Complete Speed Belt Sander Career Guide
A Speed Belt Sander operates specialized machinery to precisely smooth and finish surfaces, primarily in manufacturing and woodworking. This role demands meticulous attention to detail and a steady hand, directly impacting the quality and aesthetics of final products from furniture to automotive parts. You play a crucial part in preparing materials for subsequent processes or delivering a flawless finished surface, making it a foundational skill in various production lines.
Key Facts & Statistics
Median Salary
$39,590 USD
(U.S. national median, Source: U.S. Bureau of Labor Statistics, May 2023, for 'Woodworking Machine Setters, Operators, and Tenders')
Range: $30k - $55k+ USD
Growth Outlook
0%
as fast as average (Source: U.S. Bureau of Labor Statistics, for 'Woodworking Machine Setters, Operators, and Tenders', 2022-2032)
Annual Openings
≈30k
openings annually (Source: U.S. Bureau of Labor Statistics, for 'Woodworking Machine Setters, Operators, and Tenders')
Top Industries
Typical Education
High school diploma or equivalent; on-the-job training
What is a Speed Belt Sander?
A Speed Belt Sander is a skilled production worker who operates and maintains specialized machinery designed to smooth, finish, and shape various materials using abrasive belts. This role is crucial in manufacturing and fabrication, preparing surfaces for painting, coating, assembly, or final inspection by removing imperfections, burrs, or excess material.
Unlike a general laborer who might use basic hand tools for sanding, a Speed Belt Sander possesses expertise in selecting appropriate abrasive types, adjusting machine parameters for different materials and desired finishes, and ensuring precision. Their focus is on achieving specific surface quality and dimensional accuracy, making them integral to product quality and efficiency in industries ranging from woodworking and metal fabrication to plastics manufacturing and automotive production.
What does a Speed Belt Sander do?
Key Responsibilities
- Operate fixed or portable belt sanders to smooth and finish surfaces of wood, metal, or plastic components.
- Inspect surfaces for imperfections, such as scratches, dents, or rough spots, before and after sanding.
- Select appropriate abrasive belts and grit sizes based on the material type and desired finish.
- Adjust machine settings, including belt tension and speed, to achieve optimal sanding results.
- Clean and maintain sanding equipment, replacing worn belts and ensuring proper functioning.
- Measure and verify dimensions of sanded parts using calipers, rulers, or other measuring tools.
- Follow safety protocols, including wearing personal protective equipment and maintaining a clean work area.
Work Environment
A Speed Belt Sander typically works in a manufacturing plant, workshop, or fabrication facility. The environment is often noisy due to machinery operation and can be dusty, requiring good ventilation systems. Operators usually work standing for extended periods, maneuvering parts on and off the sanding equipment. Collaboration is common with other production line workers, quality control inspectors, and supervisors to ensure product flow and quality standards. Shifts can be standard day hours, but some facilities operate 24/7, requiring evening or night shifts. The pace of work is steady and production-driven, focused on efficiency and meeting output targets. Overtime may be available during peak production periods.
Tools & Technologies
Speed Belt Sanders utilize specialized sanding machines, which can be stationary industrial models or handheld portable units. Operators select and change various abrasive belts, distinguished by grit size (e.g., 60-grit for rough shaping, 220-grit for fine finishing), material composition, and backing type. They also use measuring tools like calipers, micrometers, and tape measures to ensure parts meet specifications. Common hand tools for machine adjustments and maintenance include wrenches, screwdrivers, and air hoses for cleaning. Personal protective equipment (PPE) like safety glasses, dust masks or respirators, hearing protection, and gloves are essential for daily operations. Depending on the industry, they may also use material handling equipment like dollies or forklifts for moving larger components.
Speed Belt Sander Skills & Qualifications
A Speed Belt Sander operates specialized machinery to smooth and finish surfaces, primarily in manufacturing, woodworking, or metalworking industries. This role focuses on precision and efficiency in preparing materials for subsequent processes like painting, coating, or assembly. The qualification landscape for a Speed Belt Sander emphasizes practical experience and demonstrated competency over formal academic degrees.
Requirements for a Speed Belt Sander vary significantly by industry and company size. In large-scale manufacturing, employers often prefer candidates with formal vocational training or prior experience with industrial machinery. Smaller workshops might prioritize adaptability and a willingness to learn on the job. Geographic location also plays a role; regions with strong manufacturing sectors may have more formalized training programs and a higher demand for certified operators.
