5 Bandmill Operator Interview Questions and Answers
Bandmill Operators are responsible for operating and maintaining band sawmills to cut logs into lumber or other wood products. They ensure the equipment runs efficiently, monitor the quality of cuts, and perform routine maintenance. Junior operators typically assist with basic tasks and learn the machinery, while senior and lead operators oversee operations, troubleshoot issues, and may supervise a team. Need to practice for an interview? Try our AI interview practice for free then unlock unlimited access for just $9/month.
Unlimited interview practice for $9 / month
Improve your confidence with an AI mock interviewer.
No credit card required
1. Junior Bandmill Operator Interview Questions and Answers
1.1. Can you describe your experience operating a bandmill and any safety protocols you followed?
Introduction
This question is crucial as it assesses your practical experience and understanding of safety, which are vital in operating heavy machinery like a bandmill.
How to answer
- Begin by outlining your hands-on experience with bandmill operations
- Detail specific safety protocols you adhered to, such as personal protective equipment (PPE) usage
- Discuss any training or certifications you have received related to machinery operation
- Explain how you ensure your work area is safe and organized
- Mention any instances where you identified and mitigated potential hazards
What not to say
- Vaguely stating you have operated machinery without providing specifics
- Neglecting to mention safety protocols or dismissing their importance
- Overlooking your role in maintaining a safe work environment
- Failing to demonstrate awareness of potential hazards
Example answer
“During my internship at a local lumber mill, I operated the bandmill daily and always wore my PPE, including gloves, goggles, and steel-toed boots. I followed all safety protocols, such as keeping the area around the bandmill clear and conducting regular maintenance checks. Once, I noticed a possible malfunction in the blade tension and reported it immediately to my supervisor, preventing a potential accident.”
Skills tested
Question type
1.2. Describe a situation where you had to troubleshoot a problem with the bandmill. What steps did you take?
Introduction
This question evaluates your troubleshooting abilities and problem-solving skills, which are essential for a Junior Bandmill Operator.
How to answer
- Use the STAR method to structure your response
- Clearly describe the problem you encountered with the bandmill
- Detail the steps you took to diagnose the issue
- Explain how you implemented a solution or escalated the problem if necessary
- Share the outcome and what you learned from the experience
What not to say
- Describing a situation without outlining your specific actions
- Ignoring the importance of teamwork or communication in resolving issues
- Providing vague answers without clarity on the troubleshooting process
- Failing to mention the learning experience from the situation
Example answer
“Once, while operating the bandmill, I noticed that the feed rate was slower than normal. I checked the settings, but everything seemed in order. I then inspected the blade and found it was dull. I informed my supervisor and we replaced the blade together. This experience taught me the importance of proactive monitoring and timely maintenance.”
Skills tested
Question type
1.3. How do you prioritize safety while working under pressure in a fast-paced environment?
Introduction
This question assesses your ability to maintain safety standards and prioritize tasks effectively in a high-pressure setting, which is critical in manufacturing operations.
How to answer
- Discuss your understanding of the importance of safety in all circumstances
- Explain how you manage your time and tasks to ensure safety isn't compromised
- Share specific strategies you use to stay calm and focused under pressure
- Mention any experiences where you had to balance efficiency with safety
- Emphasize your commitment to a safety-first mindset at all times
What not to say
- Indicating that safety can be overlooked if time is tight
- Lacking concrete examples of managing pressure while ensuring safety
- Failing to acknowledge the importance of maintaining safety standards
- Suggesting that safety protocols are burdensome or unnecessary
Example answer
“In my role at the mill, I always prioritize safety, even when under pressure. For instance, during a busy day, I make sure to communicate clearly with my team about our tasks and remind everyone to follow safety protocols. I also take short breaks to assess our workflow and ensure that we are not rushing through tasks at the expense of safety. This commitment has helped create a culture of safety in our team.”
Skills tested
Question type
2. Bandmill Operator Interview Questions and Answers
2.1. Can you describe your experience with operating and maintaining bandmills?
Introduction
This question assesses your technical expertise and familiarity with bandmill operations, which is crucial for ensuring efficiency and safety in the lumber processing industry.
How to answer
- Detail your hands-on experience with bandmills, including specific models you've operated.
- Explain your routine maintenance practices to ensure optimal performance.
- Discuss any troubleshooting techniques you have employed during operations.
