Complete Lift Operator Career Guide
Lift Operators play a crucial role in ensuring the safe and efficient movement of people and materials, whether it's powering ski resorts, managing construction sites, or facilitating logistics in warehouses. This hands-on career offers a direct impact on operational flow and safety, providing essential services in diverse environments. You'll develop specialized skills in machine operation and safety protocols, opening doors to various industries.
Key Facts & Statistics
Median Salary
$44,790 USD
(U.S. national median for Material Moving Machine Operators, U.S. Bureau of Labor Statistics, May 2023)
Range: $30k - $60k+ USD (varies significantly by industry and location, for entry-level to experienced operators)
Growth Outlook
4%
as fast as average (U.S. Bureau of Labor Statistics, 2022-2032 for material moving machine operators)
Annual Openings
≈30k
openings annually (based on various operator roles that include lift operation, U.S. Bureau of Labor Statistics)
Top Industries
Typical Education
High School Diploma or equivalent; often requires on-the-job training, specific certifications (e.g., OSHA forklift certification), or a commercial driver's license (CDL) depending on equipment and industry.
What is a Lift Operator?
A Lift Operator is a specialized professional responsible for the safe and efficient operation of powered industrial trucks and aerial work platforms. These machines include forklifts, reach trucks, order pickers, pallet jacks, scissor lifts, and boom lifts. Their core purpose involves moving, lifting, and positioning materials, equipment, or personnel within a designated area, ensuring productivity while prioritizing safety.
This role differs significantly from a general laborer or truck driver; a lift operator possesses specific certifications and training to handle complex machinery that demands precision, balance, and a deep understanding of load capacities and stability. Unlike a crane operator who manages much larger, often fixed, lifting apparatuses for heavier loads over greater distances, a lift operator typically works within defined indoor or outdoor spaces, focusing on horizontal and vertical movement of goods or personnel at lower heights.
What does a Lift Operator do?
Key Responsibilities
- Operate various types of lifts, such as forklifts, cherry pickers, or scissor lifts, to move materials, equipment, or personnel safely around the worksite.
- Conduct pre-operation safety checks on lift equipment, including inspecting controls, brakes, fuel/battery levels, and hydraulic systems, reporting any defects immediately.
- Load and unload materials from trucks or storage areas, ensuring proper weight distribution and secure placement to prevent shifting during transport.
- Transport goods to designated locations, navigating tight spaces and crowded areas while adhering to all site-specific traffic and safety protocols.
- Maintain accurate logs of equipment usage, including hours of operation, maintenance performed, and any incidents or malfunctions.
- Perform routine maintenance tasks like cleaning, lubricating, and refueling equipment to ensure optimal performance and extend machine lifespan.
- Communicate effectively with ground crews, supervisors, and other operators using hand signals, two-way radios, or verbal instructions to coordinate movements and ensure safety.
Work Environment
Lift operators typically work in dynamic environments such as warehouses, construction sites, manufacturing plants, distribution centers, and retail storage facilities. The work often involves a mix of indoor and outdoor tasks, exposed to varying weather conditions, dust, and noise.
The pace is often fast, requiring constant attention to surroundings and coordination with other workers. Operators work independently while operating equipment but frequently communicate with ground crews and supervisors. Schedules can vary, including day, night, or rotating shifts, with some roles requiring overtime, especially in logistics or construction. The work demands precision, focus, and adherence to strict safety protocols.
Tools & Technologies
Lift operators primarily use various types of powered industrial trucks, including counterbalance forklifts, reach trucks, order pickers, pallet jacks, and specialized aerial lifts like scissor lifts and boom lifts. They interact with control panels, joysticks, and foot pedals specific to each machine.
Essential safety equipment includes hard hats, safety glasses, steel-toed boots, and high-visibility vests. Operators also use two-way radios or communication systems to coordinate with teams. They often work with material handling accessories like pallets, crates, and specialized attachments for their lifts. Maintenance tasks require basic hand tools for inspections and minor adjustments.
Lift Operator Skills & Qualifications
Qualifications for a Lift Operator primarily focus on practical competence and safety adherence, rather than extensive formal education. Employers prioritize demonstrated ability to operate heavy machinery safely, coupled with a strong understanding of site-specific safety protocols. The requirements for this role can vary significantly based on the industry (e.g., construction, warehouse, manufacturing, ski resort) and the type of lift being operated.