Formal education, such as a high school diploma or GED, provides a foundational understanding but is rarely the primary hiring criterion. Practical experience with various materials and sanding techniques holds greater weight. Certifications in machine operation, safety protocols, or specific material handling can significantly enhance a candidate's profile, demonstrating a commitment to safety and professional standards. The skill landscape for a Speed Belt Sander is stable, but a growing emphasis on precision and automated processes means operators benefit from understanding basic machinery maintenance and quality control procedures.
Education Requirements
Technical Skills
- Operation of industrial belt sanding machines (e.g., wide-belt sanders, edge sanders)
- Selection and replacement of abrasive belts (grit sizes, types)
- Understanding of material properties (wood, metal, composites) and their sanding requirements
- Measurement tools proficiency (calipers, micrometers, rulers) for verifying dimensions
- Surface quality inspection and defect identification
- Basic machine maintenance and cleaning (e.g., dust collection, lubrication)
- Adherence to quality control standards and specifications
- Dust collection system operation and maintenance
- Safe handling of materials and finished products
- Reading and interpreting work orders and technical drawings
Soft Skills
- Attention to Detail: Essential for achieving smooth, consistent finishes and identifying surface imperfections.
- Manual Dexterity: Crucial for handling materials and operating the sander with precision and control.
- Problem-Solving: Important for troubleshooting minor machine issues or adjusting techniques for different materials.
- Safety Consciousness: Paramount for adhering to strict safety protocols and operating heavy machinery responsibly.
- Work Ethic: Necessary for maintaining productivity and meeting production quotas in a repetitive task environment.
- Adaptability: Valuable for adjusting to different material types, project specifications, and machine settings.
How to Become a Speed Belt Sander
Entering the field as a Speed Belt Sander operator involves hands-on skill development and a clear understanding of safety protocols. While traditional apprenticeships are less common for this specific role, vocational training and on-the-job learning are primary pathways. Expect a relatively short timeline for entry, often within a few months, for those dedicated to practical skill acquisition.
Many entry-level roles for Speed Belt Sanders exist in manufacturing, woodworking, and metal fabrication shops. Geographic location plays a role; areas with strong industrial bases will have more opportunities. Smaller shops might offer faster entry and more direct mentorship, while larger corporations may have more structured training programs.
A common misconception is that this role requires extensive prior experience. Many employers are willing to train new hires who demonstrate mechanical aptitude, attention to detail, and a strong work ethic. Focus on showcasing your willingness to learn and your commitment to safety rather than solely relying on formal certifications.
Understand the fundamentals of abrasive tools and materials by researching different types of sandpaper, grits, and their applications on various surfaces. This foundational knowledge helps you speak intelligently about the work and quickly adapt to specific job requirements.
Develop practical skills through hands-on experience by practicing with a speed belt sander on scrap materials. Focus on achieving consistent finishes, managing material removal rates, and maintaining proper safety distances. Seek out local workshops or community colleges that might offer access to equipment or basic woodworking/metalworking classes.
Prioritize safety training and obtain relevant certifications, such as OSHA 10-hour or specific machinery operation certificates if available. Employers highly value candidates who demonstrate a commitment to workplace safety and have a basic understanding of industrial regulations.
Build a portfolio of small projects or finished samples demonstrating your sanding capabilities on different materials like wood, metal, or plastics. Include before-and-after photos or even short video clips to showcase your precision and the quality of your work.
Network with professionals in manufacturing, woodworking, or fabrication shops by attending local industry events or visiting suppliers. Inquire about entry-level positions, shadow opportunities, or even part-time help. Personal connections often open doors to unadvertised roles.
Prepare a resume that highlights your practical skills, safety training, and any hands-on experience, even if it's from personal projects. During interviews, emphasize your attention to detail, mechanical aptitude, and eagerness to learn and contribute to a production environment.
Apply for entry-level operator or production assistant roles in manufacturing, furniture making, or metal fabrication companies. Many companies offer on-the-job training for specific machinery, so focus on roles that value a strong work ethic and a willingness to master new equipment.
Step 1
Understand the fundamentals of abrasive tools and materials by researching different types of sandpaper, grits, and their applications on various surfaces. This foundational knowledge helps you speak intelligently about the work and quickly adapt to specific job requirements.
Step 2
Develop practical skills through hands-on experience by practicing with a speed belt sander on scrap materials. Focus on achieving consistent finishes, managing material removal rates, and maintaining proper safety distances. Seek out local workshops or community colleges that might offer access to equipment or basic woodworking/metalworking classes.
Step 3
Prioritize safety training and obtain relevant certifications, such as OSHA 10-hour or specific machinery operation certificates if available. Employers highly value candidates who demonstrate a commitment to workplace safety and have a basic understanding of industrial regulations.
