Complete Packer Career Guide
Packers are the unsung heroes of the supply chain, ensuring products are safely and efficiently prepared for shipment, distribution, or storage. This vital role keeps goods moving, from consumer products to industrial components, directly impacting timely delivery and customer satisfaction. It's a hands-on career offering consistent opportunities to contribute to global commerce.
Key Facts & Statistics
Median Salary
$35,660 USD
(U.S. Bureau of Labor Statistics, May 2023)
Range: $27,000 - $49,000+ USD
Growth Outlook
1%
as fast as average (U.S. Bureau of Labor Statistics, 2022-2032)
Annual Openings
≈133,900
openings annually (U.S. Bureau of Labor Statistics, 2022-2032)
Top Industries
Typical Education
High school diploma or equivalent, with on-the-job training
What is a Packer?
A Packer is a crucial logistics professional responsible for preparing goods for shipment or storage. This role involves carefully selecting, arranging, and securing items within appropriate packaging to prevent damage during transit or storage. Packers ensure that products meet quality standards and are correctly labeled for their intended destination, playing a vital part in the supply chain's efficiency and customer satisfaction.
This role differs significantly from a 'Shipper' or 'Receiver.' While a Shipper focuses on coordinating outbound logistics, including paperwork and carrier communication, and a Receiver handles incoming goods verification, a Packer's primary responsibility is the physical act of packaging the product itself. Their expertise lies in protective packaging techniques and efficient assembly, ensuring items are ready for the shipping process.
What does a Packer do?
Key Responsibilities
- Inspect products for defects or damage before packing to ensure quality standards are met.
- Select appropriate packaging materials, such as boxes, bubble wrap, or styrofoam, based on product fragility and size.
- Place products carefully into containers, ensuring proper cushioning and secure placement to prevent movement during transit.
- Seal packages using tape, strapping, or other sealing equipment, verifying that all closures are secure and tamper-proof.
- Affix labels, shipping manifests, and other necessary documentation to packages, ensuring correct destination and tracking information.
- Operate machinery like shrink wrappers, pallet jacks, or automated labeling systems to streamline the packing process.
- Maintain a clean and organized work area, ensuring all packing materials are stocked and waste is properly disposed of.
Work Environment
Packers typically work in warehouses, distribution centers, or manufacturing facilities. The environment can be fast-paced, especially during peak seasons, requiring constant movement and attention to detail. Work often involves standing for long periods and repetitive tasks. Collaboration is usually with a small team of fellow packers and supervisors, focusing on meeting daily quotas. Shifts can vary, including day, evening, or night shifts, and sometimes weekends. The work environment is generally indoors, but temperatures might fluctuate depending on the facility's climate control and the nature of the products being handled.
Tools & Technologies
Packers frequently use a variety of manual and automated tools to perform their tasks efficiently. Essential hand tools include tape dispensers, box cutters, utility knives, and hand-held scanners for inventory and labeling. They also operate machinery such as automated sealing machines, shrink-wrap tunnels, and industrial scales for weighing packages. Depending on the warehouse, they might use pallet jacks or forklifts (with proper certification) to move larger loads. Software for printing labels or managing inventory, often integrated with a warehouse management system (WMS), also forms part of their daily toolkit.
Packer Skills & Qualifications
A Packer's qualifications primarily focus on efficiency, accuracy, and adherence to safety protocols. Employers prioritize practical experience in a warehouse or manufacturing setting. Formal education is less critical than demonstrated capability and a strong work ethic.
Requirements for a Packer vary significantly by industry and company size. Food processing plants demand strict hygiene and temperature control knowledge. E-commerce fulfillment centers emphasize speed and familiarity with scanning technologies. Smaller businesses might require a Packer to handle additional tasks like inventory or shipping coordination.
Certifications like forklift operation can significantly enhance a Packer's value, especially for roles involving material handling. The skill landscape for Packers is evolving with increased automation; however, human oversight and meticulous attention to detail remain indispensable. Entry-level positions often require minimal experience, while senior Packers might train new hires or manage specific packing lines.
