Complete Welding Instructor Career Guide
Welding instructors shape the next generation of skilled tradespeople, imparting essential knowledge and hands-on expertise crucial for industries from manufacturing to construction. You'll guide aspiring welders through complex techniques, ensuring they master the precision and safety required for high-demand jobs. This unique role combines technical mastery with a passion for teaching, offering a fulfilling path where your impact is visible in the careers of your students.
Key Facts & Statistics
Median Salary
$64,280 USD
(U.S. national median for Vocational Education Teachers, Postsecondary, Source: BLS, May 2023)
Range: $40k - $90k+ USD, varying significantly by institution type and experience
Growth Outlook
5%
as fast as average (Source: BLS, 2022-2032)
Annual Openings
≈17,200
openings annually (Source: BLS, 2022-2032)
Top Industries
Typical Education
Associate's degree or postsecondary nondegree award in welding, plus significant industry experience and often a teaching or instructor certification
What is a Welding Instructor?
A Welding Instructor is a skilled professional responsible for educating and training individuals in the art and science of welding. They impart both theoretical knowledge and practical skills, preparing students for careers in various industries that require metal fabrication and joining. Their core purpose is to ensure students not only master different welding techniques but also understand crucial safety procedures, material science, and blueprint reading.
This role differs significantly from a journeyman welder or a welding supervisor. While a journeyman welder focuses on executing welding tasks on a job site, and a supervisor manages a team of welders, a welding instructor's primary function is pedagogical. They design and deliver curriculum, assess learning, and mentor aspiring welders, bridging the gap between fundamental concepts and real-world application. They are educators first, translating complex technical skills into accessible learning experiences.
What does a Welding Instructor do?
Key Responsibilities
- Prepare and deliver engaging lectures and demonstrations on welding theory, safety protocols, and various welding processes.
- Guide students through hands-on practice sessions, providing individualized feedback and correcting techniques to ensure proper skill development.
- Develop and update curriculum materials, including lesson plans, assignments, and practical exercises, to align with industry standards and certification requirements.
- Assess student performance through practical tests, written exams, and project evaluations, maintaining accurate records of progress and attendance.
- Maintain and troubleshoot welding equipment, ensuring all tools and machinery are in safe working order and available for student use.
- Enforce strict adherence to safety regulations and proper shop procedures to create a secure learning environment for all students.
- Provide career guidance and mentorship to students, helping them understand industry demands, job opportunities, and pathways to professional certification or advanced training programs.
Work Environment
Welding instructors primarily work in vocational schools, community colleges, or dedicated training centers. Their environment is a blend of classroom settings for theoretical instruction and hands-on welding labs or workshops. These labs can be noisy, require proper ventilation, and expose instructors to fumes, sparks, and heat, necessitating strict adherence to safety protocols.
The role involves a significant amount of standing, demonstrating techniques, and providing individual guidance to students. Collaboration with other instructors and administrative staff is common, but much of the day is spent directly interacting with students. Schedules often align with academic calendars, though evening or weekend classes are possible. The pace is generally steady, with a focus on structured learning and practical application.
Tools & Technologies
Welding instructors work extensively with a range of welding machines, including MIG, TIG, Stick (SMAW), and Flux-Cored Arc Welding (FCAW) equipment. They also utilize plasma cutters, oxy-fuel cutting torches, grinders, and various hand tools for metal preparation and finishing.
Instructional tools include whiteboards, projectors, and specialized software for presenting theoretical concepts and welding simulations. Safety gear such as welding helmets, gloves, fire-resistant clothing, and respirators are fundamental. They also use curriculum development software, learning management systems, and assessment tools to manage student progress and course content.
Welding Instructor Skills & Qualifications
Becoming a Welding Instructor requires a blend of deep practical experience, pedagogical ability, and a commitment to safety. Qualifications are structured around proving both mastery of welding processes and the capacity to effectively transfer that knowledge. While hands-on experience is paramount, formal education and certifications significantly enhance an instructor's credibility and employability.
Requirements vary by institution and seniority. Community colleges and vocational schools often prefer instructors with associate's degrees and extensive industry experience, alongside specific welding certifications. Private training centers might prioritize certifications and practical experience over formal degrees, especially for specialized welding techniques. Senior instructor roles typically demand more years of teaching experience and potentially a broader range of welding expertise.
Practical experience in diverse welding applications is often more valued than a high-level academic degree alone. Certifications, particularly those from the American Welding Society (AWS), are critical. These certifications validate an instructor's proficiency in various welding codes and processes. The skill landscape is evolving with new materials and automated welding systems, requiring instructors to continually update their own knowledge to remain relevant and effective educators.