For entry-level positions, a high school diploma or equivalent is typically sufficient, with on-the-job training being a common pathway. As operators gain experience and move into roles involving more complex or specialized equipment, additional certifications become crucial. These certifications, often industry-recognized and sometimes legally mandated, validate an operator's proficiency and commitment to safety. Practical experience often outweighs formal degrees; employers value hands-on hours and a clean safety record above all else.
The skill landscape for Lift Operators is stable but increasingly emphasizes advanced safety features and digital controls on newer equipment. While foundational skills remain constant, operators benefit from familiarity with modern machinery interfaces. Regulatory compliance is paramount, making up-to-date certification and continuous safety training essential for career longevity. "Must-have" skills center around safe operation and equipment maintenance, while "nice-to-have" skills include versatility across different lift types and basic mechanical troubleshooting.
Education Requirements
Technical Skills
- Pre-operational equipment inspection (e.g., fluid levels, tire pressure, controls, safety devices)
- Safe operation of specific lift types (e.g., forklifts, telehandlers, aerial lifts, scissor lifts, overhead cranes)
- Load capacity calculation and adherence to weight limits
- Maneuvering in confined spaces and around obstacles
- Proper load securing and balancing techniques
- Understanding and interpreting load charts and operational manuals
- Basic equipment troubleshooting and minor maintenance checks
- Adherence to Occupational Safety and Health Administration (OSHA) regulations and site-specific safety protocols
- Use of communication devices (e.g., two-way radios, hand signals) for coordination
- Post-operational equipment shutdown procedures and reporting
Soft Skills
- Attention to Detail: Critical for identifying potential hazards, monitoring equipment performance, and ensuring precise load placement, preventing accidents and damage.
- Safety Consciousness: Paramount for adhering to strict safety regulations and procedures, protecting oneself and others on the job site.
- Situational Awareness: Essential for constantly monitoring the surrounding environment, anticipating movements of personnel or other equipment, and reacting quickly to changes.
- Problem-Solving: Important for quickly diagnosing minor equipment issues or unexpected site conditions, allowing for safe and efficient resolution.
- Reliability: Crucial for consistent attendance, punctuality, and dependable performance, ensuring operational continuity and meeting deadlines.
- Communication Skills: Necessary for clear and concise interaction with ground crews, supervisors, and other operators, especially when coordinating complex lifts or movements.
- Patience: Important when dealing with challenging loads, adverse weather conditions, or coordinating with less experienced team members, ensuring tasks are completed safely without rushing.
- Mechanical Aptitude: Useful for understanding how lift equipment works, performing pre-operation checks, and identifying potential maintenance needs before they escalate into major issues, enhancing safety and efficiency.
How to Become a Lift Operator
Becoming a Lift Operator offers a direct entry into the outdoor recreation industry, particularly in ski resorts or construction sites. While formal degrees are not required, specific certifications and a strong safety-first mindset are crucial. Entry pathways vary; some individuals start with seasonal resort jobs, gaining experience with different equipment, while others pursue direct certification for industrial lift operations.
The timeline for entry can be relatively short, often 1-3 months, especially for seasonal resort roles which frequently offer on-the-job training and certification. Industrial or construction lift operation might require a slightly longer preparation period, focusing on specific machinery certifications like OSHA-compliant training for forklifts or aerial lifts. Geographic location heavily influences opportunities; major ski resorts or construction zones in growing cities will have more openings than rural areas.
Understanding the distinction between recreational (ski lifts) and industrial (forklifts, aerial lifts) roles is key. Recreational roles prioritize customer service and safety in a dynamic, outdoor environment, often requiring physical stamina and a willingness to work irregular hours. Industrial roles focus strictly on operational safety, efficiency, and adherence to regulations, often in more structured work settings. Both pathways emphasize rigorous safety protocols and quick, decisive action in emergencies.
Step 1
Step 2
Step 3
Step 4
Step 5
Step 6
Education & Training Needed to Become a Lift Operator
Becoming a Lift Operator primarily involves on-the-job training and specific certifications, rather than formal degrees. Unlike many professions, a four-year university degree is not necessary or beneficial for this role. Most ski resorts and construction companies provide the required training once hired. This typically includes safety protocols, operational procedures for various lift types, and emergency response. New hires often shadow experienced operators for several days or weeks before working independently.
Alternative learning paths focus on industry-specific certifications. For ski lift operators, the National Ski Areas Association (NSAA) offers valuable training resources, though direct certification often comes from the employer. For construction or industrial lift operators, certifications like OSHA 10 or 30 (Occupational Safety and Health Administration) are highly valued, indicating a foundational understanding of workplace safety. Specialized certifications for specific equipment, such as a forklift operator license, are also common. These certifications usually cost between $100 and $500 and can be completed in a few days to a week.
