Complete Operations Technician Career Guide
Operations technicians are the backbone of modern industry, ensuring complex machinery and systems run smoothly and efficiently. They diagnose issues, perform maintenance, and optimize performance across critical infrastructure, preventing costly downtime and keeping essential services active. This hands-on role combines technical skill with problem-solving, offering stable career paths in vital sectors.
Key Facts & Statistics
Median Salary
$60,340 USD
(U.S. Bureau of Labor Statistics, May 2023)
Range: $40k - $90k+ USD (varies by experience, industry, and location)
Growth Outlook
1%
(little or no change) (U.S. Bureau of Labor Statistics, 2022-2032)
Annual Openings
≈170,000
openings annually (U.S. Bureau of Labor Statistics, 2022-2032)
Top Industries
Typical Education
High school diploma or equivalent, often with postsecondary vocational training, an associate's degree, or relevant military experience; certifications can enhance prospects.
What is an Operations Technician?
An Operations Technician is a skilled professional responsible for the day-to-day monitoring, maintenance, and troubleshooting of complex mechanical, electrical, and control systems within an industrial or technical facility. They ensure that equipment runs efficiently, reliably, and safely, playing a critical role in preventing downtime and optimizing performance. Their primary focus is on the operational continuity and immediate health of the systems.
This role differs significantly from an Industrial Electrician, who primarily focuses on electrical installations and repairs, or a Maintenance Mechanic, who concentrates on mechanical repairs. An Operations Technician possesses a broader understanding of integrated systems, combining elements of mechanical, electrical, and control systems to diagnose issues from a holistic operational perspective. They are often the first responders to system anomalies, identifying problems before they escalate and performing routine preventative care.
What does an Operations Technician do?
Key Responsibilities
- Conduct routine inspections of equipment and systems to identify potential malfunctions or wear, ensuring compliance with operational checklists.
- Perform preventative maintenance tasks on machinery, including lubrication, cleaning, and replacing minor components, to extend equipment lifespan.
- Respond to and troubleshoot operational alarms or system failures, diagnosing root causes and implementing immediate corrective actions.
- Calibrate and adjust instruments and controls to maintain optimal performance and accuracy within specified operational parameters.
- Document all maintenance activities, inspection findings, and operational data accurately in logbooks and digital systems.
- Collaborate with senior technicians and engineers to resolve complex technical issues and improve operational efficiency.
- Adhere strictly to safety protocols and environmental regulations during all operational and maintenance procedures.
Work Environment
An Operations Technician typically works in industrial settings such as manufacturing plants, power generation facilities, water treatment plants, or data centers. The environment can be dynamic, sometimes noisy, and may involve exposure to machinery, chemicals, or varying temperatures. They often work shifts, including nights, weekends, and holidays, to ensure continuous operation of systems. Collaboration occurs frequently with other technicians, engineers, and production staff, often requiring quick, coordinated responses to operational issues. The pace of work can range from routine inspections to urgent, high-pressure troubleshooting during outages.
Tools & Technologies
Operations Technicians regularly use a variety of specialized tools, including multimeters, oscilloscopes, and pressure gauges, for diagnostic and calibration tasks. They work with hand and power tools for maintenance and repair. Accessing and updating digital records often involves Computerized Maintenance Management Systems (CMMS) like SAP PM or Maximo, alongside SCADA (Supervisory Control and Data Acquisition) systems for monitoring industrial processes.
Depending on the industry, they might interact with Programmable Logic Controllers (PLCs), Distributed Control Systems (DCS), and various sensors. Basic office productivity software for reporting and communication is also common.
Operations Technician Skills & Qualifications
The Operations Technician role demands a blend of hands-on technical ability and meticulous attention to detail. This position often serves as the backbone of various industrial, manufacturing, or IT infrastructure environments, ensuring systems run efficiently and reliably. Qualification structures prioritize practical experience and specific technical certifications heavily, often valuing them equally or above traditional degrees, especially for entry to mid-level roles.
Requirements for an Operations Technician vary significantly based on the industry and the complexity of the systems managed. In manufacturing, precision machinery and safety protocols dominate the skill set. In IT operations, network infrastructure, server maintenance, and ticketing systems are key. Larger companies might have more specialized roles, requiring deeper expertise in one area, while smaller organizations often seek generalists capable of handling diverse tasks. Geographic location can also influence requirements, with highly industrialized regions often demanding specific industry certifications.
Formal education, such as an Associate's degree in a technical field, provides a strong foundation. However, vocational training, technical school programs, and targeted certifications are often direct pathways into this career. Many successful Operations Technicians gain their skills through apprenticeships or on-the-job training. The field evolves constantly with new technologies, so continuous learning and adaptability to emerging systems, automation tools, and data analytics capabilities are becoming increasingly critical for career advancement.