Education Requirements
Technical Skills
- Arc Welding processes (SMAW, GMAW, FCAW, GTAW) expertise and instruction
- Welding inspection and quality control procedures (visual, destructive, non-destructive testing basics)
- Blueprint reading and interpretation for welding fabrication
- Metal fabrication techniques (cutting, grinding, fitting, bending)
- Welding safety regulations and practices (OSHA, ANSI standards)
- Welding equipment maintenance and calibration
- Material science fundamentals (types of metals, properties, heat treatment)
- Welding code knowledge (AWS D1.1, ASME Section IX, API 1104, etc.)
- Joint design and weld preparation techniques
- Oxy-fuel cutting and plasma cutting operations
- Use of measuring tools (calipers, micrometers, gauges) and precision measurement techniques
- Curriculum development and lesson planning for welding programs
Soft Skills
- Instructional Communication: Instructors must clearly explain complex welding concepts, procedures, and safety protocols to diverse learners with varying skill levels.
- Patience and Empathy: Guiding students through challenging techniques and correcting mistakes requires significant patience and an understanding of individual learning paces.
- Safety Leadership: Instructors are responsible for enforcing strict safety standards in a hazardous environment, requiring strong leadership and attention to detail.
- Problem-Solving and Troubleshooting: Instructors diagnose student errors and equipment malfunctions, guiding students to identify and resolve issues during practical exercises.
- Adaptability: Instructors adjust teaching methods to suit different learning styles and adapt curriculum based on new industry standards or student needs.
- Mentorship and Encouragement: Building student confidence and providing constructive feedback are crucial for student success and retention in a hands-on learning environment.
- Organization and Planning: Managing classroom schedules, preparing materials, maintaining equipment, and assessing student progress require strong organizational skills.
- Attention to Detail: Precision is critical in welding; instructors must model and teach meticulous attention to detail in all aspects of the craft and safety procedures.
How to Become a Welding Instructor
Becoming a Welding Instructor offers a rewarding path for experienced welders to share their expertise. Pathways vary significantly, ranging from formal vocational school teaching to corporate training roles or even independent consulting. Some institutions prioritize a bachelor's degree in welding technology or education, while others value extensive industry experience and relevant certifications above all else.
Realistic timelines for entry can range from six months for a highly experienced, certified welder transitioning to a part-time role, to two years or more for someone pursuing an instructor certification or a full-time academic position. Geographic location plays a role; major industrial hubs often have more opportunities in corporate training, while rural areas might emphasize vocational school positions. Smaller welding shops or community programs may seek instructors with practical, hands-on experience, whereas larger educational institutions often require more formal credentials.
Common misconceptions include believing a teaching degree is always necessary or that only master welders can instruct. In reality, many roles value demonstrable teaching ability, strong communication skills, and a solid understanding of safety protocols alongside welding proficiency. Networking within the welding community, attending industry events, and connecting with current instructors can reveal opportunities and insights into specific hiring needs.
Step 1
Step 2
Step 3
Step 4
Step 5
Step 6
Education & Training Needed to Become a Welding Instructor
Becoming a Welding Instructor involves a blend of practical experience and formal pedagogical training. Unlike many welding roles that prioritize hands-on skill, this position requires not only mastery of welding techniques but also the ability to effectively teach and assess others. While a four-year bachelor's degree in a related field like Industrial Technology or Vocational Education might be preferred by some institutions, it is not always mandatory. Many community colleges and vocational schools accept candidates with extensive industry experience, a strong portfolio of certifications (e.g., AWS Certified Welder, CWI), and a teaching certification or a willingness to obtain one.
Formal degree programs, often costing $40,000-$100,000+, typically take four years and provide a broad educational foundation alongside specialized welding pedagogy. Vocational instructor training programs or associate degrees, ranging from $10,000-$30,000 over 1-2 years, offer a more focused path. For experienced welders, obtaining a Certified Welding Inspector (CWI) certification, which can cost $1,500-$3,000 and take 3-6 months of dedicated study, significantly enhances credibility and teaching capabilities. Many institutions also require or strongly prefer instructors to hold an AWS Certified Welder credential in the processes they will teach, which involves specific tests and can be obtained through various training centers.
The market perception of credentials varies; universities prefer degrees, while vocational schools value industry experience and certifications. Continuous learning is crucial for Welding Instructors, as new technologies and safety standards emerge constantly. Professional development often includes staying current with AWS code updates, attending industry seminars, and pursuing advanced welding certifications. The balance between theoretical knowledge and practical experience is critical; instructors must demonstrate both deep understanding of welding principles and the practical skills to perform and troubleshoot complex welds. Emerging trends include virtual reality training and advanced robotic welding, requiring instructors to adapt their teaching methods. Cost-benefit analysis should consider the earning potential and job security that come with a well-rounded educational background and strong industry credentials.
