4 Ampoule Examiner Interview Questions and Answers
Ampoule Examiners are responsible for inspecting ampoules for defects, ensuring they meet quality standards before being distributed. They play a critical role in maintaining the integrity of pharmaceutical or chemical products. Junior roles focus on basic inspection tasks, while senior and lead positions may involve overseeing teams, implementing quality control processes, and ensuring compliance with industry regulations. Need to practice for an interview? Try our AI interview practice for free then unlock unlimited access for just $9/month.
Unlimited interview practice for $9 / month
Improve your confidence with an AI mock interviewer.
No credit card required
1. Ampoule Examiner Interview Questions and Answers
1.1. Can you describe your experience with inspecting ampoules for defects?
Introduction
This question helps assess your attention to detail and your familiarity with quality control processes, which are crucial in ensuring product safety and compliance in the pharmaceutical industry.
How to answer
- Detail your previous roles involving ampoule inspection or similar responsibilities.
- Explain the specific types of defects you are trained to identify.
- Discuss the tools and techniques you use for inspection.
- Describe how you document and report defects.
- Share any relevant training or certifications in quality control.
What not to say
- Claiming to have no experience in ampoule inspection.
- Providing vague answers without specific examples.
- Failing to mention the importance of compliance and safety.
- Not discussing any quality control standards or regulations.
Example answer
“In my previous role at a pharmaceutical company, I was responsible for inspecting over 5,000 ampoules daily for issues like cracks and particulate matter. I utilized both visual inspection and automated systems to ensure compliance with GMP standards. Any defects were meticulously documented in our quality management system, which helped improve our process by reducing defect rates by 15% in six months.”
Skills tested
Question type
1.2. How do you handle a situation where you find a significant defect in a batch of ampoules?
Introduction
This question evaluates your problem-solving skills and ability to prioritize quality and safety, which is critical in the pharmaceutical industry.
How to answer
- Describe your immediate response to identifying a defect.
- Explain how you would assess the impact of the defect on the product.
- Discuss the communication process with your team and management.
- Detail how you would document the incident and any corrective actions taken.
- Mention any protocols you follow for defect reporting.
What not to say
- Suggesting to overlook the defect to avoid complications.
- Failing to outline a clear process for handling defects.
- Neglecting to discuss the importance of transparency in reporting.
- Overemphasizing personal responsibility without mentioning team collaboration.
Example answer
“If I discovered a significant defect, my first step would be to isolate the affected batch to prevent distribution. I would assess the nature of the defect and communicate immediately with my supervisor and the quality assurance team. Following our standard operating procedures, I would document the findings in our quality control log and initiate a root cause analysis to ensure proper corrective actions are taken. This method has proven effective in preventing recurrence of similar issues.”
Skills tested
Question type
2. Senior Ampoule Examiner Interview Questions and Answers
2.1. Can you describe your process for inspecting ampoules for defects?
Introduction
This question is crucial for assessing your attention to detail and understanding of quality control processes specific to ampoule examination, which are vital in ensuring product safety and efficacy.
How to answer
- Outline the standards and regulations you adhere to during inspections, such as GMP (Good Manufacturing Practices)
- Describe the specific tools and techniques you use for inspecting ampoules
- Detail the criteria you evaluate, including visual defects, fill levels, and closures
- Explain how you document your findings and communicate issues to the relevant stakeholders
- Mention any experience with troubleshooting and resolving quality issues
What not to say
- Failing to mention any industry standards or regulations
- Providing vague or generic responses about inspection without specifics
- Neglecting to address the importance of documentation and communication
- Overlooking the significance of teamwork in resolving quality issues
Example answer
“At Pfizer, I followed strict GMP protocols when inspecting ampoules. Using a combination of visual inspections under controlled lighting and automated systems, I evaluated for defects such as cracks and improper seals. I documented all findings meticulously and coordinated with the production team to address any discrepancies immediately, which helped maintain a 98% quality compliance rate.”
Skills tested
Question type
2.2. Describe a situation where you identified a significant defect in an ampoule batch. What steps did you take?
Introduction
This question aims to evaluate your problem-solving skills and ability to act decisively in quality assurance roles, which is critical in the pharmaceutical industry.
How to answer
- Use the STAR method (Situation, Task, Action, Result) to structure your response
- Clearly explain the context of the defect you found
- Detail the immediate actions you took to investigate and resolve the issue
- Highlight your communication with team members and management during this process
- Discuss the outcome and any long-term changes implemented to prevent recurrence
What not to say
- Dismissing the importance of reporting and documentation
- Not taking responsibility for ensuring product quality
- Focusing solely on the problem without discussing solutions
- Failing to mention collaboration with other departments
Example answer
“During my time at GSK, I discovered a batch of ampoules with inconsistent fill levels. I reported the issue immediately and conducted a thorough investigation to trace the source. I collaborated with the production and engineering teams to adjust the filling machine settings. As a result, we not only resolved the immediate defect but also implemented new calibration procedures that reduced future discrepancies by 30%.”