The market perception of credentials for Lift Operators heavily favors practical experience and direct certifications over academic degrees. Employers prioritize candidates with a proven safety record and equipment-specific training. Continuous learning in this field involves staying updated on safety regulations and equipment advancements. While initial training is often quick, typically 1-2 weeks, ongoing professional development ensures operators maintain competence and adapt to new technologies. The cost-benefit analysis strongly favors direct training and certifications, offering a high return on a relatively small investment in time and money, leading directly to employment.
Lift Operator Salary & Outlook
Compensation for a Lift Operator varies significantly based on several factors, extending beyond just the hourly wage. Geographic location plays a crucial role, as resorts in high cost-of-living areas or major ski destinations typically offer higher pay to attract staff. The size and prestige of the ski resort also influence earnings, with larger, more established resorts often providing better compensation packages.
Experience directly impacts earning potential. Entry-level operators earn less than those with several seasons under their belt who have mastered various lift types and operational procedures. Specialization, such as expertise in high-speed detachable lifts or advanced troubleshooting, can also command higher pay. Beyond base salary, total compensation often includes seasonal bonuses, free or discounted season passes, and housing assistance, which can significantly reduce living expenses.
Some resorts offer health benefits or retirement contributions, especially for year-round or management positions. Performance and reliability are key factors in securing raises and promotions within lift operations. While primarily a seasonal role, some operators may find year-round employment transitioning to summer operations or maintenance. International roles offer different compensation structures, but the figures provided here reflect the US market.
Salary by Experience Level
Level | US Median | US Average |
---|---|---|
Lift Operator | $30k USD | $32k USD |
Senior Lift Operator | $36k USD | $38k USD |
Lift Operations Supervisor | $48k USD | $50k USD |
Lift Operations Manager | $62k USD | $65k USD |
Market Commentary
The job market for Lift Operators is primarily seasonal, driven by winter sports tourism. Demand peaks during the ski season, particularly in regions with significant snowfall and numerous resorts. The industry's growth outlook is stable, closely tied to recreational spending and climate patterns. Technological advancements in lift systems require operators to adapt to more sophisticated controls and safety protocols, though automation is not a significant threat to this role's core functions.
Currently, many resorts face a consistent need for reliable seasonal labor, often leading to competitive recruitment efforts. Supply and demand dynamics can fluctuate based on local unemployment rates and the appeal of seasonal work. There is a consistent demand for experienced operators who understand complex lift systems and can handle various operational challenges. Emerging opportunities include year-round resort positions that blend lift operations with summer activities or maintenance.
Future-proofing this career involves developing a diverse skill set in resort operations, including maintenance, guest services, and safety management. While the role is generally recession-resistant as long as tourism continues, economic downturns can impact visitor numbers. Geographic hotspots for Lift Operators include the Rocky Mountains, the Pacific Northwest, and New England. Remote work is not applicable to this hands-on role, emphasizing the need for on-site presence and physical capability.
Lift Operator Career Path
Career progression for a Lift Operator unfolds through increasing responsibility, technical proficiency, and leadership capabilities within resort or recreational settings. Individuals typically begin in an operational role, focusing on safety and efficiency. Advancement often involves demonstrating exceptional performance, a strong commitment to safety protocols, and a willingness to take on additional duties.
Progression offers two primary pathways: an individual contributor (IC) track, which emphasizes deep operational expertise and specialized skills, or a management/leadership track, focusing on team oversight, strategic planning, and operational management. Factors influencing advancement speed include consistent high performance, the ability to manage complex situations, company size, and the specific recreational industry (e.g., ski resorts, amusement parks). Larger organizations may offer more structured advancement opportunities, while smaller operations might combine roles.
Lateral movement opportunities within this field include transitioning to other specialized operations roles, such as snowmaking or terrain park operations, or moving into related guest services or maintenance departments. Continuous learning, including certifications in safety and equipment operation, is crucial. Networking within the resort community and mentorship from experienced operators or supervisors significantly aids career growth. Industry reputation, built on reliability and a safety-first mindset, is also a key factor in securing higher-level positions.