Welding Instructor Salary & Outlook
Compensation for a Welding Instructor varies significantly based on several factors. Geographic location plays a crucial role; instructors in areas with high demand for skilled trades, or regions with a higher cost of living, typically command better salaries. For instance, an instructor in a major industrial hub might earn more than one in a rural area.
Years of experience and specialized certifications, such as Certified Welding Inspector (CWI) or Certified Welding Educator (CWE), dramatically increase earning potential. Instructors with expertise in advanced welding techniques or robotic welding can also secure premium compensation. Furthermore, the type of institution—whether a community college, vocational school, private training center, or corporate training department—impacts pay scales.
Total compensation packages often extend beyond base salary. They can include health and dental insurance, retirement contributions like 401(k) or pension plans, and paid time off. Some positions offer professional development allowances for continuing education or industry certifications. Performance bonuses are less common in this role but may exist in private training settings linked to student enrollment or program success.
Salary negotiation leverage increases with specialized skills and a proven track record of student success. Remote work is generally not applicable for hands-on welding instruction, though some curriculum development or theoretical instruction might occur virtually. While figures here focus on the USD context, international markets will have their own distinct salary structures influenced by local labor laws and economic conditions.
Salary by Experience Level
Level | US Median | US Average |
---|---|---|
Assistant Welding Instructor | $48k USD | $50k USD |
Welding Instructor | $60k USD | $62k USD |
Senior Welding Instructor | $72k USD | $75k USD |
Lead Welding Instructor | $85k USD | $88k USD |
Welding Program Coordinator | $92k USD | $95k USD |
Market Commentary
The job market for Welding Instructors shows steady demand, driven by a persistent shortage of skilled welders across various industries. The Bureau of Labor Statistics (BLS) projects employment of welding, soldering, and brazing workers to grow 2% from 2022 to 2032, which directly translates to a need for qualified instructors to train the next generation. As older generations of welders retire, the demand for new talent intensifies, creating a consistent need for educational professionals.
Emerging opportunities for Welding Instructors include teaching advanced techniques such as robotic welding, additive manufacturing with metals, and specialized alloys. Digital transformation in manufacturing also requires instructors to teach data-driven welding processes and quality control. There is a continuous demand for instructors who can adapt curricula to meet evolving industry standards and technological advancements.
The supply of qualified instructors often lags behind demand, particularly for those with significant industry experience and teaching credentials. This imbalance can lead to competitive salaries in certain regions or for specialized roles. While automation and AI are transforming welding processes, they also create new roles that require human oversight and instruction, future-proofing the need for skilled educators. This profession is relatively recession-resistant, as foundational welding skills remain essential across many sectors, including construction, manufacturing, and energy infrastructure.
Geographic hotspots for Welding Instructors align with manufacturing and industrial centers, such as the Midwest, Gulf Coast, and parts of the Southeast and Northeast. Expanding infrastructure projects and reshoring initiatives continue to bolster demand for skilled welders and, consequently, their instructors.
Welding Instructor Career Path
Career progression for a Welding Instructor typically involves a blend of deepening technical expertise, refining pedagogical skills, and expanding administrative or leadership responsibilities. Initial stages focus on mastering instructional delivery and student assessment. As instructors gain experience, they take on more complex curriculum development and mentorship roles.
Advancement can follow either an individual contributor (IC) track, emphasizing advanced technical instruction and curriculum design, or a management/leadership track, which involves overseeing programs and other instructors. Factors influencing advancement include instructional effectiveness, student success rates, the ability to integrate new welding technologies, and contributions to program accreditation or industry partnerships. Company size and industry influence career paths; larger institutions may offer more defined leadership roles, while smaller schools might see instructors take on broader responsibilities sooner.
Lateral movement opportunities exist into specialized welding fields, quality assurance, or even professional welding roles outside of education. Continuous professional development, including new welding certifications (e.g., CWI, CWE) and pedagogical training, is crucial. Networking within industry associations and educational consortiums builds reputation and opens doors for advanced roles or consulting opportunities. Common career pivots include moving into welding engineering, inspection, or business ownership within the welding sector.
Assistant Welding Instructor
0-2 yearsKey Focus Areas
Welding Instructor
2-5 yearsKey Focus Areas
Senior Welding Instructor
5-8 yearsKey Focus Areas
Lead Welding Instructor
8-12 yearsKey Focus Areas
Welding Program Coordinator
12+ yearsKey Focus Areas
Assistant Welding Instructor
0-2 yearsAssist lead instructors with classroom and lab instruction. Provide one-on-one student support during practical exercises. Prepare lab equipment and materials, ensuring a safe learning environment. Observe and learn best practices in welding instruction and curriculum delivery.
