Complete Machined Parts Quality Inspector Career Guide
Machined parts quality inspectors are the unsung heroes of precision manufacturing, ensuring every component meets exact specifications before it reaches the customer or moves to the next stage of assembly. They use advanced tools and keen eyes to detect flaws, preventing costly recalls and ensuring product reliability in industries from aerospace to medical devices. This vital role demands meticulous attention to detail and offers a stable path for those who value precision and problem-solving.
Key Facts & Statistics
Median Salary
$47,200 USD
Range: $30k - $70k+ USD
Growth Outlook
2%
slower than average
Annual Openings
≈30k
openings annually
Top Industries
Typical Education
High school diploma or equivalent; some positions prefer postsecondary certificate in quality assurance or related field. On-the-job training is common.
What is a Machined Parts Quality Inspector?
A Machined Parts Quality Inspector is a specialized professional responsible for ensuring that manufactured components, produced through machining processes like milling, turning, and grinding, meet precise engineering specifications and quality standards. This role involves meticulously examining parts for dimensional accuracy, material integrity, and surface finish, acting as a critical gatekeeper in the production lifecycle.
Unlike a general quality control inspector who might oversee various products, a Machined Parts Quality Inspector possesses specific expertise in interpreting complex mechanical drawings, understanding Geometric Dimensioning and Tolerancing (GD&T), and operating advanced metrology equipment. Their primary purpose is to prevent defective parts from advancing to assembly or reaching customers, thereby upholding product reliability, reducing waste, and safeguarding a company's reputation for quality craftsmanship.
What does a Machined Parts Quality Inspector do?
Key Responsibilities
- Conduct thorough visual inspections of machined components to identify surface defects, burrs, and inconsistencies that do not meet specifications.
- Utilize precision measuring instruments such as calipers, micrometers, height gauges, and CMM machines to verify critical dimensions and tolerances.
- Interpret complex engineering drawings, blueprints, and CAD models to ensure parts conform to specified geometric dimensioning and tolerancing (GD&T).
- Document inspection results accurately, including non-conformance reports, and maintain detailed records for traceability and quality assurance.
- Collaborate with machinists, engineers, and production teams to address quality issues, provide feedback on manufacturing processes, and implement corrective actions.
- Perform first-article inspections (FAI) on new or revised parts to validate initial production runs against design requirements.
- Calibrate and maintain inspection equipment regularly to ensure accuracy and reliability of measurements, adhering to calibration schedules and procedures.
Work Environment
Machined Parts Quality Inspectors typically work in manufacturing facilities, machine shops, or dedicated quality control laboratories. The environment can be dynamic, often involving standing for extended periods and moving between inspection stations. While the work is precise, it can be noisy due to nearby machinery.
Collaboration is constant, as inspectors interact daily with machinists, production managers, and engineers to discuss part quality and process improvements. The pace is often steady but can become fast-paced when addressing critical production deadlines or complex non-conformances. Most roles involve standard day shifts, though some facilities operate 24/7, requiring rotating shifts. Remote work is generally not an option due to the hands-on nature of the inspections.
Tools & Technologies
Machined Parts Quality Inspectors primarily use a range of precision measuring tools, including digital and dial calipers, micrometers (inside, outside, depth), bore gauges, and height gauges. They frequently operate sophisticated equipment like Coordinate Measuring Machines (CMMs) for complex geometries and optical comparators for detailed profile analysis. Surface roughness testers and hardness testers are also common for material property verification.
Beyond physical tools, inspectors interpret engineering drawings, blueprints, and 3D CAD models (e.g., SolidWorks, AutoCAD) to understand design specifications and GD&T callouts. They use enterprise resource planning (ERP) systems or dedicated quality management software for data entry, non-conformance reporting, and tracking inspection results. Proficiency with basic office software for documentation is also essential.
Machined Parts Quality Inspector Skills & Qualifications
A Machined Parts Quality Inspector plays a critical role in ensuring that manufactured components meet precise specifications, blueprints, and quality standards. Qualification requirements in this field are highly dependent on the complexity of the parts, the industry served (e.g., aerospace, automotive, medical devices), and the production volume. Companies producing highly critical components, such as those for aircraft or medical implants, demand more rigorous qualifications, often including specific certifications and extensive experience.
For entry-level positions, employers often prioritize practical experience with measurement tools and a foundational understanding of manufacturing processes over a formal degree. However, as one progresses to senior or lead inspector roles, a deeper understanding of statistical process control, metrology, and quality management systems becomes essential. Certifications from organizations like the American Society for Quality (ASQ) significantly enhance a candidate's marketability, often outweighing a general college degree in non-technical fields.
