Complete Shop Foreman Career Guide
A Shop Foreman is the linchpin of any successful workshop, overseeing operations, ensuring quality, and guiding skilled tradespeople to complete projects on time and within budget. This role combines hands-on technical expertise with critical leadership skills, making it ideal for those ready to advance their careers beyond the tools.
You will manage workflow, uphold safety standards, and troubleshoot complex issues, driving productivity while mentoring a team of technicians or mechanics.
Key Facts & Statistics
Median Salary
$75,200 USD
(U.S. national median for First-Line Supervisors of Mechanics, Installers, and Repairers, BLS May 2023)
Range: $50k - $100k+ USD (varies by industry, experience, and location)
Growth Outlook
5%
(as fast as average for first-line supervisors of mechanics, installers, and repairers, BLS)
Annual Openings
≈80k
openings annually (combining various foreman/supervisor roles across industries, BLS)
Top Industries
Typical Education
High school diploma or equivalent, plus extensive experience in a relevant trade (e.g., automotive, heavy equipment, industrial maintenance). Many gain certifications and on-the-job training, with some employers preferring associate's degrees.
What is a Shop Foreman?
A Shop Foreman is a supervisory role responsible for the day-to-day operations and productivity of a workshop or production floor. This professional ensures that all work, whether it involves manufacturing, maintenance, or repair, runs smoothly, efficiently, and safely. They act as the primary link between management and the technical staff, translating production goals into actionable tasks for their team.
Unlike a general manager who focuses on broader business strategy, or a lead technician who primarily performs hands-on work, the Shop Foreman maintains a critical balance. They combine technical expertise with leadership skills, providing guidance to staff, troubleshooting complex problems, and maintaining quality control. This role is vital for optimizing workflow and ensuring operational excellence within a production or service environment.
What does a Shop Foreman do?
Key Responsibilities
- Oversee daily shop operations, ensuring all tasks are completed efficiently and safely according to production schedules.
- Assign work to technicians and mechanics, monitoring their progress and providing technical guidance and troubleshooting support.
- Conduct regular inspections of equipment and vehicles to identify maintenance needs, ensuring all repairs meet quality standards.
- Manage inventory of parts and supplies, placing orders as needed to prevent delays and maintain optimal stock levels.
- Enforce safety protocols and maintain a clean, organized work environment, conducting regular safety briefings and training.
- Train new employees on shop procedures, equipment operation, and safety standards, fostering a skilled and compliant workforce.
- Communicate with management about production status, equipment issues, and staffing needs, contributing to strategic planning.
Work Environment
A Shop Foreman typically works in a dynamic and often noisy industrial environment, such as a garage, manufacturing plant, or a heavy equipment repair facility. The role involves a mix of hands-on work, oversight, and administrative duties. Foremen spend time on the shop floor, interacting directly with technicians and equipment, and also in an office area for planning and paperwork. The work often involves irregular hours, including early mornings, late evenings, or weekends, especially when production deadlines are tight or urgent repairs are needed. Collaboration is constant, as the foreman acts as a crucial link between management and the technical team.
Tools & Technologies
A Shop Foreman regularly uses a variety of hand and power tools, including wrenches, drills, diagnostic equipment, and specialized machinery specific to the industry, such as lifts or welding apparatus. They also utilize shop management software for scheduling, tracking work orders, and managing inventory. Communication tools like two-way radios or mobile devices are essential for coordinating teams. Proficiency with basic computer applications for reporting and administrative tasks is also crucial. The specific tools vary greatly depending on whether the shop focuses on automotive, manufacturing, or heavy equipment.
Shop Foreman Skills & Qualifications
A Shop Foreman's qualification landscape emphasizes practical experience and proven leadership over formal academic credentials. Employers prioritize hands-on mechanical expertise, diagnostic proficiency, and a strong track record of managing teams and workflows efficiently. This role requires a deep understanding of maintenance operations and the ability to troubleshoot complex issues under pressure.
Requirements for a Shop Foreman vary significantly by industry, company size, and the specific type of equipment or vehicles involved. In heavy equipment or commercial trucking, extensive field experience is crucial, often valued more than a bachelor's degree. Smaller shops might seek a versatile individual with broad mechanical knowledge, while larger operations, particularly those with a focus on precision manufacturing or advanced diagnostics, may prefer candidates with specialized certifications or associate degrees in automotive or industrial technology. Geographic location also plays a role; some regions have stronger apprenticeship traditions, while others might lean more on formal vocational training.
