Complete Orthotic Finish Grinding Technician Career Guide
Orthotic Finish Grinding Technicians are the skilled artisans who bring custom orthotic devices to life, meticulously shaping and refining them to ensure a perfect fit and optimal function for patients. This specialized role combines precision craftsmanship with a deep understanding of patient needs, transforming raw materials into comfortable, therapeutic solutions. It's a hands-on career vital to patient mobility and quality of life, offering a unique blend of technical skill and direct impact.
Key Facts & Statistics
Median Salary
$47,400 USD
(BLS, May 2023)
Range: $30k - $60k+ USD
Growth Outlook
5%
as fast as average (BLS, 2022-2032)
Annual Openings
≈1,300
openings annually (BLS, 2022-2032)
Top Industries
Typical Education
High school diploma or equivalent; often requires on-the-job training, vocational school, or an associate's degree in orthotics and prosthetics technology
What is an Orthotic Finish Grinding Technician?
An Orthotic Finish Grinding Technician specializes in the final shaping and smoothing of custom-made orthotic devices. These devices, which include shoe inserts, braces, and splints, support or correct biomechanical problems in the human body. This technician's primary role is to ensure that each orthotic device is precisely contoured, comfortable for the patient, and meets the exact specifications of the prescribing orthotist.
This role is distinct from an Orthotic Fabricator or a CAD/CAM Designer. While a fabricator might cast, mold, or assemble the initial device, and a designer creates the digital model, the Finish Grinding Technician performs the critical hand-finishing work. They transform a rough-formed orthotic into a patient-ready product, focusing on fine details, smooth edges, and specific anatomical contours to prevent discomfort and ensure therapeutic effectiveness. Their expertise directly impacts patient comfort and the success of the orthotic intervention.
What does an Orthotic Finish Grinding Technician do?
Key Responsibilities
- Operate specialized grinding machines to precisely shape and smooth custom orthotic devices according to patient specifications and prescription details.
- Inspect finished orthotics for surface imperfections, rough edges, and dimensional accuracy, ensuring they meet quality standards and patient comfort requirements.
- Adjust machine settings, grinding wheel types, and abrasive levels to achieve the desired finish on various orthotic materials, including plastics, carbon fiber, and foam.
- Perform routine maintenance and cleaning of grinding equipment, including replacing worn grinding wheels and ensuring proper dust collection systems are operational.
- Review work orders and blueprints to understand the exact contours, reliefs, and modifications required for each orthotic device.
- Collaborate with orthotists and other technicians to discuss complex cases, resolve finishing challenges, and ensure the final product aligns with clinical needs.
- Maintain a clean and organized workspace, adhering to safety protocols for dust control and the use of personal protective equipment (PPE).
Work Environment
Orthotic Finish Grinding Technicians typically work in a workshop or laboratory setting within an orthotic and prosthetic (O&P) facility, medical device manufacturing plant, or a hospital's orthotics department. The environment can be noisy due to grinding machinery and dusty, requiring consistent use of personal protective equipment (PPE) like respirators and safety glasses. Technicians often stand for extended periods while operating equipment.
The work is highly hands-on and detailed, requiring focus and precision. While individual grinding tasks are independent, technicians collaborate closely with other production staff, orthotists, and quality control teams to ensure devices meet specifications. The pace of work is steady, driven by patient demand and production schedules, with a strong emphasis on quality and timely delivery of custom devices. Work hours are typically standard business hours, with minimal travel.
Tools & Technologies
Orthotic Finish Grinding Technicians primarily use specialized grinding equipment, including belt sanders, bench grinders, and automated CNC grinding machines, each fitted with various abrasive wheels and papers. They also utilize hand tools such as rasps, files, and utility knives for fine detail work and manual shaping. Precision measuring instruments like calipers and micrometers are essential for verifying dimensions and ensuring accuracy.
Beyond physical tools, technicians work with material handling systems for plastics, foams, and composite materials like carbon fiber. They must understand and apply principles of material science related to orthotics to achieve optimal finishes. Safety equipment, including respirators, safety glasses, and gloves, is integral to their daily work environment.
Orthotic Finish Grinding Technician Skills & Qualifications
The Orthotic Finish Grinding Technician role demands a precise blend of manual dexterity, material knowledge, and adherence to patient-specific designs. This position focuses on the critical final stages of orthotic fabrication, ensuring devices meet exact specifications for patient comfort, function, and durability. Qualification requirements vary significantly by the size and type of the orthotic lab or practice. Larger, high-volume manufacturing facilities often prioritize speed and efficiency alongside accuracy, while smaller, custom labs may emphasize intricate craftsmanship and direct collaboration with clinicians.