The skill landscape for quality inspectors is evolving with the increased adoption of automated inspection systems and digital metrology. While traditional manual inspection skills remain crucial, proficiency with Coordinate Measuring Machines (CMMs), optical comparators, and statistical software is increasingly becoming a must-have. Prioritizing hands-on experience with diverse measurement equipment and continuous learning in advanced metrology techniques provides a strong competitive edge in this career.
Education Requirements
Technical Skills
- Blueprint Reading and Geometric Dimensioning & Tolerancing (GD&T) interpretation
- Precision Measurement Tools (calipers, micrometers, height gauges, bore gauges)
- Coordinate Measuring Machine (CMM) operation and programming (e.g., PC-DMIS, Calypso)
- Optical Comparator and Vision System operation
- Statistical Process Control (SPC) charting and analysis
- First Article Inspection (FAI) and In-Process Inspection procedures
- Non-Destructive Testing (NDT) methods (e.g., visual, dye penetrant, magnetic particle) as applicable
- Material properties and metallurgy fundamentals (e.g., hardness testing, material identification)
- Calibration procedures and equipment maintenance
- Quality Management Systems (e.g., ISO 9001, AS9100, IATF 16949) understanding
- Metrology software and data analysis tools (e.g., Minitab, Excel for data trending)
- Root Cause Analysis and Corrective/Preventive Actions (CAPA)
Soft Skills
- Attention to Detail: Critical for identifying minute defects and ensuring parts meet exact specifications.
- Problem-Solving: Essential for investigating root causes of non-conformances and suggesting corrective actions.
- Communication Skills: Necessary for clearly documenting inspection results, interacting with machinists, and relaying issues to engineering teams.
- Integrity and Objectivity: Crucial for providing unbiased inspection results and upholding quality standards without compromise.
- Organizational Skills: Important for managing inspection documentation, prioritizing tasks, and maintaining a clean work environment.
- Adaptability: Valuable in adjusting to new part designs, evolving inspection methods, and different production challenges.
- Time Management: Key for efficiently processing parts and meeting production schedules while maintaining accuracy.
How to Become a Machined Parts Quality Inspector
Entering the Machined Parts Quality Inspector field offers multiple pathways, whether you are a complete beginner, a career changer, or transitioning from a related manufacturing role. Traditional routes often involve vocational training or an associate's degree in a relevant field like Quality Assurance or Mechanical Engineering Technology. However, many successful inspectors begin their careers through apprenticeships or entry-level roles in manufacturing, gaining hands-on experience before specializing in quality control.
The timeline for entry varies significantly based on your starting point. A dedicated vocational program might prepare you in 6-12 months, while an associate's degree typically takes two years. If you start in an entry-level production role, gaining the necessary experience for an inspector position could take 1-3 years. Geographic location also plays a role; areas with a strong manufacturing base, such as the Midwest or parts of the Southeast in the U.S., often have more opportunities and varied entry points compared to regions with less industrial activity.
Misconceptions often include believing that only those with engineering degrees can succeed or that the job is purely repetitive. In reality, attention to detail, problem-solving skills, and a strong understanding of manufacturing processes are paramount. Companies, from small machine shops to large aerospace manufacturers, prioritize practical skills and a commitment to precision. Networking within local manufacturing communities and seeking mentorship from experienced inspectors can significantly accelerate your entry and provide invaluable insights into specific industry demands.
Step 1
Step 2
Step 3
Step 4
Step 5
Step 6
Education & Training Needed to Become a Machined Parts Quality Inspector
A Machined Parts Quality Inspector ensures precision and adherence to specifications for manufactured components. The educational landscape for this role includes a mix of formal and vocational training. While a four-year engineering degree is rarely necessary, a two-year associate's degree in Quality Assurance, Manufacturing Technology, or a related field can provide a strong foundation, typically costing between $8,000 and $25,000 and taking two years. These programs offer theoretical knowledge in metrology, statistical process control, and blueprint reading.
Alternatively, vocational programs and technical certifications offer more focused, hands-on training. These can range from 12-week intensive courses to 12-month certificate programs, with costs typically between $3,000 and $15,000. Employers highly value practical experience and industry-recognized certifications, such as those from the American Society for Quality (ASQ). Self-study combined with on-the-job training is also a viable path, though it may take 6 to 18 months to gain foundational skills and requires discipline to master complex measurement techniques and quality standards.
The market perception of credentials varies; while a degree can open doors to supervisory roles, certifications often prove an inspector's direct competence in specific tools and methodologies. Continuous learning is vital in this field, particularly with advancements in inspection technology like CMMs (Coordinate Measuring Machines) and laser scanners. Employers prioritize a blend of theoretical understanding and practical application. Educational needs also vary by the complexity of parts and industry, with aerospace or medical device manufacturing often requiring more stringent qualifications. Investing in specialized training for advanced measurement equipment can significantly enhance career prospects and earning potential.