Formal education, such as an associate's degree in automotive technology or diesel mechanics, provides a strong foundation but typically does not substitute for years of practical experience. Certifications from organizations like ASE (Automotive Service Excellence) for vehicle-focused roles, or specific manufacturer certifications, add significant value, demonstrating specialized knowledge and commitment to professional development. Alternative pathways into this field often involve starting as a technician, gaining extensive on-the-job experience, and then progressing through leadership training. The skill landscape is evolving, with increasing demands for diagnostic software proficiency, telematics understanding, and familiarity with hybrid or electric vehicle systems, shifting the balance towards continuous learning in technology.
Education Requirements
Technical Skills
- Advanced Diagnostic Software Operation (e.g., OEM diagnostic tools, aftermarket scan tools)
- Hydraulic and Pneumatic Systems Troubleshooting and Repair
- Electrical System Diagnostics and Wiring Repair (including multiplexing and CAN bus systems)
- Preventive Maintenance Program Development and Execution
- Welding and Fabrication (MIG, TIG, Stick) for repair and modification
- Engine Overhaul and Repair (Gasoline, Diesel, Hybrid powertrains)
- Brake System Repair and Maintenance (Air Brakes, Hydraulic Brakes)
- Transmission and Drivetrain Repair and Rebuilding (Automatic and Manual)
- Parts Inventory Management and Procurement Systems
- Shop Equipment Maintenance and Calibration (e.g., lifts, tire changers, alignment racks)
- Compliance with DOT Regulations and Safety Standards
- Computerized Maintenance Management System (CMMS) usage
Soft Skills
- Leadership and Team Management: Essential for guiding technicians, delegating tasks, and fostering a productive work environment, ensuring clear direction and accountability.
- Problem-Solving and Decision-Making: Crucial for diagnosing complex mechanical issues, optimizing repair processes, and making rapid, effective decisions to minimize downtime and costs.
- Communication and Interpersonal Skills: Vital for clearly conveying instructions to technicians, providing feedback, interacting with service advisors and customers, and reporting to management.
- Organizational and Planning Skills: Necessary for scheduling maintenance, managing parts inventory, allocating resources efficiently, and ensuring projects are completed on time and within budget.
- Adaptability and Stress Management: Important for handling unexpected breakdowns, managing multiple priorities, and maintaining composure in a fast-paced, demanding shop environment.
- Safety Consciousness: Paramount for enforcing strict safety protocols, identifying potential hazards, and ensuring a safe working environment for all shop personnel.
- Mentorship and Coaching: Key for developing junior technicians, sharing expertise, and improving the overall skill level of the team, contributing to long-term shop efficiency and quality.
- Attention to Detail: Critical for ensuring that all repairs meet quality standards, identifying subtle indicators of mechanical issues, and meticulous record-keeping for maintenance history and compliance.
How to Become a Shop Foreman
Becoming a Shop Foreman involves a blend of technical mastery, leadership aptitude, and extensive practical experience. While some enter this role through traditional apprenticeships and climbing the ranks, others transition from related trades after years of hands-on work. The timeline varies significantly; a dedicated individual with prior mechanical or trade skills might reach this position in 3-5 years, while someone starting from scratch could take 7-10 years, including foundational training.
Entry strategies differ by industry and company size. Larger corporations often seek candidates with formal certifications or associate's degrees in relevant fields, alongside proven supervisory experience. Smaller independent shops, however, may prioritize demonstrated skill, a strong work ethic, and leadership potential, valuing practical experience over formal credentials. Geographic location also plays a role; industrial hubs offer more opportunities, but competition can be higher.
A common misconception is that this role is purely about technical skill; in reality, it heavily involves people management, scheduling, and problem-solving. Building a strong network within your trade, seeking mentorship from experienced foremen, and consistently developing both your technical and soft skills are crucial for advancement. The hiring landscape values individuals who can not only perform complex tasks but also optimize workflows and lead a team effectively.
Step 1
Step 2
Step 3
Step 4
Step 5
Step 6
Step 7
Education & Training Needed to Become a Shop Foreman
A Shop Foreman, often found in manufacturing, automotive, or construction environments, requires a blend of technical mastery and leadership skills. Educational pathways range from vocational training to associate's degrees, with experience playing a crucial role. Formal trade schools or community college programs for specific trades like welding, machining, or automotive technology often form the foundational knowledge base. These programs typically cost $5,000-$20,000 and take 9 months to 2 years to complete, providing hands-on skills and theoretical understanding.
While four-year degrees are less common for a Shop Foreman role, some individuals pursue an Associate's degree in Industrial Technology or a related field, which can cost $10,000-$30,000 over two years. This provides a broader understanding of industrial processes and management principles. Many employers value practical experience and certifications equally, if not more, than formal degrees for this position. Continuous learning in areas like lean manufacturing, safety regulations, and new equipment operation is vital for career progression and effectiveness.