Education Requirements
Technical Skills
- Material Handling: Ability to safely move and organize products, including manual lifting techniques and using pallet jacks.
- Basic Math Skills: For counting items, verifying quantities, and calculating shipping weights or dimensions.
- Scanning and Labeling: Proficiency with barcode scanners, printing labels, and applying them accurately to packages.
- Quality Control: Ability to inspect products and packaging for defects, ensuring items meet quality standards before shipment.
- Inventory Management (Basic): Understanding of stock rotation, locating items, and reporting discrepancies.
- Packaging Techniques: Knowledge of various packing methods, materials (boxes, bubble wrap, tape), and ensuring secure, damage-free packaging.
- Equipment Operation (Basic): Familiarity with shrink wrap machines, tape dispensers, and potentially automated packing systems.
- Warehouse Management System (WMS) Interaction: Basic data entry and navigation within WMS for order fulfillment or inventory updates.
Soft Skills
- Attention to Detail: Essential for ensuring correct items, quantities, and packaging quality, preventing errors and customer complaints.
- Time Management: Crucial for meeting production quotas and shipping deadlines, especially in fast-paced environments like e-commerce fulfillment.
- Physical Stamina: Necessary for standing for long periods, repetitive movements, and lifting packages, maintaining productivity throughout shifts.
- Safety Consciousness: Vital for adhering to workplace safety rules, handling equipment properly, and preventing injuries in a potentially hazardous environment.
- Teamwork: Important for coordinating with other Packers, material handlers, and supervisors to maintain workflow and achieve collective goals.
- Adaptability: Useful for adjusting to changing packing demands, different product types, or new equipment without significant disruption.
- Problem-Solving: Helps in quickly identifying and resolving issues like damaged packaging, missing items, or machine malfunctions to keep operations running smoothly.
- Reliability: Fundamental for consistent attendance and punctuality, ensuring production schedules are met and team operations are not disrupted by absences or delays.
How to Become a Packer
Entering the field of a Packer involves straightforward pathways, primarily focusing on practical skills and reliability. Unlike many other careers, a formal degree is rarely a prerequisite for this role. Most individuals secure a Packer position through direct applications to manufacturing plants, warehouses, or distribution centers, often starting with little to no prior experience.
The typical timeline for landing a Packer job can be relatively quick, sometimes within a few weeks, especially in areas with high demand for logistics and production staff. Entry strategies vary by company size; larger corporations might have more structured HR processes, while smaller businesses or local agencies may hire more informally. Geographic location plays a significant role; areas with robust manufacturing or e-commerce industries will have more opportunities.
A common misconception is that these jobs offer no room for growth; however, many companies promote Packers to roles like Team Lead, Quality Control, or Inventory Management based on performance and tenure. Networking, while less formal than in professional services, still matters. Showing initiative and a strong work ethic during temporary assignments can often lead to permanent employment, overcoming any initial barriers to entry.
Step 1
Step 2
Step 3
Step 4
Step 5
Step 6
Education & Training Needed to Become a Packer
The role of a Packer primarily focuses on the efficient and accurate packaging of goods for shipment or storage. Educational pathways for this role are typically less formal than many other professions, emphasizing practical skills and on-the-job training. While no specific degree is usually required, a high school diploma or GED is often a baseline expectation for entry-level positions. This foundational education ensures basic literacy, numeracy, and the ability to follow instructions, which are crucial for maintaining quality and safety standards.
Formal degree programs are generally not relevant for a Packer role. Instead, alternative learning paths like vocational training, industry certifications, or direct on-the-job training are the most common and effective. On-the-job training can range from a few days to several weeks, depending on the complexity of the products and packaging processes. Some employers might offer internal certifications for specific packaging machinery or safety protocols. These internal programs are typically free, as they are part of the employment process, and their completion time is integrated into the initial training period.