Key Focus Areas
Develop foundational instructional skills, including classroom management and practical demonstration techniques. Understand and apply safety protocols rigorously. Seek mentorship from experienced instructors to refine teaching methods and build confidence in front of students. Learn to assess student progress effectively.
Welding Instructor
2-5 yearsDeliver comprehensive welding instruction in classroom and lab settings. Design and implement lesson plans, practical exercises, and assessments. Evaluate student performance and provide constructive feedback. Maintain equipment and ensure compliance with safety regulations.
Key Focus Areas
Master diverse welding processes and their instruction (e.g., SMAW, GMAW, GTAW). Develop strong curriculum planning and assessment skills. Integrate new welding technologies and industry standards into teaching. Begin to mentor assistant instructors and contribute to program improvement initiatives.
Senior Welding Instructor
5-8 yearsLead instruction for advanced welding courses and specialized programs. Develop and refine curriculum content, incorporating industry best practices and emerging technologies. Mentor and provide guidance to less experienced instructors. Participate in program development and accreditation processes.
Key Focus Areas
Specialize in advanced welding techniques or niche areas like robotic welding or exotic materials. Develop leadership skills by guiding junior instructors and leading curriculum review committees. Pursue advanced certifications (e.g., Certified Welding Inspector - CWI, Certified Welding Educator - CWE). Contribute to industry outreach and advisory boards.
Lead Welding Instructor
8-12 yearsOversee a team of welding instructors, providing mentorship, performance evaluations, and professional development support. Lead curriculum development and revision efforts across all welding programs. Manage lab operations, equipment procurement, and maintenance. Ensure program compliance with industry standards and regulatory requirements.
Key Focus Areas
Cultivate strong leadership and team management abilities. Develop expertise in program budgeting, resource allocation, and facility management. Enhance strategic planning skills for long-term program growth. Build and maintain strong industry relationships for student placement and program relevance.
Welding Program Coordinator
12+ yearsManage the entire welding program, including curriculum, faculty, and facilities. Develop and implement program goals, objectives, and assessment strategies. Recruit and onboard new instructors. Foster industry partnerships and secure resources to enhance program offerings. Ensure program meets all accreditation and industry standards.
Key Focus Areas
Master program administration, including budgeting, scheduling, and student recruitment strategies. Develop strong communication and negotiation skills for engaging with stakeholders. Pursue advanced degrees in education or administration if desired. Focus on strategic planning for program expansion and innovation.
Job Application Toolkit
Ace your application with our purpose-built resources:
Welding Instructor Resume Examples
Proven layouts and keywords hiring managers scan for.
View examplesWelding Instructor Cover Letter Examples
Personalizable templates that showcase your impact.
View examplesTop Welding Instructor Interview Questions
Practice with the questions asked most often.
View examplesWelding Instructor Job Description Template
Ready-to-use JD for recruiters and hiring teams.
View examplesGlobal Welding Instructor Opportunities
Welding instructors are in global demand, teaching essential skills across diverse industries like manufacturing, construction, and energy. Many countries face skilled trades shortages, increasing opportunities for experienced instructors. Regulatory differences in welding codes and safety standards exist, requiring adaptability from international professionals. Instructors often seek international roles for higher pay, better living conditions, or to contribute to developing economies. International certifications like AWS CWI or EWF/IIW diplomas enhance global mobility and recognition.
Global Salaries
Welding instructor salaries vary significantly by region, reflecting economic conditions and demand for skilled trades. In North America, particularly the US and Canada, annual salaries range from $55,000 to $80,000 USD, often including benefits like health insurance and retirement plans. European nations like Germany or Switzerland offer €45,000 to €70,000 ($48,000-$75,000 USD), with robust social security and generous vacation. The cost of living in these areas is higher, impacting purchasing power.
In Asia-Pacific, specifically Australia and New Zealand, instructors can expect AUD 60,000 to AUD 90,000 ($40,000-$60,000 USD), which provides reasonable purchasing power given local costs. Middle Eastern countries, especially Saudi Arabia and UAE, offer tax-free salaries from $40,000 to $70,000 USD, often with housing allowances, making them attractive for savings. Latin American countries like Brazil or Mexico typically offer lower nominal wages, ranging from $20,000 to $40,000 USD, but the lower cost of living can balance this.
Salary structures also differ, with some countries emphasizing base pay, while others include performance bonuses or extensive non-monetary benefits. Tax implications vary widely; for example, high-income tax rates in some European countries contrast with lower rates or tax-free environments elsewhere. Experience and specialized certifications, such as a Certified Welding Inspector (CWI) or International Welding Engineer (IWE) qualification, significantly influence global compensation.