- Mention any safety protocols you follow while operating machinery.
- If possible, quantify your contributions to production efficiency or waste reduction.
What not to say
- Vague descriptions of experience without specific examples.
- Claiming to have experience without demonstrating knowledge of bandmill operations.
- Ignoring the importance of safety protocols.
- Failing to mention the importance of teamwork in a manufacturing setting.
Example answer
“I have over five years of experience operating both portable and stationary bandmills at a lumber yard in Mpumalanga. I perform daily checks on the blades and lubricate the machinery as needed to prevent breakdowns. When faced with blade misalignment, I quickly troubleshoot by adjusting the tension, which has improved our production uptime by 15%. Safety is paramount; I always wear the necessary protective gear and follow all safety procedures.”
Skills tested
Question type
2.2. Describe a time when you had to work under pressure to meet a production deadline.
Introduction
This question evaluates your ability to handle stress and maintain productivity in a fast-paced environment, which is essential in the manufacturing sector.
How to answer
- Use the STAR method to structure your response, focusing on the Situation, Task, Action, Result.
- Describe the specific deadline you faced and the context surrounding it.
- Explain the steps you took to prioritize tasks and manage your time effectively.
- Include how you communicated with your team to ensure everyone was aligned and working efficiently.
- Highlight the outcome, focusing on any metrics or qualitative results.
What not to say
- Describing a situation where you panicked instead of taking action.
- Failing to mention teamwork or collaboration.
- Indicating that you prefer not to work under pressure.
- Providing a vague answer without specific actions or outcomes.
Example answer
“During a peak season, our team was tasked with increasing production by 30% to meet a large order. I quickly assessed the workflow and identified bottlenecks, then collaborated with my colleagues to optimize our processes. By implementing a shift system and streamlining the cutting process, we not only met the deadline but exceeded it by delivering the order a day early. This experience taught me the value of teamwork and efficient task management.”
Skills tested
Question type
3. Senior Bandmill Operator Interview Questions and Answers
3.1. Can you describe a time when you had to troubleshoot a mechanical issue with the bandmill? What steps did you take?
Introduction
This question is crucial for evaluating your technical problem-solving skills and your ability to maintain equipment, which are essential for a Senior Bandmill Operator.
How to answer
- Begin with a clear description of the mechanical issue you encountered.
- Detail the process you used to diagnose the problem, including any tools or techniques.
- Explain the steps you took to resolve the issue, emphasizing teamwork if applicable.
- Highlight the outcome and any improvements made to prevent future issues.
- Share any lessons learned from the experience.
What not to say
- Avoid vague descriptions without specifics about the issue.
- Do not downplay the importance of teamwork if others were involved.
- Avoid claiming you fixed everything on your own without collaboration.
- Steer clear of negative remarks about the equipment or company.
Example answer
“At my previous job with Yamada Lumber, we faced a sudden drop in cutting efficiency due to blade misalignment. I quickly assessed the situation, using both a dial indicator and my experience to identify the misalignment. I collaborated with the maintenance team to recalibrate the blade, and we ran a test cut to ensure precision. This not only restored efficiency but also improved our cutting accuracy by 15%. I learned that timely communication and a systematic approach are key when troubleshooting.”
Skills tested
Question type
3.2. How do you ensure safety protocols are followed in your daily operations?
Introduction
This question assesses your commitment to safety in the workplace, which is paramount in operating heavy machinery like bandmills.
How to answer
- Discuss specific safety protocols you follow regularly.
- Explain how you educate and enforce safety standards among your team.
- Share examples of how you've addressed safety violations or near misses.
- Highlight any safety training you have participated in.
- Mention the importance of a safety-first culture.
What not to say
- Avoid saying safety is not a priority if you are under pressure.
- Do not provide generic answers; be specific about protocols.
- Steer clear of stating that you have never had an incident.
- Avoid blaming others for safety issues without your involvement.
Example answer
“In my role at Sato Timber, I emphasized the importance of safety by conducting daily briefings to review protocols before operations. I implemented a buddy system for equipment checks, ensuring that two people confirm safety measures are in place before starting. When we had a near miss, I organized a team meeting to discuss it openly and reinforce our commitment to safety. This proactive approach has led to a 30% reduction in safety incidents over the past year.”
