Complete Warehouse Stocker Career Guide
Warehouse stockers are the backbone of modern supply chains, ensuring products move efficiently from receiving docks to storage, and then out for shipment. They play a critical role in maintaining inventory accuracy and operational flow, directly impacting a company's ability to deliver goods to customers. This hands-on role offers a clear path into the logistics industry, providing essential skills for a dynamic and growing sector.
Key Facts & Statistics
Median Salary
$37,290 USD
(U.S. national median, BLS, May 2023)
Range: $29k - $49k+ USD, varying by experience and location
Growth Outlook
0%
as fast as average (BLS, 2022-2032)
Annual Openings
≈300,000
openings annually (BLS, 2022-2032)
Top Industries
Typical Education
High school diploma or equivalent; on-the-job training is common
What is a Warehouse Stocker?
A Warehouse Stocker is a critical logistics professional responsible for the efficient and accurate management of incoming and outgoing inventory within a warehouse or distribution center. This role focuses on the physical handling, organization, and storage of goods, ensuring that products are correctly received, placed, and made available for order fulfillment or shipment. They maintain the structural integrity and accessibility of the warehouse's inventory.
This position differs significantly from a 'Warehouse Associate' or 'Order Picker.' While a Warehouse Associate might perform a broader range of tasks including picking and packing, the Stocker specifically specializes in the 'putting away' and 'replenishing' aspects of inventory. An 'Order Picker' focuses on retrieving items for specific customer orders. The Stocker's primary value lies in maintaining an organized, accurate, and accessible inventory system, which directly impacts the efficiency of all other warehouse operations.
What does a Warehouse Stocker do?
Key Responsibilities
- Unload incoming shipments from trucks, verifying the quantity and type of items against packing lists and purchase orders.
- Inspect products for damage or discrepancies upon arrival, reporting any issues to a supervisor or inventory manager.
- Organize and store inventory in designated warehouse locations, ensuring proper labeling and accessibility for retrieval.
- Operate forklifts, pallet jacks, or other material handling equipment to move large or heavy items safely within the warehouse.
- Replenish picking locations and shelves with products from bulk storage to maintain efficient order fulfillment.
- Conduct regular inventory counts and reconcile physical stock with system records to ensure accuracy.
- Maintain a clean and organized work area, adhering to all safety protocols and warehouse procedures.
Work Environment
Warehouse Stockers typically work in large, often bustling warehouse or distribution center environments. These spaces can be noisy due to machinery and activity, and temperatures may vary depending on the product being stored (e.g., refrigerated sections). The role requires significant physical activity, including lifting, bending, standing for long periods, and walking across large areas. Collaboration with receiving, shipping, and order fulfillment teams is common, but much of the work involves independent task execution. Schedules often include early mornings, evenings, or weekend shifts, and the pace of work can be fast, especially during peak seasons or for e-commerce operations. This role is almost exclusively on-site with no remote work possibilities.
Tools & Technologies
Warehouse Stockers primarily use material handling equipment such as pallet jacks, hand trucks, and forklifts (requiring certification) to move goods. They interact with inventory management systems (IMS) or warehouse management systems (WMS) to scan items, update stock levels, and track locations. Common software includes systems like SAP, Oracle WMS Cloud, or specialized proprietary systems for inventory tracking. Stockers also use barcode scanners, computers, and tablets for data entry and verification. Safety equipment, including gloves, safety vests, and steel-toed boots, is essential for daily operations. Depending on the warehouse, they might also use strapping machines or shrink wrap equipment.
Warehouse Stocker Skills & Qualifications
A Warehouse Stocker plays a critical role in maintaining the efficiency and accuracy of inventory within a warehouse or distribution center. This position is fundamentally about the physical handling, organization, and tracking of goods. Qualification for this role primarily emphasizes practical experience and a strong work ethic over formal academic degrees.
Requirements for a Warehouse Stocker vary significantly based on the size and type of the operation. Larger fulfillment centers often prioritize speed and technological familiarity, requiring comfort with handheld scanners and inventory management systems. Smaller warehouses might value versatility and a broader range of manual handling skills. Industry sector also plays a role; for example, a food warehouse might require specific sanitation training, while a manufacturing warehouse could demand familiarity with heavy machinery operation.