Self-study through online courses or manufacturer-specific training can supplement formal education, often costing hundreds to a few thousand dollars and taking a few weeks to several months. These options are highly regarded for staying current with industry advancements. Employers typically prioritize candidates with demonstrated leadership abilities, problem-solving skills, and a strong safety record, alongside their technical credentials. The most effective educational investment combines a solid technical foundation with ongoing professional development in leadership and operational efficiency.
Shop Foreman Salary & Outlook
Compensation for a Shop Foreman is influenced by a blend of factors beyond just base salary. Geographic location significantly impacts earnings, with higher cost-of-living areas and regions with strong industrial or manufacturing sectors typically offering better pay. For instance, a Shop Foreman in a major metropolitan area will likely earn more than one in a rural setting.
Years of experience, specific technical skills, and the size and complexity of the operation managed also create dramatic salary variations. A Foreman with specialized expertise in complex machinery or a proven track record in lean manufacturing will command higher compensation. Total compensation packages often include performance bonuses, overtime pay, health benefits, retirement contributions, and allowances for professional development or tool purchases. These components can add substantial value beyond the base wage.
Industry-specific trends, such as growth in automotive repair, heavy equipment, or specialized manufacturing, directly affect salary growth. Strong demand for skilled trades and effective leadership drives up earning potential. Shop Foremen with strong leadership abilities, problem-solving skills, and a knack for optimizing workflows possess greater negotiation leverage. Remote work is generally not applicable to this hands-on role, meaning location-based salaries remain the norm. While figures provided are in USD, international market variations exist, reflecting local economic conditions and labor laws.
Salary by Experience Level
Level | US Median | US Average |
---|---|---|
Assistant Shop Foreman | $52k USD | $55k USD |
Shop Foreman | $65k USD | $68k USD |
Senior Shop Foreman | $75k USD | $78k USD |
Shop Manager | $87k USD | $90k USD |
Operations Manager (Shop) | $110k USD | $115k USD |
Market Commentary
The job market for Shop Foremen shows steady demand, driven by the ongoing need for skilled trades and effective operational oversight in various industries. The U.S. Bureau of Labor Statistics projects stable growth for first-line supervisors of mechanics, installers, and repairers, which aligns with the Shop Foreman role. This growth is tied to the maintenance and repair needs across sectors like automotive, heavy machinery, and manufacturing, ensuring a consistent need for experienced leadership on the shop floor.
Emerging opportunities for Shop Foremen include roles in facilities adopting advanced diagnostics, automation, and robotic systems. The ability to integrate new technologies and manage a tech-savvy workforce is becoming increasingly valuable. There is a persistent demand for experienced foremen who can optimize workflows, implement safety protocols, and train junior technicians. This demand often outpaces the supply of highly qualified candidates, particularly those with strong leadership and technical expertise.
Future-proofing this career involves continuous learning in new equipment technologies and management practices, such as lean methodologies. While automation impacts some tasks, the Shop Foreman's role in human oversight, problem-solving, and team management remains crucial and less susceptible to full automation. This profession is generally recession-resistant as maintenance and repair needs persist regardless of economic cycles. Geographic hotspots for this role include industrial hubs, manufacturing centers, and areas with significant transportation infrastructure, which consistently require skilled shop leadership.
Shop Foreman Career Path
Career progression for a Shop Foreman typically involves a blend of technical mastery, leadership development, and operational management. Individuals often begin in a hands-on technical role, gaining deep expertise in the specific trade or industry the shop serves. Advancement means taking on more responsibility for team performance, safety, and operational efficiency, moving from an individual contributor to a management track.
Advancement speed depends on performance, the complexity of the shop's operations, and the company's growth. Specialization in particular equipment or processes can create unique pathways. Larger organizations often have more distinct levels, while smaller shops might see foremen assume broader responsibilities sooner. Lateral moves could involve shifting to roles in quality control, training, or specialized technical consulting within the same industry.
Continuous learning, especially in new technologies, safety regulations, and management techniques, is crucial. Building a strong reputation for reliability, problem-solving, and team leadership significantly aids progression. Networking within industry associations and seeking mentorship from experienced managers also provides valuable insights and opportunities. Many foremen eventually transition into broader operational or even general management roles, leveraging their hands-on experience and leadership skills.