Education Requirements
Technical Skills
- Troubleshooting methodologies (e.g., 5 Whys, Ishikawa diagrams) for system diagnosis and root cause analysis
- Preventive maintenance procedures and scheduling for operational equipment and infrastructure
- Diagnostic tools and equipment operation (e.g., multimeters, oscilloscopes, network analyzers, specialized software)
- Basic electrical and mechanical repair principles (e.g., motor control, hydraulics, pneumatics)
- Computer hardware and software installation, configuration, and basic network connectivity troubleshooting
- Documentation and reporting using CMMS (Computerized Maintenance Management Systems) or ticketing systems
- Understanding of PLCs (Programmable Logic Controllers) or SCADA systems (Supervisory Control and Data Acquisition) for industrial roles
- Basic scripting or automation knowledge (e.g., PowerShell, Python) for IT operations roles
- Data analysis for performance monitoring and anomaly detection
- Quality control principles and standard operating procedure (SOP) adherence
- Safety protocols and compliance (e.g., Lockout/Tagout, confined space, hazardous material handling)
- Inventory management for spare parts and consumables
Soft Skills
- Problem-solving: Operations Technicians must quickly diagnose and resolve technical issues to minimize downtime and maintain operational efficiency.
- Attention to detail: Meticulousness is crucial for following complex procedures, performing precise measurements, and identifying subtle anomalies that could indicate larger problems.
- Adaptability: Systems and processes change frequently, requiring technicians to quickly learn new technologies and adjust to evolving operational demands.
- Team collaboration: Working effectively with other technicians, engineers, and management is essential for coordinated troubleshooting and project execution.
- Communication clarity: Clearly documenting issues, solutions, and operational statuses, as well as providing concise updates to colleagues and supervisors, is vital for smooth operations.
- Time management: Prioritizing tasks and managing workload efficiently ensures critical operations are maintained and deadlines are met, especially during incidents or peak periods.
- Safety consciousness: A strong commitment to adhering to safety protocols and procedures is paramount in environments involving machinery, electrical systems, or hazardous materials.
How to Become an Operations Technician
Breaking into an Operations Technician role offers multiple pathways, whether you are a complete beginner, a career changer, or transitioning from a related field. While a formal technical degree can accelerate entry, many individuals successfully enter through vocational training, apprenticeships, or by demonstrating practical mechanical and technical aptitude. The timeline for entry can range from 3-6 months for those with some prior technical exposure and a strong hands-on learning approach, to 1-2 years if starting from scratch and pursuing formal education or a structured apprenticeship program.
Entry strategies often vary by industry and company size; large manufacturing plants or utility companies might prefer candidates with certifications or associate degrees, while smaller firms might prioritize practical experience and a willingness to learn on the job. Geographic location also plays a role, with more opportunities in industrial or manufacturing hubs. It is a misconception that you need extensive prior experience to start; often, employers seek candidates with a strong work ethic, problem-solving skills, and a foundational understanding of safety protocols and basic machinery.
Networking within industrial or technical communities, attending local trade shows, and connecting with current operations technicians can provide invaluable insights and potential leads. Building a basic toolkit of hands-on skills through personal projects or volunteer work can also demonstrate your capabilities. The hiring landscape values adaptability and a proactive approach to learning new systems and technologies, making continuous skill development crucial for long-term success in this field.
Step 1
Step 2
Step 3
Step 4
Step 5
Step 6
Step 7
Education & Training Needed to Become an Operations Technician
Becoming an Operations Technician primarily involves practical skills and hands-on experience, often more so than theoretical knowledge gained from a traditional four-year degree. Many successful Operations Technicians begin with vocational training, associate's degrees, or specialized certifications. A two-year Associate of Applied Science (AAS) in Industrial Technology, Electronics Technology, or a related engineering technology field typically costs between $5,000 and $20,000 at a community college, providing a strong theoretical foundation coupled with practical labs. These programs usually take two years to complete.
Alternatively, vocational schools and technical institutes offer certificate programs ranging from 6 to 18 months, priced from $3,000 to $15,000. These focus intensely on specific skills like instrumentation, process control, or electrical systems. Employers highly value these certifications for entry-level roles, as they demonstrate direct readiness for the job. Self-study, while possible for foundational knowledge, rarely suffices on its own due to the hands-on nature of the work. It might involve online courses from platforms like Coursera or edX, costing hundreds to a few thousand dollars, and could take 6-12 months to cover essential topics.