Entry-level positions frequently focus on developing foundational grinding techniques and material handling under supervision. As technicians gain experience, they progress to handling more complex orthotic designs, working with advanced materials, and achieving higher levels of finish quality. Senior technicians often take on mentorship roles, contribute to process improvements, and troubleshoot fabrication challenges. Formal education, while beneficial, often takes a backseat to demonstrable practical experience and on-the-job training in this field. Certifications from bodies like the American Board for Certification in Orthotics, Prosthetics & Pedorthics (ABC) are highly valued, particularly the Orthotic Fitter or Technician certifications, as they validate a standardized level of competency and commitment to the profession.
The skill landscape for Orthotic Finish Grinding Technicians is steadily evolving with the integration of CAD/CAM technologies and 3D printing. While hands-on grinding remains crucial, familiarity with digital design files and automated finishing processes is becoming increasingly important. Technicians who can bridge traditional manual skills with digital fabrication workflows will find themselves highly marketable. The balance between breadth of skills (e.g., working with various orthotic types) and depth (mastery of specific material grinding) depends on the employer's needs. Maintaining current knowledge of new materials and finishing techniques is essential for long-term career success in this specialized field.
Education Requirements
Technical Skills
- Precision Grinding Techniques (belt, bench, cone grinders)
- Material Science (thermoforming plastics, carbon fiber, metals, foams)
- Orthotic Design Interpretation (reading blueprints, prescriptions, and molds)
- Calibration and Maintenance of Grinding Equipment
- Dust Collection and Ventilation System Operation
- Quality Control and Inspection (measuring, visual checks)
- Hand Tool Proficiency (rasps, files, sanders, Dremel tools)
- Adhesive and Bonding Agent Application
- Surface Finishing and Polishing Techniques
- Basic CAD/CAM Software Familiarity (for reviewing digital models)
- Personal Protective Equipment (PPE) Usage and Protocols
- Waste Management and Material Recycling Practices
Soft Skills
- Attention to Detail: Critical for ensuring orthotics meet precise measurements and patient specifications, preventing discomfort or functional issues.
- Manual Dexterity: Essential for intricate grinding, shaping, and finishing tasks that require fine motor control and steady hands.
- Problem-Solving: Important for identifying and correcting imperfections, troubleshooting material issues, and adapting techniques for unique orthotic designs.
- Patience: Necessary for repetitive tasks and achieving high-quality finishes, especially when working with difficult materials or complex shapes.
- Time Management: Crucial for completing a high volume of finishing tasks efficiently while maintaining quality standards and meeting production deadlines.
- Adaptability: Important for adjusting to new materials, tools, and design specifications, as well as handling unexpected challenges in the fabrication process.
- Safety Consciousness: Essential for adhering to strict safety protocols when operating grinding machinery and handling materials, protecting oneself and colleagues.
How to Become an Orthotic Finish Grinding Technician
Entering the Orthotic Finish Grinding Technician field typically involves a mix of hands-on training and specific skill development. While a formal degree is not always required, vocational training or apprenticeships are highly beneficial. The timeline for entry can range from a few months for someone with related manufacturing experience to over a year for a complete beginner, as practical skills take time to develop.
Multiple entry routes exist, including direct entry-level positions, vocational programs in orthotics and prosthetics (O&P) technology, or on-the-job training within an orthotic lab. Direct entry is more common in smaller, independent labs, which may prioritize a strong work ethic and willingness to learn. Larger O&P facilities or manufacturers often prefer candidates with some prior experience or formal training, as they have established production lines and quality control standards.
Networking within the O&P community, attending industry workshops, or connecting with local orthotic labs can significantly aid your job search. Many roles are filled through word-of-mouth or referrals. Understanding the specific needs of different labs—whether they focus on custom orthotics, mass production, or specialized devices—will help you tailor your approach and highlight relevant skills. Building a portfolio of your work, even if it's from personal projects or volunteer efforts, can demonstrate your capabilities effectively.
Step 1
Step 2
Step 3
Step 4
Step 5
Step 6
Education & Training Needed to Become an Orthotic Finish Grinding Technician
Becoming an Orthotic Finish Grinding Technician primarily involves hands-on skill development rather than extensive formal degrees. Most technicians learn through on-the-job training, apprenticeships, or specialized short-term vocational programs. Four-year university degrees are not typically required or beneficial for this specific role, as the focus is on practical fabrication and finishing techniques. Alternative paths, such as vocational certificates or company-sponsored training, are highly effective and often preferred by employers.
Vocational programs or specialized courses, when available, might cost between $2,000 and $8,000 and typically last from a few weeks to six months. In contrast, on-the-job training or apprenticeships may offer paid learning opportunities, with completion times varying from six months to two years, depending on the complexity of skills required by the employer. Employers value practical experience and a demonstrated ability to work with precision, rather than academic credentials. Continuous learning often involves mastering new materials, technologies, and finishing techniques as the industry evolves.
