Complete Lacquerer Career Guide
Lacquerers are specialized artisans who apply protective and decorative finishes to a wide array of products, from fine furniture and musical instruments to luxury goods and industrial components. Their meticulous work not only enhances aesthetic appeal but also provides crucial durability and preservation, demanding a unique blend of artistic precision and technical skill. This niche craft offers a rewarding path for those passionate about detailed finishing and material science.
Key Facts & Statistics
Median Salary
$46,650 USD
(source: BLS, May 2023 for Coating, Painting, and Spraying Machine Setters, Operators, and Tenders, specifically for related roles)
Range: $30k - $65k+ USD
Growth Outlook
1%
(little or no change) (source: BLS, 2022-2032 for Coating, Painting, and Spraying Machine Setters, Operators, and Tenders, specifically for related roles)
Annual Openings
≈1,300
openings annually (source: BLS, 2022-2032 for Coating, Painting, and Spraying Machine Setters, Operators, and Tenders, specifically for related roles)
Top Industries
Typical Education
High school diploma or equivalent, with extensive on-the-job training or apprenticeship. Some technical schools offer relevant finishing courses.
What is a Lacquerer?
A Lacquerer is a skilled artisan specializing in the application of lacquer finishes to various surfaces, most commonly wood, metal, and sometimes composites. This role involves meticulous preparation, precise application, and careful finishing to achieve durable, aesthetically pleasing, and often high-gloss surfaces. Lacquerers are responsible for transforming raw or treated materials into highly finished products, enhancing their beauty and protecting them from wear and environmental factors.
Unlike a general painter or varnisher, a Lacquerer possesses specialized knowledge of lacquer chemistry, application techniques for multiple coats, and curing processes that yield a hard, resilient finish. They understand how different lacquers behave on various substrates and how to achieve specific visual effects, such as deep gloss or subtle sheen. Their expertise is crucial in industries ranging from furniture manufacturing and musical instrument crafting to automotive restoration and decorative arts, where the quality of the finish significantly impacts the final product's value and appearance.
What does a Lacquerer do?
Key Responsibilities
- Prepare surfaces by cleaning, sanding, and filling imperfections to ensure a smooth, adhesive base for lacquer application.
- Mix lacquer components, including pigments and thinners, to achieve the desired color, consistency, and finish quality.
- Apply multiple thin coats of lacquer using spray guns, brushes, or rollers, ensuring even coverage and preventing drips or runs.
- Inspect each lacquer coat for flaws such as dust particles, bubbles, or unevenness, performing light sanding or touch-ups as needed between applications.
- Cure lacquered items in controlled environments, monitoring temperature and humidity to optimize drying and hardening processes.
- Polish and buff cured lacquer surfaces to achieve a high-gloss, smooth finish, often using specialized compounds and equipment.
- Maintain and clean application equipment, including spray guns and ventilation systems, to ensure proper function and prevent contamination.
Work Environment
Lacquerers typically work in workshops, manufacturing facilities, or specialized studios. These environments often require excellent ventilation systems due to the fumes from lacquers and solvents. The work can be physically demanding, involving standing for long periods, repetitive motions, and sometimes working in cramped or awkward positions. Collaboration with other craftspeople, such as woodworkers or metalworkers, is common, especially in custom fabrication. The pace of work varies; it can be steady in a production setting or project-based and highly focused in a custom workshop. Precision and attention to detail are paramount, making for a meticulous and often quiet working atmosphere. Safety protocols are strictly followed given the chemical nature of the materials.
Tools & Technologies
Lacquerers primarily use a range of specialized tools and materials for surface preparation and application. This includes various grades of sandpaper, abrasive pads, and fillers for smoothing surfaces. For application, they rely on professional-grade spray guns, air compressors, and a selection of brushes and rollers tailored for lacquer. They also work with different types of lacquer formulations, such as nitrocellulose, acrylic, or polyurethane lacquers, along with appropriate thinners, hardeners, and color pigments. Safety equipment like respirators, gloves, and protective eyewear are essential due to the nature of the chemicals involved. Polishing tools, buffing wheels, and specialized compounds are also part of their daily toolkit.
Lacquerer Skills & Qualifications
Becoming a successful lacquerer involves a distinct blend of artistic talent, meticulous craftsmanship, and specialized technical knowledge. Qualification pathways emphasize hands-on experience and demonstrable skill over purely academic credentials. Entry-level positions often prioritize an individual's aptitude for detail and willingness to learn traditional techniques.
Requirements for a lacquerer vary significantly based on the industry and the type of lacquering work. Furniture restoration, automotive finishing, musical instrument production, and decorative arts each demand specific expertise. Seniority levels dictate increasing expectations for complex surface preparation, advanced application methods, and problem-solving capabilities for challenging materials or intricate designs. Larger companies may offer more structured apprenticeship programs, while smaller, specialized workshops often rely on direct mentorship.
Formal education, such as a degree in fine arts or conservation, can provide a strong theoretical foundation, but practical experience, often gained through apprenticeships or vocational training, remains paramount. Certifications in specific lacquering techniques or material handling, particularly for hazardous substances, enhance a candidate's profile. The field is evolving with new synthetic lacquers and application technologies, requiring continuous learning to master contemporary processes alongside traditional methods. Balancing a deep understanding of historical finishes with the ability to adapt to modern materials is crucial for long-term career success.