The market perception favors candidates with demonstrable practical skills, often gained through internships or apprenticeships alongside formal education. While a bachelor's degree in engineering technology (4 years, $40,000-$100,000+) can open doors to supervisory or engineering roles, it is not a prerequisite for an Operations Technician position and may be considered overqualified for entry-level. Continuous learning, especially in new automation technologies and safety protocols, remains crucial throughout an Operations Technician's career. Industry-specific accreditations from organizations like ISA (International Society of Automation) or NCCER (National Center for Construction Education and Research) enhance credibility and career progression.
Operations Technician Salary & Outlook
Compensation for an Operations Technician varies significantly based on several factors, extending beyond just base salary. Geographic location plays a crucial role, with higher cost-of-living areas, particularly those with a dense industrial or manufacturing presence, often offering higher wages to offset living expenses. Market demand for specific technical skills within a region also drives earnings.
Years of experience dramatically impact earning potential. Entry-level roles command lower salaries, while those with specialized certifications, advanced troubleshooting skills, or experience with complex machinery see substantial increases. Total compensation packages frequently include performance bonuses, overtime pay for shift work, and comprehensive benefits such as health insurance, retirement contributions (401k matching), and paid time off. Some companies also offer allowances for professional development or tool stipends.
Industry-specific trends influence salary growth; for instance, highly automated or precision manufacturing sectors may offer higher pay for their technicians. Negotiating salary involves highlighting specific technical proficiencies, safety records, and demonstrated problem-solving abilities. Remote work is generally not applicable to this hands-on role; however, some supervisory or planning functions might offer hybrid options. Salaries provided are in USD, reflecting the U.S. market, though international rates will differ based on local economic conditions and industry standards.
Salary by Experience Level
Level | US Median | US Average |
---|---|---|
Junior Operations Technician | $48k USD | $52k USD |
Operations Technician | $65k USD | $68k USD |
Senior Operations Technician | $82k USD | $85k USD |
Lead Operations Technician | $95k USD | $98k USD |
Operations Supervisor | $110k USD | $115k USD |
Market Commentary
The job market for Operations Technicians shows steady demand, driven by the ongoing need to maintain and optimize industrial processes across various sectors. The Bureau of Labor Statistics projects a moderate growth outlook for related occupations, indicating consistent opportunities. Automation and AI are transforming the role, shifting focus from manual tasks to monitoring automated systems, data analysis, and advanced troubleshooting. This evolution creates a need for technicians with strong analytical and digital literacy skills.
Emerging opportunities often lie in specialized areas such as robotics maintenance, industrial IoT (IIoT) integration, and sustainable energy operations. The demand for skilled technicians often outstrips supply, particularly for those proficient with modern, complex equipment and software. This imbalance can lead to competitive salaries and robust job security. While some manufacturing sectors can be cyclical, the fundamental need for operational efficiency and equipment uptime makes this profession relatively recession-resistant.
Geographic hotspots for Operations Technicians include regions with strong manufacturing bases, large utility infrastructure, or significant energy production facilities. Continuous learning in areas like predictive maintenance, cybersecurity for operational technology, and advanced control systems is essential for career longevity and upward mobility. Companies increasingly seek technicians who can adapt to new technologies and contribute to process improvement initiatives.
Operations Technician Career Path
Career progression for an Operations Technician unfolds through increasing technical mastery, problem-solving autonomy, and leadership responsibilities. Professionals typically begin in hands-on, supervised roles, gradually taking on more complex systems and independent troubleshooting. Advancement can follow either an individual contributor (IC) track, focusing on deep technical specialization, or a management/leadership track, which involves overseeing teams and operational processes.
Advancement speed depends on performance, the complexity of systems operated, and continuous skill acquisition, particularly in automation and data analysis. Company size and industry also play a role; larger corporations may offer more structured paths and specialized roles, while smaller firms might provide broader exposure. Lateral moves into related fields like maintenance, quality control, or process improvement are common for technicians seeking diverse experiences.
Networking within the industry and continuous learning through certifications in specific operational technologies or safety protocols significantly boost career prospects. Mentorship from experienced technicians and supervisors helps new professionals navigate challenges and accelerate their development. Milestones often include successful leadership of critical system deployments or significant improvements in operational efficiency.
Junior Operations Technician
0-2 yearsKey Focus Areas
Operations Technician
2-5 yearsKey Focus Areas
Senior Operations Technician
5-8 yearsKey Focus Areas
Lead Operations Technician
8-12 yearsKey Focus Areas
Operations Supervisor
12+ yearsKey Focus Areas
Junior Operations Technician
0-2 yearsPerform routine operational tasks under direct supervision, including equipment checks, data recording, and basic maintenance. Follow established procedures for system startups, shutdowns, and adjustments. Report any anomalies or issues promptly to senior staff. Impact is primarily on task completion and adherence to safety guidelines.
