your thought process
- Failing to provide a clear outcome or impact of your actions
- Not mentioning team collaboration if applicable
Example answer
“At Bombardier, I noticed a recurring calibration drift in one of our critical measuring instruments. By analyzing historical data, I pinpointed the issue to a specific environmental factor affecting readings. I adjusted the calibration procedures to account for this variable, leading to a 20% improvement in measurement accuracy and preventing potential production delays.”
Skills tested
Question type
2.2. What calibration standards are you familiar with, and how do you ensure compliance?
Introduction
This question evaluates your knowledge of industry standards and your ability to maintain compliance, which is essential for Calibration Technicians working in regulated environments.
How to answer
- List specific standards relevant to your experience, such as ISO 17025 or ASTM standards
- Explain your process for staying updated with changes in calibration standards
- Describe any tools or software you use to ensure compliance
- Discuss how you document your calibration processes and results
- Mention any training or certifications you've achieved related to calibration standards
What not to say
- Claiming familiarity with standards without specifics
- Suggesting compliance is not a priority in your work
- Failing to mention documentation or record-keeping practices
- Ignoring ongoing education in calibration standards
Example answer
“I am well-versed in ISO 17025 standards and actively monitor updates through industry newsletters and training sessions. At my previous role with Siemens, I implemented a digital tracking system for calibration records that ensured compliance and improved our audit readiness. Regular training sessions helped our team stay compliant with evolving standards.”
Skills tested
Question type
3. Senior Calibration Technician Interview Questions and Answers
3.1. Can you describe your experience with calibration tools and equipment, and how you ensure they are always accurate?
Introduction
This question assesses your technical expertise in calibration processes and your attention to detail, which are crucial for a Senior Calibration Technician role.
How to answer
- Start by mentioning specific calibration tools and equipment you have experience with
- Explain the procedures you follow for calibrating various instruments
- Detail how you verify the accuracy of the tools before and after calibration
- Mention any standards or regulations you adhere to, such as ISO 17025
- Highlight any troubleshooting methods you use when calibration results are unsatisfactory
What not to say
- Vague responses without specific examples of tools or equipment
- Downplaying the importance of accuracy in calibration
- Not mentioning adherence to industry standards or protocols
- Failing to describe any problem-solving techniques
Example answer
“In my previous role at BHP, I regularly calibrated pressure gauges and flow meters using manual and automated calibration tools. I followed a rigorous protocol to ensure accuracy, including pre-calibration checks with traceable standards and post-calibration verification with control samples. I also adhered to ISO 17025 standards, which helped maintain the integrity of our results, and I implemented a troubleshooting process for any discrepancies that arose during calibration.”
Skills tested
Question type
3.2. Describe a challenging calibration project you worked on and how you overcame any obstacles.
Introduction
This question evaluates your problem-solving skills and ability to manage challenges effectively in calibration projects.
How to answer
- Use the STAR method (Situation, Task, Action, Result) to structure your response
- Clearly describe the challenge you faced and its implications
- Detail the steps you took to address the challenge, including collaboration with team members if applicable
- Explain the final outcome and any lessons learned from the experience
- Highlight your ability to adapt and remain focused under pressure
What not to say
- Focusing on the problem rather than the actions taken to solve it
- Not providing a clear outcome or results from the situation
- Neglecting to mention teamwork or collaboration where relevant
- Avoiding discussion of lessons learned or future applications
Example answer
“At Rio Tinto, I was tasked with calibrating a set of sensors used in a critical environmental monitoring project. Midway through, we discovered that some sensors were consistently providing erroneous readings due to environmental interference. I organized a team meeting to brainstorm solutions and implemented a new shielding technique that minimized interference. As a result, we were able to complete the project on time, and I learned the importance of adaptability and teamwork in overcoming unexpected challenges.”
Skills tested
Question type
4. Lead Calibration Technician Interview Questions and Answers
4.1. Can you describe a time when you had to troubleshoot a calibration issue with a critical piece of equipment?
Introduction
This question assesses your technical problem-solving skills and your ability to handle high-pressure situations, which are crucial for a Lead Calibration Technician.
How to answer
- Use the STAR method to structure your response, focusing on the Situation, Task, Action, and Result.
- Clearly explain the calibration issue and its potential impact on operations.