Skills tested
Question type
4. Lead Bandmill Operator Interview Questions and Answers
4.1. Can you describe a time when you identified a mechanical issue with a bandmill and how you resolved it?
Introduction
This question is crucial for understanding your technical expertise and problem-solving abilities, which are vital in ensuring the efficient operation of bandmills.
How to answer
- Outline the specific mechanical issue you encountered
- Explain how you diagnosed the problem, including any tools or methods used
- Detail the steps you took to resolve the issue, emphasizing safety protocols
- Discuss the outcome of your actions, including any improvements in operation or efficiency
- Reflect on what you learned from the experience and how it has influenced your approach to maintenance
What not to say
- Vaguely describing issues without specifics or outcomes
- Failing to mention safety measures taken during repairs
- Taking sole credit for team efforts in resolving issues
- Neglecting to discuss the importance of preventative maintenance
Example answer
“At Sappi, I noticed unusual vibrations during the bandmill operation, which indicated a potential issue with the drive belt. After conducting a thorough inspection, I discovered the belt was misaligned. I carefully realigned it and replaced any worn components. This not only resolved the vibration issue but also improved our cutting efficiency by 15%. This experience reinforced my belief in proactive maintenance.”
Skills tested
Question type
4.2. How do you ensure the safety and efficiency of your team while operating heavy machinery?
Introduction
This question evaluates your leadership and safety management skills, which are essential for a lead operator responsible for team performance and workplace safety.
How to answer
- Discuss your approach to training team members on safety protocols
- Explain how you conduct regular safety audits and checks
- Detail procedures you implement to maintain machinery and reduce risks
- Share how you foster a culture of safety and open communication among team members
- Provide examples of how you have improved safety measures in your previous roles
What not to say
- Minimizing the importance of safety procedures
- Failing to provide specific examples of safety initiatives
- Not addressing team involvement or engagement in safety practices
- Suggesting safety is solely the responsibility of management
Example answer
“I prioritize safety by conducting weekly training sessions for my team on equipment handling and emergency procedures. At my previous job at Mondi, I implemented a buddy system where experienced operators mentored newer team members, which led to a 30% reduction in on-the-job incidents. Additionally, I ensure regular machinery maintenance checks to prevent failures.”
Skills tested
Question type
5. Bandmill Supervisor Interview Questions and Answers
5.1. Can you describe a time when you had to resolve a conflict between team members on the production floor?
Introduction
This question evaluates your conflict resolution and leadership skills, which are crucial for a supervisory role in a manufacturing environment like a bandmill.
How to answer
- Use the STAR method to structure your response (Situation, Task, Action, Result)
- Clearly describe the conflict and its impact on team morale and productivity
- Explain the steps you took to mediate the situation
- Detail how you communicated with both parties involved
- Share the outcome and any long-term changes implemented to prevent future conflicts
What not to say
- Avoid blaming one party without acknowledging the context
- Failing to describe your specific actions
- Not mentioning the importance of team dynamics
- Overlooking the resolution process and its effectiveness
Example answer
“In my previous role at a local sawmill, two operators had a disagreement about the correct settings for the bandmill. I facilitated a meeting where each could express their concerns. I guided the discussion towards finding a compromise while emphasizing our shared goal of efficiency. As a result, we agreed on a standardized operating procedure that improved team cohesion and reduced errors by 15%.”
Skills tested
Question type
5.2. How do you ensure safety compliance and operational efficiency on the production floor?
Introduction
This question assesses your knowledge of safety standards and your ability to implement operational procedures effectively, which is vital in a manufacturing setting.
How to answer
- Discuss your familiarity with safety regulations relevant to bandmill operations
- Explain how you conduct regular safety audits and training sessions
- Detail your approach to monitoring operational efficiency and productivity metrics
- Share experiences where you improved safety or efficiency measures
- Mention how you involve team members in safety discussions and improvements
What not to say
- Claiming safety is solely the responsibility of the safety officer
- Ignoring past incidents or not acknowledging the importance of learning from them
- Focusing only on efficiency without mentioning safety
- Not providing specific examples from your experience
Example answer
“At my previous job, I implemented a weekly safety audit that involved all team members. This ensured everyone was aware of safety protocols and engaged in discussions about potential hazards. Additionally, I introduced a system for tracking efficiency metrics, which led to a 10% increase in our production rate while maintaining a perfect safety record over six months. This dual focus on safety and efficiency is essential in our industry.”