Assistant Shop Foreman
2-4 years total experienceKey Focus Areas
Shop Foreman
4-7 years total experienceKey Focus Areas
Senior Shop Foreman
7-12 years total experienceKey Focus Areas
Shop Manager
10-15 years total experienceKey Focus Areas
Operations Manager (Shop)
15+ years total experienceKey Focus Areas
Assistant Shop Foreman
2-4 years total experienceAssists the Shop Foreman with daily tasks, including organizing workstations, preparing tools, and monitoring basic equipment function. Provides support to technicians, ensuring materials are available. Helps maintain a clean and safe work environment. Decision-making is limited, primarily following direct instructions.
Key Focus Areas
Develop strong technical proficiency in all shop equipment and processes. Learn safety protocols and quality standards rigorously. Understand inventory management basics and how to interpret work orders accurately. Build effective communication with peers and supervisors.
Shop Foreman
4-7 years total experienceDirects daily shop operations, overseeing a team of technicians and ensuring work orders are completed on time and to quality standards. Manages tool and equipment maintenance schedules. Conducts safety briefings and enforces compliance with regulations. Makes decisions on task prioritization and minor operational adjustments.
Key Focus Areas
Master scheduling and resource allocation for daily operations. Develop leadership skills, including delegating tasks, providing constructive feedback, and resolving minor team conflicts. Enhance problem-solving abilities for equipment malfunctions and workflow bottlenecks. Focus on optimizing shop efficiency and maintaining high safety standards.
Senior Shop Foreman
7-12 years total experienceLeads multiple teams or complex projects within the shop, acting as a technical expert and primary problem-solver for significant operational challenges. Responsible for training junior foremen and developing team members. Contributes to equipment procurement decisions and process improvement initiatives. Has significant autonomy in managing workflow and resource deployment.
Key Focus Areas
Refine advanced leadership and team management skills, including conflict resolution, performance evaluations, and mentorship. Develop strategic thinking for long-term shop improvements and capacity planning. Acquire deeper understanding of budgeting, cost control, and supply chain management relevant to shop operations. Pursue certifications in lean manufacturing or advanced safety practices.
Shop Manager
10-15 years total experienceOversees the entire shop's operations, encompassing all personnel, equipment, and processes. Responsible for meeting production targets, managing the shop budget, and ensuring profitability. Implements strategic initiatives to improve efficiency, safety, and quality. Manages relationships with suppliers and internal departments. Makes critical decisions impacting the shop's long-term performance.
Key Focus Areas
Develop comprehensive business acumen, including financial management, P&L responsibility, and strategic planning. Cultivate strong stakeholder management skills, interacting with sales, engineering, and HR. Focus on talent acquisition, retention, and performance management for the entire shop workforce. Understand market trends affecting shop services and capabilities.
Operations Manager (Shop)
15+ years total experienceManages the overall operational efficiency and strategic direction of multiple shops or a significant division within the company's production or service operations. Responsible for setting high-level operational goals, allocating major resources, and ensuring compliance across all facilities. Drives continuous improvement initiatives and technological adoption at an organizational level. Makes decisions that impact the company's overall operational footprint and profitability.
Key Focus Areas
Master high-level strategic planning, organizational development, and change management. Develop expertise in cross-departmental collaboration and enterprise-wide process optimization. Focus on integrating shop operations with broader company objectives and supply chain strategies. Cultivate executive presence and advanced negotiation skills.
Job Application Toolkit
Ace your application with our purpose-built resources:
Global Shop Foreman Opportunities
A Shop Foreman's role translates globally, focusing on operational oversight, team leadership, and quality control in manufacturing or repair environments. Global demand for skilled foremen remains steady, particularly in industrializing nations and sectors like automotive, heavy machinery, and construction. Regulatory differences impact safety standards and labor laws, while cultural nuances affect team management styles. Professionals consider international roles for career advancement, exposure to new technologies, and higher earning potential. No specific international certifications exist, but strong technical skills and leadership experience are universally valued.
Global Salaries
Shop Foreman salaries vary significantly by region and industry. In North America, a foreman can expect to earn between $60,000 and $90,000 USD annually in the United States, or CAD 65,000-95,000 in Canada. These figures reflect a high cost of living in major industrial hubs. Benefits packages often include health insurance, retirement plans, and paid vacation.
European salaries range from €40,000 to €70,000 EUR in countries like Germany and the Netherlands, where manufacturing is strong. In the UK, this is roughly £35,000-£60,000 GBP. Southern European nations like Spain might offer €28,000-€45,000 EUR. European compensation frequently includes generous vacation time and comprehensive social security benefits, impacting take-home pay differently than in North America.
In Asia-Pacific, salaries for a Shop Foreman in Australia might be AUD 70,000-100,000, while in Japan, JPY 4.5-7.5 million (approx. $30,000-$50,000 USD) is typical. China's industrial centers offer RMB 150,000-300,000 ($20,000-$40,000 USD), often supplemented by housing allowances. Purchasing power parity must be considered; a lower nominal salary in some Asian countries can still provide a good standard of living due to lower costs.
