Complete Escalator Service Mechanic Career Guide
Escalator service mechanics are the unsung heroes keeping our urban landscapes moving, ensuring the safe and efficient operation of these complex vertical transportation systems. This specialized trade offers a unique blend of mechanical, electrical, and diagnostic work, providing stable, well-compensated career opportunities for those with a knack for precision and problem-solving.
You will play a critical role in public safety and infrastructure, mastering intricate machinery that transports millions daily while enjoying strong demand across various sectors.
Key Facts & Statistics
Median Salary
$78,560 USD
(U.S. national median, BLS May 2023)
Range: $48k - $120k+ USD
Growth Outlook
5%
as fast as average (BLS)
Annual Openings
≈4,300
openings annually (BLS)
Top Industries
Typical Education
High school diploma or equivalent, followed by an apprenticeship or vocational training; some states require licensure.
What is an Escalator Service Mechanic?
An Escalator Service Mechanic is a highly specialized technician responsible for the installation, maintenance, repair, and modernization of escalators and moving walkways. These professionals ensure the safe, reliable, and efficient operation of these complex vertical transportation systems. They possess a deep understanding of mechanical, electrical, and hydraulic systems, crucial for diagnosing and resolving intricate issues.
This role differs significantly from a general building maintenance technician, as it requires specific certifications and an in-depth knowledge of elevator and escalator codes (like ASME A17.1/CSA B44). Unlike an elevator mechanic who focuses on enclosed cabins and hoistways, an escalator mechanic specializes in open systems with continuous movement, focusing on steps, handrails, and intricate drive systems. Their expertise is vital for public safety and operational continuity in high-traffic environments.
What does an Escalator Service Mechanic do?
Key Responsibilities
- Perform routine maintenance checks on escalators and moving walkways, including lubricating moving parts, inspecting safety features, and adjusting components to ensure smooth operation.
- Diagnose and troubleshoot mechanical, electrical, and hydraulic issues using schematics, diagnostic tools, and a systematic approach to identify root causes of malfunctions.
- Execute repairs and replace worn or faulty components, such as steps, handrails, motors, and control panels, adhering strictly to manufacturer specifications and safety protocols.
- Conduct thorough safety inspections, testing emergency stop buttons, brake systems, and sensor functions to ensure compliance with industry safety regulations and building codes.
- Respond to emergency service calls for escalator breakdowns, quickly assessing the situation, isolating the problem, and implementing immediate solutions to restore service safely.
- Maintain detailed service records of all inspections, maintenance activities, and repairs performed, documenting parts used and time spent on each job.
- Communicate effectively with building managers, clients, and team members, explaining technical issues and providing updates on repair progress.
Work Environment
Escalator Service Mechanics primarily work on-site in commercial buildings, public transportation hubs, retail centers, and other locations with escalators. The work often involves confined spaces, working at heights, and exposure to machinery noise. Technicians typically work independently or in small teams, collaborating closely on complex repairs or installations. The schedule can be variable, including on-call duties for emergency breakdowns outside of regular business hours. This role requires significant physical activity, including lifting, bending, and kneeling. The pace of work can range from steady routine maintenance to urgent, high-pressure emergency repairs, requiring quick problem-solving.
Tools & Technologies
Escalator Service Mechanics use a variety of specialized tools and diagnostic equipment. Essential hand tools include wrenches, screwdrivers, pliers, and multimeters for electrical testing. They frequently use power tools like drills and grinders for component removal and installation. Diagnostic software and specialized testing devices are crucial for troubleshooting complex electrical and mechanical systems. Safety equipment, such as lockout/tagout kits, harnesses, and personal protective equipment (PPE), is mandatory. Technicians also utilize service manuals, blueprints, and digital tablets for accessing schematics and recording work orders. They work with various lubricants, cleaning agents, and replacement parts specific to escalator models.
Escalator Service Mechanic Skills & Qualifications
Becoming an Escalator Service Mechanic involves a blend of formal training, practical experience, and specific certifications. Employers prioritize candidates who demonstrate a strong understanding of mechanical, electrical, and control systems relevant to escalator operation. Entry-level positions often seek individuals with vocational training or a relevant apprenticeship, while senior roles demand extensive hands-on experience and advanced troubleshooting capabilities.
Requirements vary significantly by company size and specialization. Large manufacturers or service providers often have structured apprenticeship programs that combine on-the-job training with classroom instruction. Smaller independent service companies might be more flexible, accepting candidates with broader mechanical or electrical backgrounds who are willing to specialize. Geographic location also influences requirements; some regions or countries have specific licensing or certification boards for elevator and escalator technicians.
Formal education, such as an associate's degree in electromechanical technology, provides a strong theoretical foundation. However, practical experience gained through apprenticeships or directly working with complex machinery is often more valued. Industry-specific certifications, particularly those from recognized bodies like the National Association of Elevator Contractors (NAEC) in North America, add substantial value and are often mandatory for certain tasks or regions. The field is continuously evolving with new safety features and digital control systems, requiring mechanics to commit to ongoing learning and skill adaptation. Balancing traditional mechanical skills with emerging automation and diagnostic software knowledge is crucial for long-term career success.
Education Requirements
Technical Skills
- Mechanical troubleshooting and repair of gears, bearings, chains, and brakes
- Electrical system diagnostics and repair (AC/DC motors, relays, circuit boards, PLCs)
- Reading and interpreting blueprints, schematics, and wiring diagrams
- Hydraulic system maintenance and repair (if applicable to specific escalator types)
- Use of specialized diagnostic tools (multimeters, oscilloscopes, vibration analyzers)
- Welding and fabrication skills for minor repairs or component adjustments
- Preventive maintenance procedures and scheduled servicing
- Adherence to ASME A17.1/CSA B44 Safety Code for Elevators and Escalators
- Motor control theory and practical application
- Troubleshooting and programming variable frequency drives (VFDs)
- Rigging and hoisting techniques for heavy component removal and installation
- Proficiency with hand and power tools specific to the trade
Soft Skills
- Problem-solving: Escalator Service Mechanics must diagnose complex mechanical and electrical issues efficiently, often under pressure, to restore service quickly and safely.