Formal education typically holds less weight than demonstrated capability in this field. A high school diploma or equivalent is often a baseline, but practical experience in a similar setting or a proven ability to follow instructions and perform physical tasks consistently is often more important. Certifications, such as forklift operation or specialized equipment training, significantly enhance a candidate's value and can open doors to higher-paying or more specialized stocker roles. The skill landscape for stockers is evolving, with increasing automation requiring a blend of physical dexterity and technical proficiency with warehouse management software. Basic data entry and familiarity with digital tools are becoming increasingly important for accurate inventory tracking.
Education Requirements
Technical Skills
- Inventory management systems (e.g., WMS, ERP basic functions)
- Handheld scanner operation for barcode scanning and data entry
- Pallet jack operation (manual and electric)
- Forklift operation (sit-down, stand-up, reach truck - depending on facility)
- Basic computer literacy for data entry and system navigation
- Material handling equipment operation (e.g., dollies, hand trucks)
- Stock rotation and FIFO (First-In, First-Out) principles
- Loading and unloading procedures and safety
Soft Skills
- Attention to detail: Crucial for accurate inventory placement, picking, and preventing errors in stock counts.
- Physical stamina: Essential for standing, lifting, bending, and moving heavy items for extended periods.
- Time management: Important for completing stocking tasks efficiently and meeting daily quotas.
- Team collaboration: Necessary for coordinating with other stockers, pickers, and supervisors to maintain workflow.
- Problem-solving: Required for identifying and resolving discrepancies in inventory or shelving issues.
- Adherence to safety protocols: Vital for preventing accidents and injuries in a busy warehouse environment.
- Dependability: Employers rely on stockers to be punctual and consistently perform their duties.
- Adaptability: Needed to adjust to changing priorities, new inventory layouts, or different equipment quickly and effectively.
How to Become a Warehouse Stocker
Entering the warehouse stocker field offers multiple pathways, typically favoring practical skills and reliability over formal education. While some large corporations might prefer candidates with a high school diploma, many smaller operations prioritize a strong work ethic and the ability to learn quickly. The timeline for securing a position can be as short as a few weeks for entry-level roles, especially in regions with high logistics activity.
Traditional entry often involves applying directly for open positions, but non-traditional routes like temporary staffing agencies can provide a faster entry point and valuable initial experience. Geographic location significantly impacts opportunities; major distribution hubs and industrial zones will have more frequent openings than rural areas. Misconceptions often include the belief that heavy lifting is the only requirement; precision, organization, and basic inventory management skills are equally crucial.
Building a reputation for reliability and attention to detail is paramount. While a formal portfolio is not required, demonstrating a history of punctuality and a willingness to follow procedures through references or past employment will significantly enhance a candidate's appeal. The hiring landscape values efficiency and safety, making any prior experience in logistics or a fast-paced environment a strong asset.
Step 1
Step 2
Step 3
Step 4
Step 5
Step 6
Step 7
Education & Training Needed to Become a Warehouse Stocker
Becoming a Warehouse Stocker primarily involves practical skills and efficiency, rather than extensive formal education. Many roles require only a high school diploma or GED. Employers prioritize reliability, physical stamina, and the ability to follow instructions. While some entry-level positions offer on-the-job training, basic certifications in safety or equipment operation can significantly improve job prospects and starting wages.
Formal degree programs are generally not necessary for this role. Instead, vocational training, community college courses in logistics or supply chain fundamentals, or specific certifications are more relevant. A 4-year degree offers little direct benefit for a stocker position and incurs substantial costs, typically $40,000-$100,000+, with a 4-year time commitment. In contrast, short vocational courses or certifications can range from a few hundred to a few thousand dollars and take 1-6 weeks. Self-study of safety protocols and warehouse procedures can take 1-3 months.
Employers value practical experience and demonstrated competence. Certifications such as OSHA 10 or forklift operation demonstrate a proactive approach to safety and efficiency. These credentials are widely recognized and often preferred. Continuous learning in areas like inventory management software or advanced material handling techniques can lead to promotions to roles like lead stocker or warehouse associate. The cost-benefit analysis strongly favors targeted, short-term training over lengthy academic programs for a Warehouse Stocker role.