The market perception of credentials for this role heavily favors practical experience and precision skills. While no specific accreditation is universally mandatory, some employers may prefer candidates with certifications in specific manufacturing processes or safety protocols. Educational needs for an Orthotic Finish Grinding Technician focus on material science, proper use of grinding and finishing tools, and quality control. The ability to work with various materials like plastics, carbon fiber, and metals is crucial. Cost-benefit considerations strongly lean towards vocational training or apprenticeships, as they provide direct, relevant skills without the significant time and financial investment of a traditional degree.
Orthotic Finish Grinding Technician Salary & Outlook
Compensation for an Orthotic Finish Grinding Technician varies significantly based on several factors. Geographic location plays a crucial role, with higher salaries typically found in areas with a higher cost of living or concentrated medical device manufacturing. For example, salaries in major metropolitan areas or states with strong healthcare sectors often exceed those in rural regions.
Years of experience and specialized skills also dramatically influence earning potential. Technicians with a deep understanding of various materials, advanced grinding techniques, or CAD/CAM integration command higher pay. Total compensation packages often extend beyond base salary to include performance bonuses, health and dental benefits, and retirement contributions like 401(k) plans. Some employers may also offer professional development allowances for specialized training or certifications.
Industry-specific trends, such as the increasing demand for custom orthotics and prosthetic devices, drive salary growth in this field. Facilities serving a high volume of patients or specializing in complex cases may offer more competitive wages. Negotiating leverage comes from demonstrating precision, efficiency, and a proven track record of quality work. Remote work is generally not applicable to this hands-on role, which requires specialized equipment and a controlled environment.
While the salary figures provided are in USD and reflect the U.S. market, international variations exist. Countries with robust healthcare systems and similar manufacturing needs may offer comparable or adjusted compensation. Understanding these factors helps technicians maximize their earning potential throughout their careers.
Salary by Experience Level
Level | US Median | US Average |
---|---|---|
Junior Orthotic Finish Grinding Technician | $35k USD | $38k USD |
Orthotic Finish Grinding Technician | $45k USD | $47k USD |
Senior Orthotic Finish Grinding Technician | $55k USD | $58k USD |
Lead Orthotic Finish Grinding Technician | $65k USD | $68k USD |
Market Commentary
The job market for Orthotic Finish Grinding Technicians shows steady demand, largely driven by an aging population and increased awareness of foot and ankle health. The Bureau of Labor Statistics projects growth for medical equipment repairers, a broader category that includes these technicians, at about 7% from 2022 to 2032, which is about as fast as the average for all occupations. This growth translates into approximately 2,000 new jobs over the decade.
Demand is particularly strong in areas with a high concentration of orthotic and prosthetic labs, hospitals, and specialized clinics. Technological advancements, such as the integration of 3D scanning and printing into orthotic fabrication, are evolving the role. Technicians who can adapt to these new technologies, combining traditional grinding skills with digital finishing processes, will find emerging opportunities. There is a consistent need for skilled individuals who can produce precise, high-quality custom devices.
The supply of qualified technicians often lags behind demand, creating a favorable market for those with specialized training and experience. This field is relatively recession-resistant, as the need for medical devices remains consistent regardless of economic fluctuations. Future-proofing involves continuous learning in new materials, advanced machinery operation, and quality control methodologies. Geographic hotspots include states like California, Florida, and Texas, which have large populations and significant healthcare infrastructure. Remote work is not feasible for this hands-on position.
Orthotic Finish Grinding Technician Career Path
Career progression for an Orthotic Finish Grinding Technician focuses on developing specialized manual dexterity, precision, and material knowledge. Advancement typically moves from foundational skill development to mastering complex custom adjustments and eventually leading teams.
Progression offers both individual contributor (IC) growth, emphasizing increasingly intricate fabrication and problem-solving, and a management track, which involves overseeing production, quality control, and training. Performance, dedication to continuous learning, and an eye for detail significantly influence advancement speed. Company size, from small custom labs to large manufacturing facilities, also dictates the available career paths and the scope of responsibilities at each level.
Lateral movement often involves specializing in specific orthotic types, such as prosthetics or advanced biomechanical devices, or transitioning into quality assurance, R&D, or even sales roles within the orthotic and prosthetic industry. Networking within professional organizations and continuous skill refinement through workshops or certifications, though less common for this specific role, can open doors to new opportunities and enhance industry reputation.
Junior Orthotic Finish Grinding Technician
0-2 yearsKey Focus Areas
Orthotic Finish Grinding Technician
2-5 yearsKey Focus Areas
Senior Orthotic Finish Grinding Technician
5-8 yearsKey Focus Areas
Lead Orthotic Finish Grinding Technician
8+ yearsKey Focus Areas
Junior Orthotic Finish Grinding Technician
0-2 yearsPerforms basic grinding and finishing tasks on orthotic devices under direct supervision. Follows detailed instructions to smooth edges, remove excess material, and prepare devices for final assembly. Works on less complex orthotic types, ensuring a clean and safe work environment. Limited decision-making; all work is quality checked.