Step 4
Build a portfolio of small projects or finished samples demonstrating your sanding capabilities on different materials like wood, metal, or plastics. Include before-and-after photos or even short video clips to showcase your precision and the quality of your work.
Step 5
Network with professionals in manufacturing, woodworking, or fabrication shops by attending local industry events or visiting suppliers. Inquire about entry-level positions, shadow opportunities, or even part-time help. Personal connections often open doors to unadvertised roles.
Step 6
Prepare a resume that highlights your practical skills, safety training, and any hands-on experience, even if it's from personal projects. During interviews, emphasize your attention to detail, mechanical aptitude, and eagerness to learn and contribute to a production environment.
Step 7
Apply for entry-level operator or production assistant roles in manufacturing, furniture making, or metal fabrication companies. Many companies offer on-the-job training for specific machinery, so focus on roles that value a strong work ethic and a willingness to master new equipment.
Education & Training Needed to Become a Speed Belt Sander
The role of a Speed Belt Sander primarily involves operating industrial sanding machines to finish surfaces, often in manufacturing, woodworking, or metalworking. Formal university degrees are generally not required for this role. Instead, vocational training, apprenticeships, and on-the-job training are the most common and effective pathways.
Vocational programs or technical schools offer specialized courses in machine operation, safety protocols, and material handling, typically costing between $3,000 and $15,000 for programs lasting 6 to 18 months. These programs provide a structured learning environment, often leading to certifications that can enhance job prospects. Apprenticeships, often lasting 1-3 years, provide hands-on experience under skilled professionals and may offer paid training, making them a cost-effective option. Employer acceptance of these credentials is high, as practical skills are paramount.
Self-study through online tutorials or manufacturer-specific training modules can supplement learning, though this rarely replaces formal training or direct experience. Continuous learning in this field primarily involves staying updated on new machinery, materials, and safety standards through employer-provided training or industry workshops. The emphasis for a Speed Belt Sander is overwhelmingly on practical proficiency and safety, making hands-on experience and vocational certifications more valuable than academic degrees. Educational needs can vary slightly based on the specific industry (e.g., aerospace vs. furniture), but foundational machine operation and safety remain critical.
Speed Belt Sander Salary & Outlook
Compensation for a Speed Belt Sander varies significantly based on several factors beyond just the base hourly wage. Geographic location plays a crucial role, with higher wages typically found in areas with a greater concentration of manufacturing or woodworking industries, often reflecting the local cost of living and specific labor demand. For instance, salaries in industrial hubs may be higher than in rural areas.
Experience levels, specialized skills, and the complexity of the materials or products handled also drive salary variations. Speed Belt Sanders who can operate advanced machinery, work with delicate finishes, or handle precision tasks often command higher compensation. Performance bonuses, overtime pay, and benefits like health insurance, retirement contributions, and paid time off often form a significant part of the total compensation package, especially in larger manufacturing facilities.
Industry-specific trends, such as growth in custom furniture production or aerospace component manufacturing, can influence earning potential. Companies with high-volume production or those requiring intricate finishing skills may offer premium pay. Salary negotiation leverage increases with proven efficiency, reliability, and the ability to minimize material waste. While most salary figures presented are in USD, international markets will show different compensation structures based on local economic conditions and labor laws.
Salary by Experience Level
Level | US Median | US Average |
---|---|---|
Speed Belt Sander | $36k USD | $38k USD |
Senior Speed Belt Sander | $43k USD | $45k USD |
Lead Speed Belt Sander | $50k USD | $52k USD |
Speed Belt Sander Supervisor | $58k USD | $60k USD |
Market Commentary
The job market for Speed Belt Sanders is stable, primarily driven by the consistent demand for finished products in manufacturing, woodworking, and construction sectors. Automation and robotic sanding technologies are emerging, but the need for skilled human operators remains crucial for tasks requiring precision, quality control, and adaptability to varied materials and designs. This human element ensures continued relevance for the role.
Growth in custom fabrication, artisan furniture, and specialized industrial components contributes to ongoing demand. However, the overall growth rate for this specific role is modest, projected at around 2-3% over the next decade, in line with general manufacturing employment trends. Supply and demand are relatively balanced, with a steady stream of new entrants replacing retirees. Employers often seek candidates with a strong work ethic, attention to detail, and a commitment to safety.
Future-proofing in this role involves embracing new technologies, such as learning to program or maintain automated sanding equipment, and developing expertise in advanced finishing techniques. The profession is generally recession-resistant as essential manufacturing and repair work continues even in economic downturns. Geographic hotspots for Speed Belt Sanders include states with robust manufacturing bases, such as Michigan, Ohio, and North Carolina. Remote work is not applicable to this hands-on role.