Education Requirements
Technical Skills
- Surface Preparation: Cleaning, degreasing, sanding (various grits), filling, and sealing substrates (wood, metal, plastic) to create an ideal base.
- Lacquer Application Techniques: Proficiency in brush application, spray gun operation (HVLP, airless), French polishing, and dipping methods.
- Material Knowledge: Understanding of different lacquer types (nitrocellulose, shellac, polyurethane, acrylic, urushi), their properties, and appropriate solvents/thinners.
- Color Matching and Toning: Ability to mix pigments and dyes to achieve precise color matches and create desired finishes, including translucent and opaque effects.
- Sanding and Polishing: Wet sanding, dry sanding, and buffing techniques to achieve various finishes, from matte to high-gloss mirror finishes.
- Tool and Equipment Maintenance: Cleaning and maintaining spray guns, brushes, sanding equipment, and ventilation systems.
- Safety Protocols: Knowledge of proper handling of hazardous materials, ventilation requirements, and use of personal protective equipment (PPE).
- Defect Identification and Correction: Ability to recognize and rectify common lacquering flaws such as runs, sags, blushing, orange peel, and fisheyes.
- Masking and Taping: Precise application of masking tape and other protective materials for intricate designs or multi-color finishes.
- Repair and Restoration: Techniques for repairing damaged lacquer finishes, including touch-ups, spot repairs, and re-lacquering damaged areas.
Soft Skills
- Attention to Detail: Lacquering demands extreme precision in surface preparation, application, and finishing to achieve flawless results. Even minor imperfections are highly visible.
- Patience: Many lacquering processes involve multiple thin coats, extensive drying times, and meticulous sanding, requiring significant patience and perseverance.
- Manual Dexterity: Fine motor skills are essential for precise brushwork, controlled spraying, and delicate handling of objects, especially when working on intricate designs.
- Problem-Solving: Lacquerers often encounter challenges with material compatibility, environmental factors, or surface defects, requiring analytical thinking to diagnose and resolve issues.
- Color Perception: An acute eye for color matching and consistency is vital for achieving desired aesthetic outcomes and ensuring uniformity across projects.
- Focus and Concentration: Sustained concentration is necessary during application to maintain an even coat and avoid mistakes, particularly over long periods.
- Adaptability: Lacquerers must adapt to varying materials, object shapes, and client specifications, often requiring adjustments to technique or process.
- Discipline: Adherence to strict procedures, safety protocols, and quality control standards is crucial for consistent, high-quality output and personal safety.
How to Become a Lacquerer
Entering the field of lacquering offers various pathways, blending traditional craftsmanship with modern artistic applications. A complete beginner can expect a timeline of 1-3 years to develop foundational skills and build a portfolio, while someone with related artistic or woodworking experience might transition in 6-18 months. The journey often involves a mix of formal training, apprenticeships, and extensive self-directed practice.
Traditional entry routes often involve apprenticeships with master lacquerers, particularly in regions known for specific lacquering traditions like Japan (Urushi) or Vietnam. Non-traditional paths include fine arts programs with a focus on materials, specialized workshops, or even self-taught individuals who demonstrate exceptional skill through their portfolio. Geographic location significantly impacts opportunities; major art centers or regions with historical lacquering traditions offer more avenues than smaller markets. Company size also matters: small artisan studios prioritize hands-on skill and unique styles, while larger furniture restoration companies might focus on production efficiency and specific techniques.
A common misconception is that lacquering is solely about applying a finish; it is a complex art form involving meticulous surface preparation, multi-layered applications, and often intricate decorative work. Building a strong portfolio showcasing diverse techniques and materials is paramount, often outweighing formal degrees. Networking within fine arts, conservation, or furniture restoration communities, along with seeking mentorship, proves crucial for discovering opportunities and gaining recognition. The hiring landscape values proven skill and a keen eye for detail above all else.
Research diverse lacquering traditions and techniques to understand the breadth of this art form. Explore different materials, historical applications, and contemporary uses, identifying areas that align with your artistic interests. This foundational knowledge helps you choose a specific niche within the field.
Acquire fundamental artistic and craft skills through workshops, online courses, or self-study. Focus on drawing, color theory, surface preparation, sanding, and basic finishing techniques, as these are prerequisites for any lacquering work. Dedicate at least 3-6 months to mastering these foundational elements.
Practice various lacquering techniques on different substrates to build practical experience. Experiment with shellac, oil-based lacquers, and modern synthetic lacquers, documenting your process and results for each. Create small projects to refine your application, polishing, and repair skills, aiming for consistency and precision.
Build a focused portfolio showcasing 5-7 high-quality lacquered pieces that demonstrate your skill and artistic vision. Include examples of different techniques, finishes, and levels of complexity, ensuring each piece is meticulously documented with process photos and detailed descriptions. This portfolio will be your primary tool for securing opportunities.
Seek out apprenticeships, internships, or volunteer opportunities with experienced lacquerers, furniture restorers, or art conservation studios. Hands-on experience under a master provides invaluable practical knowledge, industry insights, and networking connections that are difficult to obtain otherwise. Expect to dedicate 6-12 months to such a learning experience.