The market perception and employer acceptance for Packers heavily favor practical experience and a strong work ethic over academic credentials. Employers prioritize candidates who demonstrate attention to detail, efficiency, and reliability. Continuous learning in this field often involves staying updated on new packaging technologies, safety regulations, and inventory management systems, which are typically learned through employer-provided training modules. The cost for relevant training is usually minimal, often covered by the employer, and time commitments are typically short, focusing on immediate operational needs rather than long-term academic study.
Packer Salary & Outlook
Compensation for a Packer varies significantly based on several factors, extending beyond just base wages. Geographic location plays a crucial role; areas with a higher cost of living or strong industrial presence often command higher hourly rates. For instance, salaries in major metropolitan logistics hubs typically exceed those in rural regions due to localized demand and economic conditions.
Experience, specialization, and the specific materials handled also influence earning potential. Packers who handle hazardous materials, operate specialized machinery, or possess certifications for specific packing techniques may earn more. Total compensation packages often include benefits such as health insurance, paid time off, and retirement contributions, which add substantial value beyond the hourly wage. Some roles may also offer production bonuses or overtime pay, significantly boosting annual income.
Industry-specific trends affect compensation. The e-commerce sector, for example, often sees fluctuating demand that can lead to higher wages during peak seasons. Larger companies generally offer more competitive pay and benefits compared to smaller operations. While remote work is not applicable for this hands-on role, understanding local market dynamics and negotiating based on demonstrated efficiency and reliability can enhance earning potential. International markets present different wage structures, with these U.S. figures serving as a benchmark.
Salary by Experience Level
Level | US Median | US Average |
---|---|---|
Packer | $34k USD | $36k USD |
Senior Packer | $38k USD | $40k USD |
Packing Supervisor | $48k USD | $50k USD |
Packing Manager | $62k USD | $65k USD |
Market Commentary
The job market for Packers shows consistent demand, driven by the expanding e-commerce sector and global supply chain requirements. The Bureau of Labor Statistics projects stable growth for material moving occupations, which includes Packers, with an outlook influenced by consumer spending habits and manufacturing output. Automation in warehousing and logistics facilities, including advanced packing machinery, is a significant trend. While this technology can streamline processes, it also shifts the demand towards Packers who can operate and oversee these automated systems, rather than solely manual labor.
Emerging opportunities for Packers include roles in specialized logistics, cold chain packaging for pharmaceuticals, and custom crating for high-value goods. The supply and demand dynamics for general packing roles are relatively balanced, though peak seasons, such as holidays, often create temporary spikes in demand, leading to increased hiring and overtime opportunities. Geographic hotspots for packing jobs include major port cities, industrial zones, and areas with large distribution centers.
Future-proofing for Packers involves continuous learning and adapting to new technologies. Acquiring skills in inventory management software, operating forklifts, or understanding lean manufacturing principles can enhance job security. The profession is generally recession-resistant as the movement of goods remains essential even during economic downturns. However, economic slowdowns can impact specific industries, leading to temporary lulls in demand. The long-term outlook emphasizes efficiency, precision, and adaptability to evolving packaging standards.
Packer Career Path
Career progression for a Packer typically unfolds through demonstrated efficiency, attention to detail, and a commitment to quality. Initial advancement often focuses on mastering the core packing processes and becoming a reliable individual contributor. Growth in this field largely depends on an individual's ability to take on more complex tasks, train new colleagues, and eventually oversee team operations.
Advancement can lead to supervisory or management roles, shifting from hands-on packing to coordinating workflows, managing staff, and optimizing packing operations. While the individual contributor (IC) track might involve becoming a highly specialized or lead packer, the management track emphasizes leadership, process improvement, and team development. Company size, industry, and the specific products handled significantly influence these paths, with larger organizations often offering more structured promotional avenues.
Lateral movement might involve transitioning to roles in inventory management, shipping, or quality control, leveraging a deep understanding of product handling and logistics. Continuous learning, particularly in areas like lean manufacturing, safety protocols, and inventory systems, supports progression. Networking within the facility and demonstrating consistent reliability are key to moving up. Certifications in areas like forklift operation or hazardous material handling can also mark significant progression and open new opportunities.