Remote Work
International remote work for welding instructors is generally limited due to the hands-on nature of the profession. While theoretical aspects can be taught online, practical training requires physical presence in a workshop or lab. Some opportunities exist for developing online course content, creating instructional videos, or providing virtual consultations on welding theory and safety protocols.
Companies hiring internationally for remote roles in this field often focus on curriculum development or specialized technical writing. Digital nomad visas are less common for this role, as most require a physical workspace. Employer policies on international remote work for instructors are rare, given the practical training demands. Income expectations for remote instructional work are usually lower than for in-person teaching. Essential equipment includes high-quality cameras and microphones for content creation, and reliable internet access for virtual sessions.
Visa & Immigration
Welding instructors commonly use skilled worker visas in countries with demand for vocational trainers. Popular destinations include Canada (Express Entry), Australia (Skilled Nominated Visa), Germany (Blue Card), and the UK (Skilled Worker visa). Requirements often include a relevant vocational qualification, significant industry experience, and a job offer from an accredited institution.
Credential recognition is crucial; institutions may require specific national or international certifications. The application process typically involves submitting educational and professional documents, undergoing skills assessments, and proving English or local language proficiency through tests like IELTS or Goethe-Zertifikat. Visa timelines vary from a few months to over a year, depending on the country and visa type. Some countries offer pathways to permanent residency after several years of skilled employment. Family members can often apply for dependent visas, allowing them to accompany the primary visa holder.
2025 Market Reality for Welding Instructors
Understanding current market conditions is crucial for aspiring and existing welding instructors. The landscape has evolved significantly over the past few years, influenced by post-pandemic shifts and the increasing integration of automation in manufacturing.
Broader economic factors, such as infrastructure spending and industrial growth, directly impact the demand for skilled welders and, consequently, the need for those who train them. Market realities for instructors vary by experience level, the type of institution, and regional industrial activity. This analysis offers an honest assessment to help you navigate these realities.
Current Challenges
Finding qualified instructors remains a hurdle, as many skilled welders prefer higher-paying industry jobs over teaching. This creates a supply-demand imbalance for educational institutions. Competition for top teaching roles can be high, especially in desirable geographic areas or at well-funded institutions.
Keeping curriculum current with rapid technological advancements in welding, including automated and robotic welding systems, demands continuous professional development. Securing funding for new equipment and lab upgrades often poses a significant challenge for vocational schools.
Growth Opportunities
Areas experiencing strong demand for welding instructors include institutions offering specialized training in advanced welding techniques, such as robotic welding, orbital welding, and pipe welding. These niche areas command higher salaries and require instructors with specific industry experience.
Emerging opportunities exist in developing and delivering customized corporate training programs for manufacturing firms upgrading their workforce. Instructors with expertise in welding inspection, quality control, or non-destructive testing also find strong demand. Professionals can position themselves advantageously by acquiring certifications in advanced welding processes and teaching methodologies.
Underserved markets often align with regions experiencing industrial revitalization or where older instructors are retiring. These areas may offer more immediate opportunities. Certifications in specific industry codes (e.g., ASME, AWS) and experience with a variety of welding processes provide a significant competitive advantage.
Market corrections or economic downturns can sometimes lead to increased enrollment in vocational programs as individuals seek new skills, potentially creating more teaching positions. Strategic career moves involve focusing on institutions with strong industry partnerships or those investing in state-of-the-art welding labs. Pursuing further education in educational technology or curriculum development also enhances an instructor's marketability.
Current Market Trends
Demand for skilled welders remains consistently strong across many industries, including manufacturing, construction, energy, and infrastructure. This sustained demand directly fuels the need for qualified welding instructors at vocational schools, community colleges, and private training centers. Hiring patterns show a steady, rather than explosive, growth for instructors, driven by program expansion and instructor retirements.
The integration of advanced technologies like robotic welding, laser welding, and additive manufacturing is reshaping curriculum requirements. Instructors must now teach not only traditional arc and MIG welding but also digital fabrication techniques and equipment operation. Employers increasingly seek graduates proficient in automated systems, placing pressure on instructors to update their own skills and teaching methods.
Economic conditions generally support vocational training, as companies invest in workforce development to address skill gaps. Layoffs in other sectors sometimes lead to increased enrollment in welding programs, indirectly boosting instructor demand. Salary trends for welding instructors are stable, often competitive with entry-level industry positions, but typically less than experienced, specialized welders.