Key Focus Areas
Develop foundational understanding of operational procedures, safety protocols, and equipment. Focus on active listening, following instructions precisely, and basic troubleshooting. Begin learning about system monitoring tools and data logging. Seek mentorship to understand the broader operational context.
Operations Technician
2-5 yearsOperate and monitor complex systems with moderate supervision, performing routine and non-routine adjustments. Troubleshoot and resolve common operational faults independently, escalating complex issues. Contribute to process improvement discussions and ensure compliance with operational standards. Responsible for maintaining system uptime and efficiency.
Key Focus Areas
Enhance diagnostic and problem-solving skills for common operational issues. Gain proficiency in using advanced monitoring systems and interpreting performance data. Develop effective communication with cross-functional teams, including engineering and maintenance. Explore specialized training in specific operational technologies.
Senior Operations Technician
5-8 yearsIndependently manage the operation of critical systems, making real-time adjustments and optimizing performance. Lead troubleshooting efforts for complex issues, often cross-referencing multiple data sources. Provide guidance and training to junior technicians. Play a key role in implementing new operational procedures and technology upgrades. Impact directly on system reliability and output.
Key Focus Areas
Master advanced troubleshooting techniques and root cause analysis for system failures. Develop strong analytical skills to optimize operational performance and identify inefficiencies. Begin mentoring junior technicians and contributing to training material development. Pursue certifications in relevant industry-specific technologies or lean methodologies.
Lead Operations Technician
8-12 yearsAct as a technical lead for specific operational areas or shifts, guiding a team of technicians through daily tasks and complex problem-solving. Coordinate with other departments to ensure seamless operational flow. Develop and implement new operational procedures and best practices. Lead incident response and post-mortem analysis for significant events. Accountable for team performance and operational continuity.
Key Focus Areas
Develop strong leadership and communication skills, focusing on guiding technical teams through complex operational challenges. Master project management principles for operational initiatives. Cultivate a deep understanding of business objectives and how operational efficiency contributes to them. Explore advanced training in automation, data analytics, or process optimization.
Operations Supervisor
12+ yearsManage and oversee a team of Operations Technicians, ensuring operational targets are met safely and efficiently. Responsible for scheduling, performance reviews, and professional development of team members. Develop and implement departmental policies and procedures. Collaborate with senior management on strategic operational planning and budget management. Direct impact on team productivity and overall operational excellence.
Key Focus Areas
Focus on strategic planning, resource allocation, and team development. Enhance leadership skills, including conflict resolution, performance management, and motivational techniques. Develop a comprehensive understanding of operational budgets, regulatory compliance, and long-term strategic goals. Network with industry peers to adopt best practices and innovations.
Job Application Toolkit
Ace your application with our purpose-built resources:
Operations Technician Resume Examples
Proven layouts and keywords hiring managers scan for.
View examplesOperations Technician Cover Letter Examples
Personalizable templates that showcase your impact.
View examplesTop Operations Technician Interview Questions
Practice with the questions asked most often.
View examplesOperations Technician Job Description Template
Ready-to-use JD for recruiters and hiring teams.
View examplesGlobal Operations Technician Opportunities
Operations Technicians maintain and troubleshoot complex industrial equipment and systems globally. This role is crucial across diverse sectors like manufacturing, energy, and IT infrastructure. Global demand remains steady, particularly in industrialized nations and emerging markets. International opportunities exist due to the universal need for skilled technical support. Cultural nuances affect workplace safety standards and communication protocols. Certifications like CompTIA A+ or industry-specific qualifications enhance global mobility.
Global Salaries
Operations Technician salaries vary significantly by region and industry focus. In North America, particularly the U.S. and Canada, annual salaries range from $50,000 to $80,000 USD, reflecting high demand in tech and manufacturing. European countries like Germany and the UK offer €35,000 to €60,000 (approximately $38,000 to $65,000 USD), with robust social benefits and healthcare reducing out-of-pocket expenses. Nordic countries often feature higher gross salaries but also higher tax rates.
Asia-Pacific markets, such as Australia and Singapore, see salaries from AUD 60,000 to AUD 90,000 (around $40,000 to $60,000 USD). These regions often have lower income taxes but higher living costs in major cities. Latin American countries, including Mexico and Brazil, typically offer $15,000 to $30,000 USD annually, but purchasing power can be surprisingly strong due to lower living expenses. Middle Eastern nations, especially in oil and gas, might offer tax-free salaries from $45,000 to $75,000 USD, often including housing allowances.
Compensation structures differ, with North America often emphasizing base pay plus bonuses, while Europe provides more comprehensive social security and longer vacation periods. Experience and specialized certifications directly impact earning potential across all regions. Understanding local tax implications and cost of living is crucial for comparing offers effectively.