Lift Operator
0-2 yearsKey Focus Areas
Senior Lift Operator
2-4 yearsKey Focus Areas
Lift Operations Supervisor
4-7 yearsKey Focus Areas
Lift Operations Manager
7+ yearsKey Focus Areas
Lift Operator
0-2 yearsOperates ski lifts or other recreational lifts, ensuring the safe loading and unloading of guests. Performs routine daily checks and maintenance tasks on lift equipment. Communicates effectively with guests regarding safety procedures and resort information. Responds to minor operational interruptions under direct supervision, following established protocols.
Key Focus Areas
Mastering safe and efficient lift operation procedures. Focusing on guest interaction and maintaining a positive attitude. Developing basic troubleshooting skills for common lift issues. Understanding and adhering to all safety regulations and emergency protocols. Learning effective communication with guests and team members.
Senior Lift Operator
2-4 yearsAssists in training new lift operators and provides guidance on complex operational scenarios. Takes lead on specific lift stations, managing guest flow and addressing operational challenges. Performs more complex routine maintenance and assists with minor repairs. Acts as a primary point of contact for guest issues and ensures adherence to safety standards across assigned lifts.
Key Focus Areas
Developing advanced diagnostic and problem-solving skills for lift machinery. Training and mentoring new operators on safety and operational best practices. Taking initiative in identifying and resolving operational inefficiencies. Contributing to safety meetings and suggesting improvements. Acquiring specialized certifications in advanced lift maintenance or specific equipment types.
Lift Operations Supervisor
4-7 yearsDirects and supervises a team of lift operators, ensuring all lifts run safely and efficiently. Manages daily staffing, scheduling, and performance of the team. Conducts regular safety briefings and ensures compliance with all operational procedures. Handles escalated guest concerns and operational issues, making real-time decisions to maintain service levels.
Key Focus Areas
Developing strong leadership and team management skills. Excelling in conflict resolution and performance management. Focusing on operational planning, scheduling, and resource allocation. Improving communication and coordination across different resort departments. Understanding budget management and cost control principles for lift operations.
Lift Operations Manager
7+ yearsOversees the entire lift operations department, including all lifts, personnel, and related infrastructure. Develops and implements operational policies, safety programs, and training protocols. Manages departmental budgets, forecasts staffing needs, and oversees equipment maintenance schedules. Collaborates with other resort departments to ensure seamless guest experiences and operational efficiency.
Key Focus Areas
Focusing on strategic planning for lift operations, including long-term maintenance and capital improvements. Developing advanced financial management and budgeting skills. Cultivating strong relationships with other department heads and senior management. Leading major safety initiatives and emergency preparedness planning. Staying current with industry trends, technology, and regulations to optimize operations.
Job Application Toolkit
Ace your application with our purpose-built resources:
Global Lift Operator Opportunities
Lift operators find global demand, particularly in regions with established tourism and winter sports industries. This profession translates directly across countries; operating a lift requires universal safety standards and mechanical understanding. International opportunities arise in ski resorts, amusement parks, and construction sites worldwide. Cultural nuances may affect customer interaction, but core duties remain consistent. The global job market for lift operators remains stable, with seasonal peaks in leisure sectors. No specific international certifications are typically required, but local licenses or training often apply.
Global Salaries
Salaries for lift operators vary significantly by country and type of operation. In North America, specifically the USA and Canada, annual salaries range from USD 25,000 to USD 40,000 for ski resort operators. European countries like Switzerland and Austria offer EUR 28,000 to EUR 45,000 (approx. USD 30,000 - USD 49,000), often including housing or meal benefits due to high cost of living in resort towns. Australia and New Zealand provide AUD 45,000 to AUD 60,000 (approx. USD 30,000 - USD 40,000).
Asian markets, such as Japan's ski resorts, typically pay JPY 2.5 million to JPY 4 million annually (approx. USD 17,000 - USD 27,000), which may include dormitory-style accommodation. South American countries like Chile or Argentina offer lower nominal wages, often USD 8,000 to USD 15,000 per year, but purchasing power can be higher locally. Salary structures differ; some regions include comprehensive health benefits and generous vacation time, while others prioritize hourly wages with minimal additional perks.
Tax implications also vary widely; countries with higher social welfare systems, like in Europe, may have higher deductions. Experience does not significantly alter compensation for this role internationally; entry-level and experienced operators often earn similar wages. There are no international pay scales or standardized compensation frameworks for lift operators.
Remote Work
Lift operator is a hands-on, location-dependent role. International remote work opportunities are non-existent for this profession. The core duties involve operating physical machinery and interacting directly with the public or materials at a specific site. There are no digital nomad or international remote work policies applicable to lift operators. The job requires physical presence at a lift station or control booth.