Machined Parts Quality Inspector Salary & Outlook
Compensation for a Machined Parts Quality Inspector varies significantly based on several factors. Geographic location plays a crucial role, as areas with high manufacturing activity and a higher cost of living, such as the Northeast or parts of the Midwest, typically offer better salaries. Conversely, regions with lower demand or cost of living may see lower pay.
Years of experience and specialized skills, particularly in precision measurement, GD&T (Geometric Dimensioning and Tolerancing), and CMM (Coordinate Measuring Machine) operation, directly correlate with earning potential. Inspectors with certifications in quality management or specific inspection techniques often command premium compensation.
Total compensation extends beyond base salary to include performance bonuses, overtime pay, and comprehensive benefits packages. These often encompass health insurance, retirement contributions like 401(k) plans, and allowances for professional development or certification renewals. Larger manufacturing firms or those in highly regulated industries, like aerospace or medical devices, generally offer more robust compensation packages compared to smaller job shops.
Remote work is uncommon for this hands-on role, but some companies may offer flexible shifts. Salary negotiation leverage increases with proven expertise in complex part inspection and a strong track record of defect prevention. While the provided figures are in USD, international markets will have their own distinct salary scales influenced by local economic conditions and industry prevalence.
Salary by Experience Level
Level | US Median | US Average |
---|---|---|
Junior Quality Inspector | $42k USD | $45k USD |
Quality Inspector | $55k USD | $58k USD |
Senior Quality Inspector | $68k USD | $72k USD |
Lead Quality Inspector | $80k USD | $85k USD |
Quality Assurance Supervisor | $93k USD | $98k USD |
Quality Assurance Manager | $108k USD | $115k USD |
Market Commentary
The job market for Machined Parts Quality Inspectors shows stable demand, driven by the ongoing need for precision manufacturing across various industries. The U.S. Bureau of Labor Statistics projects a modest growth for inspectors, testers, sorters, samplers, and weighers. This growth is influenced by the re-shoring of manufacturing and continued investment in advanced manufacturing technologies.
Emerging opportunities for Quality Inspectors include roles in automated inspection systems and data analytics for quality control. Proficiency in interpreting CMM data, utilizing statistical process control (SPC) software, and understanding Industry 4.0 principles is becoming increasingly valuable. The demand for meticulous inspection remains high, especially in critical sectors like aerospace, automotive, and medical device manufacturing, where product reliability is paramount.
The supply of skilled inspectors with expertise in modern metrology tools can sometimes lag behind demand, creating opportunities for qualified candidates. Automation and AI are impacting the inspection field, but they are more likely to augment the role rather than replace it entirely. Inspectors will increasingly oversee automated systems and analyze their outputs, requiring a blend of traditional inspection skills and technological aptitude.
Geographic hotspots for this role align with major manufacturing hubs. The profession is generally considered recession-resistant due to the universal need for quality assurance in production. Future-proofing involves continuous learning in new inspection technologies, software, and materials science.
Machined Parts Quality Inspector Career Path
Career progression for a Machined Parts Quality Inspector typically involves a gradual increase in complexity, responsibility, and leadership. Professionals advance by mastering inspection techniques, understanding material properties, and developing a keen eye for detail. This field distinguishes between individual contributor (IC) tracks, where inspectors become highly specialized technical experts, and management tracks, which involve leading teams and overseeing quality systems.
Advancement speed depends on performance, the ability to specialize in advanced metrology or specific material types, and the company's size and industry. Larger corporations often have more structured paths and diverse roles, while smaller shops might offer quicker jumps in responsibility. Lateral movement within quality assurance, such as moving into a quality engineering or supplier quality role, is common as inspectors gain a broader understanding of manufacturing processes.
Networking within professional organizations, pursuing certifications like ASQ Certified Quality Inspector (CQI) or Certified Quality Technician (CQT), and continuous learning in areas like GD&T (Geometric Dimensioning and Tolerancing) and CMM (Coordinate Measuring Machine) programming are crucial for progression. Mentorship from experienced inspectors or quality engineers significantly aids development. Some inspectors may pivot into roles like manufacturing engineering, process improvement, or even product design, leveraging their deep understanding of product specifications and defect analysis.
Junior Quality Inspector
0-2 yearsKey Focus Areas
Quality Inspector
2-4 yearsKey Focus Areas
Senior Quality Inspector
4-7 yearsKey Focus Areas
Lead Quality Inspector
7-10 yearsKey Focus Areas
Quality Assurance Supervisor
10-15 yearsKey Focus Areas
Quality Assurance Manager
15+ yearsKey Focus Areas
Junior Quality Inspector
0-2 yearsPerforms routine visual and dimensional inspections on machined parts using standard hand tools and basic inspection equipment. Works under direct supervision, following established procedures and work instructions. Identifies non-conforming parts and escalates issues to senior inspectors or supervisors. Primarily focuses on single-piece or small-batch inspections.