Warehouse Stocker Salary & Outlook
Compensation for a Warehouse Stocker reflects a blend of geographic, experience, and operational factors. Location significantly impacts earnings, with higher cost-of-living areas and major logistical hubs often offering better wages due to increased demand and local economic conditions. For instance, salaries in urban centers or states with large port operations typically exceed those in rural areas. International markets also vary widely, so the figures provided are in USD and reflect the U.S. context.
Years of experience directly correlate with earning potential; entry-level positions command lower wages than senior or specialized roles. Specific skill sets like forklift operation certification, proficiency with inventory management software, or experience with automated systems can also lead to higher pay. Total compensation extends beyond base salary to include overtime pay, performance bonuses for efficiency or accuracy, and benefits packages. These often encompass health insurance, retirement contributions, and paid time off, significantly adding to overall value.
Industry-specific trends, such as the growth of e-commerce and the need for rapid fulfillment, can drive salary growth for skilled stockers. Larger companies or those with highly automated warehouses may offer more competitive packages. Negotiation leverage comes from demonstrating reliability, efficiency, and a willingness to adapt to new technologies. Remote work is not applicable to this hands-on role, but geographic arbitrage can occur if individuals relocate to areas with lower living costs while maintaining higher-paying positions, although this is less common for stockers.
Salary by Experience Level
Level | US Median | US Average |
---|---|---|
Entry-Level Warehouse Stocker | $33k USD | $35k USD |
Warehouse Stocker | $37k USD | $39k USD |
Senior Warehouse Stocker | $42k USD | $44k USD |
Warehouse Team Lead | $47k USD | $49k USD |
Warehouse Supervisor | $55k USD | $58k USD |
Market Commentary
The job market for Warehouse Stockers shows consistent demand, largely driven by the ongoing expansion of e-commerce and the need for efficient supply chain operations. The Bureau of Labor Statistics projects a steady growth for material moving machine operators, which includes stockers, indicating a stable outlook. Automation and AI are impacting the broader warehousing sector, but the need for human stockers remains crucial for tasks requiring dexterity, problem-solving, and handling varied items that robots cannot yet manage effectively.
Emerging opportunities for stockers include roles in highly specialized warehouses, such as those handling cold storage, hazardous materials, or high-value goods, which often require additional training and offer better pay. The increasing complexity of inventory management systems also means stockers with tech-savviness or a willingness to learn new software have an advantage. The supply of qualified candidates generally meets demand, but specific skills or certifications can create a competitive edge.
This profession is relatively recession-resistant due to the essential nature of logistics and goods movement, though economic downturns can slow growth. Geographic hotspots for employment include major distribution centers, port cities, and areas with significant manufacturing or retail activity. Future-proofing involves continuous learning, embracing new technologies like augmented reality for picking, and adapting to increasingly automated environments to remain valuable assets within the evolving warehouse ecosystem.
Warehouse Stocker Career Path
Career progression for a Warehouse Stocker involves a clear ladder, primarily focused on increasing efficiency, responsibility, and leadership within warehouse operations. Individuals typically begin with foundational tasks, gradually taking on more complex assignments and eventually supervising teams. This path emphasizes operational excellence and team coordination.
Advancement speed depends on performance, reliability, and a willingness to learn new systems and equipment. Specialization in areas like inventory management systems or specific material handling equipment can accelerate progression. Company size significantly impacts career paths; larger corporations often have more structured advancement programs and diverse roles, while smaller operations might offer broader responsibilities earlier.
Lateral movement opportunities within the warehouse sector include transitioning into inventory control, logistics coordination, or quality assurance roles. Continuous learning in safety protocols, warehouse management software, and efficient stocking techniques is crucial. Building a reputation for meticulous work and problem-solving helps with internal promotions and industry recognition. Networking within the company and with logistics professionals can open doors to supervisory or management positions.
Entry-Level Warehouse Stocker
0-1 yearKey Focus Areas
Warehouse Stocker
1-3 yearsKey Focus Areas
Senior Warehouse Stocker
3-5 yearsKey Focus Areas
Warehouse Team Lead
5-8 years total experienceKey Focus Areas
Warehouse Supervisor
8-12 years total experienceKey Focus Areas
Entry-Level Warehouse Stocker
0-1 yearAn Entry-Level Warehouse Stocker performs basic tasks like unloading incoming shipments, organizing products on shelves, and preparing outgoing orders. This role operates under direct supervision, focusing on completing assigned tasks accurately and safely. Impact is primarily on individual task completion and maintaining an organized work area.