Remote Work
International remote work for Operations Technicians is limited due to the hands-on nature of the role. Most tasks require physical presence to maintain, troubleshoot, or repair equipment. However, some aspects, like remote monitoring, diagnostics, and software updates, can be performed remotely. Companies with distributed operational centers might employ technicians for centralized remote support. This often involves managing systems across different time zones.
Digital nomad opportunities for Operations Technicians are rare; the role typically necessitates fixed physical locations. Legal and tax implications for the remote components of the job, such as software support, still apply. Employers hiring internationally for remote roles often have specific policies regarding equipment provision and internet requirements. Salary expectations for remote support might be lower than on-site roles, reflecting less travel or physical demand. Platforms for global remote IT support sometimes list relevant positions.
Visa & Immigration
Skilled worker visas are the most common pathway for Operations Technicians seeking international roles. Countries like Canada (Express Entry), Australia (Skilled Nominated Visa), and Germany (EU Blue Card) often list this profession on their in-demand occupation lists. Requirements typically include relevant vocational qualifications or a diploma, several years of experience, and a job offer from a local employer. Education credential recognition is vital; applicants often need their qualifications assessed by a designated authority in the destination country.
The typical visa application process involves submitting an online application, providing documentation, and attending an interview. Processing times vary from a few months to over a year. Language proficiency tests, such as IELTS for English-speaking countries or Goethe-Zertifikat for Germany, are frequently required. Some countries offer pathways to permanent residency after a few years of skilled work. Family visas are usually available for spouses and dependents. Intra-company transfers are also possible for technicians working for multinational corporations.
2025 Market Reality for Operations Technicians
Understanding current market conditions is crucial for Operations Technicians. The field has evolved significantly from 2023 to 2025, influenced by post-pandemic shifts and the accelerating AI revolution. Broader economic factors, such as inflation and supply chain stability, directly impact investment in operational infrastructure and, consequently, technician demand. Market realities vary considerably by experience level, geographic region, and the size of the operating company, from large-scale industrial complexes to smaller specialized facilities.
The following analysis provides an honest assessment of the current landscape for Operations Technicians, helping job seekers set realistic expectations and craft effective career strategies. It addresses how technological advancements, particularly in automation and AI, reshape job responsibilities and skill requirements.
Current Challenges
Significant challenges for Operations Technicians include increased competition, particularly for entry-level roles, as automation streamlines some tasks. Economic uncertainty in manufacturing and logistics sectors can lead to hiring freezes or reduced expansion. A notable skill gap exists where employers increasingly seek technicians proficient in AI-driven predictive maintenance and advanced data analytics, which many current candidates lack.
Growth Opportunities
Despite market challenges, strong demand persists for Operations Technicians in specialized areas. Data centers, renewable energy facilities (solar farms, wind turbines), and advanced manufacturing plants using robotics and AI-driven processes actively seek skilled technicians. These sectors prioritize uptime and efficiency, making the role indispensable.
Emerging opportunities exist in roles focused on 'smart' operational systems, where technicians manage IoT sensors, analyze performance data, and implement predictive maintenance routines. Professionals who can bridge the gap between traditional mechanical/electrical skills and IT/OT (Operational Technology) convergence are highly valued. Underserved markets often include rural areas with new energy infrastructure projects or regions experiencing industrial revitalization.
Acquiring certifications in industrial automation, network protocols, or specific vendor equipment for AI-integrated systems provides a significant competitive advantage. Even in a market correction, companies must maintain their core operations, ensuring a baseline demand for skilled technicians. Strategic career moves involve targeting industries investing heavily in automation and digital transformation. Investing in training for AI-powered diagnostic tools or industrial cybersecurity also positions technicians for long-term growth.
Current Market Trends
The market for Operations Technicians in 2025 shows a mixed but generally stable demand. While core roles remain essential for maintaining infrastructure and production lines, recent industry shifts, particularly in manufacturing and data centers, influence hiring patterns. The integration of advanced automation and AI into operational workflows means employers increasingly seek technicians capable of monitoring and troubleshooting complex, integrated systems rather than just mechanical components.
Economic conditions, including fluctuating energy prices and supply chain adjustments, impact capital expenditure on new facilities, directly affecting the creation of new technician roles. Conversely, the push for efficiency and uptime in existing operations sustains demand for skilled technicians. Generative AI assists in diagnostics and predictive maintenance scheduling, reducing the need for purely reactive, manual intervention. This shifts the technician's role toward oversight and complex problem-solving.