Key Focus Areas
Mastering fundamental inspection tools such as calipers, micrometers, and height gauges. Developing a strong understanding of blueprints and basic GD&T symbols. Learning to accurately document inspection results and identify common manufacturing defects. Building foundational knowledge of material types and their properties.
Quality Inspector
2-4 yearsConducts detailed dimensional and visual inspections of complex machined components, often involving tight tolerances and intricate geometries. Operates and may perform basic programming on CMMs and other automated inspection equipment. Works with minimal supervision, making independent decisions on part acceptance based on specifications. Participates in initial non-conformance investigations.
Key Focus Areas
Enhancing proficiency with advanced inspection equipment like CMMs and optical comparators. Deepening understanding of complex GD&T callouts and their application. Improving problem-solving skills for identifying root causes of defects. Developing communication skills for interacting with machinists and engineers regarding quality issues.
Senior Quality Inspector
4-7 yearsServes as a subject matter expert for complex inspection challenges and critical parts. Provides technical guidance and training to junior inspectors on advanced inspection methods and equipment. Troubleshoots inspection equipment issues and assists in calibration activities. Leads non-conformance resolution efforts and collaborates with engineering and production to implement corrective actions. May review and approve inspection plans.
Key Focus Areas
Developing expertise in specific metrology techniques or product lines. Mentoring junior inspectors and providing technical guidance. Contributing to the development of inspection procedures and documentation. Expanding knowledge of statistical process control (SPC) and its application in quality monitoring. Taking initiative in continuous improvement projects.
Lead Quality Inspector
7-10 yearsCoordinates the daily workflow and assignments for a team of quality inspectors, ensuring efficient throughput and adherence to inspection schedules. Acts as the primary point of contact for production and engineering regarding inspection status and critical quality issues. Provides technical leadership, resolves complex inspection disputes, and ensures consistent application of quality standards. May conduct performance reviews for team members.
Key Focus Areas
Leading and coordinating the daily activities of a small team of inspectors. Developing project management skills for managing inspection queues and priorities. Improving advanced CMM programming and data analysis capabilities. Contributing to the strategic planning of quality control processes. Fostering a culture of quality within the inspection team.
Quality Assurance Supervisor
10-15 yearsManages and oversees the daily operations of the quality inspection department, including staffing, training, and resource allocation. Ensures compliance with company quality standards, customer specifications, and industry regulations. Implements and monitors key performance indicators (KPIs) for the inspection process. Leads continuous improvement initiatives within the quality control function. Participates in internal and external quality audits.
Key Focus Areas
Developing leadership and team management skills, including scheduling, performance management, and conflict resolution. Gaining a deeper understanding of quality management systems (QMS) like ISO 9001. Improving analytical skills for identifying trends in quality data and implementing preventive measures. Learning to effectively communicate quality performance to upper management.
Quality Assurance Manager
15+ yearsResponsible for the overall planning, implementation, and management of the organization's quality assurance programs for machined parts. Develops and executes quality strategies aligned with business objectives. Leads a team of quality professionals, including inspectors and supervisors. Drives continuous improvement efforts across all manufacturing processes to enhance product quality and reduce defects. Represents the company on quality matters with customers and regulatory bodies.
Key Focus Areas
Developing strategic planning and executive communication skills. Mastering advanced quality methodologies such as Six Sigma and Lean manufacturing. Building strong cross-functional leadership abilities to influence quality across the organization. Understanding financial implications of quality decisions and return on investment for quality initiatives. Cultivating external relationships with suppliers and customers.
Job Application Toolkit
Ace your application with our purpose-built resources:
Machined Parts Quality Inspector Resume Examples
Proven layouts and keywords hiring managers scan for.
View examplesMachined Parts Quality Inspector Cover Letter Examples
Personalizable templates that showcase your impact.
View examplesTop Machined Parts Quality Inspector Interview Questions
Practice with the questions asked most often.
View examplesMachined Parts Quality Inspector Job Description Template
Ready-to-use JD for recruiters and hiring teams.
View examplesGlobal Machined Parts Quality Inspector Opportunities
Machined Parts Quality Inspectors ensure precision and compliance in manufacturing globally. This role translates well across industrial nations, given universal standards like ISO. Demand remains steady in 2025 across advanced manufacturing hubs, driven by supply chain integrity. Differences exist in specific industry regulations, but core inspection principles are consistent. International opportunities allow exposure to diverse manufacturing techniques and career advancement. Certifications such as ASQ Certified Quality Inspector (CQI) enhance global mobility.