Key Focus Areas
Develop foundational skills in item identification, proper lifting techniques, and basic safety protocols. Learn to operate manual pallet jacks and hand trucks efficiently. Focus on accuracy in picking and placing items, and understanding basic warehouse layout.
Warehouse Stocker
1-3 yearsA Warehouse Stocker handles a wider range of products and stocking procedures. This role involves more independent work, including verifying inventory counts, restocking shelves, and assisting with cycle counts. They contribute to maintaining accurate inventory records and ensuring product availability.
Key Focus Areas
Refine efficiency in stocking and picking processes. Understand inventory rotation principles (FIFO/LIFO). Begin to learn basic warehouse management system (WMS) functions for tracking inventory. Develop problem-solving skills for common stocking issues.
Senior Warehouse Stocker
3-5 yearsA Senior Warehouse Stocker takes on more complex stocking assignments and often handles high-value or difficult-to-manage inventory. This role acts as a resource for less experienced stockers, troubleshooting issues, and ensuring adherence to safety and efficiency standards. They contribute to optimizing warehouse flow and inventory accuracy.
Key Focus Areas
Master advanced WMS functionalities and data entry. Develop expertise in handling specialized equipment like forklifts (requiring certification). Improve communication skills for coordinating with other departments. Begin mentoring newer stockers and identifying process improvements.
Warehouse Team Lead
5-8 years total experienceA Warehouse Team Lead directly oversees a small group of stockers, coordinating daily tasks, ensuring productivity, and addressing immediate operational issues. This role is responsible for team performance, adherence to schedules, and maintaining a safe working environment. They serve as the primary point of contact for their team and report to supervisors.
Key Focus Areas
Develop leadership and delegation skills, effectively assigning tasks and monitoring progress. Learn conflict resolution and motivation techniques for team members. Understand key performance indicators (KPIs) for warehouse operations. Begin participating in training and onboarding processes.
Warehouse Supervisor
8-12 years total experienceA Warehouse Supervisor manages overall daily operations for a section or shift within the warehouse. This role involves planning staff schedules, managing inventory levels, overseeing equipment maintenance, and ensuring all safety protocols are followed. They are responsible for meeting operational targets, improving efficiency, and developing their team members.
Key Focus Areas
Acquire strong analytical skills for data-driven decision-making in inventory and logistics. Master advanced safety regulations and compliance. Develop talent management skills, including performance reviews and disciplinary actions. Focus on strategic planning for warehouse layout and efficiency improvements.
Job Application Toolkit
Ace your application with our purpose-built resources:
Warehouse Stocker Cover Letter Examples
Personalizable templates that showcase your impact.
View examplesWarehouse Stocker Job Description Template
Ready-to-use JD for recruiters and hiring teams.
View examplesGlobal Warehouse Stocker Opportunities
The Warehouse Stocker role translates globally as a fundamental position in logistics and supply chain operations. International demand remains consistent across e-commerce, manufacturing, and retail sectors, especially with growing global trade. Regulatory differences in safety standards and equipment use vary by country. Professionals consider international roles for better pay or living conditions. No specific international certifications are typically required for this role, as skills are largely transferable.
Global Salaries
Warehouse Stocker salaries vary significantly worldwide, reflecting local economic conditions and cost of living. In North America, a Warehouse Stocker in the United States earns between $30,000 and $45,000 USD annually, while in Canada, it ranges from $35,000 to $50,000 CAD (approx. $25,000-$36,000 USD). These figures often include benefits like health insurance and paid time off.
European salaries differ by region. In Western Europe, countries like Germany or the Netherlands offer €25,000-€35,000 (approx. $27,000-$38,000 USD) annually. Eastern European countries like Poland or Hungary might offer €10,000-€15,000 (approx. $11,000-$16,000 USD). Scandinavian countries, with higher costs of living, offer higher nominal wages, around €30,000-€40,000 (approx. $32,000-$43,000 USD), but purchasing power might be similar to Western Europe.