- Detail the steps you took to diagnose the problem, including any tools or methods used.
- Describe the solution you implemented and the outcome it achieved.
- Reflect on any lessons learned from the experience that could improve future calibration processes.
What not to say
- Providing vague descriptions without specific technical details.
- Blaming others for the issue without taking responsibility.
- Neglecting to mention the importance of team collaboration in solving the problem.
- Failing to discuss the outcome or improvement achieved after your intervention.
Example answer
“At Siemens, we faced a critical calibration issue with a temperature sensor on a manufacturing line that was causing inconsistent product quality. I led a team to conduct a thorough investigation, using precision measurement tools to identify that the calibration was off due to a sensor drift. We recalibrated the equipment and implemented a more frequent maintenance schedule. This reduced downtime by 30% and improved overall product quality significantly. The experience taught me the importance of proactive maintenance and team communication.”
Skills tested
Question type
4.2. How do you ensure compliance with calibration standards and regulations in your team?
Introduction
This question evaluates your knowledge of industry standards and your leadership in maintaining compliance, which is essential for a Lead Calibration Technician.
How to answer
- Discuss specific calibration standards relevant to your industry (e.g., ISO 17025).
- Describe your methods for training team members on compliance procedures.
- Explain how you monitor and assess compliance within your team.
- Share examples of how you have successfully implemented changes to improve compliance.
- Highlight the importance of maintaining accurate records and documentation.
What not to say
- Indicating that compliance is not a priority for your team.
- Focusing solely on personal knowledge without mentioning team involvement.
- Ignoring the consequences of non-compliance.
- Failing to provide concrete examples of compliance enforcement.
Example answer
“In my role at Bosch, I ensured compliance with ISO 17025 by conducting regular training sessions for my team on the latest standards. I implemented a digital tracking system for calibration records, which allowed us to monitor compliance in real-time. Additionally, I performed quarterly audits to identify areas for improvement. This proactive approach led to a 20% reduction in compliance-related issues over the past year, reinforcing our commitment to quality and safety.”
Skills tested
Question type
5. Calibration Specialist Interview Questions and Answers
5.1. Can you describe a challenging calibration issue you encountered and how you resolved it?
Introduction
This question assesses your technical problem-solving abilities and your experience with calibration processes, which are critical for a Calibration Specialist's role.
How to answer
- Begin with a clear description of the calibration issue and its context
- Explain the steps you took to diagnose the problem
- Detail the resolution process, including any tools or techniques used
- Share the outcome and how it benefited the project or organization
- Reflect on what you learned from the experience
What not to say
- Vaguely describing a problem without specific details
- Failing to mention the resolution process
- Not discussing the impact of the resolution
- Ignoring lessons learned from the experience
Example answer
“At Mitsubishi Electric, I faced a calibration issue with precision measuring instruments that were consistently giving inaccurate readings. I performed a systematic analysis and discovered that environmental factors were affecting the measurements. By adjusting the calibration process to control for temperature and humidity variations, we improved measurement accuracy by 30%. This experience reinforced the importance of considering external factors in calibration.”
Skills tested
Question type
5.2. What calibration standards and procedures are you familiar with, and how do you ensure compliance?
Introduction
This question evaluates your knowledge of industry standards and your ability to maintain compliance, which is essential for ensuring quality and accuracy in calibration work.
How to answer
- List specific calibration standards relevant to your experience, such as ISO 9001 or ISO/IEC 17025
- Explain your process for staying updated on changes to these standards
- Detail steps you take to ensure compliance during calibration activities
- Provide examples of how you’ve implemented standard operating procedures
- Discuss the importance of documentation and traceability in your work
What not to say
- Claiming to be unfamiliar with key industry standards
- Providing a generic response without specific examples
- Neglecting to mention the importance of compliance
- Overlooking the role of documentation in calibration
Example answer
“I am well-versed in ISO/IEC 17025 and ensure compliance by regularly reviewing the latest updates. At my previous position at Sony, I implemented a quality management system that adhered to these standards, which included regular audits and staff training. By maintaining detailed documentation, we achieved a 100% compliance rate during external audits.”
Skills tested
Question type
6. Calibration Supervisor Interview Questions and Answers
6.1. Can you explain your approach to ensuring the accuracy and reliability of calibration processes in a manufacturing environment?