Global Salaries
Salaries for Machined Parts Quality Inspectors vary significantly by region and industrial density. In North America, particularly the USA, inspectors earn between $50,000 and $75,000 USD annually. Canadian salaries are comparable, often ranging from CAD 55,000 to CAD 80,000.
European compensation sees a wide range. In Germany, a major manufacturing hub, inspectors can expect €40,000 to €60,000 (approximately $43,000-$65,000 USD). The UK offers £30,000 to £45,000 (around $38,000-$57,000 USD). Southern European countries like Spain or Italy might offer less, typically €25,000 to €40,000 ($27,000-$43,000 USD).
Asia-Pacific markets present diverse figures. In Japan, salaries range from ¥4,000,000 to ¥6,500,000 (about $27,000-$44,000 USD). Australia offers AUD 60,000 to AUD 85,000 ($40,000-$57,000 USD). Cost of living adjustments are crucial; for instance, a lower nominal salary in a country with lower living expenses might offer similar purchasing power to a higher salary in an expensive city.
Salary structures also differ. European countries often include more robust benefits packages like extended paid leave and comprehensive healthcare. Tax implications vary, affecting take-home pay. For example, high income taxes in some Western European nations contrast with lower rates in parts of North America. International experience and specialized skills, like CMM programming, can significantly boost compensation globally. While no single international pay scale exists, industry-specific certifications and a proven track record of precision enhance earning potential.
Remote Work
Direct international remote work for Machined Parts Quality Inspectors is limited due to the hands-on nature of the role. Physical presence is necessary for inspecting parts, operating CMMs, and performing visual checks. However, some aspects can be remote.
Inspectors might conduct remote documentation review, data analysis of inspection reports, or virtual audits of supplier quality systems. Companies may hire inspectors for remote oversight of quality processes across multiple international sites, requiring occasional travel. Digital nomad opportunities are generally not applicable for the core inspection duties.
Employers hiring internationally for this role often seek on-site talent. Salary expectations for remote tasks would align with administrative or analytical roles, not the full inspector compensation. Internet stability and secure data transfer are key for any remote components. Most companies prefer local hires for the actual inspection work.
Visa & Immigration
Skilled worker visas are the most common pathway for Machined Parts Quality Inspectors seeking international employment. Major manufacturing nations like Germany, Canada, and the USA offer specific visa categories for skilled trades and technical professionals. Requirements often include a job offer, relevant experience, and recognized certifications.
For instance, Canada's Express Entry system and Germany's Blue Card or skilled worker visa require proof of qualifications and a contract. Education credential recognition is vital; official evaluations ensure foreign degrees or diplomas meet local standards. Some countries, like Australia, may require specific professional licensing or trade assessments.
Visa timelines vary, typically ranging from a few months to over a year. The application process involves submitting detailed documentation, including educational certificates, work history, and financial proofs. Language proficiency tests, such as IELTS for English or Goethe-Zertifikat for German, are often mandatory.
Pathways to permanent residency exist in many nations for skilled workers after several years of employment. Family visas allow dependents to accompany the primary applicant. Some countries may offer expedited processing for in-demand occupations, though this role is not always on such lists. Intra-company transfers are also possible for inspectors working for multinational corporations.
2025 Market Reality for Machined Parts Quality Inspectors
Understanding current market conditions for a Machined Parts Quality Inspector is vital for career success. The manufacturing landscape, especially after the pandemic and amidst the AI revolution, has shifted employer expectations significantly.
Market realities vary by experience level, geographic region, and the size of the manufacturing facility. Broader economic factors, such as supply chain stability and industrial output, directly influence the demand for quality assurance roles. This analysis will provide an honest assessment of current hiring trends and practical realities in the field.
Current Challenges
Machined Parts Quality Inspectors face increased competition, particularly from automation. Market saturation at entry-level positions makes securing initial roles difficult. Economic uncertainty also leads some manufacturers to delay hiring or optimize existing staff through AI-powered tools. These factors extend job search timelines for many candidates.
Growth Opportunities
Despite challenges, strong demand exists in specialized manufacturing sectors like aerospace, medical devices, and defense. These industries require extremely high precision, making human inspection and oversight irreplaceable for critical components. Opportunities are emerging for inspectors skilled in advanced metrology, such as laser scanning and 3D optical measurement, especially when integrated with AI-driven analysis.
Professionals can position themselves advantageously by acquiring certifications in CMM programming, GD&T, and statistical process control. Expertise in validating and overseeing automated inspection systems, rather than just manual checks, offers a significant competitive edge. Underserved markets often exist in smaller, high-precision custom fabrication shops that cannot afford full automation yet or require complex, low-volume inspection.