Latin American countries typically show lower nominal salaries, with a Shop Foreman in Mexico earning MXN 250,000-450,000 ($15,000-$27,000 USD) annually. Brazil's range is BRL 60,000-120,000 ($12,000-$24,000 USD). These regions often have fewer non-wage benefits but potentially lower tax burdens. Experience and specific industry sector significantly influence international compensation, with specialized manufacturing or heavy industries often offering higher pay.
Remote Work
The Shop Foreman role requires on-site presence, making full international remote work generally impractical. This position involves direct supervision of production lines, equipment, and personnel. Therefore, digital nomad opportunities are not applicable for this hands-on profession. Companies do not typically hire Shop Foremen for remote, international work.
However, some administrative or planning aspects might be managed remotely within the same country or region. This typically involves reporting, scheduling, or inventory management, but the core supervisory duties remain facility-based. Any international remote work for a Shop Foreman would be highly unusual and limited to specific, short-term project management tasks, not the day-to-day operational role. Equipment and internet requirements are not a factor for the primary duties.
Visa & Immigration
Skilled worker visas are the most common pathway for a Shop Foreman seeking international employment. Countries like Canada, Australia, Germany, and the UK have specific programs for skilled trades. Requirements generally include a job offer, relevant experience, and sometimes trade certifications or diplomas. Educational credential recognition is crucial; some countries require an assessment to validate foreign qualifications.
Visa application timelines vary, from a few months in some European countries to over a year for certain Canadian or Australian programs. English language proficiency tests, like IELTS, are often mandatory for English-speaking nations. German language skills are beneficial for opportunities in Germany. Pathways to permanent residency exist in several countries after a period of skilled employment.
Intra-company transfers can facilitate moves for foremen within multinational corporations. Family visas are usually available for spouses and dependent children. While no specific fast-track programs exist solely for Shop Foremen, their practical skills are in demand in many industrial economies. Understanding each country's specific labor market needs and immigration points systems is vital for a successful application.
2025 Market Reality for Shop Foremans
Understanding current market realities is crucial for any Shop Foreman aiming for career advancement or a new role. The landscape for foremen has evolved significantly since 2023, shaped by post-pandemic shifts and the accelerating integration of technology.
Broader economic factors, such as supply chain stability and consumer spending, directly influence shop activity and, consequently, demand for leadership roles like the foreman. Market realities also vary by a foreman's experience level, the specific industry (e.g., automotive vs. heavy machinery), geographic location, and the size of the operation. This analysis provides an honest assessment of current hiring conditions and strategic insights.
Current Challenges
Competition for experienced Shop Foremen remains high, especially for those with strong technical and leadership skills. Many shops seek candidates proficient with modern diagnostic tools and management software, creating a skill gap for some. Economic uncertainties can lead to reduced shop activity, affecting hiring stability. Finding roles with genuine growth potential beyond the foreman position also presents a challenge.
Growth Opportunities
Despite challenges, strong opportunities exist for Shop Foremen who adapt to modern demands. Shops actively seek foremen skilled in lean management principles and predictive maintenance. Specialized areas like electric vehicle service, advanced manufacturing automation, and heavy equipment diagnostics offer significant growth for foremen with relevant expertise.
Foremen who can lead digital transformation within a shop, including implementing new software and training technicians on AI-powered tools, possess a distinct competitive advantage. Underserved markets, particularly in rapidly developing industrial zones or rural areas with growing agricultural or construction needs, often present better opportunities with less competition. Strategic career moves involve acquiring certifications in emerging technologies or pursuing management training.
Current Market Trends
The demand for skilled Shop Foremen holds steady in 2025 across various sectors like automotive, heavy equipment, and manufacturing. Shops increasingly prioritize foremen who can manage teams, optimize workflow, and implement new technologies effectively. AI integration impacts foremen by providing advanced diagnostic tools and predictive maintenance software, requiring foremen to lead adoption and training.
Economic conditions show a mixed impact; while some sectors experience growth, others face supply chain disruptions or fluctuating consumer demand. This translates to stable but not explosive hiring. Employers now seek foremen with strong digital literacy, not just mechanical expertise. Salary trends show modest increases for highly qualified candidates, but market saturation exists at the entry-level foreman positions.
Geographic variations in market strength are notable. Urban and industrial hubs typically offer more opportunities and better compensation. Remote work normalization has little impact on this hands-on role. Seasonal hiring patterns are less pronounced for foremen compared to technician roles, though year-end or early-year hiring can see slight upticks as shops plan budgets.