Packer
0-2 yearsKey Focus Areas
Senior Packer
2-4 yearsKey Focus Areas
Packing Supervisor
4-7 years total experienceKey Focus Areas
Packing Manager
7+ years total experienceKey Focus Areas
Packer
0-2 yearsResponsible for accurately and efficiently packing products according to specific guidelines and customer orders. Ensures products are safely prepared for shipment, preventing damage. Works independently on assigned packing stations, contributing to daily output targets. Collaborates with team members to maintain a clean and organized work area.
Key Focus Areas
Mastering various packing techniques, including proper product handling, labeling, and protective packaging. Developing speed and accuracy while maintaining high quality standards. Understanding and adhering to all safety protocols and company policies. Learning to operate basic packing machinery and tools efficiently.
Senior Packer
2-4 yearsHandles more complex or specialized packing tasks, often involving delicate or high-value items. Acts as a go-to resource for less experienced packers, offering informal training and support. Maintains high levels of productivity and quality, often exceeding standard expectations. May assist with inventory checks and material replenishment.
Key Focus Areas
Developing expertise in handling diverse product types and complex packing requirements. Training new packers and providing on-the-job guidance. Identifying and suggesting improvements to packing processes for increased efficiency or safety. Taking initiative in problem-solving and quality assurance.
Packing Supervisor
4-7 years total experienceDirectly supervises a team of packers, overseeing daily operations and ensuring production targets are met. Responsible for assigning tasks, monitoring performance, and providing immediate feedback. Troubleshoots operational issues and ensures compliance with safety and quality standards. Manages packing material inventory and equipment readiness.
Key Focus Areas
Developing leadership skills, including effective communication, delegation, and conflict resolution. Learning to schedule and assign tasks to optimize team productivity. Understanding and implementing quality control procedures. Focusing on process improvement and waste reduction within the packing area.
Packing Manager
7+ years total experienceManages the entire packing department, including multiple teams and supervisors. Develops and implements operational strategies to optimize efficiency, cost-effectiveness, and quality. Responsible for hiring, training, and performance management of all packing staff. Oversees budget for packing materials and equipment, ensuring regulatory compliance and safety.
Key Focus Areas
Strategic planning for packing operations, including capacity planning and resource allocation. Developing and implementing training programs for packing staff. Collaborating with other departments like logistics, production, and quality assurance to streamline the supply chain. Driving continuous improvement initiatives using data and analytics.
Job Application Toolkit
Ace your application with our purpose-built resources:
Global Packer Opportunities
The Packer role offers limited direct international mobility, as it often involves physical presence in manufacturing or logistics facilities. However, global demand for efficient supply chains means opportunities exist in countries with robust industrial sectors. Cultural differences impact workplace safety standards and labor laws. Individuals consider international opportunities to access better wages or working conditions in developed economies.
Global Salaries
Packer salaries vary significantly by region and country, reflecting local economies and labor laws. In North America, specifically the United States, average hourly wages range from $15 to $20 USD, translating to $31,200 to $41,600 annually. Canada offers similar ranges, often between CAD $18 and CAD $25 per hour, or approximately $37,440 to $52,000 annually.
European countries present diverse compensation. In Germany, a Packer might earn €12 to €16 per hour, which is €24,960 to €33,280 annually (approximately $27,000 to $36,000 USD). The UK sees hourly rates of £10 to £13, equating to £20,800 to £27,040 annually (around $26,000 to $34,000 USD). These figures reflect higher purchasing power in Western Europe compared to Eastern Europe.
Asia-Pacific regions, like Australia, offer AUD $22 to AUD $28 per hour, or AUD $45,760 to AUD $58,240 annually (about $30,000 to $38,000 USD). In contrast, countries like India or Vietnam have much lower wages, often below $500 USD per month, reflecting lower cost of living and different economic structures. Latin America, such as Mexico, offers wages around MXN $7,000 to MXN $12,000 per month (approximately $400 to $700 USD).