Geographic variations are notable; regions with strong manufacturing or energy sectors, such as the Midwest or Gulf Coast, show higher demand for instructors. Remote work is not applicable for this hands-on role. There are no significant seasonal hiring patterns, as programs run year-round, though new instructor hires often align with academic terms.
Emerging Specializations
The welding industry is experiencing a significant transformation driven by advancements in automation, materials science, and digital technologies. This evolution creates distinct new specialization opportunities for welding instructors. Understanding these shifts and positioning oneself early in emerging areas is crucial for career advancement and securing premium compensation in 2025 and beyond.
Emerging specializations often command higher salaries due to the scarcity of expertise and the critical nature of these advanced skills. While established welding techniques remain fundamental, future-oriented instructors will find substantial growth by focusing on next-generation applications. These areas are not yet mainstream but are rapidly gaining traction, indicating a strong potential for significant job opportunities within the next few years.
Pursuing an emerging specialization involves a balance of risk and reward. It requires proactive learning and adaptation to new technologies and methodologies. However, the early adoption of these skills allows instructors to become leaders in their field, shaping the next generation of welders and securing a competitive edge in a rapidly evolving market.
Robotic Welding Systems Instructor
As robotic welding systems become more sophisticated and prevalent in manufacturing, the demand for instructors who can teach programming, operation, and troubleshooting of these advanced machines is soaring. This specialization involves understanding robotic kinematics, sensor integration, and software interfaces specific to welding applications. Instructors in this field prepare students for highly automated production environments, bridging the gap between traditional welding and industrial automation.
Additive Manufacturing (3D Metal Printing) Instructor
Additive manufacturing, particularly through processes like Wire Arc Additive Manufacturing (WAAM) and Laser Metal Deposition (LMD), is revolutionizing how complex metal parts are produced. Welding instructors specializing in these techniques teach students how to build three-dimensional objects layer by layer using welding principles. This area requires a deep understanding of material properties, deposition strategies, and post-processing techniques unique to 3D printing with metals, preparing students for cutting-edge manufacturing roles.
Advanced Materials Welding Instructor
The increasing use of specialized materials, such as advanced high-strength steels, aluminum alloys, titanium, and composites, demands instructors with expertise in their specific welding characteristics. This specialization focuses on the unique challenges and techniques required for joining these materials, including precise heat input control, shielding gas selection, and pre/post-weld treatments. Instructors in this area prepare welders for industries like aerospace, automotive, and energy, where material performance is critical.
Digital & Simulation-Based Welding Instructor
The integration of digital tools for design, simulation, and quality assurance is transforming welding education. Instructors specializing in virtual and augmented reality (VR/AR) welding simulators teach students using immersive digital environments that replicate real-world welding scenarios without consuming materials. This area also includes teaching data analytics for weld quality, predictive maintenance of welding equipment, and digital record-keeping, preparing students for smart factory environments and data-driven quality control.
Sustainable & Green Welding Practices Instructor
The growing emphasis on sustainable practices and energy efficiency within manufacturing impacts welding processes. Instructors specializing in green welding techniques focus on methods that reduce energy consumption, minimize waste, and utilize environmentally friendly materials. This includes teaching optimized processes that lower fume emissions, explore alternative energy sources for welding, and promote the use of recyclable or repurposed materials. This specialization aligns with global environmental regulations and corporate sustainability goals, preparing welders for eco-conscious industries.
Pros & Cons of Being a Welding Instructor
Choosing a career involves understanding both its appealing aspects and its genuine difficulties. A career as a Welding Instructor offers unique rewards but also distinct challenges. Experiences can vary significantly based on the type of educational institution, the specific curriculum, and the instructor's personal teaching philosophy. Factors like class size, available equipment, and student demographics also play a role. Some aspects considered a 'pro' by one individual, such as the routine of teaching, might be a 'con' for another who prefers less structure. Furthermore, the balance of pros and cons can shift as an instructor gains more experience or moves into different roles within the educational system. This assessment provides an honest overview to help set realistic expectations for this specialized teaching profession.
Pros
- Welding instructors derive significant satisfaction from sharing their expertise and seeing students develop practical skills, directly contributing to workforce development and individual career success.
- The work schedule often aligns with academic calendars, providing regular hours, weekends off, and extended breaks during holidays or summer, which can offer a good work-life balance.
- Instructors maintain and refine their own welding skills through demonstrations and practical instruction, ensuring their craftsmanship remains sharp and relevant.
- There is consistent demand for skilled trades education, providing a stable career path for experienced welders who transition into teaching roles.
- Teaching allows for a creative approach to problem-solving, as instructors must find innovative ways to explain complex welding concepts and troubleshoot student projects.
- Building a network with local industries and employers is common, as instructors often help place their graduates, which can open doors for consulting or part-time work.