Key Focus Areas
Develop fundamental grinding techniques, including material removal and shaping. Learn to identify different orthotic materials and their properties. Focus on safety protocols and proper use of grinding equipment. Begin understanding basic orthotic designs and their functional purpose. Attention to detail and consistency are critical early development points.
Orthotic Finish Grinding Technician
2-5 yearsIndependently performs grinding and finishing for a wide range of orthotic devices, including more complex custom pieces. Exercises judgment in selecting appropriate tools and methods for specific materials and designs. Maintains high quality standards with minimal supervision. May assist with initial quality checks on own work.
Key Focus Areas
Master advanced grinding techniques for various orthotic types and materials. Develop problem-solving skills for minor imperfections and deviations. Improve efficiency and speed while maintaining high quality standards. Begin assisting with training of new junior technicians. Understand the clinical implications of precise finishing.
Senior Orthotic Finish Grinding Technician
5-8 yearsHandles the most intricate and custom orthotic finishing projects, often serving as a subject matter expert. Provides technical guidance and troubleshooting support to other technicians. Conducts quality assurance checks on finished products. May participate in prototyping new designs or materials. Works with significant autonomy and takes ownership of complex cases.
Key Focus Areas
Refine expertise in highly specialized or challenging orthotic finishing. Develop strong mentorship and coaching abilities for junior colleagues. Contribute to process improvement initiatives and quality control standards. Understand workflow optimization and material waste reduction. Begin to develop leadership qualities and a broader understanding of orthotic manufacturing.
Lead Orthotic Finish Grinding Technician
8+ yearsManages the daily operations of the finish grinding department, ensuring production targets and quality standards are met. Responsible for training, scheduling, and performance reviews of the team. Implements process improvements and new techniques to enhance efficiency and product quality. Collaborates with other department leads to optimize overall production flow.
Key Focus Areas
Lead and manage a team of orthotic finish grinding technicians. Develop comprehensive training programs and standard operating procedures. Oversee production schedules, quality control, and workflow efficiency for the grinding department. Focus on team development, conflict resolution, and performance management. Strategic planning for equipment maintenance and material procurement.
Job Application Toolkit
Ace your application with our purpose-built resources:
Orthotic Finish Grinding Technician Resume Examples
Proven layouts and keywords hiring managers scan for.
View examplesOrthotic Finish Grinding Technician Cover Letter Examples
Personalizable templates that showcase your impact.
View examplesTop Orthotic Finish Grinding Technician Interview Questions
Practice with the questions asked most often.
View examplesOrthotic Finish Grinding Technician Job Description Template
Ready-to-use JD for recruiters and hiring teams.
View examplesGlobal Orthotic Finish Grinding Technician Opportunities
An Orthotic Finish Grinding Technician shapes and finishes custom orthopedic devices. This specialized role is crucial globally as demand for prosthetics and orthotics rises due to aging populations and chronic conditions. Technicians adapt to diverse healthcare standards and material specifications across countries. International opportunities exist, especially in regions with growing rehabilitation sectors or advanced medical manufacturing. No specific international certifications are broadly recognized, but local training and experience are highly valued.
Global Salaries
Salaries for Orthotic Finish Grinding Technicians vary significantly by region and experience. In North America, particularly the USA, entry-level technicians earn $35,000-$45,000 USD annually, while experienced professionals can reach $55,000-$70,000 USD. Canadian salaries are comparable, often ranging from $40,000-$60,000 CAD.
European salaries differ by country. In Germany, technicians might earn €30,000-€45,000 annually ($32,000-$48,000 USD equivalent), reflecting a strong manufacturing sector. The UK sees salaries from £22,000-£35,000 ($28,000-$45,000 USD). Scandinavian countries offer higher nominal salaries but also higher living costs. For example, in Sweden, earnings could be SEK 280,000-SEK 400,000 ($26,000-$37,000 USD).
Asia-Pacific markets, like Australia, offer $50,000-$70,000 AUD ($33,000-$47,000 USD). In emerging markets like India or Southeast Asia, salaries are considerably lower, perhaps $8,000-$15,000 USD annually, but purchasing power is higher. Benefits packages also differ; European countries often include more comprehensive healthcare and generous vacation time, while North American packages may involve higher employee contributions.
Tax rates and social security contributions significantly impact take-home pay, with European countries generally having higher deductions. Experience and specialized skills in advanced materials or digital finishing techniques can command higher compensation globally. There are no standardized international pay scales for this niche role, making local market research essential.
Remote Work
Orthotic Finish Grinding Technicians perform highly tactile, hands-on work. This role requires specialized machinery and direct interaction with materials, making full-time international remote work impossible. The core tasks of grinding, shaping, and finishing orthotic devices must occur on-site in a workshop or laboratory setting.