Speed Belt Sander Career Path
Career progression for a Speed Belt Sander involves mastering the operation and maintenance of specialized machinery used for finishing surfaces. Advancement typically follows a clear path from operational proficiency to leadership and supervisory roles. Individuals can pursue an individual contributor (IC) track, focusing on deep technical expertise and efficiency, or a management track, overseeing teams and production.
Factors influencing advancement speed include demonstrated precision, adherence to safety protocols, and continuous improvement in efficiency. Specialization might involve working with specific materials or types of products, enhancing an individual's value. Company size and industry also play a role; larger manufacturing operations may offer more structured advancement opportunities compared to smaller, specialized shops.
Lateral movement often involves transitioning to related finishing roles or machinery operation within the same facility. Networking within the production environment, mentoring junior operators, and maintaining an impeccable safety record are crucial for recognition and progression. Certifications in specific machinery operation or safety standards can also mark significant milestones, enhancing a professional's standing and opening doors to higher roles.
Speed Belt Sander
0-2 yearsOperates speed belt sanders for finishing various materials according to specifications. Performs routine machine adjustments and material handling. Works under direct supervision, focusing on individual output and quality control for assigned tasks. Ensures work area cleanliness and organization.
Key Focus Areas
Develop foundational skills in machine setup, operation, and troubleshooting. Focus on achieving consistent surface finishes and understanding different abrasive types. Prioritize adherence to all safety regulations and standard operating procedures. Build proficiency in basic machine maintenance and cleaning.
Senior Speed Belt Sander
2-5 yearsOperates speed belt sanders with high precision on complex or high-value components. Independently sets up and calibrates machinery for diverse production runs. Troubleshoots minor equipment issues and trains new operators. Contributes to process improvement initiatives, often with minimal oversight.
Key Focus Areas
Master advanced sanding techniques for complex geometries and delicate materials. Develop expertise in identifying and resolving common machine malfunctions and quality issues. Begin mentoring new operators on best practices and safety. Focus on optimizing workflow and reducing material waste.
Lead Speed Belt Sander
5-8 yearsActs as the primary technical expert for speed belt sanding operations, guiding other operators. Oversees daily production schedules and ensures quality standards are consistently met. Provides on-the-job training and performs advanced troubleshooting and minor repairs. Leads continuous improvement projects to enhance efficiency and safety.
Key Focus Areas
Cultivate strong leadership and problem-solving skills for production challenges. Develop expertise in advanced machine diagnostics and preventative maintenance scheduling. Focus on optimizing overall line efficiency, material flow, and quality assurance processes. Participate in cross-functional team meetings and production planning.
Speed Belt Sander Supervisor
8+ years total experienceManages a team of Speed Belt Sanders, overseeing their performance, training, and scheduling. Ensures the efficient operation of the sanding department, meeting production targets and quality benchmarks. Implements and enforces safety protocols and company policies. Reports directly to production management, contributing to broader operational strategies.
Key Focus Areas
Develop comprehensive team management and operational planning skills. Focus on resource allocation, performance evaluation, and conflict resolution within the team. Gain proficiency in production reporting, budget management, and safety compliance. Engage in strategic planning for departmental goals and equipment upgrades.
Speed Belt Sander
0-2 yearsOperates speed belt sanders for finishing various materials according to specifications. Performs routine machine adjustments and material handling. Works under direct supervision, focusing on individual output and quality control for assigned tasks. Ensures work area cleanliness and organization.
Key Focus Areas
Develop foundational skills in machine setup, operation, and troubleshooting. Focus on achieving consistent surface finishes and understanding different abrasive types. Prioritize adherence to all safety regulations and standard operating procedures. Build proficiency in basic machine maintenance and cleaning.
Senior Speed Belt Sander
2-5 yearsOperates speed belt sanders with high precision on complex or high-value components. Independently sets up and calibrates machinery for diverse production runs. Troubleshoots minor equipment issues and trains new operators. Contributes to process improvement initiatives, often with minimal oversight.
Key Focus Areas
Master advanced sanding techniques for complex geometries and delicate materials. Develop expertise in identifying and resolving common machine malfunctions and quality issues. Begin mentoring new operators on best practices and safety. Focus on optimizing workflow and reducing material waste.
Lead Speed Belt Sander
5-8 yearsActs as the primary technical expert for speed belt sanding operations, guiding other operators. Oversees daily production schedules and ensures quality standards are consistently met. Provides on-the-job training and performs advanced troubleshooting and minor repairs. Leads continuous improvement projects to enhance efficiency and safety.