Emerging Specializations
The role of a Shop Foreman is evolving rapidly, driven by significant advancements in automation, data analytics, and sustainable manufacturing practices. These technological shifts are creating new specialization opportunities that can significantly enhance career trajectories and earning potential. Early positioning in these emerging areas by 2025 and beyond is crucial for professionals seeking to lead and innovate within their field, moving beyond traditional operational oversight.
Specializing in cutting-edge areas often commands premium compensation and offers accelerated career growth, as demand for these niche skills outpaces supply. While established specializations remain vital for day-to-day operations, future-oriented foremen will find greater strategic value in developing expertise where technology intersects with traditional shop floor management. The timeline for these emerging areas to become mainstream and generate a significant volume of job opportunities is relatively short, often within three to five years, making proactive skill acquisition essential.
Pursuing emerging specializations involves a balance of risk and reward. The risk lies in the initial investment of time and resources into fields that are still maturing. However, the reward includes becoming an indispensable leader, shaping the future of manufacturing, and securing a competitive advantage in a transforming industry. Understanding these dynamics helps professionals make informed choices about their career development.
Automated Systems & Robotics Integration Foreman
As manufacturing processes become increasingly automated, the Shop Foreman’s role shifts towards overseeing and optimizing robotic systems. This specialization involves managing robotic work cells, programming automated tasks, and troubleshooting complex integration issues between human operators and machinery. It ensures seamless, efficient, and safe operation within advanced manufacturing environments.
Data-Driven Operations & Predictive Maintenance Foreman
The proliferation of IoT devices and sensors on the shop floor generates vast amounts of operational data. A Shop Foreman specializing in data-driven operations uses this information to predict equipment failures, optimize production schedules, and identify inefficiencies. This involves interpreting real-time data from machinery to make informed decisions that enhance productivity and reduce downtime.
Sustainable Manufacturing & Green Operations Foreman
With increasing emphasis on environmental responsibility, foremen can specialize in implementing and monitoring sustainable manufacturing practices. This involves optimizing energy consumption, managing waste reduction programs, overseeing the adoption of eco-friendly materials, and ensuring compliance with environmental regulations. This role drives efficiency while reducing the ecological footprint of manufacturing operations.
Additive Manufacturing & 3D Printing Foreman
Additive manufacturing, particularly 3D printing, is transforming prototyping and production. A Shop Foreman specializing in this area oversees the operation, maintenance, and quality control of 3D printing equipment. This includes managing material inventories, optimizing print parameters, and integrating additive processes into existing production workflows, opening new possibilities for custom fabrication and rapid prototyping.
Operational Technology (OT) Cybersecurity Foreman
Cybersecurity is no longer just an IT concern; it extends to the operational technology (OT) of the shop floor. A Shop Foreman specializing in OT cybersecurity focuses on protecting industrial control systems, networked machinery, and production data from cyber threats. This involves implementing security protocols, monitoring for anomalies, and training staff on secure operational practices to prevent disruptions and data breaches.
Pros & Cons of Being a Shop Foreman
Understanding both the advantages and challenges of a career as a Shop Foreman is crucial for making an informed decision. Career experiences can vary significantly based on the specific industry, the size and culture of the company, and the type of products or services being managed. What might be a pro for one individual, such as hands-on problem-solving, could be a con for another who prefers a more strategic, less physical role. Furthermore, the nature of pros and cons can shift at different career stages; for example, the initial learning curve might be steep, but it leads to greater autonomy later on. This assessment provides a realistic outlook to help set appropriate expectations for this demanding but rewarding leadership position.
Pros
- A Shop Foreman holds a position of significant authority and leadership, directly influencing daily operations, team performance, and production outcomes, which provides a strong sense of responsibility and accomplishment.
- The role offers diverse problem-solving opportunities, from optimizing workflows and improving efficiency to troubleshooting complex mechanical issues and resolving team conflicts, keeping the work intellectually engaging.
- Direct impact on product quality and operational efficiency allows for immediate gratification when improvements are implemented successfully, contributing visibly to the company's success.
- This position typically commands a higher salary than general shop floor positions, reflecting the increased responsibility, specialized skills, and management duties involved.
- A Shop Foreman develops a comprehensive skill set encompassing technical expertise, personnel management, project coordination, and safety compliance, making them highly valuable in manufacturing and industrial sectors.
- The role often involves a blend of hands-on technical work and strategic planning, appealing to individuals who enjoy both practical application and organizational oversight.
- Building strong relationships with a team and mentoring junior staff provides immense personal satisfaction, as you directly contribute to the growth and development of others.