Skills tested
Question type
3. Lead Ampoule Examiner Interview Questions and Answers
3.1. Can you describe your experience with quality control processes specific to ampoule examination?
Introduction
This question is crucial as it assesses your technical expertise and understanding of the quality control processes that ensure the safety and efficacy of pharmaceutical products.
How to answer
- Start by outlining your relevant experience in ampoule examination and quality control.
- Discuss the specific techniques and tools you used for inspecting ampoules.
- Explain how you ensure compliance with industry standards and regulations (e.g., ISO, GMP).
- Provide examples of issues you identified and how you addressed them.
- Mention any training or certifications you have that enhance your qualifications.
What not to say
- Vague responses that lack specific examples.
- Ignoring the importance of compliance and regulations.
- Assuming quality control is solely about visual inspection.
- Failing to mention teamwork or collaboration with other departments.
Example answer
“In my previous role at Grifols, I was responsible for the quality control of ampoules. I utilized both visual inspection and automated testing equipment to check for defects such as cracks or improper sealing. I ensured compliance with GMP standards and conducted regular training sessions for my team on new inspection techniques. One significant instance was when I identified a batch with micro-cracks early in the process, preventing a costly recall and ensuring product safety.”
Skills tested
Question type
3.2. Describe a situation where you had to train a new team member on the inspection process. How did you ensure they learned effectively?
Introduction
This question evaluates your leadership and mentorship skills, which are important for a lead position where you may be responsible for training new staff.
How to answer
- Use the STAR method to structure your answer.
- Explain the training process you implemented.
- Discuss how you tailored your training approach to the individual’s learning style.
- Highlight the resources or materials you provided to aid learning.
- Share the outcomes of the training and any feedback received.
What not to say
- Claiming that training is not part of your role.
- Providing a generic training approach without personalization.
- Failing to mention follow-up or assessment of the new hire's progress.
- Neglecting to discuss the importance of teamwork in training.
Example answer
“At my previous position with Famar, I trained a new technician on the ampoule inspection process. I started by assessing their prior knowledge and tailored the training to their level. We used hands-on demonstrations alongside detailed manuals. I scheduled regular check-ins to review their progress and offered feedback. By the end of the month, they were able to independently perform inspections with a 98% accuracy rate, which was a great achievement.”
Skills tested
Question type
4. Quality Control Specialist (Ampoules) Interview Questions and Answers
4.1. Can you describe a time when you identified a significant quality issue during the production of ampoules? What steps did you take to address it?
Introduction
This question assesses your analytical skills and ability to respond to quality control issues, which are crucial in the ampoule manufacturing process where product integrity is paramount.
How to answer
- Use the STAR method (Situation, Task, Action, Result) to structure your response
- Clearly explain the quality issue you discovered and its potential impact on production and safety
- Detail the steps you took to investigate and resolve the issue, including any collaboration with other departments
- Highlight any changes you implemented to prevent future occurrences
- Quantify the results, such as reduced defect rates or improved compliance
What not to say
- Dismissing the issue without explaining the consequences
- Not mentioning any collaborative efforts with other teams or departments
- Focusing solely on the problem without outlining your actions
- Failing to discuss the learning or preventive measures taken after the incident
Example answer
“At my previous role with a pharmaceutical company, I identified a recurring issue where ampoules were showing signs of contamination during the quality inspection phase. I immediately conducted a thorough investigation to trace the contamination source, which led us to an uncleaned production line. I coordinated with the production team to implement a revised cleaning protocol and increased inspection frequency. As a result, we reduced contamination incidents by 70% over the next quarter, significantly enhancing our compliance with safety standards.”
Skills tested
Question type
4.2. How do you ensure compliance with industry standards and regulations in the quality control of ampoules?
Introduction
This question evaluates your knowledge of regulatory requirements and your approach to maintaining compliance within the quality control framework.
How to answer
- Mention specific industry standards relevant to ampoule production (e.g., ISO, GMP)
- Explain your process for staying updated with regulatory changes
- Describe how you implement training and procedures to ensure compliance
- Discuss how you conduct audits and inspections to maintain standards
- Highlight any experience in preparing for regulatory inspections
What not to say
- Assuming regulations are static without acknowledging the need to stay informed
- Neglecting the importance of documentation and record-keeping in compliance
- Not addressing the role of teamwork in ensuring compliance
- Providing vague answers without concrete examples
Example answer
“I ensure compliance with GMP and ISO standards by regularly reviewing the latest regulations and participating in training sessions. I implement a comprehensive quality control checklist that aligns with these standards and conduct quarterly audits to assess adherence. In my previous position, I led a successful preparation for a regulatory inspection, where we achieved zero non-conformances, demonstrating our commitment to maintaining high-quality standards in ampoule production.”