Key Focus Areas
Cultivate strong leadership and problem-solving skills for production challenges. Develop expertise in advanced machine diagnostics and preventative maintenance scheduling. Focus on optimizing overall line efficiency, material flow, and quality assurance processes. Participate in cross-functional team meetings and production planning.
Speed Belt Sander Supervisor
8+ years total experienceManages a team of Speed Belt Sanders, overseeing their performance, training, and scheduling. Ensures the efficient operation of the sanding department, meeting production targets and quality benchmarks. Implements and enforces safety protocols and company policies. Reports directly to production management, contributing to broader operational strategies.
Key Focus Areas
Develop comprehensive team management and operational planning skills. Focus on resource allocation, performance evaluation, and conflict resolution within the team. Gain proficiency in production reporting, budget management, and safety compliance. Engage in strategic planning for departmental goals and equipment upgrades.
Job Application Toolkit
Ace your application with our purpose-built resources:
Speed Belt Sander Cover Letter Examples
Personalizable templates that showcase your impact.
View examplesSpeed Belt Sander Job Description Template
Ready-to-use JD for recruiters and hiring teams.
View examplesGlobal Speed Belt Sander Opportunities
The Speed Belt Sander role involves precision finishing and material removal across various industries globally. Demand remains steady in manufacturing, automotive, and woodworking sectors worldwide. Regulatory differences impact machinery safety standards and operational procedures, but the core skills are universally transferable. Professionals consider international roles for specialized projects or better industrial infrastructure. No specific international certifications exist; practical experience and adherence to local safety protocols are key.
Global Salaries
Salaries for Speed Belt Sanders vary significantly by region and industry. In North America, particularly the US, annual salaries range from $35,000 to $55,000 USD, reflecting demand in manufacturing hubs. European countries like Germany offer €30,000 to €45,000 (approx. $32,000-$48,000 USD), with strong benefits packages and social security contributions. The cost of living in Western Europe is generally higher, impacting purchasing power.
Asia-Pacific markets, such as Australia, see salaries between AUD 50,000 and AUD 70,000 (approx. $33,000-$46,000 USD), often with lower tax burdens than some European nations. In Southeast Asia, wages are lower, typically $15,000-$25,000 USD, but the cost of living is substantially less. Latin American countries like Mexico might offer $10,000-$20,000 USD, though local purchasing power can be surprisingly strong.
Salary structures also differ; European roles often include more vacation time and universal healthcare, while North American packages might emphasize direct pay. Experience and specialized skills in materials like composites or aerospace alloys significantly increase compensation globally. Tax implications vary; for instance, some Middle Eastern countries offer tax-free income, but the overall compensation might be lower. There are no standardized international pay scales for this manual trade.
Remote Work
International remote work for a Speed Belt Sander is generally not feasible. This role requires hands-on operation of machinery in a physical workshop or factory setting. The nature of the work, involving material finishing and precision sanding, demands direct access to equipment and materials.
Digital nomad opportunities or international remote work policies do not apply to this occupation. Employers do not typically hire Speed Belt Sanders for off-site or home-based work, given the equipment and safety requirements. Therefore, salary expectations are tied to the local labor market where the physical work is performed. International collaboration for this role is limited to on-site teams or specific project-based travel.
Visa & Immigration
Immigration for Speed Belt Sanders typically falls under skilled worker visa categories in countries with manufacturing sectors. Popular destinations include Canada, Australia, and Germany due to industrial demand. Canada's Express Entry system might consider skilled trades, requiring an Educational Credential Assessment for foreign qualifications and often an offer of employment. Australia's skilled migration program also lists various trades, requiring skills assessment and English language proficiency.
Germany's skilled immigration law facilitates entry for certain trades, often requiring vocational qualifications recognized by German authorities. Visa timelines vary from a few months to over a year. Language requirements are common in non-English speaking countries. Pathways to permanent residency exist in many nations after several years of continuous employment and tax contributions. Family visas are usually available for dependents, but specific profession-specific advantages are rare for this role.
2025 Market Reality for Speed Belt Sanders
Understanding current market conditions is crucial for anyone pursuing a career as a speed belt sander. The landscape for this specific trade has transformed significantly from 2023 to 2025, influenced by post-pandemic shifts in manufacturing and the rapid integration of advanced automation.
Broader economic factors, such as supply chain stability and consumer demand for finished goods, directly impact job availability. Market realities also vary by experience level—highly skilled artisans find more niche opportunities—and by geographic region, as some areas retain more traditional manufacturing. This analysis provides an honest assessment of these realities.