Skills tested
Question type
Similar Interview Questions and Sample Answers
Simple pricing, powerful features
Upgrade to Himalayas Plus and turbocharge your job search.
Himalayas
Himalayas Plus
Himalayas Max
Find your dream job
Sign up now and join over 100,000 remote workers who receive personalized job alerts, curated job matches, and more for free!
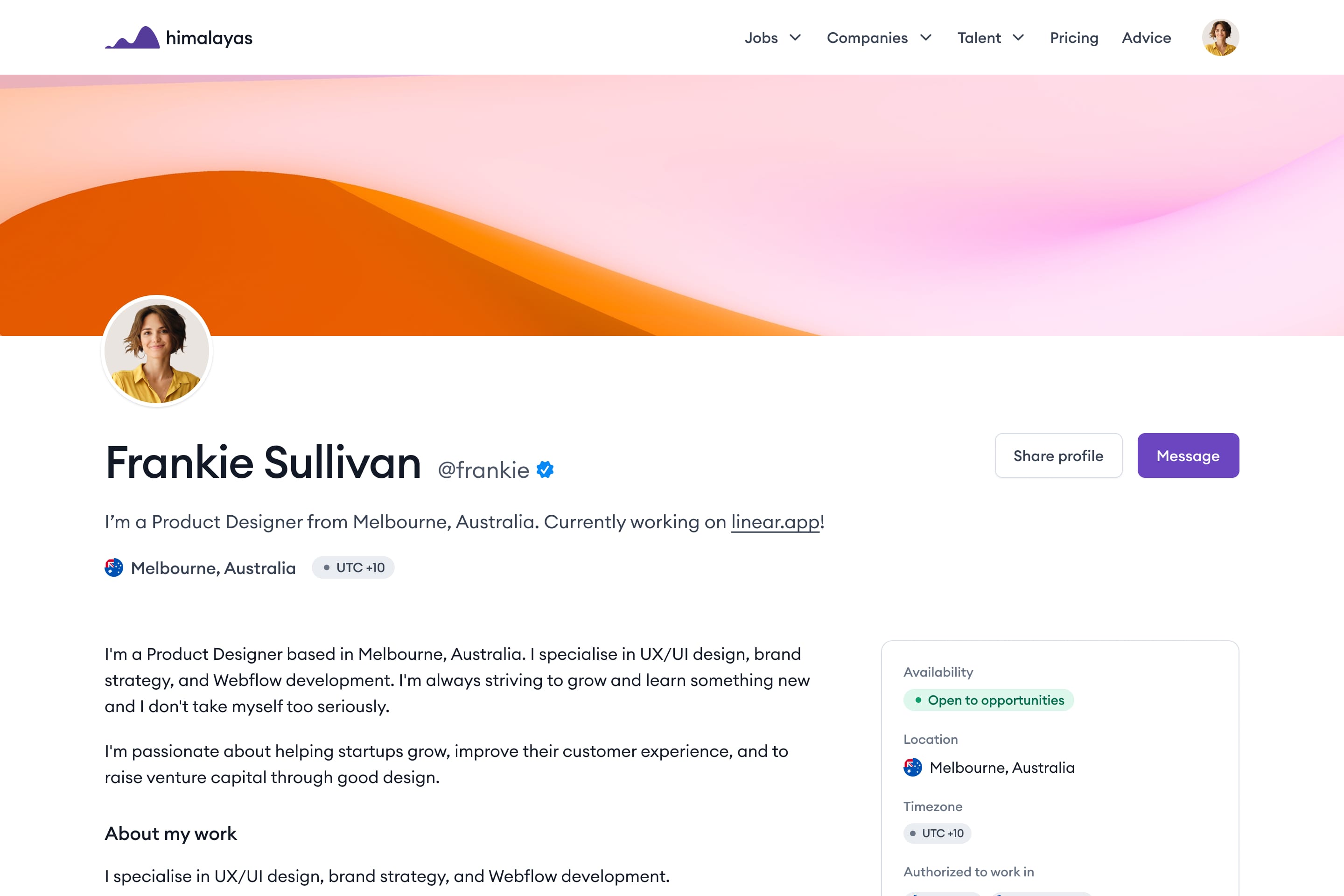