Network within the fine arts, antique restoration, and custom furniture communities by attending exhibitions, workshops, and trade shows. Connect with established artists, conservators, and gallery owners to learn about potential openings and gain referrals. Informational interviews can also provide valuable guidance and reveal hidden opportunities.
Prepare for job applications by tailoring your resume to highlight your specific lacquering skills, materials expertise, and project experience. Practice articulating your process and artistic philosophy during interviews, demonstrating your passion and attention to detail. Be persistent in your search, as entry-level positions in this specialized field can be competitive.
Step 1
Research diverse lacquering traditions and techniques to understand the breadth of this art form. Explore different materials, historical applications, and contemporary uses, identifying areas that align with your artistic interests. This foundational knowledge helps you choose a specific niche within the field.
Step 2
Acquire fundamental artistic and craft skills through workshops, online courses, or self-study. Focus on drawing, color theory, surface preparation, sanding, and basic finishing techniques, as these are prerequisites for any lacquering work. Dedicate at least 3-6 months to mastering these foundational elements.
Step 3
Practice various lacquering techniques on different substrates to build practical experience. Experiment with shellac, oil-based lacquers, and modern synthetic lacquers, documenting your process and results for each. Create small projects to refine your application, polishing, and repair skills, aiming for consistency and precision.
Step 4
Build a focused portfolio showcasing 5-7 high-quality lacquered pieces that demonstrate your skill and artistic vision. Include examples of different techniques, finishes, and levels of complexity, ensuring each piece is meticulously documented with process photos and detailed descriptions. This portfolio will be your primary tool for securing opportunities.
Step 5
Seek out apprenticeships, internships, or volunteer opportunities with experienced lacquerers, furniture restorers, or art conservation studios. Hands-on experience under a master provides invaluable practical knowledge, industry insights, and networking connections that are difficult to obtain otherwise. Expect to dedicate 6-12 months to such a learning experience.
Step 6
Network within the fine arts, antique restoration, and custom furniture communities by attending exhibitions, workshops, and trade shows. Connect with established artists, conservators, and gallery owners to learn about potential openings and gain referrals. Informational interviews can also provide valuable guidance and reveal hidden opportunities.
Step 7
Prepare for job applications by tailoring your resume to highlight your specific lacquering skills, materials expertise, and project experience. Practice articulating your process and artistic philosophy during interviews, demonstrating your passion and attention to detail. Be persistent in your search, as entry-level positions in this specialized field can be competitive.
Education & Training Needed to Become a Lacquerer
Becoming a Lacquerer involves a unique blend of artistry and technical skill, often requiring hands-on training rather than traditional academic degrees. Formal university programs specifically for lacquer work are rare; instead, specialized workshops, apprenticeships, and vocational training centers form the core educational pathways. A 4-year art degree might cost $40k-$100k+, but it typically focuses on broader art principles, not specific lacquer techniques. Specialized workshops or short courses range from a few hundred dollars to several thousand, with completion times from a few days to several weeks.
Apprenticeships are a highly valued path, offering extensive practical experience and often leading directly to employment. These can last from 2 to 5 years, providing an immersive learning experience with minimal upfront cost, as apprentices often earn a stipend. Employer acceptance of credentials heavily favors demonstrated skill and a portfolio over academic degrees. Continuous learning is crucial, especially in mastering new materials or traditional techniques. The educational needs for a Lacquerer vary by specialization; for instance, furniture restoration requires different expertise than modern art lacquering.
Practical experience is paramount in lacquering, often outweighing theoretical knowledge gained in a classroom setting. Emerging trends in the field, such as the use of new synthetic lacquers or traditional Asian techniques, necessitate ongoing professional development. The cost-benefit of a direct apprenticeship or specialized vocational training generally surpasses that of a broad art degree for this specific career. Industry-specific accreditation for lacquer work is not common; instead, reputation and a strong portfolio serve as quality standards. Many high-quality programs exist in regions with a rich history of lacquer art, such as East Asia or specific European centers known for restoration.
Lacquerer Salary & Outlook
Compensation for a Lacquerer varies significantly based on several factors, extending beyond just the base salary. Geographic location plays a crucial role, with higher wages typically found in regions with a strong demand for specialized finishing work, such as furniture restoration hubs or areas with luxury goods manufacturing. Cost of living in these areas also influences salary scales.
Years of experience and the mastery of specific lacquering techniques, such as French polishing or specialized automotive finishes, create substantial salary variations. A Lacquerer's ability to handle delicate, high-value items or work with rare materials commands premium compensation. Total compensation often includes performance bonuses for project completion or quality, and sometimes profit-sharing, especially in smaller, high-end workshops.
Benefits packages, including health insurance, retirement contributions, and allowances for specialized tools or continuous training, add significant value to the overall compensation. Industry-specific trends, such as the demand for bespoke furniture or restoration services, drive salary growth. Negotiating leverage comes from a proven portfolio of high-quality work and unique skill sets. While remote work is rare for hands-on lacquering, some preparatory or design aspects may offer limited flexibility. International markets, particularly in Europe and Asia, may offer different compensation structures, but figures provided here are in USD.