Current Challenges
Finding consistent, full-time employment remains a primary hurdle for speed belt sanders. Automation continues to reduce demand in some manufacturing sectors. Additionally, the increasing expectation for multi-skilled workers means pure sanding roles are less common, requiring broader capabilities.
Growth Opportunities
Despite overall declining demand, specialized opportunities for speed belt sanders persist in niche markets. Custom furniture makers, high-end cabinetry shops, and specialized automotive restoration companies still require skilled manual finishing for unique projects where automated systems lack the necessary precision or artistry.
Emerging opportunities exist for sanders who cross-train in related skills, such as advanced machine operation, quality inspection, or even programming simple robotic arms. Professionals who can demonstrate versatility and adapt to new technologies, rather than solely relying on manual sanding, gain a significant competitive advantage.
Underserved markets might include smaller, independent workshops focusing on bespoke items or restoration projects. Focusing on acquiring certifications in specific materials, like exotic woods or unique composites, can also set candidates apart. For strategic career moves, consider roles that blend traditional craftsmanship with modern manufacturing techniques, ensuring long-term relevance in an evolving industrial landscape.
Current Market Trends
The demand for speed belt sanders shows a steady decline in 2025, largely due to automation and evolving manufacturing processes. Many companies now integrate automated sanding systems or expect workers to operate multi-functional machinery, reducing the need for dedicated manual sanders.
Economic conditions influence hiring, particularly in furniture, automotive, and construction industries where manual finishing is still present. Layoffs in these sectors sometimes affect ancillary roles like sanding. However, specialized, high-end custom fabrication, where precision hand-finishing remains critical, offers pockets of demand.
Technology trends, specifically advanced robotics and CNC machining, are significantly impacting this profession. These machines can achieve consistent finishes with greater speed, leading to reduced manual labor requirements. Employer requirements are shifting; applicants with broader skills in assembly, machine operation, or quality control are preferred over those solely skilled in sanding.
Salary trends for dedicated speed belt sanders are stagnant or slightly decreasing, reflecting reduced demand and increased competition from automation. Market saturation is evident at entry levels, as many new manufacturing workers possess basic sanding skills. Geographic variations exist; regions with robust custom woodworking, boat building, or specialized automotive restoration might offer more openings than mass production hubs.
Emerging Specializations
Technological advancements and evolving material science are constantly creating new specialization opportunities for professionals across various sectors, including those operating precision machinery. For a Speed Belt Sander, understanding these shifts is crucial for career advancement beyond 2025. Early positioning in emerging areas allows professionals to become indispensable, often commanding premium compensation and accelerated career growth.
While established sanding techniques remain vital, the future increasingly favors those who adapt to novel materials, automated systems, and specialized finishing requirements. Focusing on emerging specializations, rather than solely on traditional methods, prepares you for next-generation opportunities. These cutting-edge areas typically transition from niche to mainstream within five to seven years, creating a significant number of job openings as industries adopt new processes.
Pursuing emerging specializations involves a balance of risk and reward. It requires investing time in new learning and adapting to unfamiliar challenges. However, the potential for higher demand, less competition, and greater influence within a specialized field often outweighs these initial considerations. Strategic choices now can define a more lucrative and impactful career trajectory.
Precision Micro-Finishing Technician
Automated Sanding Systems Operator
Advanced Composite Material Finisher
Surface Preparation Specialist (for Advanced Coatings)
Restoration and Preservation Finisher
Pros & Cons of Being a Speed Belt Sander
Making an informed career decision requires understanding both the benefits and the challenges of a profession. While some aspects of a job offer significant advantages, others can present genuine difficulties. Career experiences vary greatly based on factors like company culture, the specific industry sector, the materials being worked on, and even an individual's personal preferences and resilience. What one person considers a benefit, another might view as a drawback. These pros and cons can also evolve at different stages of a career, from entry-level to senior positions. This assessment provides an honest, balanced overview to help set realistic expectations for a Speed Belt Sander role.
Pros
The role typically requires a short training period, allowing for quick entry into the workforce and immediate earning potential without extensive prior education or certifications.
Speed Belt Sander positions often offer stable employment within manufacturing or woodworking industries, providing consistent work hours and a predictable income.
Developing proficiency in operating a speed belt sander builds a specialized, hands-on skill that is directly applicable in various production and finishing environments, making workers valuable assets.
There is a tangible sense of accomplishment in seeing raw materials transformed into finished products, providing immediate gratification from your work.
Many manufacturing facilities operate on consistent schedules, which can offer a predictable work-life balance compared to roles with fluctuating demands or on-call requirements.