However, some related tasks might support remote work. These include digital design collaboration, material ordering, or quality control documentation. These activities represent a small fraction of the job. Digital nomad opportunities are not applicable to this profession due to its physical demands. Employers hiring internationally expect technicians to relocate and work within their facilities. International remote work policies are not relevant for this role, as physical presence is mandatory for the grinding and finishing processes.
Visa & Immigration
Orthotic Finish Grinding Technicians seeking international work typically apply for skilled worker visas. Countries like Canada, Australia, and Germany often have pathways for skilled trades and specialized manufacturing roles. Requirements usually include demonstrating professional experience, relevant training, and often an employer sponsorship.
Key destination countries as of 2025 include Canada (Express Entry, Provincial Nominee Programs), Australia (Skilled Nominated Visa subclass 190, Skilled Regional Visa subclass 491), and Germany (Skilled Immigration Act). These countries require credential recognition; applicants may need to have their training assessed by a local professional body. Language proficiency tests, such as IELTS for English or Goethe-Zertifikat for German, are often mandatory.
Visa timelines vary, from a few months to over a year, depending on the country and application volume. Permanent residency pathways exist, usually after several years of continuous skilled employment. Some countries may offer specific advantages if there is a demonstrated shortage in this specialized trade. Family visas for dependents are generally available once the primary applicant secures their work visa.
2025 Market Reality for Orthotic Finish Grinding Technicians
Understanding current market conditions is vital for Orthotic Finish Grinding Technicians to navigate career paths effectively. The orthotics field, while stable, has experienced subtle shifts since 2023 due to technological advancements and evolving healthcare landscapes. Post-pandemic, demand for custom orthotics has remained consistent, driven by an aging population and increased sports participation, but clinics face new operational considerations.
Broader economic factors, particularly healthcare spending and insurance policies, indirectly influence the volume of custom orthotic prescriptions, affecting lab workflow. Market realities for this specialized role vary significantly by geographic region, the presence of major medical centers, and the size of orthotic fabrication labs. This analysis provides an honest assessment of current hiring realities, helping technicians set realistic expectations and plan strategically.
Current Challenges
Orthotic Finish Grinding Technicians face increased competition for available roles, especially as some automation tools emerge for initial shaping processes. Market saturation exists in regions with numerous orthotic labs but limited patient growth. Economic uncertainty can delay elective medical procedures, reducing demand for custom orthotics. This creates fluctuating workflow for technicians. Expect job searches to take several weeks to a few months, depending on location and specialization.
Growth Opportunities
Despite some automation in initial stages, strong demand persists for Orthotic Finish Grinding Technicians skilled in precision work. Facilities specializing in complex neurological, pediatric, or sports orthotics frequently seek highly skilled finishers. Technicians can position themselves advantageously by mastering new materials like advanced composites and carbon fiber, which require specialized grinding techniques beyond traditional plastics.
Emerging opportunities exist in labs integrating 3D printing for orthotic blanks, where technicians are essential for the final, critical post-processing and fine-tuning. Underserved markets, particularly in rural or expanding suburban areas, may offer better opportunities for experienced technicians than highly saturated urban centers. Acquiring certifications in specific orthotic types or advanced materials provides a significant competitive advantage. Strategic career moves might involve seeking roles in research and development labs that focus on new orthotic designs and materials, or in facilities with strong patient referral networks and diverse case loads. The consistent need for custom fit ensures a stable, albeit specialized, career path for skilled grinding technicians.
Current Market Trends
Demand for Orthotic Finish Grinding Technicians remains steady but highly localized as of 2025. Hiring patterns show a consistent need for skilled technicians in specialized orthotic labs and prosthetic-orthotic facilities. The industry has seen minor shifts with some labs adopting advanced CAD/CAM for initial shaping, but the critical finish grinding still requires hands-on expertise. This ensures the precise fit and comfort of custom devices.
Economic conditions generally support the medical device sector, including orthotics, due to an aging population and increasing awareness of biomechanical support. However, insurance reimbursement policies and healthcare spending trends indirectly influence the volume of custom orthotic prescriptions. Technology trends, particularly 3D scanning and additive manufacturing, are transforming the initial design and fabrication of orthotic blanks. However, the final, crucial grinding and finishing steps remain highly manual, requiring a technician's detailed eye and skilled hand for optimal patient outcomes.
Employer requirements now emphasize not just manual dexterity but also an understanding of various materials, from thermoplastics to carbon fiber. Candidates with experience in complex geometries or specialized orthoses (e.g., for pediatrics or sports) are particularly sought after. Salary trends show modest growth, with experienced technicians commanding higher wages, especially in areas with fewer qualified professionals. Market saturation is low for highly skilled, experienced finish grinding technicians, though entry-level roles can be competitive in metropolitan areas. Remote work is not feasible for this hands-on role. Seasonal patterns are minimal, but patient referrals can fluctuate with school years or sports seasons.