Salary structures also differ; some countries offer comprehensive social benefits like healthcare and generous vacation time, which effectively increase total compensation. Tax implications vary widely, impacting take-home pay. Experience and education for a Packer role generally have a lesser impact on international compensation compared to highly skilled professions, though specific certifications in logistics or safety can sometimes provide a slight edge.
Remote Work
Remote work opportunities for a Packer are virtually non-existent, as the role inherently requires physical presence and hands-on interaction with products and packaging equipment. This profession is fundamentally location-dependent, performed within warehouses, factories, or distribution centers.
Digital nomad lifestyles do not apply to this role. International remote work policies by employers are not relevant for Packers. The nature of the work, involving physical handling and assembly, makes it impossible to perform from a remote location. Therefore, considerations like time zones, internet requirements, or digital collaboration tools are not applicable to this specific job title.
Visa & Immigration
Securing a visa for a Packer role in another country can be challenging due to the generally low-skilled nature of the position. Most skilled worker visa programs prioritize professions requiring specialized education or training. Common pathways might involve general labor or seasonal worker visas, if available, rather than specific skilled worker categories.
Popular destination countries for such roles often include those with high demand for manual labor in manufacturing or agriculture, like Canada, Australia, or some European nations. However, requirements are strict, often necessitating a pre-arranged job offer and demonstrating that no local workers are available. Education credential recognition is usually not a primary concern for this role, as formal degrees are not typically required.
Visa timelines vary, but applications for non-skilled labor can take several months. Pathways to permanent residency through this role are uncommon and usually require long-term continuous employment and meeting general immigration criteria. Language requirements depend on the destination country, but basic proficiency is often sufficient. Practical considerations include proving financial stability and adhering to all immigration regulations.
2025 Market Reality for Packers
Understanding the current market realities for packers is crucial for career planning. The landscape for manual labor roles, including packing, has seen significant evolution from 2023 to 2025, largely driven by post-pandemic supply chain adjustments and the accelerating integration of automation and AI in logistics.
Broader economic factors directly influence packing volumes, as demand for goods dictates production and distribution activity. Market realities for packers also vary considerably by experience level, with entry-level roles facing different challenges than those requiring some specialization. Geographic region and company size also play a large role, as large e-commerce giants or manufacturing plants have different needs than smaller local businesses. This analysis provides an honest assessment to help set realistic expectations.
Current Challenges
Packers face increasing pressure from automation. Many companies invest in robotic packing solutions, reducing the need for manual labor in high-volume settings. Competition for available roles remains high, especially for entry-level positions without specialized skills. Economic shifts can quickly impact consumer demand, leading to fluctuating work availability in manufacturing and logistics.
Growth Opportunities
Despite automation trends, strong demand persists for packers in specialized areas. These include handling fragile or complex items, custom packaging, and quality control. Roles requiring a blend of manual dexterity and basic machine operation or data entry are emerging as valuable specializations.
Packers can position themselves advantageously by acquiring skills in operating automated packing machinery, basic maintenance, or using inventory management software. Underserved markets often include smaller, niche manufacturing sectors or local fulfillment centers that have not yet fully automated. Developing strong attention to detail and efficiency in a fast-paced environment also provides a competitive edge.
Certain sectors, such as food processing, pharmaceuticals, and specialized manufacturing, maintain consistent demand for skilled packers due to specific handling or regulatory requirements. Investing in training for forklift operation or warehouse management systems can open doors to more advanced roles. The market correction might lead to more localized production, potentially creating new, smaller-scale packing opportunities closer to consumers.
Current Market Trends
Demand for packers remains stable in specific sectors, particularly e-commerce fulfillment and essential goods manufacturing. However, the overall hiring landscape for manual packing roles shows a gradual shift. Companies increasingly seek efficiency through automation, impacting the volume of purely manual packing jobs. This trend accelerated between 2023 and 2025 as businesses optimized supply chains post-pandemic and adopted AI-driven logistics.