Cons
- High pressure and stress levels are common, as a Shop Foreman must ensure production quotas are met, troubleshoot unexpected issues, and manage personnel conflicts, often under tight deadlines.
- Long and irregular hours are frequently required, especially in busy periods or when equipment breaks down unexpectedly, which can impact work-life balance.
- Dealing with difficult employees or interpersonal conflicts is a regular part of the job, requiring strong mediation skills and often leading to emotionally draining situations.
- The role demands continuous problem-solving for mechanical failures, logistical bottlenecks, and human errors, which can be mentally exhausting and require constant vigilance.
- Exposure to hazardous working conditions, including loud noise, heavy machinery, and potential chemical exposure, is inherent to shop environments, posing safety risks.
- Limited opportunities for upward mobility beyond this role often exist within a single company, as the Shop Foreman position is typically a senior operational management level.
- The position can feel isolating, as you bridge the gap between management and the shop floor, sometimes being seen as 'the boss' by workers and 'the worker' by upper management.
Frequently Asked Questions
A Shop Foreman balances technical expertise with team leadership, facing unique challenges in managing workflow, ensuring quality, and motivating staff. This section addresses crucial questions about transitioning into this supervisory role, from required experience to navigating team dynamics and career progression.
What experience and qualifications do I need to become a Shop Foreman?
Becoming a Shop Foreman typically requires significant hands-on experience in the specific trade, usually 5-10 years. This foundational experience is crucial for understanding the work and gaining the respect of your team. Additionally, employers often look for demonstrated leadership potential, strong problem-solving skills, and a solid understanding of safety protocols and operational efficiency.
How long does it typically take to advance to a Shop Foreman position from an entry-level role?
The transition timeline varies greatly depending on your current experience and the company's structure. If you are already a skilled technician with leadership aspirations, you might move into a foreman role within 2-5 years of focused effort and mentorship. For those starting with less experience, it could take 5-10 years to build the necessary technical mastery and leadership acumen before being considered for such a position.
What are the typical salary expectations and benefits for a Shop Foreman?
Shop Foreman salaries vary by industry, location, and company size, but they generally earn more than skilled technicians due to their added responsibilities. You can expect a salary range from $50,000 to $80,000 annually, with experienced foremen in specialized fields potentially earning more. Benefits packages often include health insurance, retirement plans, and sometimes performance-based bonuses related to shop productivity and safety.
What is the typical work-life balance like for a Shop Foreman, and what are the demands?
The work-life balance for a Shop Foreman can be challenging, as the role often demands long hours, especially during peak seasons or when urgent issues arise. You are responsible for ensuring production targets are met and problems are resolved, which can lead to extended shifts. However, some companies offer more predictable schedules, and effective delegation and strong team management can help mitigate the demands.
What is the job security and market demand like for Shop Foremen?
The job security for a Shop Foreman is generally strong, as these roles are essential for operational efficiency and quality control in most industrial and skilled trade environments. Demand remains consistent because businesses always need experienced leaders to manage their production floors and technical teams. However, job availability can fluctuate with economic cycles and industry-specific growth.
What are the potential career growth opportunities for a Shop Foreman?
Career growth for a Shop Foreman often leads to roles like Production Manager, Operations Manager, or even Plant Manager, especially in larger organizations. You can also specialize further in quality control, safety management, or training and development. Acquiring certifications in project management or lean manufacturing can significantly enhance your upward mobility and open doors to executive-level positions.
What are the biggest challenges unique to being a Shop Foreman, beyond technical skills?
The biggest challenge for a Shop Foreman is balancing technical oversight with effective team leadership and conflict resolution. You must maintain productivity, ensure quality, and manage personnel issues, often under pressure. Developing strong communication skills, learning to delegate effectively, and mastering conflict resolution are crucial for success in this demanding role.
Is remote work a realistic option for a Shop Foreman, or is it primarily an on-site role?
Remote work is generally not feasible for a Shop Foreman, as the role requires a constant physical presence on the shop floor to oversee operations, ensure safety, and directly manage the team. Your responsibilities include hands-on problem-solving, real-time supervision, and direct interaction with equipment and personnel. While some administrative tasks might be done remotely, the core functions are site-dependent.
Related Careers
Explore similar roles that might align with your interests and skills:
Automotive Manager
A growing field with similar skill requirements and career progression opportunities.
Explore career guideAutomotive Service Manager
A growing field with similar skill requirements and career progression opportunities.
Explore career guideBody Shop Manager
A growing field with similar skill requirements and career progression opportunities.
Explore career guideForeman
A growing field with similar skill requirements and career progression opportunities.
Explore career guideShop Manager
A growing field with similar skill requirements and career progression opportunities.