All aspects of the role, including equipment operation, safety checks, and customer assistance, demand on-site presence. Therefore, discussions of international team collaboration, time zone considerations, or digital work platforms are irrelevant to a lift operator's job. This profession does not lend itself to geographic arbitrage or any form of remote employment.
Visa & Immigration
International lift operators typically require seasonal or temporary work visas. Popular destinations include Canada, the USA, Australia, New Zealand, and European alpine nations like Switzerland and Austria. Specific requirements vary by country; for instance, Canada often uses the Temporary Foreign Worker Program for ski resort staff. The USA requires H-2B visas for seasonal non-agricultural workers, which can be competitive.
Education credential recognition is generally not an issue, as specific degrees are not required. Professional licensing might be needed, but this is typically local training provided by the employer. Visa timelines range from a few weeks to several months. Application processes involve employer sponsorship and government review.
Pathways to permanent residency through a lift operator role are rare; these are typically temporary positions. Language requirements vary; English is often sufficient in North America, while European countries may require basic proficiency in the local language. Family visas for dependents are generally not available for these short-term work permits. Some countries might offer specific seasonal worker programs that simplify the process, but they are not profession-specific.
2025 Market Reality for Lift Operators
Understanding the current market for lift operators is crucial for career planning in 2025. This field, central to logistics and manufacturing, has seen significant evolution due to post-pandemic supply chain shifts and the ongoing integration of automation. Broader economic factors, such as inflation and consumer spending, directly influence material handling volumes and, consequently, job availability for operators.
Market realities for lift operators vary significantly by experience level, with certified and multi-skilled operators finding more stability. Geographic region plays a large role, as demand concentrates in logistics hubs and industrial zones. Company size also matters; smaller local businesses might offer fewer roles but more direct engagement, while large corporations often feature structured career paths and advanced equipment. This analysis provides an honest assessment of these dynamics, helping operators navigate the current landscape.
Current Challenges
Increased automation in warehousing and manufacturing presents a direct challenge, reducing the need for manual lift operation in some facilities. Competition for the remaining positions intensifies, especially for roles requiring specialized certifications or night shifts. Economic slowdowns impact construction and logistics, sectors where lift operators find significant employment, leading to fewer new projects and lower demand. Companies also expect more from operators, including basic maintenance skills and familiarity with digital inventory systems.
Growth Opportunities
Despite automation, strong opportunities exist for lift operators proficient with diverse equipment types, including specialized lifts like turret trucks and automated guided vehicle (AGV) interfaces. Roles in cold storage facilities, hazmat handling, and oversized material logistics are experiencing consistent demand due to their specialized nature. These areas often present fewer automation solutions, requiring skilled human operation.
Operators who gain certifications for multiple lift types or cross-train in inventory management software and basic machine maintenance stand out. Companies increasingly value operators who can contribute to overall warehouse efficiency, not just move products. Underserved markets often include smaller industrial towns or specific manufacturing niches requiring on-site, specialized material handling. The ongoing expansion of distribution networks for e-commerce and last-mile delivery also creates sustained demand for efficient operators, particularly in roles involving varied load types and fast turnaround times. Investing in advanced safety training or niche equipment certifications can significantly boost employability and earning potential.
Current Market Trends
Hiring for lift operators shows steady demand in logistics, warehousing, and manufacturing, though growth varies by region and industry. E-commerce expansion continues to drive the need for efficient material handling, keeping demand robust in distribution centers. However, the integration of automation and robotics in some large facilities changes the nature of the role, requiring operators to oversee automated systems rather than solely perform manual tasks. This shift means employers increasingly seek candidates with basic troubleshooting skills for automated equipment.
Economic conditions influence hiring, with construction-related lift operator roles seeing fluctuations based on project starts and interest rates. Manufacturing sector demand remains consistent, especially in industries with high production volumes. Salaries for experienced operators are stable, but entry-level wages face pressure in areas with high competition. Remote work does not apply to this role; all positions are on-site. Seasonal peaks often occur around holidays for retail logistics and during construction season for outdoor projects.
Employers now emphasize safety compliance and efficient operation more than ever, with certifications like OSHA 1910.178 becoming standard requirements. The move towards larger, more complex warehouses means operators frequently handle diverse types of lifts, from forklifts to reach trucks and order pickers. This requires versatility and adaptability. Some companies also implement telematics on their lifts, collecting data on operator performance, which adds a layer of accountability for efficiency and safety.