In Asia-Pacific, salaries are lower. Australia offers AUD 45,000-AUD 55,000 (approx. $30,000-$37,000 USD), while in Southeast Asia, such as Vietnam or Thailand, a stocker might earn $3,000-$6,000 USD annually. Latin American countries like Mexico typically offer $6,000-$10,000 USD per year. Tax implications and social security contributions vary greatly, impacting take-home pay. Experience has a moderate impact on compensation, with long-term stockers earning slightly more, but entry-level education credentials do not significantly affect pay scales internationally for this role.
Remote Work
International remote work opportunities are virtually non-existent for Warehouse Stockers. This role requires physical presence to handle inventory, load/unload goods, and organize warehouse spaces. The nature of the work, involving tangible products and specific equipment, makes it impossible to perform remotely.
Digital nomad opportunities do not apply to this profession. Companies do not hire Warehouse Stockers for international remote work. Salary expectations for this role are always tied to the physical location of the warehouse. Equipment needs are specific to the warehouse environment, including forklifts, pallet jacks, and safety gear, which are not suitable for a remote setup.
Visa & Immigration
For Warehouse Stockers seeking international work, common visa categories include temporary work visas for low-skilled or semi-skilled labor. Many countries have specific programs for roles experiencing labor shortages. Popular destinations often include Canada (Seasonal Agricultural Worker Program or certain Provincial Nominee Programs that might include general labor), Australia (Working Holiday Visa or specific regional sponsored visas), and parts of Europe (seasonal work permits in logistics or agriculture).
Requirements typically involve a job offer from an employer, a clean criminal record, and sometimes a basic English or host country language proficiency. Educational credential recognition is generally not a significant hurdle for this role, as formal degrees are rarely required. The application process usually involves the employer sponsoring the visa and can take a few weeks to several months, depending on the country and visa type.
Pathways to permanent residency are limited directly through this role, often requiring several years of continuous work and meeting other immigration criteria. Family visas for dependents are usually available if the primary applicant secures a long-term work permit. There are no profession-specific fast-track immigration programs for Warehouse Stockers, given the nature of the work.
2025 Market Reality for Warehouse Stockers
Understanding current market realities is crucial for anyone pursuing a warehouse stocker career. The logistics sector has undergone significant evolution, particularly in the post-pandemic era and with the advent of increased automation. This has reshaped job availability and skill requirements.
Broader economic factors directly influence warehouse operations; a strong economy generally means higher consumer spending and thus more goods needing to be stocked. Market realities for stockers vary by experience level, as experienced individuals might transition into lead roles, and by geographic region, with higher demand in e-commerce hubs. Company size also matters, as large distribution centers often have different operational scales and technology integrations than smaller local warehouses. This analysis provides an honest assessment to help job seekers navigate these dynamics.
Current Challenges
Warehouse stockers face increased competition, especially at entry levels, due to a steady supply of candidates. Economic uncertainty can lead to hiring freezes or slower expansion for some companies. Automation is a growing concern, as some tasks previously done by stockers are now handled by machines, potentially reducing demand for manual labor in certain facilities. Job searches might take longer as companies optimize staffing.
Growth Opportunities
Despite automation, strong demand persists for warehouse stockers in specific areas. Facilities handling fresh produce, pharmaceuticals, or oversized goods often require a human touch due to product fragility or unique handling needs. Smaller, local distribution centers and third-party logistics (3PL) providers serving diverse client bases also offer consistent opportunities.
Emerging opportunities exist for stockers willing to cross-train on automated systems, such as operating automated guided vehicles (AGVs) or interacting with robotic picking arms. Professionals who demonstrate strong organizational skills, attention to detail, and a proactive approach to learning new warehouse management software gain a competitive advantage. Underserved markets in rural areas or regions with new industrial park developments often have better opportunities due to less competition.
Certain skills like forklift certification, proficiency with inventory software, or experience with quality control processes provide significant competitive advantages. Companies value stockers who can identify inefficiencies or improve picking accuracy. Market corrections might create opportunities as some companies scale back on expensive automation, temporarily increasing reliance on manual labor. The retail and food distribution sectors remain strong, offering stable employment for stockers. Investing in certifications for equipment operation or basic IT skills for logistics software can significantly enhance career prospects and timing these certifications with peak hiring seasons can be beneficial.