Salary by Experience Level
Level | US Median | US Average |
---|---|---|
Junior Lacquerer | $35k USD | $38k USD |
Lacquerer | $47k USD | $49k USD |
Senior Lacquerer | $60k USD | $62k USD |
Lead Lacquerer | $72k USD | $75k USD |
Market Commentary
The job market for Lacquerers shows a steady demand driven by specialized sectors and a limited supply of highly skilled artisans. Current trends indicate a particular need in high-end furniture restoration, custom cabinetry, and luxury vehicle detailing. The economic factors affecting this profession include consumer spending on durable goods and luxury items, as well as the preservation of historical artifacts.
The growth outlook for Lacquerers is stable, with projections for a continued need for skilled craftspeople who can perform intricate finishing work. While specific percentage growth is not widely tracked for this niche role, the aging workforce in traditional trades suggests ongoing replacement demand. Emerging opportunities lie in eco-friendly lacquering techniques and the application of advanced protective coatings, which require new skill sets.
The supply and demand dynamics for Lacquerers often lean towards a shortage of qualified candidates, especially those proficient in traditional or highly specialized methods. This imbalance provides leverage for experienced professionals. Automation and AI have minimal impact on the hands-on, artistic nature of lacquering, making it a relatively future-proof profession. The role is generally recession-resistant due to its specialization, as demand for restoration and bespoke items persists even in slower economic periods. Geographic hotspots include major metropolitan areas with strong arts and crafts communities or luxury markets.
Lacquerer Career Path
Career progression for a Lacquerer typically involves a deep mastery of materials, techniques, and artistic application over time. Professionals advance by refining their precision, understanding of various lacquer types, and ability to handle increasingly complex projects. This path often emphasizes individual craftsmanship and technical expertise rather than a traditional management track.
Advancement speed depends on consistent performance, the complexity of work undertaken, and the specific industry, such as furniture restoration, automotive finishes, or fine arts. Specialization in particular lacquer types, like urushi or shellac, significantly influences opportunities. Company size also plays a role; smaller workshops might offer broader exposure, while larger operations might allow for deeper specialization.
Lateral movement often involves shifting between different lacquering applications, for example, from decorative arts to instrument finishing. Networking within artisan communities and continuous learning about new materials and historical techniques are crucial for career growth. Developing a strong portfolio and reputation for quality craftsmanship marks significant progression in this field.
Junior Lacquerer
0-2 yearsPerforms preparatory tasks, including cleaning, sanding, and masking surfaces. Applies initial base coats and simple lacquer layers under direct supervision. Handles basic finishing processes and assists senior lacquerers with material preparation. Works on less intricate pieces, adhering to established procedures.
Key Focus Areas
Developing foundational skills in surface preparation, sanding, and dust control. Learning various application methods such as brushing and spraying. Understanding different lacquer types and their properties. Focus on meticulous execution and following instructions precisely.
Lacquerer
2-5 yearsApplies various lacquer types, including clear coats, solid colors, and simple decorative finishes. Manages the full lacquering process for individual pieces or components with moderate supervision. Identifies and corrects minor imperfections. Collaborates with design or restoration teams to achieve desired aesthetic outcomes.
Key Focus Areas
Mastering multiple lacquer application techniques and achieving consistent, high-quality finishes. Developing problem-solving skills for common lacquering challenges like runs, sags, and dust inclusions. Expanding knowledge of color matching, tinting, and special effects. Beginning to work independently on standard projects.
Senior Lacquerer
5-8 yearsExecutes intricate lacquering projects requiring advanced techniques and precision, such as high-gloss finishes, distressed effects, or specialized patinas. Troubleshoots complex application issues and develops custom solutions. Advises on material selection and process optimization. Often responsible for quality control on finished pieces.
Key Focus Areas
Refining expertise in complex lacquering methods, including multi-layer applications, polishing, and repair. Developing an understanding of advanced material science related to adhesion, durability, and environmental factors. Mentoring junior staff and providing technical guidance. Taking ownership of challenging and high-value projects.
Lead Lacquerer
8+ years total experienceOversees all lacquering operations, ensuring adherence to quality standards and project specifications. Manages project workflows, material procurement, and scheduling for lacquering teams. Acts as the primary technical authority, advising on the most challenging finishes and restoration work. May design and implement new lacquering processes or finishes.
Key Focus Areas
Providing expert consultation on lacquering processes and material compatibility. Leading teams on large-scale or highly specialized projects. Innovating new techniques or adapting historical methods for contemporary applications. Developing client relationships and managing project timelines. Contributing to training and skill development within the workshop.
Junior Lacquerer
0-2 yearsPerforms preparatory tasks, including cleaning, sanding, and masking surfaces. Applies initial base coats and simple lacquer layers under direct supervision. Handles basic finishing processes and assists senior lacquerers with material preparation. Works on less intricate pieces, adhering to established procedures.
Key Focus Areas
Developing foundational skills in surface preparation, sanding, and dust control. Learning various application methods such as brushing and spraying. Understanding different lacquer types and their properties. Focus on meticulous execution and following instructions precisely.