Economic conditions influence packing volumes directly. A slowdown in consumer spending or manufacturing output can lead to reduced shifts or temporary layoffs for packers. Technology, especially advanced robotics and AI-powered sorting systems, changes the job requirements. Employers now value packers who can operate or monitor automated machinery, troubleshoot minor issues, and adapt to digital inventory systems.
Salary trends for packers show modest growth, often tied to minimum wage adjustments or cost-of-living increases, rather than significant skill-based premiums. Market saturation exists at the basic entry level, while roles requiring machine operation or quality control experience see slightly less competition. Geographic variations are significant; areas with large distribution centers, manufacturing hubs, or robust e-commerce operations offer more consistent work. Remote work is not applicable to this hands-on role.
Emerging Specializations
Technological advancement and industry evolution consistently create new specialization opportunities across various fields, even in roles traditionally viewed as manual. For Packers, automation, data integration, and advanced logistics are reshaping responsibilities, leading to emerging niches that demand refined skills. Early positioning in these evolving areas is crucial for career advancement and securing premium compensation in 2025 and beyond.
Specializing in cutting-edge areas allows professionals to move beyond routine tasks into roles with higher strategic value. While established specializations offer stability, emerging areas often promise accelerated career growth and increased earning potential due to a scarcity of skilled professionals. The timeline for these emerging areas to become mainstream and create significant job opportunities varies, but many are already gaining traction, indicating a shift in industry needs.
Pursuing emerging specializations involves a balance of risk and reward. It requires proactive learning and adaptability, but the payoff includes enhanced job security and the chance to shape future operational standards. Understanding these shifts helps Packers identify strategic career paths, ensuring they remain valuable contributors in an increasingly automated and data-driven supply chain environment.
Automated Packing System Operator
Smart Packaging Quality Analyst
Eco-Conscious Packaging Specialist
Virtual Packing Workflow Designer
Pros & Cons of Being a Packer
Choosing a career path requires a thorough understanding of both its appealing aspects and its inherent difficulties. The experience within any profession, including that of a packer, can vary significantly based on the specific company culture, the industry (e.g., food, retail, manufacturing), and the nature of the products handled. Factors such as individual personality and career stage also influence how one perceives the daily realities. What one person considers a benefit, another might view as a challenge. This assessment aims to provide an honest, balanced overview of the packer role, helping prospective individuals set realistic expectations for the work environment, demands, and potential rewards.
Pros
Entry into this role typically requires minimal formal education or prior experience, making it accessible to a wide range of job seekers, including those new to the workforce.
Job availability is generally high across various industries, as almost all products require some form of packing before distribution, offering consistent employment opportunities.
The work often provides a clear and immediate sense of accomplishment as products are prepared for shipment, allowing workers to see the tangible results of their efforts.
Many packing jobs offer regular, predictable shifts, which can help in planning personal life and maintaining a stable routine compared to roles with highly variable hours.
This role can be a good entry point into manufacturing or logistics, providing foundational experience that can lead to other roles within the same company or industry over time.
For individuals who prefer active work over desk-bound jobs, the physical nature of packing keeps them moving and engaged, which can be beneficial for physical health.
Some packing roles, especially in larger operations, may offer opportunities for overtime pay, allowing individuals to increase their earnings if they are willing to work additional hours.
Cons
The work is often highly repetitive, performing the same motions and tasks repeatedly throughout a shift, which can lead to monotony and boredom over time.
Physical strain is common due to standing for long periods, bending, lifting, and repetitive arm movements, potentially leading to back pain, joint issues, or repetitive strain injuries.
Work environments can be noisy, dusty, or temperature-controlled (very hot or very cold) depending on the products being packed, which can be uncomfortable or require specific personal protective equipment.
Career advancement opportunities are typically limited within a packing role itself; progression usually requires moving into supervisory roles, quality control, or other departments, which may demand additional training or education.
Wages for packing positions often start at or near minimum wage, and while they can increase with experience or seniority, the overall earning potential may be lower compared to other industrial or manufacturing roles.