Emerging Specializations
The field of lift operation, while traditionally hands-on, is undergoing a quiet transformation driven by advancements in automation, safety protocols, and smart infrastructure. Understanding these shifts creates new specialization opportunities for operators who are willing to adapt and expand their skill sets. Early positioning in these emerging areas can significantly enhance career trajectories and earning potential beyond 2025.
Specializing in cutting-edge lift technologies allows operators to move beyond routine tasks into roles that demand higher technical expertise and problem-solving capabilities. These specialized positions often command premium compensation due to the unique skills required and the critical nature of the work. While established specializations remain vital, focusing on emerging niches can provide a competitive edge and open doors to leadership or advanced technical roles.
Emerging specializations often take a few years to become mainstream and generate a significant number of job opportunities, typically 3-5 years from initial adoption to widespread implementation. Pursuing these areas involves a calculated risk, as not all innovations achieve widespread adoption. However, the reward for successful early adoption includes pioneering roles, higher demand, and the chance to shape future industry standards.
Autonomous Lift System Supervisor
As autonomous lift systems become more prevalent in warehouses, construction sites, and even passenger transport, a new need arises for operators who can monitor, troubleshoot, and manage these sophisticated machines. This role involves overseeing multiple autonomous units simultaneously, intervening remotely when anomalies occur, and ensuring seamless operation through intelligent control systems. It shifts the operator's focus from direct physical control to supervisory oversight and data interpretation.
Eco-Efficient Fleet Operator
The increasing emphasis on sustainable practices and energy efficiency within logistics and construction drives demand for operators skilled in managing and optimizing electric and hybrid lift fleets. This specialization involves understanding battery management systems, charging infrastructure, energy consumption analytics, and implementing operational strategies that minimize environmental impact while maximizing efficiency. Operators in this area contribute directly to a company's green initiatives and cost savings.
Smart Lift Data Analyst
With the rise of IoT devices and interconnected machinery, lifts are becoming data-generating assets. A specialized operator can leverage this data to predict maintenance needs, optimize routes, and enhance safety. This involves interpreting telemetry, sensor data, and operational logs to identify patterns, anticipate equipment failures, and suggest improvements. This role transforms a traditional operator into a proactive, data-driven asset manager.
VR/AR Enabled Operations Specialist
Virtual Reality (VR) and Augmented Reality (AR) are increasingly used for training, remote assistance, and complex lift operations in hazardous environments. A VR/AR Enabled Lift Operator specializes in using these technologies for simulated training scenarios, receiving real-time augmented guidance during complex lifts, or even remotely operating machinery in dangerous zones. This combines traditional operational skills with advanced spatial computing literacy.
Pros & Cons of Being a Lift Operator
Making informed career decisions requires a clear understanding of both the benefits and challenges of a specific profession. A career's experience can vary significantly based on factors such as company culture, industry sector, specific specialization, and individual preferences. For example, what one person considers a perk, like working outdoors, another might see as a drawback. Additionally, the pros and cons may shift at different stages of a career, with entry-level roles often presenting different challenges and opportunities than senior positions. This assessment offers an honest, balanced view of the advantages and disadvantages of being a lift operator, helping prospective individuals set realistic expectations and determine if this path aligns with their personal values and lifestyle.
Pros
- Lift operators often receive free or discounted access to the ski resort or amusement park facilities, which is a significant perk for enthusiasts of these activities.
- The job provides a unique opportunity to work outdoors in scenic environments, offering fresh air and views that differ from a typical indoor office setting.
- The role is relatively straightforward to learn, with most training provided on-site, making it accessible to individuals without extensive prior experience or specialized education.
- Lift operators meet a wide variety of people from different backgrounds, which can lead to interesting interactions and opportunities for social engagement.
- This position offers a seasonal work schedule, which can be ideal for students, retirees, or individuals seeking employment that allows for extended periods off during the off-season.
- Working as a lift operator helps develop strong customer service and communication skills through constant interaction with the public, which are valuable in many other roles.
- The job often fosters a strong sense of community and camaraderie among staff, as teams work closely together to ensure smooth and safe operations.
Cons
- Lift operators often work outdoors in all weather conditions, from extreme cold and snow to rain and strong winds, which can be physically demanding and uncomfortable.
- The job involves long periods of standing or sitting in a small booth, which can lead to boredom or monotony during slow periods or on clear, uneventful days.
- Lift operators are typically among the lowest-paid positions at ski resorts or construction sites, with limited opportunities for significant wage increases without moving into supervisory roles.
- The work schedule can be unpredictable and demanding, often requiring early mornings, late evenings, weekends, and holidays, especially during peak seasons.