Emerging Specializations
The field of orthotics and prosthetics is experiencing a significant transformation, driven by advancements in materials science, digital manufacturing, and personalized medicine. These technological shifts are creating entirely new specialization opportunities for skilled professionals like Orthotic Finish Grinding Technicians. Understanding these emerging niches allows technicians to proactively position themselves for future-oriented roles and secure enhanced career prospects.
Early positioning in these developing areas, particularly by 2025 and beyond, offers a distinct advantage. Professionals who acquire expertise in cutting-edge techniques and technologies often command premium compensation and experience accelerated career growth. While established specializations remain vital, focusing on emerging areas can unlock pathways to leadership and innovation within the industry.
Many emerging areas, initially niche, tend to become mainstream within three to five years, generating a significant number of job opportunities as adoption increases. Pursuing these cutting-edge specializations involves a balance of risk and reward. While some areas may evolve differently than expected, the potential for significant professional advancement and higher earning potential typically outweighs the initial uncertainty. Strategic skill development now can lead to a more resilient and rewarding career trajectory.
3D Print Post-Processing Specialist
This specialization focuses on the final finishing of orthotic devices created using advanced 3D printing technologies. As additive manufacturing becomes more prevalent for custom orthoses, technicians must adapt their grinding and finishing skills to new materials and complex geometries produced by these printers. This involves understanding material properties of various polymers and composites, and utilizing specialized tools for precise post-processing of printed parts, ensuring optimal fit and patient comfort.
Biomechanical Optimization Grinder
This area involves specializing in the precise finishing of orthotic devices designed for specific biomechanical corrections, often integrating sensor technologies. Technicians will work with orthoses that require intricate contouring to interact optimally with patient movement and data feedback. This demands a deeper understanding of biomechanics and how grinding techniques impact the functional performance of the device, ensuring it provides accurate support and alignment based on patient gait analysis or pressure mapping.
Sustainable Materials Finishing Technician
As sustainability becomes a critical concern, this specialization focuses on the finishing and repair of orthotic devices made from recycled, biodegradable, or sustainable composite materials. Technicians in this role will need to develop expertise in working with novel eco-friendly materials, understanding their unique grinding and finishing characteristics. This includes techniques for refurbishing and extending the lifespan of existing devices, contributing to a circular economy within orthotics.
Pediatric Orthotic Micro-Finishing Specialist
This specialization involves the advanced finishing of orthoses for pediatric patients, who often require extremely precise and lightweight devices due to their rapid growth and sensitive skin. Technicians will focus on achieving ultra-smooth surfaces and feather-light edges to prevent skin irritation and accommodate growth patterns. This demands exceptional attention to detail and a nuanced understanding of pediatric patient needs, ensuring maximum comfort and compliance.
Performance Sports Orthotic Finisher
This niche focuses on the meticulous finishing of orthotic devices for high-performance athletes, where minimal weight and maximum durability are paramount. Technicians will work with advanced composite materials and employ specialized grinding techniques to achieve ultra-lightweight yet robust devices. This area requires an understanding of sports biomechanics and material stress points, ensuring the orthosis withstands rigorous athletic activity while providing optimal support and enhancing performance.
Pros & Cons of Being an Orthotic Finish Grinding Technician
Making informed career choices requires understanding both the benefits and challenges of a profession. The experience of an Orthotic Finish Grinding Technician varies significantly based on the employer, the specific types of orthotics produced, and individual aptitudes. What one person views as a benefit, such as a hands-on, repetitive task, another might find monotonous. Career stages also influence perception; early career technicians might focus on skill acquisition, while senior technicians might value stability or mentorship opportunities. This assessment provides a realistic outlook on what to expect in this specialized fabrication role, helping individuals set appropriate expectations and determine if this path aligns with their personal values and lifestyle preferences.
Pros
- This role offers a tangible sense of accomplishment, as technicians directly contribute to creating custom orthotic devices that significantly improve patients' mobility and quality of life.
- The demand for skilled Orthotic Finish Grinding Technicians is consistent, as orthotic devices are essential for rehabilitation and support across various medical conditions, ensuring stable employment.
- Developing expertise in grinding and finishing techniques builds valuable manual dexterity and precision skills, which are highly transferable to other detailed fabrication or craft-based professions.
- Working in this niche field provides a stable work environment, often within a workshop or laboratory setting, with predictable hours and less patient-facing interaction compared to clinical roles.
- Entry into this career often requires vocational training or on-the-job experience rather than a lengthy university degree, making it accessible for individuals seeking a direct path into a skilled trade.
- Technicians gain in-depth knowledge of various materials used in orthotics, such as thermoplastics, carbon fiber, and foam, understanding their properties and how they behave during the finishing process.
- The work is hands-on and practical, appealing to individuals who enjoy working with their hands, operating specialized machinery, and seeing the physical results of their efforts.