Current Market Trends
Demand for warehouse stockers remains steady in 2025, driven by the continued growth of e-commerce and the need for efficient supply chains. While overall demand is consistent, some facilities are implementing more automation, which shifts stocker responsibilities towards operating machinery, quality control, or more specialized inventory management rather than purely manual stocking. This means employers increasingly seek candidates with basic tech literacy or a willingness to learn new systems.
Economic conditions have had a mixed impact. While some sectors saw layoffs, the logistics and warehousing industries largely maintained or increased staffing to handle consumer demand. However, companies are now more focused on efficiency, meaning fewer purely manual roles and more roles requiring adaptability to new tech. Salary trends show modest increases, largely influenced by local cost of living and the level of automation in a specific warehouse. Market saturation varies; highly automated warehouses might have fewer openings, while traditional facilities still hire consistently.
Technology trends, particularly robotics and advanced inventory software, are reshaping the stocker role. Generative AI is not directly impacting stockers, but AI-driven logistics systems are optimizing warehouse layouts and picking paths, requiring stockers to follow precise digital instructions. This emphasizes accuracy and adherence to system guidelines over manual decision-making. Employer requirements now often include basic computer skills, familiarity with handheld scanners, and a strong safety orientation. Remote work is not applicable to this hands-on role. Seasonal hiring peaks remain significant during holiday seasons and major sales events, requiring temporary increases in staffing.
Emerging Specializations
Technological advancements and evolving supply chain dynamics are creating new specialization opportunities even within traditionally hands-on roles like the Warehouse Stocker. Understanding these shifts allows professionals to position themselves for next-generation career paths. Early positioning in these emerging areas, particularly from 2025 onwards, often leads to enhanced career advancement and can command premium compensation.
While established specializations offer stability, pursuing emerging areas provides a strategic advantage. These cutting-edge roles integrate new technologies and processes, making individuals indispensable as industries modernize. Emerging specializations typically take a few years to become mainstream, offering a window for proactive professionals to develop expertise before the market becomes saturated.
Embracing these new specializations involves a balance of risk and reward. While some areas are still developing, the potential for significant career growth and higher earning potential is substantial. Investing in relevant skills now prepares Warehouse Stockers for a future where their roles are increasingly augmented by automation and data, rather than replaced.
Automated System Stocker
AR-Guided Stocker
Drone-Assisted Inventory Stocker
Specialized Materials Stocker
Data-Optimized Layout Stocker
Pros & Cons of Being a Warehouse Stocker
Understanding both the advantages and challenges of a career is crucial for making informed decisions. Career experiences can vary significantly based on company culture, the specific industry sector, and individual preferences or personality. What one person views as a benefit, another might see as a drawback. Furthermore, the pros and cons may shift at different stages of a career, from early entry-level positions to more senior roles. This assessment provides an honest, balanced overview to help set realistic expectations for a Warehouse Stocker role.
Pros
The role typically has low barriers to entry, often requiring only a high school diploma or equivalent, making it accessible for individuals without extensive prior experience or higher education.
Warehouse stocker positions are generally in high demand across various industries, offering good job security and consistent employment opportunities, especially with the growth of e-commerce.
This job provides a consistent routine and clear tasks, which can be appealing for individuals who prefer structured work environments with predictable daily responsibilities.
Many companies offer opportunities for overtime hours, allowing stockers to increase their earnings, particularly during peak seasons or busy periods.
It offers a physically active work environment, which can be a pro for those who prefer to be on their feet and engaged in physical tasks rather than sedentary office work.
The role allows for immediate entry into the workforce and provides practical experience in logistics, inventory management, and supply chain operations, which can be foundational for other roles.
Some companies provide basic benefits packages, including health insurance and paid time off, which can be a significant advantage for entry-level positions.
Cons
The work can be physically demanding, involving repetitive lifting, bending, and carrying heavy items, which may lead to muscle strain or injuries over time.
Warehouse environments often have temperature extremes, being very cold in winter or hot in summer, which can make working conditions uncomfortable for long shifts.
The job typically offers limited opportunities for upward career mobility within the warehouse, with few advanced roles beyond lead stocker or supervisor positions.