Employer requirements now emphasize digital literacy, data interpretation, and proficiency with remote monitoring tools, alongside traditional mechanical and electrical skills. Companies are less interested in technicians who only perform routine maintenance; they want individuals who can optimize system performance through data insights. Salary trends for experienced Operations Technicians are showing modest growth, especially for those with specialized IT/OT convergence skills, while entry-level salaries remain competitive. Geographic variations are pronounced, with stronger markets in regions with significant data center expansion, advanced manufacturing hubs, or critical infrastructure projects. Remote work is rarely an option for this hands-on role, anchoring opportunities to physical locations. Some cyclical hiring patterns align with new facility commissioning or major upgrade cycles within industrial sectors.
Emerging Specializations
The operational landscape for technicians is rapidly evolving, driven by advancements in automation, data analytics, and sustainable practices. These technological shifts are not merely optimizing existing processes; they are fundamentally reshaping the skills required and creating entirely new specialization opportunities. Understanding these emerging areas allows operations technicians to proactively position themselves for future career growth and enhanced earning potential.
Early adoption and specialization in these cutting-edge fields are crucial for career advancement from 2025 onwards. Professionals who develop expertise in next-generation operational methodologies often command premium compensation due to their specialized knowledge and the high demand for these skills. While established specializations remain relevant, focusing on emerging areas can provide a significant competitive edge and open doors to leadership roles in innovative operational environments.
Many emerging areas, particularly those involving advanced robotics, predictive maintenance, or circular economy principles, are on the cusp of becoming mainstream. They are moving beyond pilot programs into widespread industrial application, which will create a significant number of job opportunities in the coming years. Pursuing these cutting-edge specializations involves a balance of risk and reward. While they require investment in new learning, the potential for accelerated career progression and impact within an organization is substantial.
Robotics and Automation Technician
This specialization focuses on managing, maintaining, and optimizing robotic systems and automated guided vehicles (AGVs) within manufacturing and logistics operations. As companies increasingly integrate robotics for efficiency and safety, operations technicians with expertise in robot programming, troubleshooting, and preventive maintenance become essential. This role ensures the seamless integration of automated solutions into existing workflows, minimizing downtime and maximizing output.
Predictive Maintenance Specialist
This area involves leveraging data from sensors and operational systems to predict equipment failures and optimize maintenance schedules. Operations technicians in this field utilize data analytics tools and machine learning outputs to identify anomalies, diagnose potential issues before they escalate, and implement proactive maintenance strategies. This shift from reactive to predictive maintenance significantly reduces operational costs and improves system reliability.
OT Cybersecurity Technician
This specialization focuses on ensuring the operational efficiency and security of industrial control systems and operational technology (OT) networks. Operations technicians are critical in implementing cybersecurity protocols, monitoring for threats, and responding to incidents that could disrupt production or compromise data integrity. They bridge the gap between IT security practices and the unique vulnerabilities of industrial environments.
Sustainable Operations Technician
This emerging role centers on implementing and managing sustainable operational practices, including waste reduction, energy efficiency, and resource optimization within industrial processes. Operations technicians contribute to achieving environmental compliance and corporate sustainability goals by optimizing equipment for lower energy consumption, managing recycling programs, and identifying opportunities for circular economy initiatives in production.
Additive Manufacturing Operations Technician
This specialization involves the hands-on management and optimization of additive manufacturing (3D printing) processes for industrial production. Operations technicians are responsible for preparing print jobs, monitoring print quality, performing post-processing, and maintaining the specialized equipment. They ensure the efficient and reliable production of parts using various additive manufacturing technologies, from prototyping to end-use component fabrication.
Pros & Cons of Being an Operations Technician
Making a career choice requires understanding both the benefits and the challenges. Every profession, including an Operations Technician, offers a unique set of experiences. These can vary significantly based on the company culture, the specific industry sector, the level of specialization, and individual preferences. What one person views as a pro, another might see as a con. For instance, the structured routine in some roles might be a comfort for one person but a source of boredom for another. Furthermore, the advantages and challenges can evolve as you progress from an early career to mid-career or senior levels. This assessment provides an honest, balanced perspective to help you set realistic expectations for a career as an Operations Technician.
Pros
- Operations technicians are consistently in demand across various industries, including manufacturing, energy, and utilities, providing strong job security.
- Entry into this field often requires an associate's degree or vocational training, making it accessible without a four-year university degree, and offering a quicker path to employment.
- The role provides hands-on problem-solving opportunities, as technicians regularly diagnose and repair equipment, offering a sense of accomplishment in keeping systems running.
- Operations technicians typically receive competitive hourly wages, and overtime opportunities are often available, significantly boosting earning potential.
- Many companies provide on-the-job training and opportunities for continuous learning, allowing technicians to develop specialized skills and adapt to new technologies.
- The work environment often fosters a strong sense of team camaraderie, as technicians frequently collaborate with colleagues to troubleshoot issues and maintain operational efficiency.
- The job offers tangible results; seeing equipment run smoothly and production targets met provides a clear sense of contribution and impact on the organization's success.