Certain skills, like proficiency with Minitab, advanced CMM software, or interpreting complex CAD models for inspection planning, provide a distinct advantage. While broader manufacturing faces economic headwinds, sectors focused on innovation or high-value, low-volume production often remain robust. Strategic career moves involve targeting companies investing in Industry 4.0 technologies and seeking inspectors who can bridge the gap between traditional quality control and automated systems. Investing in continuous learning for new inspection technologies and data analytics will be key.
Current Market Trends
Hiring for Machined Parts Quality Inspectors shows stable demand in specialized manufacturing sectors, but overall growth remains modest. Recent industry changes emphasize precision and efficiency, driven by advanced CNC machining and automation. The post-pandemic supply chain recalibration has led to some reshoring of manufacturing, which in turn creates localized demand for inspection roles.
Economic conditions influence hiring, with sectors like aerospace and medical devices showing consistent need for highly precise inspection. However, general industrial manufacturing may see slower growth. Generative AI and machine learning are impacting the field, not by replacing inspectors entirely, but by automating repetitive visual checks and data analysis. This shifts the inspector's role towards overseeing automated systems, validating complex measurements, and troubleshooting discrepancies identified by AI.
Employer requirements now frequently include proficiency with digital inspection tools, CMM programming, and statistical process control software. Companies seek inspectors who understand data analytics and can interpret output from automated systems. Salary trends are relatively flat for experienced inspectors, but those with advanced metrology skills or AI tool experience may command slightly higher wages. Market saturation is more apparent at the entry level, where candidates often lack the specific software and advanced equipment experience now expected.
Geographic variations are significant; states with strong aerospace, automotive, or defense manufacturing clusters, such as Michigan, Texas, and California, show stronger demand. Remote work is generally not applicable for this hands-on role. Seasonal hiring patterns are less pronounced, but capital expenditure cycles in manufacturing can create periodic increases in demand for quality control staff.
Emerging Specializations
Technological advancements and evolving manufacturing processes continuously create new specialization opportunities within the quality inspection field. For Machined Parts Quality Inspectors, understanding these future-oriented paths is crucial for career advancement and securing high-demand roles from 2025 onwards.
Early positioning in emerging areas often commands premium compensation and accelerated career growth. As industries adopt advanced manufacturing techniques and smart factory concepts, the demand for inspectors with specialized knowledge in these areas intensifies. This strategic foresight allows professionals to become early experts in next-generation quality control.
While established specializations remain vital, focusing on emerging areas offers a distinct competitive advantage. Many cutting-edge fields are still nascent, meaning fewer experienced professionals exist, creating significant opportunities for those who invest in new skill sets. These emerging areas typically take several years to become mainstream, offering a window for proactive professionals to build expertise and become industry leaders.
Embracing these cutting-edge specializations involves a balance of risk and reward. While the demand for specific skills may be less defined initially, the potential for high impact and rapid career progression in a less crowded field is substantial. Professionals must assess industry trends carefully and align their skill development with genuine market shifts.
Additive Manufacturing Quality Inspector
Automated & Data-Driven Quality Inspector
High-Precision & Critical Components Inspector
Electric Vehicle Component Quality Inspector
Robotics & Automated Inspection System Specialist
Pros & Cons of Being a Machined Parts Quality Inspector
Making informed career decisions requires a clear understanding of both the benefits and challenges associated with a specific profession. A career as a Machined Parts Quality Inspector, like any other, comes with its own unique set of advantages and disadvantages. These experiences can vary significantly based on the specific industry (e.g., automotive, aerospace, medical), the size and culture of the manufacturing company, and the complexity of the parts being inspected. Furthermore, what one individual views as a positive aspect, another might perceive as a challenge, depending on personal values, work style, and career aspirations. It is important to consider how these pros and cons might evolve at different stages of your career, from entry-level to senior positions. This assessment provides a realistic overview to help you set appropriate expectations.
Pros
- There is consistent demand for skilled Machined Parts Quality Inspectors across various manufacturing sectors, ensuring good job security and a steady availability of positions.
- The role offers a sense of accomplishment and direct contribution to product quality and safety, as inspectors play a critical part in preventing defective parts from reaching customers.
- The work involves precise measurement and analytical thinking, providing intellectual stimulation for individuals who enjoy meticulous tasks and problem-solving.
- Entry-level positions often require vocational training or an associate's degree, making it an accessible career path without the need for an extensive four-year university education.
- Many manufacturing companies offer stable day shifts with predictable hours, providing a good work-life balance compared to some other industrial roles.
- The skills acquired, such as proficiency with various measurement tools, blueprint reading, and quality standards, are highly transferable across different manufacturing industries.
- There are opportunities to specialize in advanced metrology techniques or specific materials, which can lead to higher earning potential and more specialized roles.
Cons
- The work environment can be monotonous, involving repetitive tasks of measuring and inspecting similar parts for extended periods, which may lead to boredom or reduced engagement over time.