Productivity demands and quotas are frequently in place, creating pressure to maintain a fast pace throughout the shift, which can add stress and reduce the ability to take breaks at will.
Work schedules can be inflexible, with shifts that may include nights, weekends, or mandatory overtime, making it challenging to balance with personal life or other commitments.
Frequently Asked Questions
Packers face distinct questions about the physical demands, work environment, and career stability within this essential role. This section addresses the most common concerns about entry requirements, daily tasks, and opportunities for growth, helping individuals understand if this career aligns with their expectations.
What are the typical entry requirements for a packer role?
Many packer positions do not require specific educational degrees or extensive prior experience. Employers often provide on-the-job training covering safety protocols, packing techniques, and equipment operation. However, a strong work ethic, attention to detail, and the ability to follow instructions are essential for success in this role.
How long does it take to become job-ready as a packer?
The timeline to become job-ready as a packer is usually very short, often just a few days to a week of on-the-job training. Most companies focus on quickly integrating new hires into the workflow, teaching them the specific packing procedures and safety guidelines for their products. You can often start earning quickly after being hired.
What are the salary expectations and financial benefits for a packer?
Packer salaries vary based on location, industry, and experience, but most entry-level positions offer hourly wages. Many roles also provide benefits like health insurance, paid time off, and opportunities for overtime, which can significantly boost overall earnings. It is important to inquire about the full compensation package during the hiring process.
What is the typical work-life balance and physical demand of a packer job?
Packer roles often involve consistent schedules, which can be beneficial for work-life balance. However, the work can be physically demanding, requiring prolonged standing, lifting, and repetitive motions. Some positions may involve shift work or overtime during peak seasons, so it is important to understand the specific demands of the role you are considering.
Is the packer role a secure job with good market demand?
Job security for packers is generally stable, as these roles are essential across various industries, including manufacturing, logistics, and e-commerce. While automation may impact some tasks, the need for human oversight and specialized packing remains high. The demand for efficient and reliable packing continues to grow with consumer needs.
What are the career growth opportunities for a packer?
Career growth for packers often involves advancing to roles like lead packer, quality control inspector, or warehouse supervisor. Many companies offer internal training programs to help employees develop new skills and take on more responsibilities. Demonstrating reliability, efficiency, and leadership can open doors to these advancement opportunities.
Can I work remotely as a packer, or is it always an on-site role?
Packer roles are typically on-site due to the nature of handling physical goods and operating equipment. Remote work options are extremely rare for this specific position. Most packing facilities require workers to be present to manage inventory, operate machinery, and ensure products are packaged correctly for shipment.
What are some common misconceptions about being a packer?
A common misconception is that packing is a simple, unskilled job. While entry-level, it requires strong attention to detail, precision, and adherence to strict safety and quality standards. Mistakes can lead to damaged goods, shipping errors, and significant costs, making the packer's role critical to a company's efficiency and customer satisfaction.
Related Careers
Explore similar roles that might align with your interests and skills:
Packaging Operator
A growing field with similar skill requirements and career progression opportunities.
Explore career guidePackaging Supervisor
A growing field with similar skill requirements and career progression opportunities.
Explore career guidePackaging Technician
A growing field with similar skill requirements and career progression opportunities.
Explore career guideWarehouse Packer
A growing field with similar skill requirements and career progression opportunities.
Explore career guidePacking Line Operator
A growing field with similar skill requirements and career progression opportunities.
Explore career guideAssess your Packer readiness
Understanding where you stand today is the first step toward your career goals. Our Career Coach helps identify skill gaps and create personalized plans.
Skills Gap Analysis
Get a detailed assessment of your current skills versus Packer requirements. Our AI Career Coach identifies specific areas for improvement with personalized recommendations.
See your skills gapCareer Readiness Assessment
Evaluate your overall readiness for Packer roles with our AI Career Coach. Receive personalized recommendations for education, projects, and experience to boost your competitiveness.
Assess your readinessSimple pricing, powerful features
Upgrade to Himalayas Plus and turbocharge your job search.