Cons
- This role involves constant exposure to dust and fine particulate matter from grinding materials, requiring diligent use of personal protective equipment and potentially impacting respiratory health over time.
- The work is highly repetitive, involving the same motions for grinding and finishing numerous devices daily, which can lead to monotony and repetitive strain injuries if proper ergonomics are not maintained.
- Accuracy is paramount, as even minor errors in grinding can compromise the fit and function of an orthotic device, leading to increased pressure and stress to avoid mistakes.
- The job requires significant physical stamina, involving standing for extended periods, operating heavy machinery, and handling materials, which can be physically demanding over a full shift.
- Career advancement opportunities within this specific role are often limited; progression typically involves moving into supervisory roles, quality control, or transitioning to other areas of orthotics fabrication.
- Working with various materials like plastics, carbon fiber, and metals can expose technicians to odors and fumes, necessitating good ventilation and adherence to safety protocols to mitigate health risks.
- Pay scales for this specialized manual labor role can be modest compared to other healthcare-related positions, especially for entry-level technicians, though experience can lead to higher wages.
Frequently Asked Questions
Orthotic Finish Grinding Technicians face unique challenges in precision handcrafting and material science within a medical manufacturing setting. This section addresses common questions about entering this specialized role, from mastering intricate finishing techniques to understanding its impact on patient care and career progression.
What are the basic educational or experience requirements to become an Orthotic Finish Grinding Technician?
Entry into this role typically requires a high school diploma or GED. Many technicians learn on the job through apprenticeships or structured training programs offered by orthotic labs. Some vocational schools offer courses in prosthetics and orthotics technology, which can provide a strong foundation. Prior experience with detailed handwork, carving, or precision finishing is highly beneficial.
How long does it typically take to become fully competent in orthotic finish grinding?
Becoming proficient enough to work independently as an Orthotic Finish Grinding Technician usually takes 6 to 18 months of dedicated training. This timeline includes mastering various grinding tools, understanding different orthotic materials, and developing the fine motor skills and attention to detail required for precise finishing. Initial training often focuses on safety and basic techniques before advancing to complex shapes and patient-specific modifications.
What are the typical salary expectations for an Orthotic Finish Grinding Technician?
Starting salaries for Orthotic Finish Grinding Technicians can range from $30,000 to $45,000 annually, depending on location, employer, and prior experience. With several years of experience and demonstrated expertise, salaries can increase to $50,000 or more. Opportunities for overtime or specialized work may also boost earning potential. This role offers stable employment within a growing healthcare sector.
What is the typical work-life balance like, and are there any physical demands or hazards?
The work-life balance for an Orthotic Finish Grinding Technician is generally stable, with most positions being full-time during standard business hours. Overtime might be available or required during peak periods, but it is less common than in some other manufacturing roles. The work is physically demanding, requiring standing for long periods and repetitive motions, which impacts daily energy levels.
Is there a strong job market for Orthotic Finish Grinding Technicians, or is it a declining field?
The demand for Orthotic Finish Grinding Technicians is steady and growing, driven by an aging population and increased awareness of orthotic benefits. While automation impacts some manufacturing sectors, the precision and customization required for orthotic finishing often necessitate skilled human touch. Job security is relatively high due to the specialized nature of the work and the consistent need for custom medical devices.
What are the potential career advancement opportunities for an Orthotic Finish Grinding Technician?
Career growth paths for Orthotic Finish Grinding Technicians often involve specialization in particular types of orthotics, becoming a lead technician, or moving into quality control. Some technicians advance to supervisory roles within the lab or transition into roles requiring direct patient interaction, such as an Orthotic Fitter, after further certification. Continuous learning about new materials and technologies supports advancement.
Can Orthotic Finish Grinding Technicians work remotely, or is it primarily an on-site role?
Many Orthotic Finish Grinding Technician roles are based in manufacturing labs, requiring on-site presence due to specialized equipment and the hands-on nature of the work. Remote work is generally not feasible for the core finishing tasks. However, some administrative or design aspects might offer limited flexibility if a technician also takes on those responsibilities within a larger organization.
What are the biggest challenges or common difficulties in the day-to-day work of this role?
The most challenging aspects include maintaining extreme precision and consistency with hand tools, especially when working with diverse materials and complex anatomical shapes. Technicians must also manage dust and noise exposure from grinding processes, requiring strict adherence to safety protocols. Balancing speed with meticulous attention to detail to meet production deadlines without compromising quality is a constant challenge.
Related Careers
Explore similar roles that might align with your interests and skills:
Certified Orthotic Fitter
A growing field with similar skill requirements and career progression opportunities.
Explore career guideManufacturing Orthopedic Technologist
A growing field with similar skill requirements and career progression opportunities.
Explore career guideOrthotic Fabricator Technician
A growing field with similar skill requirements and career progression opportunities.
Explore career guideOrthotics Fitter
A growing field with similar skill requirements and career progression opportunities.