Introduction
This question assesses your technical knowledge and practical experience in managing calibration processes, which are critical for maintaining equipment accuracy and product quality.
How to answer
- Outline the steps you take to develop and implement calibration procedures
- Discuss how you ensure compliance with industry standards and regulations
- Explain your approach to training staff on calibration techniques and best practices
- Share how you monitor and evaluate calibration results to identify areas for improvement
- Describe how you handle non-conformance issues and corrective actions
What not to say
- Failing to mention specific calibration standards or procedures
- Relying solely on software or automated systems without discussing hands-on practices
- Not addressing the importance of team training and knowledge sharing
- Neglecting to mention the impact of calibration on overall product quality
Example answer
“At Bombardier, I developed a comprehensive calibration program that aligned with ISO 9001 standards. I trained my team on proper techniques, conducted regular audits, and used statistical tools to analyze calibration data. When we found recurring discrepancies, I implemented a corrective action plan that reduced errors by 30%, ensuring our equipment consistently met specifications.”
Skills tested
Question type
6.2. Describe a challenging situation you faced regarding equipment calibration and how you resolved it.
Introduction
This question aims to evaluate your problem-solving skills and ability to handle pressure while ensuring quality standards in calibration processes.
How to answer
- Use the STAR method to frame your response, highlighting the Situation, Task, Action, and Result
- Provide details about the specific calibration challenge you encountered
- Explain your thought process and the steps you took to address the issue
- Discuss the outcome and how it benefited the workflow or product quality
- Share any lessons learned or changes made to prevent future issues
What not to say
- Overemphasizing blame on others without taking responsibility
- Vague descriptions without clear actions or results
- Ignoring the importance of teamwork and communication in resolving issues
- Failing to reflect on what you learned from the experience
Example answer
“In my previous role at Siemens, we discovered that a key piece of calibration equipment was consistently producing inaccurate readings. I quickly organized a cross-functional team to investigate the issue. We identified a calibration procedure that hadn't been updated. By revising the protocol and retraining the team, we improved accuracy by 25% and established regular checks to maintain standards.”
Skills tested
Question type
7. Calibration Manager Interview Questions and Answers
7.1. Can you describe your experience with developing and implementing calibration processes in a manufacturing environment?
Introduction
This question is crucial for understanding your hands-on experience and expertise in establishing calibration protocols, which are vital for maintaining product quality and compliance in a manufacturing setting.
How to answer
- Outline the specific calibration processes you have developed or improved
- Discuss the methodologies or standards you used (e.g., ISO, ANSI)
- Explain how you ensured compliance with industry regulations
- Share examples of how your processes led to measurable improvements in quality or efficiency
- Highlight any training or mentoring you provided to team members on these processes
What not to say
- Vaguely describing processes without specifics or measurable outcomes
- Failing to mention compliance with relevant standards
- Ignoring the importance of team involvement in calibration processes
- Focusing solely on theoretical knowledge without practical application
Example answer
“In my previous role at Fiat Chrysler Automobiles, I developed a comprehensive calibration process for our assembly line equipment, aligning with ISO 9001 standards. This involved implementing regular calibration schedules and training staff on compliance. As a result, we reduced measurement errors by 30%, significantly improving product quality and customer satisfaction.”
Skills tested
Question type
7.2. Describe a challenging calibration issue you faced and how you resolved it.
Introduction
This question assesses your problem-solving and critical thinking skills, essential for a Calibration Manager who must navigate complex technical challenges.
How to answer
- Use the STAR method to structure your response
- Clearly identify the calibration issue you encountered
- Explain the root cause analysis you performed
- Discuss the steps you took to resolve the issue and implement solutions
- Share the impact of your resolution on the overall calibration process and product quality
What not to say
- Blaming others for the calibration issue without taking ownership
- Providing a solution that lacked a thorough analysis
- Failing to quantify the results or improvements made
- Describing a situation without detailing your specific contributions
Example answer
“At a previous company, we noticed a persistent discrepancy in our torque wrench calibrations. I conducted a root cause analysis that revealed improper storage conditions were affecting precision. I implemented a new storage protocol and retrained the team on proper handling techniques. As a result, we improved the accuracy of our torque measurements by 25%, enhancing product reliability.”