This role can provide a gateway into the broader manufacturing sector, allowing individuals to gain experience and potentially transition into other production or quality control roles over time.
Some companies offer opportunities for cross-training on other machinery or processes, which can broaden a worker's skillset and increase their versatility within the plant.
Cons
This role often involves repetitive motions and standing for long periods, which can lead to physical strain, fatigue, and potential musculoskeletal issues over time.
Exposure to fine dust particles from sanding materials is a constant concern, requiring diligent use of personal protective equipment and proper ventilation to prevent respiratory problems.
The noise from speed belt sanders can be significant, necessitating consistent ear protection to prevent hearing damage and creating a challenging communication environment.
Working with powerful machinery like speed belt sanders carries inherent safety risks, including the potential for cuts, abrasions, or more serious injuries if proper protocols are not followed.
Career progression options for a dedicated Speed Belt Sander role can be limited, often requiring additional training or a shift into different production or supervisory positions for advancement.
The work environment is typically a factory or workshop setting, which may be hot, cold, or poorly lit depending on the facility and the specific materials being processed.
The demand for this specialized skill can fluctuate with manufacturing cycles and economic conditions, potentially affecting job security compared to more diversified roles.
Frequently Asked Questions
A Speed Belt Sander operates specialized machinery for high-volume, precision sanding. This role involves distinct challenges around maintaining equipment, ensuring consistent finish quality, and managing physical demands. This FAQ addresses common questions about entry, daily tasks, and career progression in this specific manufacturing position.
What are the basic educational or experience requirements to become a Speed Belt Sander?
You typically need a high school diploma or equivalent. Many employers prefer candidates with vocational training in manufacturing or machine operation, but on-the-job training is common. Experience with basic hand tools and a strong mechanical aptitude are highly beneficial for this role.
How long does it take to become proficient as a Speed Belt Sander?
On-the-job training for a Speed Belt Sander usually takes 2-4 weeks to learn the machine's basic operation and safety protocols. Mastering the nuances of different materials, finishes, and troubleshooting can take several months. Full proficiency often requires 6-12 months of consistent work and learning.
What are the typical salary expectations for a Speed Belt Sander role?
Entry-level Speed Belt Sanders can expect to earn between $15 and $20 per hour. With experience, specialized skills, and consistent performance, hourly wages can increase to $20-$28 or more. Overtime opportunities are often available, which can significantly boost overall earnings.
What is the typical work schedule and work-life balance for a Speed Belt Sander?
The work-life balance can vary, but most Speed Belt Sander roles are full-time, often on a fixed shift schedule (e.g., 8-hour or 10-hour shifts). Overtime may be required during peak production periods. The work is physically demanding, requiring standing for long periods and repetitive motions.
Is the Speed Belt Sander role a secure job, or is it at risk from automation?
Job security for Speed Belt Sanders is generally stable, especially in manufacturing sectors with consistent demand for finished products like furniture, automotive parts, or construction materials. As long as there is a need for precision finishing, skilled machine operators remain valuable. Automation may change the nature of the work but often creates a need for operators with advanced skills.
What are the potential career advancement opportunities for a Speed Belt Sander?
Career growth paths include becoming a lead operator, a machine maintenance technician, or a quality control inspector. Some experienced Speed Belt Sanders advance into supervisory roles, managing a team of operators. Further training in lean manufacturing or advanced machinery can also open up new opportunities.
What are the biggest challenges or downsides of working as a Speed Belt Sander?
The main challenges involve managing dust exposure, dealing with repetitive motion, and maintaining precision under high production demands. Operators must also be adept at quickly identifying and resolving machine malfunctions or material defects. Regular machine maintenance is crucial to prevent downtime and ensure quality.
Can a Speed Belt Sander role be performed remotely, or is it always on-site?
Speed Belt Sander roles are almost exclusively on-site due to the nature of operating heavy machinery. Remote work is not an option for this position. The work environment is typically a manufacturing plant or workshop, which can be noisy and require personal protective equipment.
Related Careers
Explore similar roles that might align with your interests and skills:
Drywall Sander
A growing field with similar skill requirements and career progression opportunities.
Explore career guideFloor Sander
A growing field with similar skill requirements and career progression opportunities.
Explore career guideFloor Sanding Machine Operator
A growing field with similar skill requirements and career progression opportunities.
Explore career guideFurniture Sander
A growing field with similar skill requirements and career progression opportunities.
Explore career guideTool Polishing Machine Operator
A growing field with similar skill requirements and career progression opportunities.
Explore career guideAssess your Speed Belt Sander readiness
Understanding where you stand today is the first step toward your career goals. Our Career Coach helps identify skill gaps and create personalized plans.