Lacquerer
2-5 yearsApplies various lacquer types, including clear coats, solid colors, and simple decorative finishes. Manages the full lacquering process for individual pieces or components with moderate supervision. Identifies and corrects minor imperfections. Collaborates with design or restoration teams to achieve desired aesthetic outcomes.
Key Focus Areas
Mastering multiple lacquer application techniques and achieving consistent, high-quality finishes. Developing problem-solving skills for common lacquering challenges like runs, sags, and dust inclusions. Expanding knowledge of color matching, tinting, and special effects. Beginning to work independently on standard projects.
Senior Lacquerer
5-8 yearsExecutes intricate lacquering projects requiring advanced techniques and precision, such as high-gloss finishes, distressed effects, or specialized patinas. Troubleshoots complex application issues and develops custom solutions. Advises on material selection and process optimization. Often responsible for quality control on finished pieces.
Key Focus Areas
Refining expertise in complex lacquering methods, including multi-layer applications, polishing, and repair. Developing an understanding of advanced material science related to adhesion, durability, and environmental factors. Mentoring junior staff and providing technical guidance. Taking ownership of challenging and high-value projects.
Lead Lacquerer
8+ years total experienceOversees all lacquering operations, ensuring adherence to quality standards and project specifications. Manages project workflows, material procurement, and scheduling for lacquering teams. Acts as the primary technical authority, advising on the most challenging finishes and restoration work. May design and implement new lacquering processes or finishes.
Key Focus Areas
Providing expert consultation on lacquering processes and material compatibility. Leading teams on large-scale or highly specialized projects. Innovating new techniques or adapting historical methods for contemporary applications. Developing client relationships and managing project timelines. Contributing to training and skill development within the workshop.
Job Application Toolkit
Ace your application with our purpose-built resources:
Global Lacquerer Opportunities
The Lacquerer's role, focusing on applying decorative or protective finishes, translates across various global art, restoration, and manufacturing sectors. International demand exists in fine art conservation, antique restoration, and specialized furniture production, particularly in East Asia and Europe. Cultural nuances significantly impact techniques and materials, while regulatory differences affect material safety and import. Professionals pursue international roles for specialized projects, unique material access, or to preserve traditional techniques. No specific international certifications are broadly recognized, but portfolio and master-level apprenticeships are crucial for global mobility.
Global Salaries
Lacquerer salaries vary significantly by region, experience, and specialization (e.g., art restoration vs. industrial application). In North America, a Lacquerer typically earns USD 35,000-60,000 annually in the United States, and CAD 30,000-55,000 in Canada. These ranges reflect a moderate cost of living. Europe sees diverse compensation; in France, a skilled Lacquerer might earn EUR 28,000-45,000 (USD 30,000-48,000), while in Germany, it could be EUR 30,000-50,000 (USD 32,000-54,000). Southern European countries generally offer lower salaries, but also have a lower cost of living.
Asia-Pacific, especially Japan and China, holds unique significance for lacquer work. In Japan, a master Lacquerer can command JPY 4,000,000-8,000,000 (USD 27,000-54,000), reflecting highly specialized skills and cultural value. China's industrial lacquer market offers CNY 80,000-180,000 (USD 11,000-25,000) for experienced workers, with higher pay for traditional art restoration. Latin America offers fewer structured opportunities, with salaries ranging from USD 10,000-25,000 in countries like Mexico or Brazil, often in artisan workshops.
Salary structures also differ. European contracts often include more vacation time and comprehensive healthcare benefits. North American packages might offer performance bonuses. Taxes and social security contributions vary widely, impacting take-home pay. For instance, high taxes in Western Europe reduce net income more than in some Asian countries. Education and a demonstrated portfolio of specialized techniques significantly influence international compensation, often outweighing formal degrees in this craft-based profession. No international pay scales standardize Lacquerer compensation; it depends on local market demand, skill rarity, and project scope.
Remote Work
International remote work for a Lacquerer is highly limited. The craft is inherently hands-on, requiring direct material application and a specific workshop environment. It is not a digital-first profession. However, some aspects, like client consultations, design planning, or theoretical training, can occur remotely. Digital nomad opportunities for Lacquerers are minimal, as the physical presence for work is essential.
Legal and tax implications for the limited remote aspects would follow general international remote work rules, focusing on where the service is performed versus where the client is located. Time zone considerations are less critical for the physical work itself but apply to remote administrative tasks. Employers typically do not hire Lacquerers for fully remote international roles. Salary expectations for any remote component would align with the client's location rather than the Lacquerer's. Platforms for international remote Lacquerer work are non-existent, given the nature of the craft. Essential equipment includes specialized tools, ventilation, and a dedicated workspace, which cannot be remote.
Visa & Immigration
Lacquerers seeking international work typically apply for skilled worker visas or specialized artisan visas, often tied to specific projects or cultural exchange programs. Popular destinations include Japan, known for traditional lacquerware, and European countries like France or Italy, recognized for furniture restoration. Requirements often include a strong portfolio, letters of invitation from employers or cultural institutions, and proof of financial stability.