- While relatively simple, the job carries significant responsibility for rider safety, and any operational error or lapse in attention can have serious consequences.
- Interacting with a constant stream of diverse individuals, some of whom may be impatient or uncooperative, requires strong interpersonal skills and patience, which can be draining.
- Career progression within a lift operator role is limited; advancement usually means transitioning into other departments like ski patrol, maintenance, or management, requiring additional training or experience outside the core role of a lift operator itself, or moving into a different industry entirely where the skills are not directly transferable without further training, making it a stepping stone rather than a long-term career for many individuals who seek significant professional development or higher earning potential.
Frequently Asked Questions
Lift Operators face unique questions around seasonal employment, safety protocols, and guest interaction. This section addresses the most common concerns about entering this role, from required certifications and training to managing work-life balance during peak seasons and understanding career progression.
What are the basic requirements and qualifications to become a Lift Operator?
Becoming a Lift Operator typically requires minimal formal education, often just a high school diploma or equivalent. Most training occurs on the job, focusing heavily on safety procedures, lift mechanics, and guest service. You'll need to pass a practical and written safety test to operate the lifts. Some resorts might require a valid driver's license or specific first aid certifications, but these are generally not prerequisites for entry-level roles.
How long does it take to get hired and become fully trained as a Lift Operator?
The timeline to become a Lift Operator is quite short, usually just a few days to a week of intensive training. After being hired, you'll undergo specific training provided by the resort, covering everything from emergency procedures to daily operational checks. The hiring process itself can take a few weeks as resorts ramp up for the season, so applying early is beneficial.
What are the typical salary expectations and benefits for a Lift Operator?
The salary for Lift Operators varies significantly by resort location and size, but it is generally an hourly wage, often around minimum wage or slightly above. Many operators earn between $12-$18 per hour, with some high-demand or specialized roles paying more. Benefits often include a free ski pass, discounts on food and retail, and sometimes subsidized housing, which can offset the lower hourly pay.
What is the work-life balance like for a Lift Operator, especially during peak seasons?
Work-life balance for a Lift Operator can be challenging during peak seasons, as shifts often start very early in the morning and can extend into the evening, especially on weekends and holidays. You'll work outdoors in all weather conditions. However, off-season offers significant downtime, and during the operating season, you often have access to the mountain for recreation, which can be a major perk for outdoor enthusiasts.
Is the Lift Operator job secure, and what happens in the off-season?
Job security for Lift Operators is seasonal, tied directly to the operating season of ski resorts. While there's high demand during winter, employment typically ends when the snow melts. Some operators transition to summer roles within the resort (e.g., bike park operations, maintenance), but this isn't guaranteed. Building a good reputation can lead to re-hiring year after year.
What are the potential career growth opportunities for a Lift Operator?
Career growth for a Lift Operator often involves moving into supervisory roles, such as Lead Operator, Lift Supervisor, or even Lift Operations Manager. These roles involve more responsibility, training new staff, and managing daily operations. Some operators also transition into other resort departments like maintenance, guest services, or snowmaking, leveraging their knowledge of mountain operations.
What are the biggest challenges and daily tasks involved in being a Lift Operator?
The main challenges include working long hours in diverse and sometimes extreme weather conditions, handling repetitive tasks, and managing guest expectations and safety concerns. You must possess excellent customer service skills and remain vigilant about safety at all times. Physical stamina is also important due to standing for long periods and performing manual tasks.
Can Lift Operators work remotely, or is location flexibility a major consideration?
Lift Operator roles are inherently location-dependent, requiring you to work at a physical ski resort. Remote work is not an option. However, many resorts offer staff housing or assist with finding local accommodation, especially in remote mountain towns. This can be a significant factor when considering where to apply and whether the cost of living is feasible.
Related Careers
Explore similar roles that might align with your interests and skills:
Operator
A growing field with similar skill requirements and career progression opportunities.
Explore career guideRide Operator
A growing field with similar skill requirements and career progression opportunities.
Explore career guideElevator Repair and Maintenance Technician
A growing field with similar skill requirements and career progression opportunities.
Explore career guideHoist Operator
A growing field with similar skill requirements and career progression opportunities.
Explore career guideSki Resort Manager
A growing field with similar skill requirements and career progression opportunities.
Explore career guideAssess your Lift Operator readiness
Understanding where you stand today is the first step toward your career goals. Our Career Coach helps identify skill gaps and create personalized plans.