Cons
- Operations technicians often work shifts, including nights, weekends, and holidays, which can significantly disrupt personal life and social schedules.
- Many operations technician roles involve repetitive tasks, which can lead to monotony and a lack of intellectual stimulation for those who prefer dynamic, varied work.
- The work environment can be physically demanding, requiring standing for long periods, lifting heavy equipment, and working in noisy or temperature-controlled industrial settings.
- Career advancement opportunities may be limited without further education or specialized certifications, often leading to a plateau in responsibilities and salary.
- Exposure to hazardous materials, loud machinery, and high-voltage equipment is common, requiring strict adherence to safety protocols and carrying inherent risks.
- Troubleshooting complex system failures under pressure can be highly stressful, especially when production or critical services depend on quick resolution.
- The technical skills required are often specific to the machinery or processes of a particular facility, which might limit direct transferability to other industries without retraining, making job transitions potentially challenging if the industry declines or changes.
Frequently Asked Questions
Operations Technicians face unique challenges balancing technical maintenance with process optimization in various industrial settings. This section addresses common questions about entering this hands-on role, from required certifications and shift work realities to career progression and job stability in critical infrastructure.
What are the typical educational and certification requirements to become an Operations Technician?
Entry-level Operations Technician roles typically require a high school diploma or GED, often combined with vocational training or an Associate's degree in a relevant field like industrial technology, electronics, or process operations. Employers also value certifications in areas such as OSHA safety, hazmat, or specific equipment operation. Demonstrating mechanical aptitude and problem-solving skills is crucial.
How long does it take to become a qualified Operations Technician, especially if I'm starting from scratch?
The timeline to become job-ready as an Operations Technician varies. If you pursue an Associate's degree, it usually takes two years. Vocational programs or technical certifications can range from a few months to a year. Many companies also offer apprenticeships or on-the-job training programs, which provide a direct path into the role over 1-2 years while gaining practical experience.
What kind of work schedule and hours can I expect as an Operations Technician, and how does it affect work-life balance?
Operations Technicians often work rotating shifts, including nights, weekends, and holidays, particularly in 24/7 industrial environments. This schedule can impact work-life balance, requiring careful planning for personal life. While some roles offer standard daytime hours, be prepared for the possibility of non-traditional shifts and overtime, especially during equipment breakdowns or critical operations.
What are the typical salary expectations for an Operations Technician, both entry-level and experienced?
The salary for an Operations Technician varies significantly based on industry, location, experience, and specific responsibilities. Entry-level positions might range from $40,000 to $55,000 annually. Experienced technicians, especially those in specialized or high-demand industries like oil and gas or advanced manufacturing, can earn $60,000 to $85,000 or more, often with opportunities for overtime pay.
Is the role of an Operations Technician stable, and what is the job market outlook for this career?
The job outlook for Operations Technicians is generally stable, as these roles are essential for maintaining critical infrastructure and production across various industries. Demand remains consistent in sectors like utilities, manufacturing, and chemical processing. Automation may change some tasks, but the need for skilled technicians to oversee, maintain, and troubleshoot complex systems will likely persist, adapting to new technologies.
What are the potential career advancement opportunities for an Operations Technician?
Career growth for Operations Technicians can lead to several advanced roles. Many progress to Senior Technician, Lead Technician, or Supervisor positions, taking on more responsibility for teams and complex projects. Further development might include specializing in specific equipment or processes, moving into maintenance management, or even transitioning into engineering or safety roles with additional education and experience. Continuous learning and certifications are key for advancement.
What are the common safety concerns and physical demands associated with this job?
Working as an Operations Technician often involves exposure to various industrial hazards, including heavy machinery, electrical systems, chemicals, and elevated noise levels. Safety protocols are paramount, and technicians receive extensive training on personal protective equipment (PPE) and emergency procedures. The physical demands can also be significant, requiring lifting, climbing, and working in confined spaces or extreme temperatures.
Can Operations Technicians work remotely, or is this primarily an on-site role?
While some administrative or planning aspects of an Operations Technician role might be done remotely, the core responsibilities involve hands-on work with equipment and processes on-site. Therefore, the vast majority of Operations Technician positions require physical presence at a plant, facility, or field location. Fully remote work is generally not feasible for this hands-on career.
Related Careers
Explore similar roles that might align with your interests and skills:
Field Operator
A growing field with similar skill requirements and career progression opportunities.
Explore career guideOperation Engineer
A growing field with similar skill requirements and career progression opportunities.
Explore career guideOperations Engineer
A growing field with similar skill requirements and career progression opportunities.
Explore career guideOperator
A growing field with similar skill requirements and career progression opportunities.
Explore career guideProcess Technician
A growing field with similar skill requirements and career progression opportunities.