Many stocker roles involve night shifts, early mornings, or weekend work, which can disrupt personal and social life and make maintaining a regular schedule difficult.
The work can be monotonous and repetitive, performing the same tasks for extended periods, which may lead to boredom or a lack of intellectual stimulation for some individuals.
Pay for warehouse stockers is often near minimum wage, providing limited financial growth potential without moving into management or specialized roles.
There is a constant pressure to meet quotas and maintain efficiency, leading to a fast-paced environment where errors can significantly impact productivity and inventory accuracy.
Frequently Asked Questions
Warehouse Stockers face unique challenges around physical demands, efficiency, and safety within a fast-paced environment. This section addresses common questions about entering this role, from the necessary physical abilities to opportunities for advancement and managing the daily grind.
What are the basic educational or experience requirements to become a Warehouse Stocker?
A high school diploma or GED is usually sufficient for entry-level Warehouse Stocker positions. Employers prioritize a strong work ethic, reliability, and the physical ability to perform the job's demands. While not always required, some roles may prefer candidates with basic experience using forklifts or pallet jacks, often providing on-the-job training for these skills.
How long does it take to become proficient and job-ready as a Warehouse Stocker?
Most individuals can become job-ready for a Warehouse Stocker role relatively quickly, often within a few weeks of starting. Many companies offer comprehensive on-the-job training that covers safety protocols, inventory systems, and equipment operation. The primary learning curve involves adapting to the specific warehouse layout and workflow, which typically takes a short period of focused effort.
What is the typical work-life balance like, considering shift work and physical demands?
The work-life balance for a Warehouse Stocker can vary significantly based on the employer and industry. Many warehouses operate 24/7, offering various shifts including nights, weekends, and holidays. While this can provide flexibility for some, it often means irregular hours or working during peak seasons. Overtime is common and can impact personal time, so it's important to clarify typical schedules during the interview process.
How stable is the job market for Warehouse Stockers, and is it affected by automation?
Job security for Warehouse Stockers is generally stable, driven by the continuous demand for goods and efficient supply chains. E-commerce growth, in particular, has increased the need for skilled warehouse personnel. While automation is advancing, human oversight and manual stocking remain essential in many operations, ensuring a consistent need for these roles.
What are the common career advancement opportunities for a Warehouse Stocker?
Career growth for Warehouse Stockers often involves moving into supervisory roles, inventory management, or specialized equipment operation. With experience, you can pursue positions like Lead Stocker, Inventory Clerk, or Forklift Operator. Some companies also offer pathways to logistics coordination or warehouse management, often requiring additional training or certifications in supply chain operations.
What are the salary expectations and benefits for a Warehouse Stocker?
Compensation for Warehouse Stockers typically ranges from entry-level hourly wages to slightly higher rates with experience or specialized skills. Pay varies by location, company size, and industry. Many roles offer benefits like health insurance and retirement plans. Overtime hours can significantly boost earnings, especially during busy periods like holiday seasons.
How physically demanding is the job, and what are the common health considerations?
The physical demands of a Warehouse Stocker role are significant, involving frequent lifting, bending, standing for long periods, and moving heavy items. It requires good physical stamina and the ability to lift up to 50 pounds regularly. While challenging, proper lifting techniques, safety training, and adequate rest can help manage the physical toll and reduce the risk of injury.
Related Careers
Explore similar roles that might align with your interests and skills:
Stocker
A growing field with similar skill requirements and career progression opportunities.
Explore career guideStockroom Associate
A growing field with similar skill requirements and career progression opportunities.
Explore career guideRetail Stocker
A growing field with similar skill requirements and career progression opportunities.
Explore career guideStockroom Attendant
A growing field with similar skill requirements and career progression opportunities.
Explore career guideStore Stocker
A growing field with similar skill requirements and career progression opportunities.
Explore career guideAssess your Warehouse Stocker readiness
Understanding where you stand today is the first step toward your career goals. Our Career Coach helps identify skill gaps and create personalized plans.
Skills Gap Analysis
Get a detailed assessment of your current skills versus Warehouse Stocker requirements. Our AI Career Coach identifies specific areas for improvement with personalized recommendations.
See your skills gapCareer Readiness Assessment
Evaluate your overall readiness for Warehouse Stocker roles with our AI Career Coach. Receive personalized recommendations for education, projects, and experience to boost your competitiveness.