Skills Gap Analysis
Get a detailed assessment of your current skills versus Lift Operator requirements. Our AI Career Coach identifies specific areas for improvement with personalized recommendations.
See your skills gapCareer Readiness Assessment
Evaluate your overall readiness for Lift Operator roles with our AI Career Coach. Receive personalized recommendations for education, projects, and experience to boost your competitiveness.
Assess your readinessSimple pricing, powerful features
Upgrade to Himalayas Plus and turbocharge your job search.
Himalayas
Himalayas Plus
Himalayas Max
Find your dream job
Sign up now and join over 100,000 remote workers who receive personalized job alerts, curated job matches, and more for free!
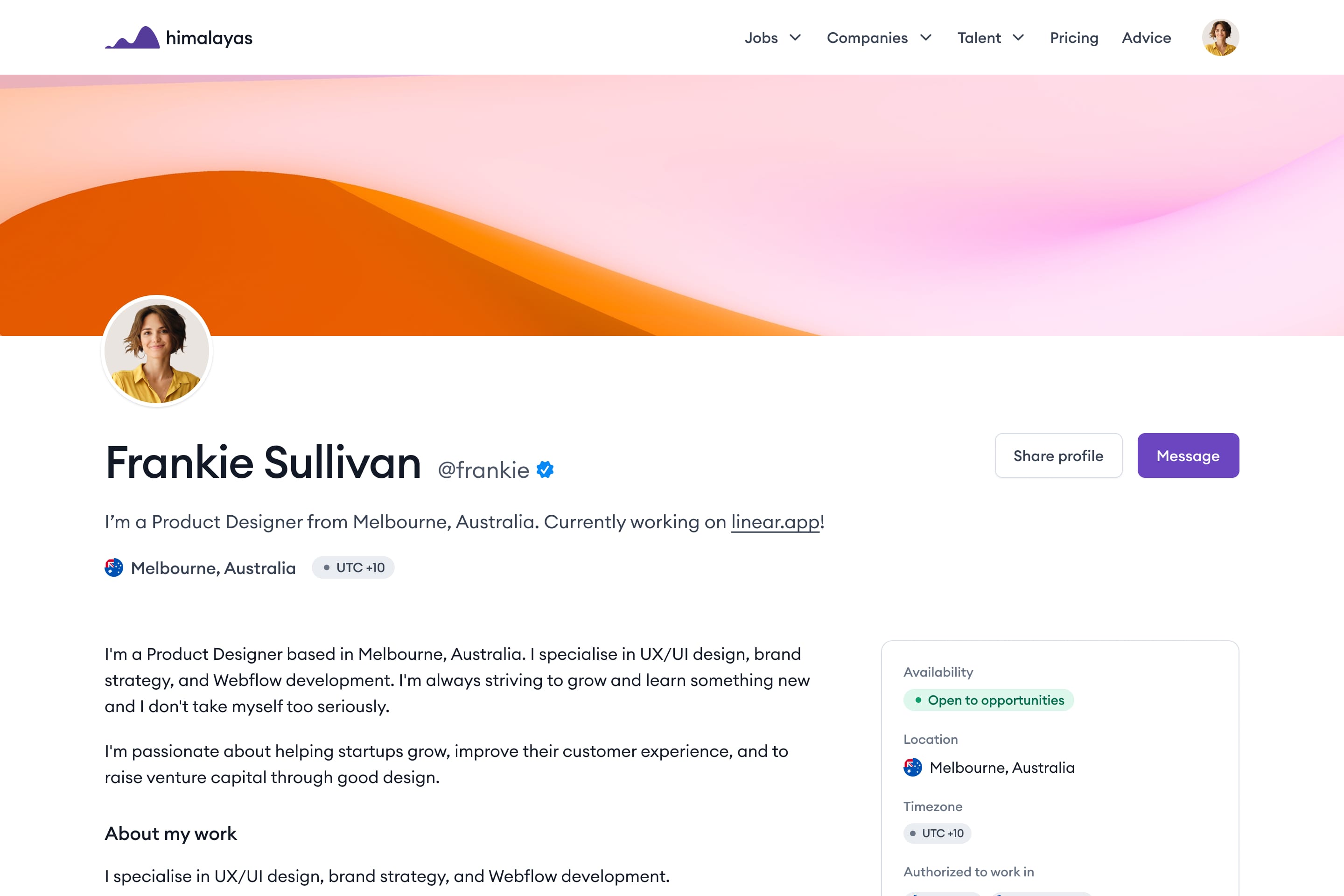