Education credential recognition is less formal for this craft; instead, master-level apprenticeships and a demonstrable skill set are paramount. Visa timelines vary from a few weeks to several months. Pathways to permanent residency are rare and usually tied to long-term employment or significant cultural contributions, not a standard professional immigration track. Language requirements depend on the country; for instance, basic Japanese proficiency assists in Japan, while English or the local language is necessary elsewhere. Lacquerers do not typically benefit from fast-track programs. Family visas and dependent rights are generally available under the primary visa holder's status, following standard immigration procedures for the host country.
2025 Market Reality for Lacquerers
Understanding the current market for lacquerers is vital for anyone considering or currently in this highly specialized trade. The landscape for this traditional craft has undergone substantial shifts since 2023, influenced by evolving manufacturing processes and economic factors.
Post-pandemic shifts saw a brief spike in interest for home restoration, but this faded as economic pressures mounted. The rise of AI and automation has not directly impacted the manual skill of lacquering, but it has accelerated the decline of demand for hand-finished products in favor of machine-applied alternatives. Market realities for lacquerers vary significantly by experience level, with entry-level opportunities being almost non-existent, and by region, with only a few urban centers sustaining a viable market.
Current Challenges
Skilled lacquerers face a shrinking market for traditional bespoke finishes. Mass-produced furniture and industrial coatings have largely replaced demand for artisanal hand-applied lacquer.
Competition for the few remaining high-end restoration or custom art projects is fierce, often coming from established, niche studios. Economic downturns reduce discretionary spending on luxury or antique item restoration, directly impacting workflow.
Growth Opportunities
Despite market shrinkage, specific opportunities for lacquerers persist in highly specialized niches. High-end antique furniture restoration and conservation offer consistent, albeit limited, work, particularly for pieces requiring historical accuracy and delicate handling.
The luxury goods sector, including bespoke automotive interiors or custom musical instruments, represents a small but lucrative area. Here, clients prioritize unique, hand-finished quality that machines cannot replicate. Lacquerers with expertise in exotic materials or specialized finishes find strong demand in these segments.
Opportunities exist for those who can adapt traditional skills to modern artistic applications or collaborate with contemporary designers creating unique, hand-finished art pieces. Developing a strong portfolio showcasing diverse techniques and a deep understanding of material science provides a competitive edge. Strategic career moves involve relocating to major art and design hubs or establishing a reputation within a specific, high-end clientele.
Current Market Trends
Demand for lacquerers has significantly declined in 2025, largely due to shifts in manufacturing and consumer preferences. Most furniture and automotive finishes now use spray application or industrial processes, not traditional hand-lacquering techniques.
The remaining market for lacquerers exists primarily in niche areas: high-end antique restoration, custom luxury furniture, musical instrument finishing, or specialized art conservation. These roles are scarce and often require extensive experience with historical techniques and materials.
Economic conditions directly impact this field; during downturns, consumers defer spending on luxury goods or antique restoration, reducing project availability. Generative AI and automation have minimal direct impact on the manual skill of a lacquerer, but they influence broader market trends by making mass production more efficient and cost-effective, further marginalizing traditional methods.
Employer requirements now heavily emphasize conservation skills, color matching, and a deep understanding of historical lacquer types. Salary trends are stagnant or declining for general skills, with higher compensation only for highly specialized, rare expertise. Geographic variations are stark; opportunities are concentrated in major metropolitan areas with high concentrations of wealth, art collectors, or luxury goods manufacturers.
Emerging Specializations
Technological advancements and evolving consumer demands are continually reshaping traditional crafts, creating new specialization opportunities for lacquerers. Understanding these shifts and positioning oneself early in emerging areas is crucial for career advancement in 2025 and beyond. These future-oriented paths often command premium compensation and offer significant career growth, moving beyond conventional restoration or decorative work.
While established lacquer techniques remain valuable, focusing on cutting-edge applications allows professionals to align with future market needs. This strategic choice helps to secure a competitive edge. Emerging specializations typically gain significant traction within three to five years, transitioning from niche markets to mainstream demand, creating substantial job opportunities.
Professionals considering these nascent fields should weigh the risk and reward. Early adoption requires continuous learning and adaptability, yet it offers the potential for pioneering new artistic and commercial frontiers. Balancing the pursuit of innovative techniques with a strong foundation in traditional skills ensures long-term career resilience and expands a lacquerer's market value.
Advanced Industrial Lacquer Finishing
Interactive & Smart Lacquer Coatings
Sustainable & Bio-Based Lacquer Formulation
Digital Fabrication & Lacquer Hybridization
Integrated Conservation of Multi-Material Lacquer Artifacts
Pros & Cons of Being a Lacquerer
Making informed career decisions requires understanding both the benefits and challenges of a profession. The experience of a lacquerer can vary significantly based on the industry, company culture, specific materials used, and the individual's specialization. Pros and cons may also shift across different career stages, from an apprentice learning the ropes to a seasoned master craftsman. What one person finds appealing, such as meticulous detail work, another might find tedious. This assessment provides a realistic outlook on the advantages and genuine difficulties of working as a lacquerer, helping individuals set appropriate expectations and determine if this path aligns with their personal values and lifestyle preferences.
Pros
- Developing highly specialized manual skills in surface preparation, application, and finishing, which are valued in niche markets like luxury furniture, musical instruments, and antique restoration.