Assess your readinessSimple pricing, powerful features
Upgrade to Himalayas Plus and turbocharge your job search.
Himalayas
Himalayas Plus
Himalayas Max
Find your dream job
Sign up now and join over 100,000 remote workers who receive personalized job alerts, curated job matches, and more for free!
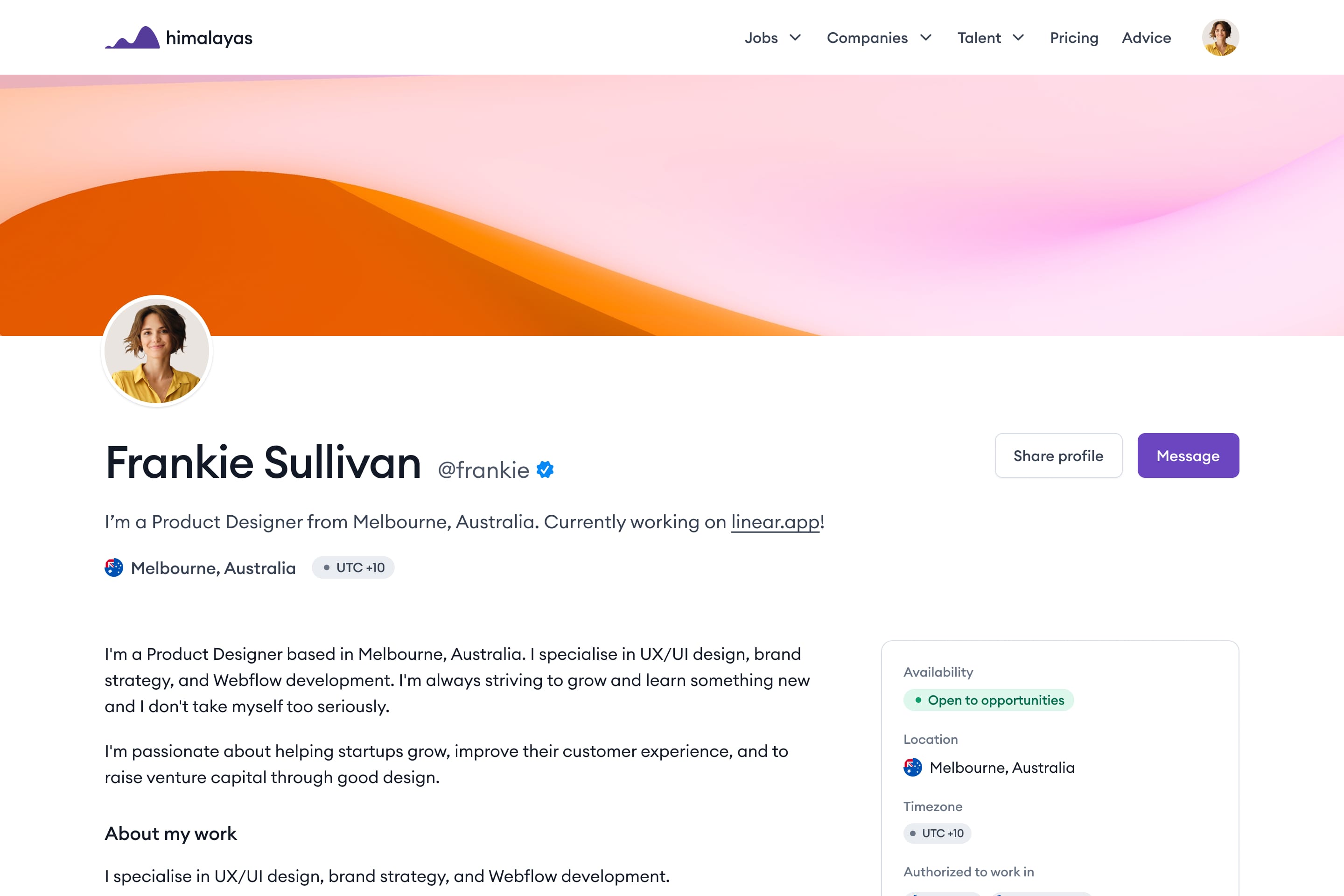