Skills tested
Question type
Similar Interview Questions and Sample Answers
Simple pricing, powerful features
Upgrade to Himalayas Plus and turbocharge your job search.
Himalayas
Himalayas Plus
Himalayas Max
Find your dream job
Sign up now and join over 100,000 remote workers who receive personalized job alerts, curated job matches, and more for free!
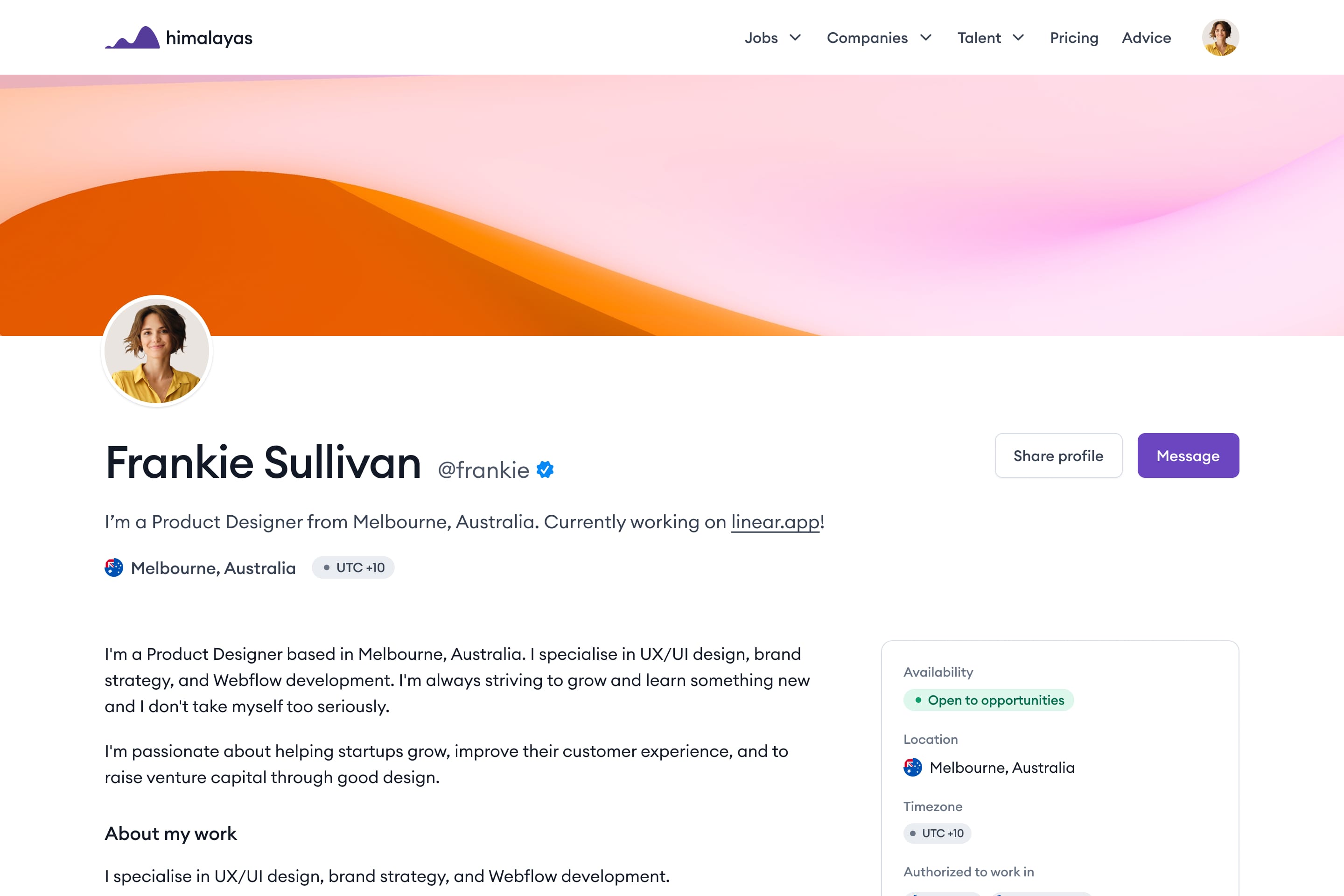