- The satisfaction of transforming raw or damaged materials into beautiful, high-gloss, or protective finished products provides a strong sense of accomplishment and artistic fulfillment.
- Working with a variety of materials and projects keeps the job interesting, from wood and metal to plastics, each requiring unique techniques and approaches to achieve the desired finish.
- Opportunities for self-employment or specialized contract work allow for greater autonomy in project selection and scheduling, appealing to those who prefer independent work.
- There is a continuous learning curve as new lacquer technologies and application methods emerge, providing ongoing intellectual stimulation and opportunities to refine one's craft.
- The ability to work on unique and high-value items, such as custom-made furniture, vintage cars, or intricate art pieces, offers a sense of prestige and involvement in preserving craftsmanship.
- The tangible results of a lacquerer's work are visually appealing, allowing for a clear demonstration of skill and artistry, which can be a source of pride and recognition within the craft community.
Cons
- Exposure to hazardous chemicals, including solvents and lacquers, requires strict adherence to safety protocols and proper ventilation to prevent respiratory issues and skin irritation.
- The work environment often involves strong odors from the lacquers and chemicals, which can be unpleasant for some individuals and may require wearing respirators for prolonged periods.
- Repetitive motions involved in sanding, spraying, and polishing can lead to musculoskeletal strain and injuries over time, especially in the hands, wrists, and shoulders.
- Achieving a flawless finish demands extreme precision, patience, and attention to detail, as even minor imperfections are highly visible and can ruin a piece.
- The demand for skilled lacquerers can be niche and dependent on specific industries like furniture making, automotive restoration, or fine art, potentially limiting widespread job opportunities.
- Working with delicate and valuable items means any mistake can be costly, leading to significant financial loss or damage to irreplaceable pieces, increasing pressure on the lacquerer.
- Income can fluctuate based on project availability and the type of work, with less consistency compared to salaried positions, especially for freelance or specialized contract work, making financial planning challenging at times and requiring a steady influx of new clients or projects to maintain a stable income flow.
Frequently Asked Questions
Lacquerers face distinct challenges balancing artistic precision with the physical demands of the craft. This section addresses key questions about entering this specialized field, from mastering traditional techniques to understanding the market for lacquered goods and managing health considerations.
What are the typical entry requirements or educational paths to become a Lacquerer?
Formal education is not strictly required, but apprenticeships or vocational training are highly recommended to become a skilled lacquerer. Most learn through hands-on experience under master craftsmen, which can take several years. Some art schools or specialty workshops offer courses focusing on traditional or modern lacquering techniques, providing a foundational understanding of materials and processes.
How long does it take to become a skilled Lacquerer and work independently?
Becoming proficient enough to work independently as a lacquerer typically takes 3-5 years of dedicated practice or apprenticeship. Mastery, however, can take a decade or more, as the craft involves intricate techniques, deep material knowledge, and a developed artistic sensibility. Your progress depends on consistent practice, the quality of your mentorship, and your natural aptitude for precision work.
What are the salary expectations for a Lacquerer, and how does it vary by experience?
Income for lacquerers varies widely based on skill level, specialization, and market demand. Entry-level positions or apprenticeships might offer modest wages. Highly skilled lacquerers specializing in restoration, custom furniture, or fine art can command significant fees for their work, potentially earning a comfortable living. Building a reputation and client base is crucial for higher earning potential.
What is the typical work-life balance like for a Lacquerer, considering the demands of the craft?
The work-life balance for a lacquerer can be demanding, especially when working on complex projects with tight deadlines. The craft often requires long hours of meticulous, focused work, which can be physically taxing due to posture and repetitive motions. Self-employed lacquerers have more control over their schedule but also manage business aspects like marketing and client acquisition.
Is there good job security or market demand for skilled Lacquerers today?
Job security in lacquering depends on the niche you pursue. Restoration of antiques, custom furniture, and high-end artistic pieces often have consistent demand from discerning clients. While the field is specialized, skilled lacquerers are rare, which can create strong job security for those with proven expertise. Networking and maintaining a strong portfolio are key to stability.
What are the potential career growth and advancement opportunities for a Lacquerer?
Career growth for a lacquerer often means progressing from apprentice to master craftsman, gaining recognition for your unique style or specialization. You can open your own studio, teach workshops, or collaborate with designers and architects on high-profile projects. Specializing in rare techniques or historical restoration can also open up new opportunities and increase your value in the market.
What are the main health and safety concerns Lacquerers face, and how are they managed?
Lacquerers frequently encounter health and safety concerns due to exposure to solvents, dust, and fine particulates. Proper ventilation, personal protective equipment (PPE), and adherence to safety protocols are essential to mitigate risks like respiratory issues or skin irritation. The meticulous nature of the work can also lead to eye strain or musculoskeletal discomfort over time.
Can a Lacquerer work remotely, or is it primarily an in-person profession?
Working as a lacquerer is primarily hands-on and requires a dedicated studio or workshop space. While some administrative tasks or client consultations can be done remotely, the actual lacquering process demands a physical setup with proper ventilation, specific temperature and humidity controls, and specialized tools. Therefore, it is not a remote-friendly profession in its core practical aspects.
Related Careers
Explore similar roles that might align with your interests and skills:
Cabinet Finisher
A growing field with similar skill requirements and career progression opportunities.