Explore career guideOrthotics Technician
A growing field with similar skill requirements and career progression opportunities.
Explore career guideAssess your Orthotic Finish Grinding Technician readiness
Understanding where you stand today is the first step toward your career goals. Our Career Coach helps identify skill gaps and create personalized plans.
Skills Gap Analysis
Get a detailed assessment of your current skills versus Orthotic Finish Grinding Technician requirements. Our AI Career Coach identifies specific areas for improvement with personalized recommendations.
See your skills gapCareer Readiness Assessment
Evaluate your overall readiness for Orthotic Finish Grinding Technician roles with our AI Career Coach. Receive personalized recommendations for education, projects, and experience to boost your competitiveness.
Assess your readinessSimple pricing, powerful features
Upgrade to Himalayas Plus and turbocharge your job search.
Himalayas
Himalayas Plus
Himalayas Max
Find your dream job
Sign up now and join over 100,000 remote workers who receive personalized job alerts, curated job matches, and more for free!
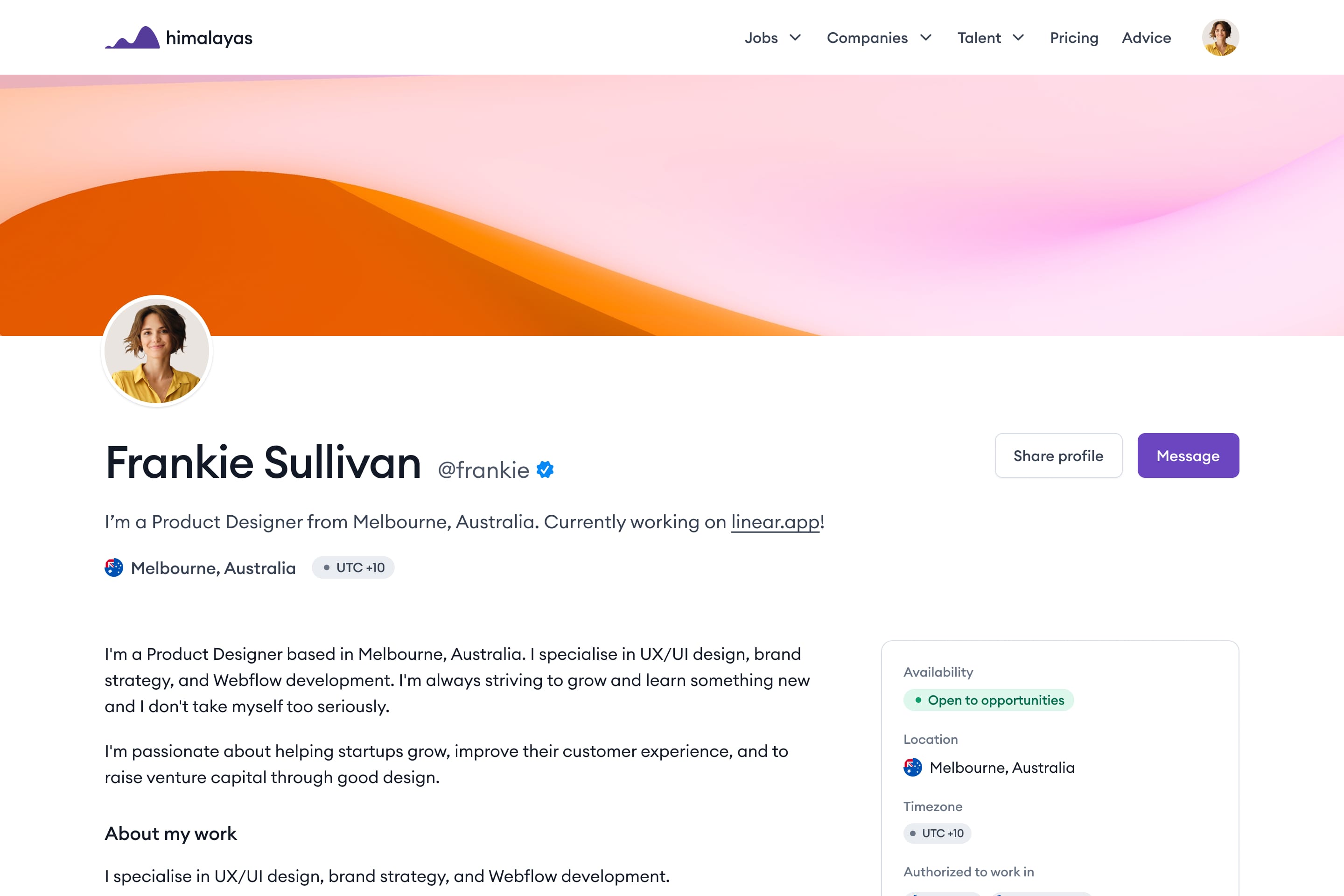