Skills tested
Question type
Similar Interview Questions and Sample Answers
Simple pricing, powerful features
Upgrade to Himalayas Plus and turbocharge your job search.
Himalayas
Himalayas Plus
Himalayas Max
Find your dream job
Sign up now and join over 100,000 remote workers who receive personalized job alerts, curated job matches, and more for free!
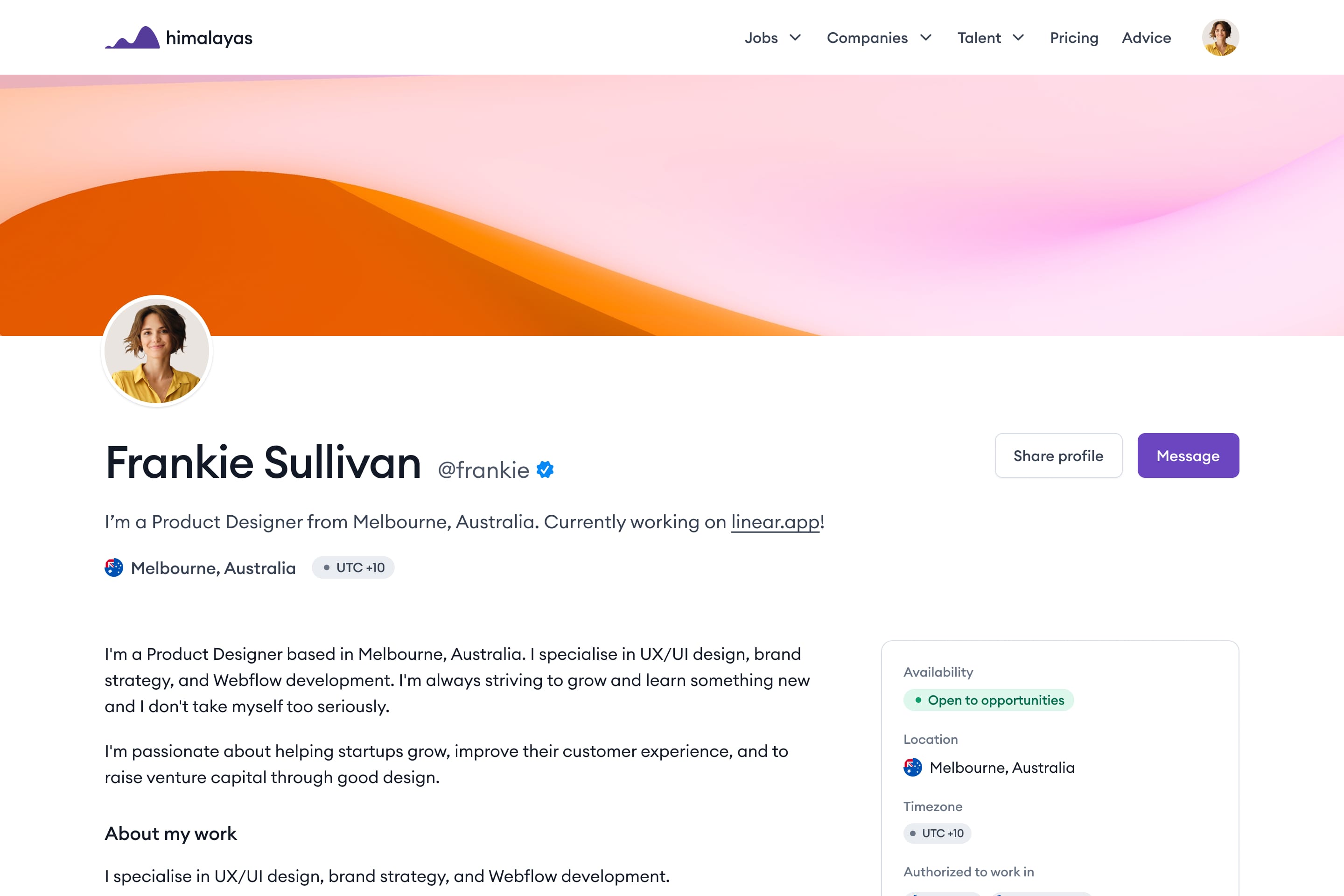