Explore career guideFloor Refinisher
A growing field with similar skill requirements and career progression opportunities.
Explore career guideHardwood Finisher
A growing field with similar skill requirements and career progression opportunities.
Explore career guideLacquer Spray Booth Operator
A growing field with similar skill requirements and career progression opportunities.
Explore career guideWood Cabinet Finisher
A growing field with similar skill requirements and career progression opportunities.
Explore career guideAssess your Lacquerer readiness
Understanding where you stand today is the first step toward your career goals. Our Career Coach helps identify skill gaps and create personalized plans.
Skills Gap Analysis
Get a detailed assessment of your current skills versus Lacquerer requirements. Our AI Career Coach identifies specific areas for improvement with personalized recommendations.
See your skills gapCareer Readiness Assessment
Evaluate your overall readiness for Lacquerer roles with our AI Career Coach. Receive personalized recommendations for education, projects, and experience to boost your competitiveness.
Assess your readinessLand your dream job with Himalayas Plus
Upgrade to unlock Himalayas' premium features and turbocharge your job search.
Himalayas
Himalayas Plus
Himalayas is trusted by hundreds of thousands of job seekers every month
Get started for freeNo credit card required
Find your dream job
Sign up now and join over 100,000 remote workers who receive personalized job alerts, curated job matches, and more for free!
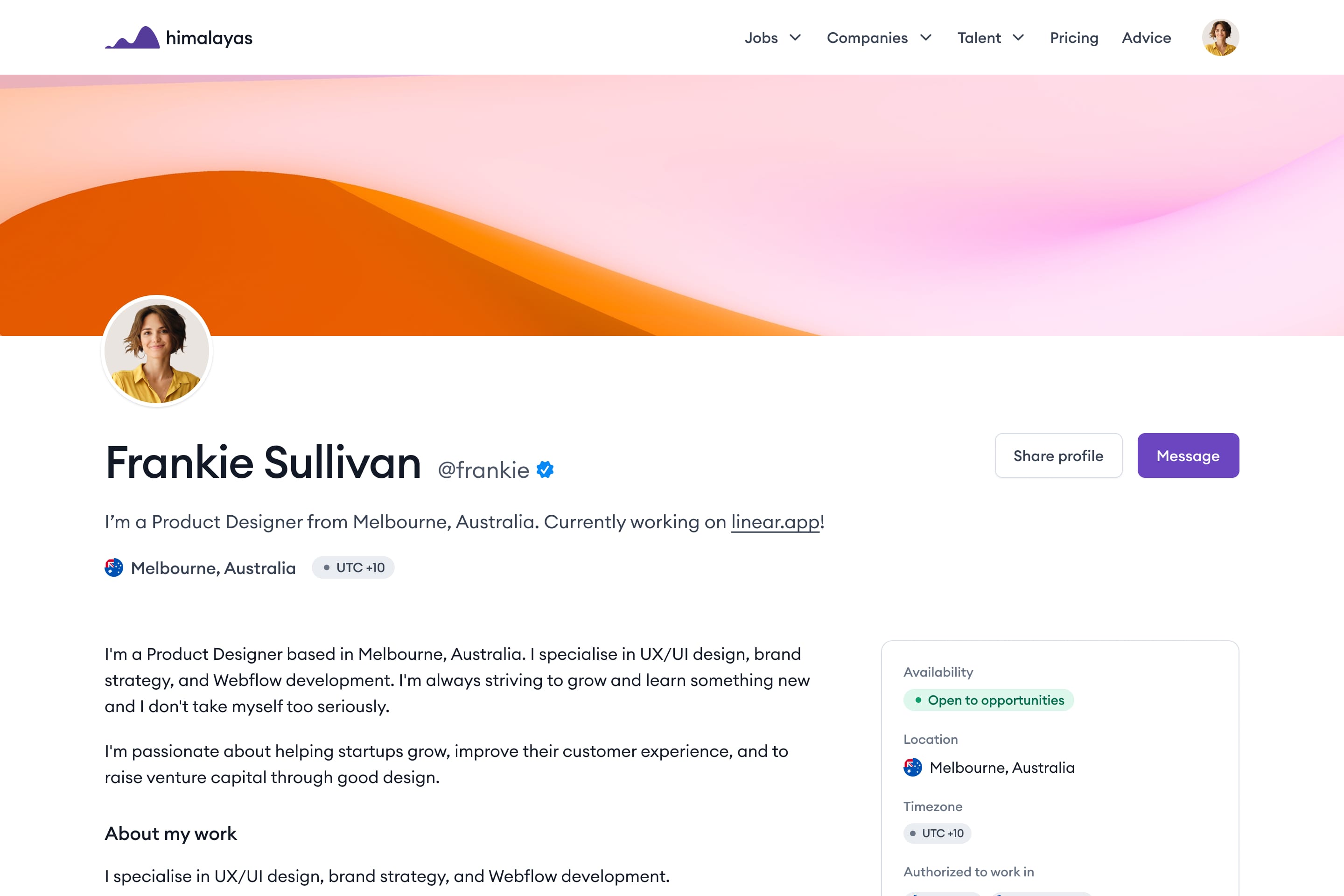