Explore career guideAssess your Shop Foreman readiness
Understanding where you stand today is the first step toward your career goals. Our Career Coach helps identify skill gaps and create personalized plans.
Skills Gap Analysis
Get a detailed assessment of your current skills versus Shop Foreman requirements. Our AI Career Coach identifies specific areas for improvement with personalized recommendations.
See your skills gapCareer Readiness Assessment
Evaluate your overall readiness for Shop Foreman roles with our AI Career Coach. Receive personalized recommendations for education, projects, and experience to boost your competitiveness.
Assess your readinessSimple pricing, powerful features
Upgrade to Himalayas Plus and turbocharge your job search.
Himalayas
Himalayas Plus
Himalayas Max
Find your dream job
Sign up now and join over 100,000 remote workers who receive personalized job alerts, curated job matches, and more for free!
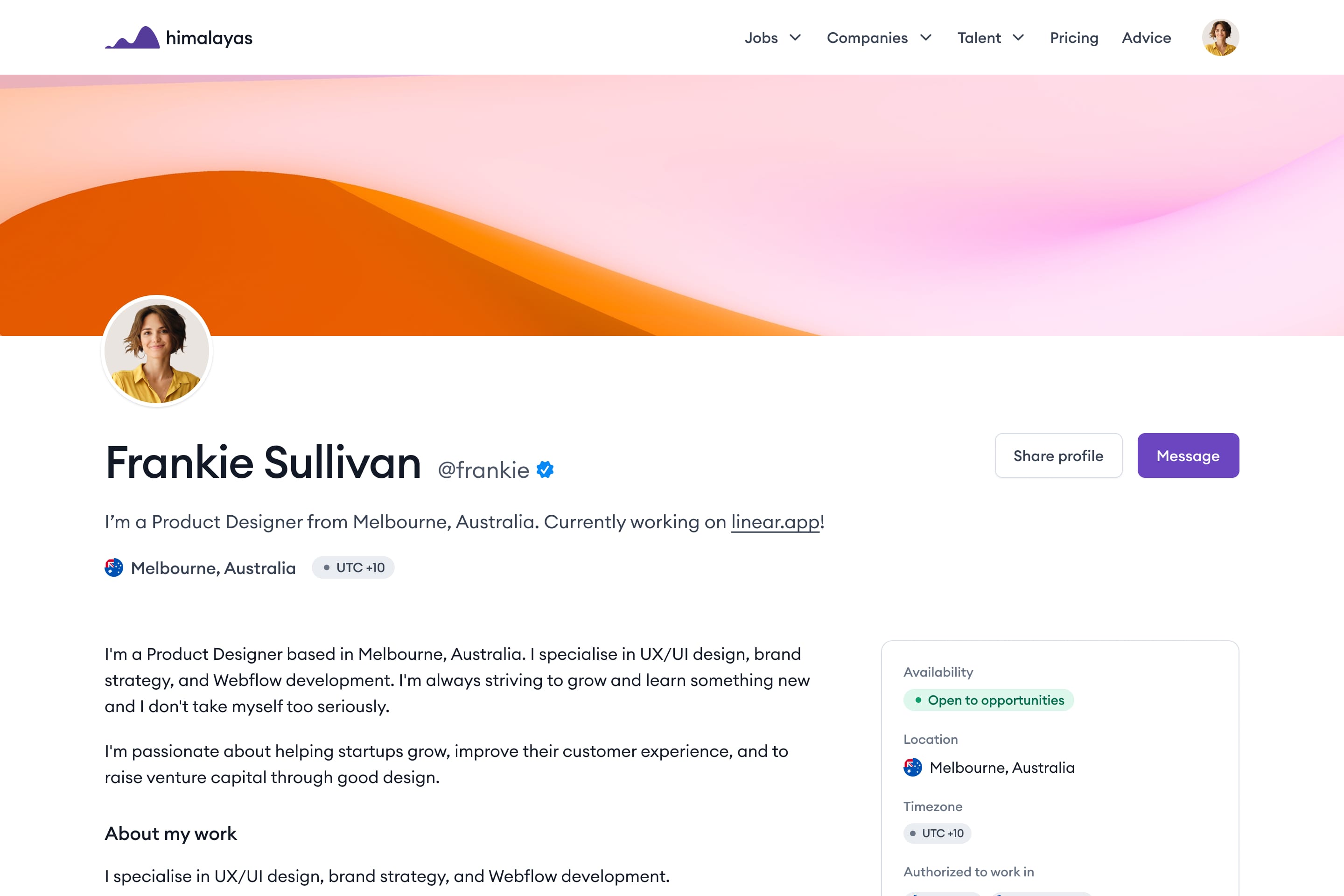