- There is a risk of eye strain and fatigue due to continuous close-up work and focus on intricate details, especially when inspecting small or complex machined components.
- Potential for exposure to industrial noise, oils, coolants, and metal dust in manufacturing settings, requiring consistent use of personal protective equipment and adherence to safety protocols.
- Pressure to maintain high accuracy and detect even minute flaws can be intense, as missing a defect can lead to costly product failures, rework, or customer complaints.
- Career advancement opportunities may be limited without pursuing additional education or specialized certifications in quality management, metrology, or engineering disciplines.
- The job often requires standing for long periods or performing repetitive motions, which can lead to physical discomfort or musculoskeletal issues over time.
- Adapting to new inspection technologies, software, and evolving industry standards demands continuous learning and training to remain proficient and effective in the role.
Frequently Asked Questions
Machined Parts Quality Inspectors face distinct challenges ensuring precision and adherence to strict specifications. This section addresses common concerns about entering this role, from mastering measurement tools to understanding industry standards and maintaining a sharp eye for detail in a demanding environment.
What educational background or certifications do I need to become a Machined Parts Quality Inspector?
Most Machined Parts Quality Inspector roles require a high school diploma or GED, often supplemented by vocational training or an associate's degree in a relevant field like manufacturing technology or quality assurance. Employers highly value certifications from organizations such as the American Society for Quality (ASQ), particularly the Certified Quality Inspector (CQI) certification. Practical experience with precision measurement tools and reading blueprints is essential.
What is the typical salary range for a Machined Parts Quality Inspector?
Entry-level Machined Parts Quality Inspectors can expect to earn between $35,000 and $55,000 annually, depending on location, company size, and specific responsibilities. With experience, specialized certifications, and the ability to operate advanced inspection equipment like CMMs, salaries can increase significantly, potentially reaching $60,000 to $80,000 or more for senior roles. Overtime opportunities are often available and can boost total compensation.
How long does it take to become proficient enough to work as a Machined Parts Quality Inspector?
The time to become job-ready depends on your starting point. If you have a strong mechanical aptitude, you could gain entry-level skills within 6-12 months through a vocational program or on-the-job training. Obtaining a relevant associate's degree usually takes two years. Building proficiency with a wide range of inspection tools and understanding complex blueprints often requires several years of practical experience in the field.
What is the typical work-life balance like for a Machined Parts Quality Inspector?
The work-life balance for Machined Parts Quality Inspectors can vary. Many roles are standard Monday-Friday, 8-hour shifts. However, some manufacturing environments operate 24/7, meaning inspectors might work rotating shifts, evenings, or weekends, especially in facilities with high production demands. Overtime is common, particularly when deadlines are tight or production issues arise, which can impact personal time.
Is the Machined Parts Quality Inspector role a secure career path with good job prospects?
The job market for Machined Parts Quality Inspectors remains stable due to the ongoing need for precision manufacturing across various industries, including aerospace, automotive, and medical devices. As manufacturing processes become more complex and automation increases, the demand for skilled inspectors who can interpret advanced data and ensure compliance is likely to grow. Job security is generally good for those with strong technical skills and relevant certifications.
What are the common career advancement opportunities for a Machined Parts Quality Inspector?
Career growth for Machined Parts Quality Inspectors can lead to several advanced roles. You might advance to Senior Quality Inspector, Quality Control Lead, or Quality Assurance Supervisor, overseeing teams and processes. Further specialization in areas like metrology, calibration, or non-destructive testing can open doors to highly specialized positions. Some inspectors transition into quality engineering or management roles with additional education or experience.
Can a Machined Parts Quality Inspector work remotely, or is it an on-site role?
Working remotely as a Machined Parts Quality Inspector is generally not feasible because the role requires hands-on inspection of physical parts using specialized equipment. You need to be present on the manufacturing floor or in a dedicated quality lab to perform inspections, operate machinery, and interact directly with production teams. Some administrative or documentation tasks might be done remotely, but the core inspection duties are on-site.
What are the biggest challenges or common frustrations in this role?
The most significant challenge is maintaining extreme attention to detail and precision under pressure, often with high production volumes and tight deadlines. You must accurately interpret complex blueprints, utilize various measuring instruments, and identify minute defects consistently. Keeping up with evolving manufacturing technologies and quality standards also requires continuous learning and adaptability.
Related Careers
Explore similar roles that might align with your interests and skills:
QA Inspector
A growing field with similar skill requirements and career progression opportunities.
Explore career guideQuality Assurance Inspector
A growing field with similar skill requirements and career progression opportunities.
Explore career guideQuality Control Inspector
A growing field with similar skill requirements and career progression opportunities.
Explore career guideQuality Inspector
A growing field with similar skill requirements and career progression opportunities.
Explore career guideQuality Technician
A growing field with similar skill requirements and career progression opportunities.