Cons
- Dealing with students of varying skill levels and motivation can be challenging, requiring constant adaptation of teaching methods and patience, especially with those who struggle with practical application.
- The work environment can be noisy and physically demanding, as instructors often demonstrate techniques in a workshop setting, leading to exposure to fumes and potential for minor injuries.
- Salary progression for welding instructors in educational institutions may be slower compared to highly skilled production or industrial welding roles, often tied to fixed pay scales.
- Maintaining up-to-date knowledge and skills in welding technology and safety protocols requires continuous professional development, as techniques and equipment evolve frequently.
- Managing a classroom and workshop simultaneously demands strong organizational skills and attention to safety, as instructors must supervise multiple students operating potentially dangerous equipment.
- Job openings can be tied to the funding and needs of vocational schools or community colleges, potentially leading to fewer opportunities in certain geographic areas or during budget cuts.
Frequently Asked Questions
Welding Instructors face unique challenges balancing technical expertise with teaching methodologies. This section addresses the most common questions about transitioning into this rewarding role, from required certifications and teaching experience to salary expectations and the demand for qualified educators in the trades.
What qualifications and experience do I need to become a Welding Instructor?
Becoming a Welding Instructor typically requires significant industry experience, often 5-10 years, as a certified welder. Many institutions also look for an Associate's degree in welding technology or a related field, alongside specific welding certifications like AWS Certified Welding Inspector (CWI) or Certified Welding Educator (CWE). Some roles might require a teaching certification or completion of a 'train-the-trainer' program, especially in public education.
How long does it typically take to transition from a welder to a Welding Instructor?
The transition time varies depending on your existing credentials and the specific requirements of the institution. If you already have extensive welding experience and relevant certifications, you might need 6-12 months to acquire any necessary teaching certifications or complete a pedagogical training program. For those needing to gain more industry experience or advanced welding certifications, the path could take several years.
What are the typical salary expectations for a Welding Instructor, and what benefits are common?
Salaries for Welding Instructors can vary widely based on the type of institution (vocational school, community college, private academy), location, and your experience level. Entry-level instructors might earn $45,000-$60,000 annually, while experienced instructors with advanced certifications or leadership roles could make $70,000-$90,000+. Benefits packages often include health insurance, retirement plans, and tuition assistance.
What is the typical work-life balance like for a Welding Instructor compared to a production welder?
The work-life balance for a Welding Instructor is generally better than many production welding roles. Most instructors work a set schedule, often 40 hours a week, with evenings or weekends sometimes required for special classes or labs. Unlike project-based welding, teaching provides more predictable hours and often aligns with academic calendars, offering holidays and summer breaks.
Is there strong job security and market demand for Welding Instructors?
Job security for Welding Instructors is strong due to the persistent demand for skilled tradespeople and the aging workforce of current instructors. Vocational schools and community colleges consistently need qualified educators to train the next generation of welders. The field is stable and less susceptible to economic downturns than some other industries, as welding skills are always in demand across various sectors.
What are the potential career growth and advancement opportunities for a Welding Instructor?
Career growth for Welding Instructors can involve specializing in advanced welding techniques, developing new curriculum, or moving into administrative roles such as department head, program coordinator, or dean of trades. Opportunities also exist in corporate training for manufacturing companies or becoming a freelance welding consultant and trainer. Continuous professional development through new certifications and industry engagement is key.
Can Welding Instructors work remotely, or is it primarily an in-person role?
While some theoretical instruction can be delivered remotely, the hands-on nature of welding makes fully remote instruction challenging. Most Welding Instructor roles require significant in-person presence in a lab setting to supervise practical exercises, ensure safety, and provide direct, real-time feedback. Hybrid models, combining online lectures with in-person lab work, are becoming more common, but purely remote positions are rare.
What are the biggest challenges a Welding Instructor might face when starting out?
One significant challenge is adapting your expert practical skills into effective teaching methods for diverse learners. You must be able to break down complex welding processes into understandable steps, manage a classroom and lab environment, and assess student progress fairly. Staying current with evolving welding technologies and industry standards also requires continuous learning and professional development.
Related Careers
Explore similar roles that might align with your interests and skills:
Welding Supervisor
A growing field with similar skill requirements and career progression opportunities.
Explore career guideBuilding Trades Instructor
A growing field with similar skill requirements and career progression opportunities.
Explore career guideIndustrial Electrical Technology Instructor
A growing field with similar skill requirements and career progression opportunities.
Explore career guideIndustrial Maintenance Instructor
A growing field with similar skill requirements and career progression opportunities.
Explore career guideMachine Tool Technician Instructor
A growing field with similar skill requirements and career progression opportunities.