Skills Gap Analysis
Get a detailed assessment of your current skills versus Speed Belt Sander requirements. Our AI Career Coach identifies specific areas for improvement with personalized recommendations.
See your skills gapCareer Readiness Assessment
Evaluate your overall readiness for Speed Belt Sander roles with our AI Career Coach. Receive personalized recommendations for education, projects, and experience to boost your competitiveness.
Assess your readinessSimple pricing, powerful features
Upgrade to Himalayas Plus and turbocharge your job search.
Himalayas
Himalayas Plus
Himalayas Max
Find your dream job
Sign up now and join over 100,000 remote workers who receive personalized job alerts, curated job matches, and more for free!
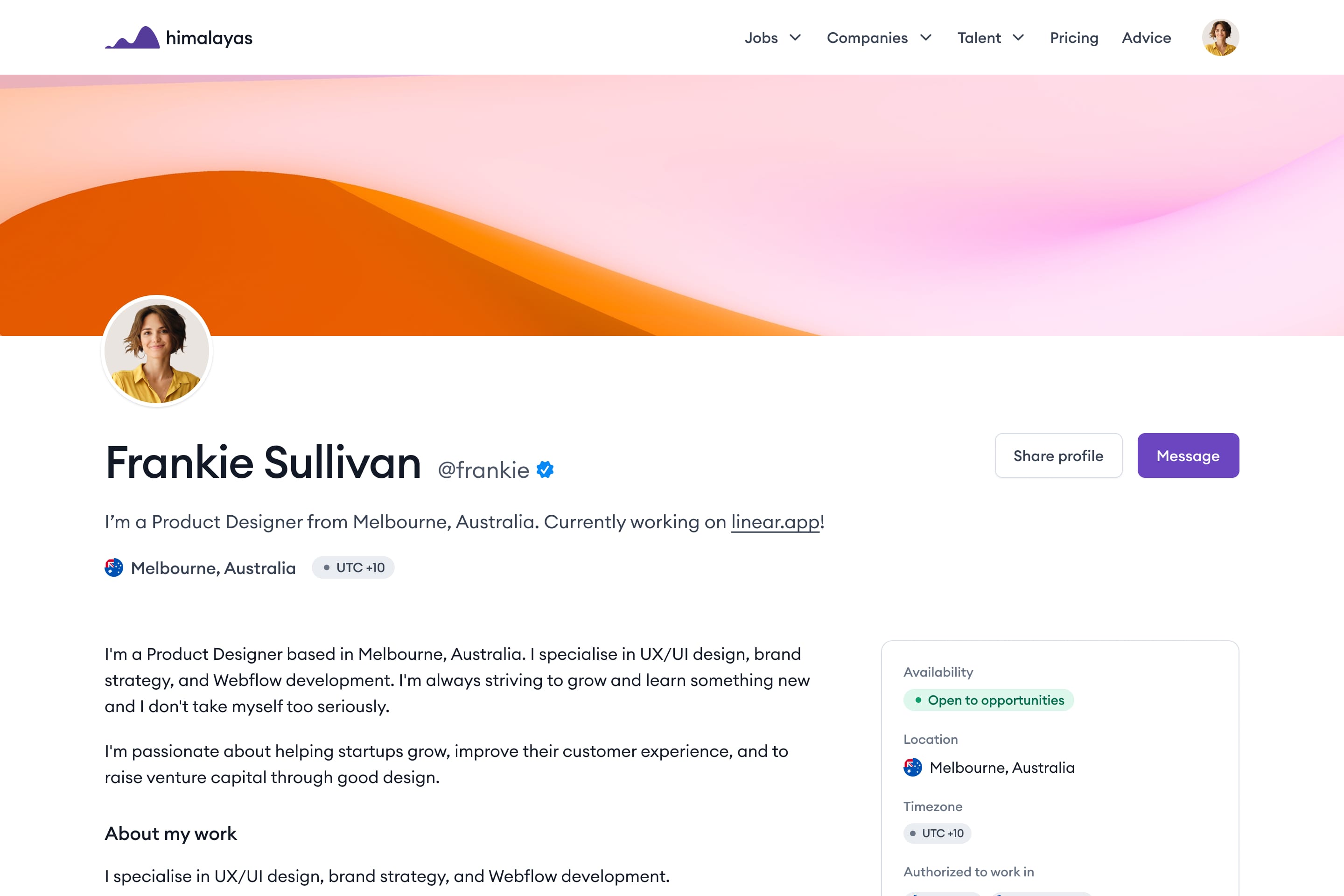