Explore career guideAssess your Machined Parts Quality Inspector readiness
Understanding where you stand today is the first step toward your career goals. Our Career Coach helps identify skill gaps and create personalized plans.
Skills Gap Analysis
Get a detailed assessment of your current skills versus Machined Parts Quality Inspector requirements. Our AI Career Coach identifies specific areas for improvement with personalized recommendations.
See your skills gapCareer Readiness Assessment
Evaluate your overall readiness for Machined Parts Quality Inspector roles with our AI Career Coach. Receive personalized recommendations for education, projects, and experience to boost your competitiveness.
Assess your readinessSimple pricing, powerful features
Upgrade to Himalayas Plus and turbocharge your job search.
Himalayas
Himalayas Plus
Himalayas Max
Find your dream job
Sign up now and join over 100,000 remote workers who receive personalized job alerts, curated job matches, and more for free!
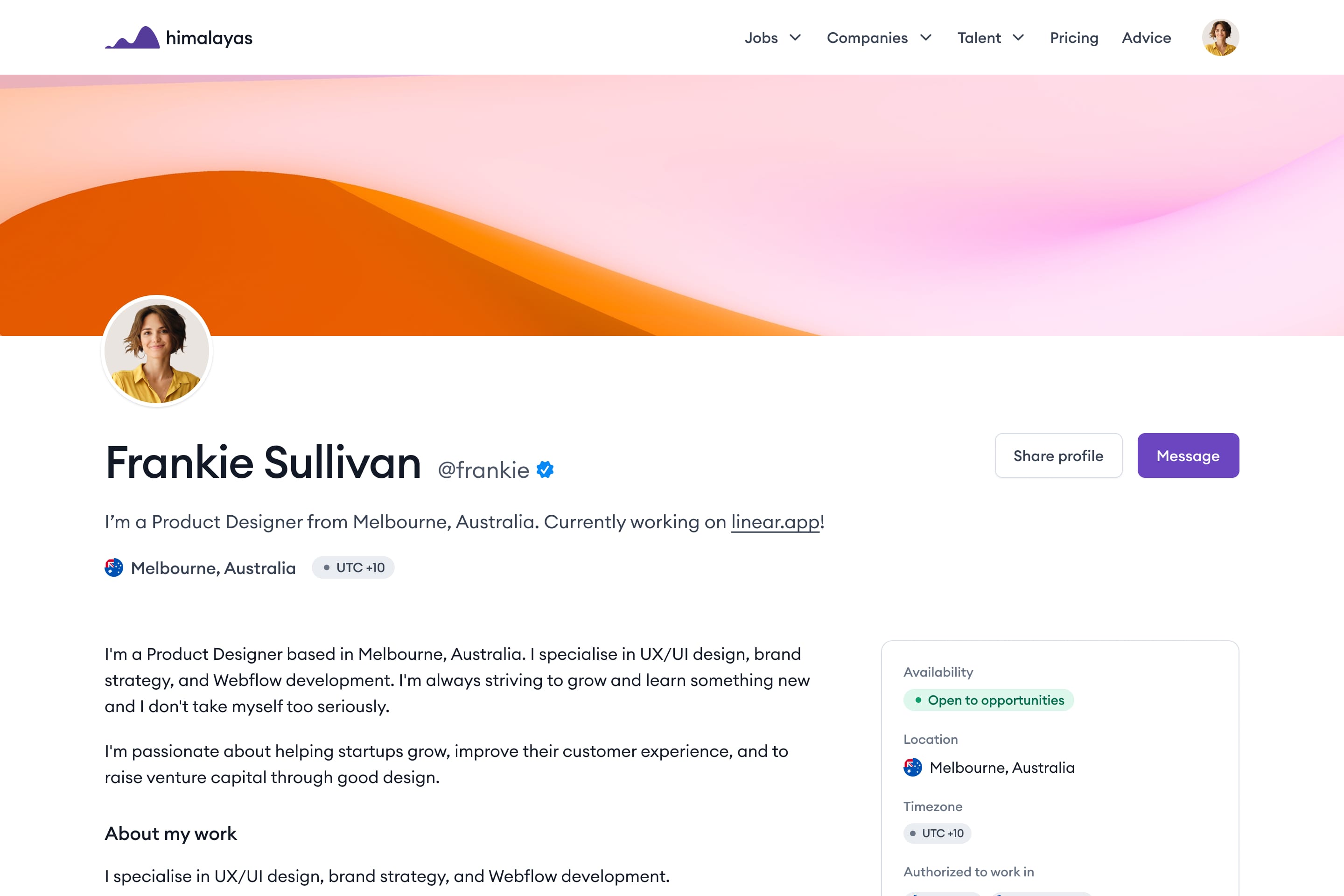