Himalayas
Himalayas Plus
Himalayas Max
Find your dream job
Sign up now and join over 100,000 remote workers who receive personalized job alerts, curated job matches, and more for free!
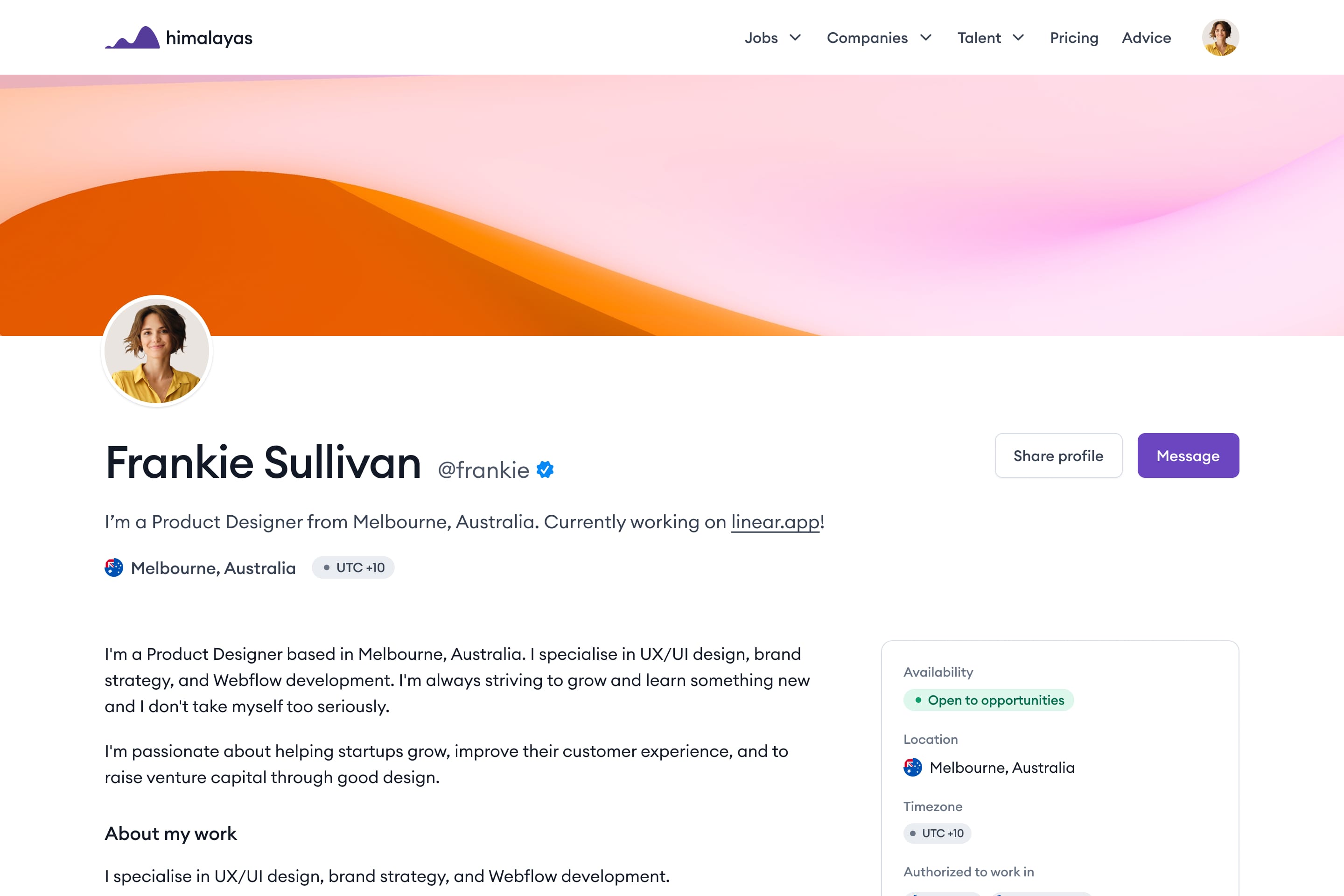