Explore career guideAssess your Welding Instructor readiness
Understanding where you stand today is the first step toward your career goals. Our Career Coach helps identify skill gaps and create personalized plans.
Skills Gap Analysis
Get a detailed assessment of your current skills versus Welding Instructor requirements. Our AI Career Coach identifies specific areas for improvement with personalized recommendations.
See your skills gapCareer Readiness Assessment
Evaluate your overall readiness for Welding Instructor roles with our AI Career Coach. Receive personalized recommendations for education, projects, and experience to boost your competitiveness.
Assess your readinessSimple pricing, powerful features
Upgrade to Himalayas Plus and turbocharge your job search.
Himalayas
Himalayas Plus
Himalayas Max
Find your dream job
Sign up now and join over 100,000 remote workers who receive personalized job alerts, curated job matches, and more for free!
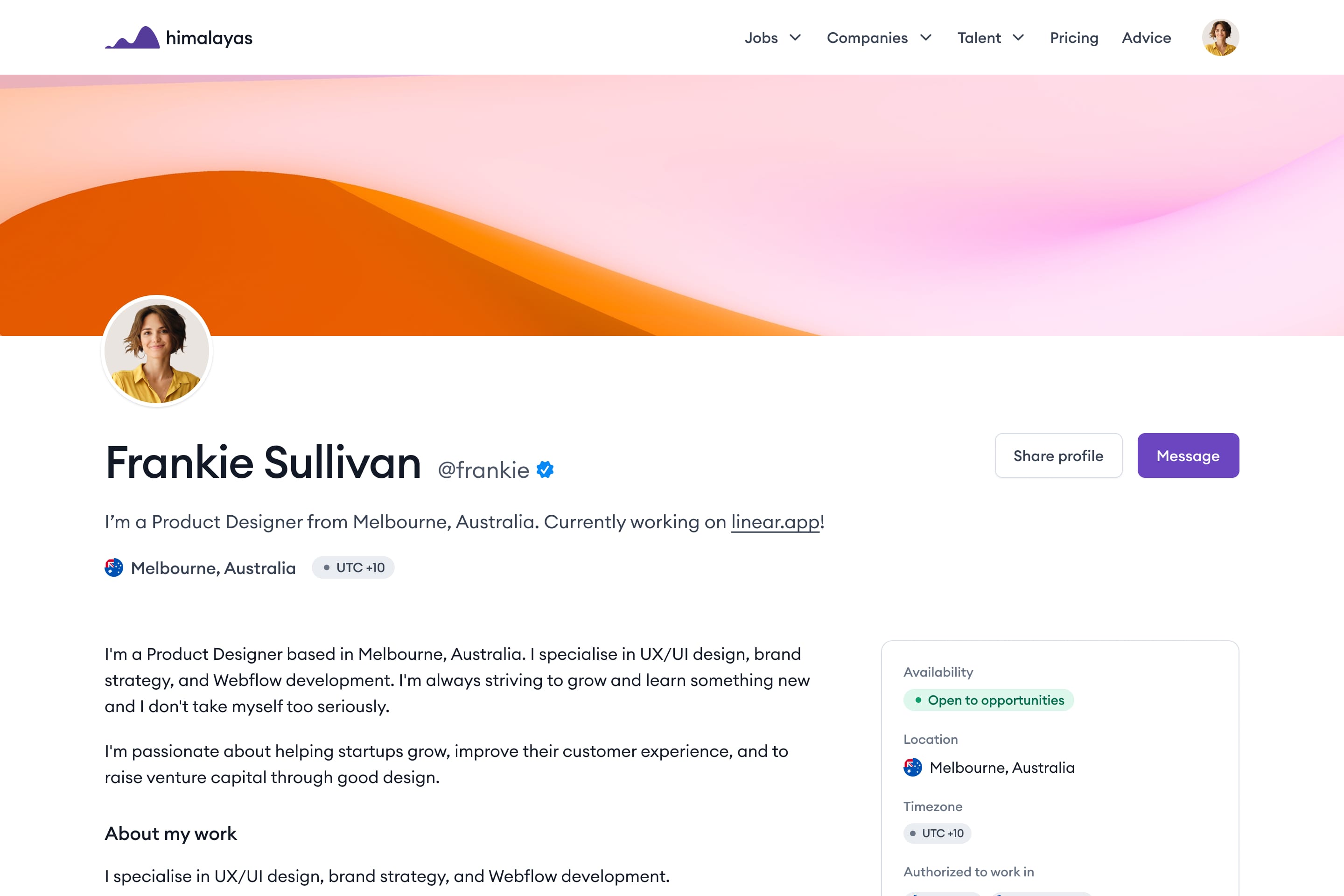