Explore career guideAssess your Operations Technician readiness
Understanding where you stand today is the first step toward your career goals. Our Career Coach helps identify skill gaps and create personalized plans.
Skills Gap Analysis
Get a detailed assessment of your current skills versus Operations Technician requirements. Our AI Career Coach identifies specific areas for improvement with personalized recommendations.
See your skills gapCareer Readiness Assessment
Evaluate your overall readiness for Operations Technician roles with our AI Career Coach. Receive personalized recommendations for education, projects, and experience to boost your competitiveness.
Assess your readinessSimple pricing, powerful features
Upgrade to Himalayas Plus and turbocharge your job search.
Himalayas
Himalayas Plus
Himalayas Max
Find your dream job
Sign up now and join over 100,000 remote workers who receive personalized job alerts, curated job matches, and more for free!
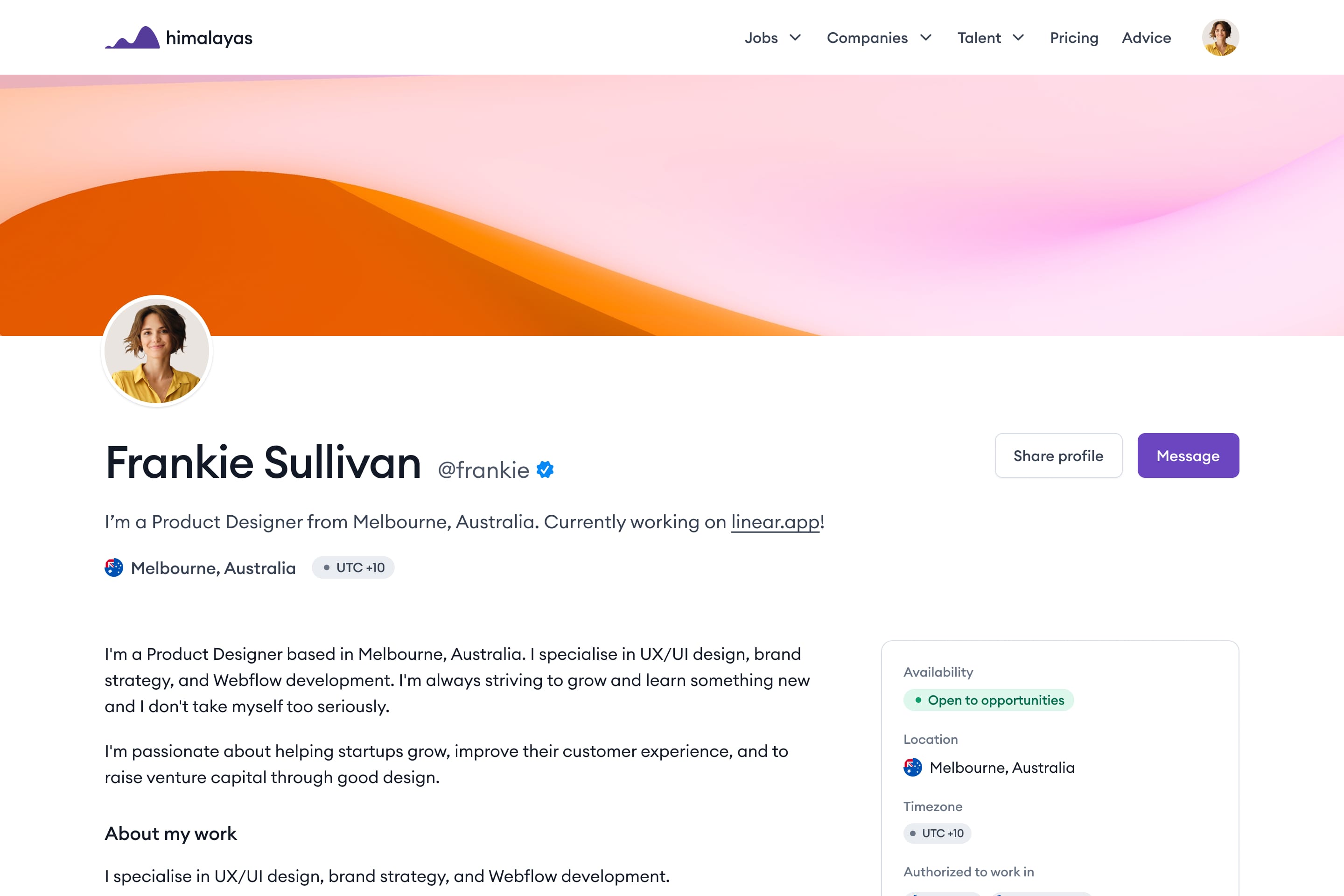