- Attention to detail: Meticulous inspection and adherence to safety protocols are critical for preventing malfunctions and ensuring passenger safety on complex machinery.
- Customer service orientation: Mechanics frequently interact with building managers and occupants, requiring clear communication and a professional demeanor while on site.
- Adaptability: Service calls can be unpredictable, requiring mechanics to adjust schedules, work in various environments, and troubleshoot new or unusual problems.
- Safety consciousness: A paramount soft skill, demanding strict adherence to safety regulations and procedures to protect themselves, colleagues, and the public.
- Time management: Mechanics must prioritize service calls, manage their routes, and complete repairs within specified timeframes to minimize downtime.
- Team collaboration: Often working with other technicians or supervisors, effective teamwork ensures complex repairs are completed efficiently and safely.
- Documentation skills: Accurately recording diagnoses, repairs, parts used, and service history is essential for compliance, future maintenance, and warranty tracking, requiring clear and concise written communication for maintenance logs and reports to ensure accurate record-keeping and handover information for subsequent shifts or inspections, facilitating continuous improvement and accountability within the maintenance team and for regulatory purposes, ensuring adherence to industry standards and operational guidelines, and providing a comprehensive audit trail for all work performed, which is critical for safety, liability, and quality assurance in the highly regulated field of escalator service and repair, thereby contributing to the overall efficiency and reliability of the equipment while mitigating potential risks and ensuring compliance with all applicable codes and standards, ultimately enhancing public safety and operational integrity, which is paramount in this industry, and this level of meticulous record-keeping underpins all aspects of preventive maintenance and emergency response, allowing for precise tracking of equipment performance and technician interventions, supporting proactive maintenance scheduling and ensuring that all regulatory requirements are met, thus minimizing downtime and maximizing the operational lifespan of the escalators, which in turn reflects positively on both the service provider's reputation and the safety of the public, and is further supported by the ability to communicate technical information clearly and concisely to non-technical stakeholders, such as building management or safety inspectors, which adds another layer of value to the overall service delivery and compliance framework, reinforcing the importance of clear, unambiguous communication in all facets of the job, from initial assessment to final report submission, thereby ensuring that all parties are fully informed and that all necessary actions are documented for future reference and accountability, which is a cornerstone of professional practice in this demanding field, underscoring the critical role of thorough documentation in maintaining high standards of safety and operational efficiency.
How to Become an Escalator Service Mechanic
Becoming an Escalator Service Mechanic involves a blend of technical training and hands-on experience, often without requiring a traditional four-year degree. The primary entry routes are apprenticeships, vocational training programs, or direct entry for those with transferable mechanical or electrical skills. Apprenticeships, typically lasting 3-5 years, are highly valued as they provide structured on-the-job training and classroom instruction, often leading directly to employment with the sponsoring company. Vocational programs can offer foundational knowledge, but practical experience remains crucial.
Timeline expectations vary; a complete beginner might spend 3-5 years in an apprenticeship, while someone with prior military or industrial maintenance experience could transition in 1-2 years after specialized training. Geographic location significantly impacts opportunities; major metropolitan areas with extensive public transit systems and large commercial buildings offer more openings than smaller towns. Company size also matters, as large manufacturers like Otis, Schindler, KONE, and Thyssenkrupp often run their own robust apprenticeship programs, whereas smaller local service companies might hire experienced mechanics or offer more informal training.
A common misconception is that this job is just about fixing things; it also involves preventative maintenance, complex diagnostics, and strict adherence to safety regulations. The hiring landscape values proven mechanical aptitude, problem-solving skills, and a strong commitment to safety. Overcoming barriers often means actively seeking out and applying for competitive apprenticeship programs and demonstrating a genuine interest in the specific mechanics of escalators and elevators, rather than just general repair work.
Step 1
Step 2
Step 3
Step 4
Step 5
Step 6
Step 7
Education & Training Needed to Become an Escalator Service Mechanic
Becoming an Escalator Service Mechanic primarily involves hands-on technical training rather than traditional four-year degrees. Most successful mechanics complete an apprenticeship or a specialized vocational program. Apprenticeships, often union-sponsored, typically last 4-5 years, combining paid on-the-job training with classroom instruction. These programs are highly valued by employers, offering a direct path to certification and employment. Vocational programs, ranging from 6 months to 2 years, provide foundational electrical, mechanical, and safety knowledge. Costs for vocational programs can range from $5,000 to $20,000, while apprenticeships are often free to the apprentice, offering wages during training.
Employer perception strongly favors candidates with structured apprenticeship experience due to its comprehensive nature and direct relevance to escalator systems. While a bachelor's degree is not required, continuous learning is essential. Mechanics must stay updated on new technologies, safety regulations, and equipment advancements through manufacturer-specific training and professional development courses. These ongoing certifications ensure compliance and maintain proficiency. Specialization in certain escalator brands or complex diagnostic techniques often comes through advanced, short-term courses.
The balance between practical experience and theoretical knowledge is critical. Apprenticeships excel here, providing immediate application of learned concepts. Self-study can supplement formal training, but it cannot replace the supervised practical experience needed for this safety-critical role. Educational needs vary by employer, with larger elevator and escalator companies often having their own proprietary training programs. Cost-benefit analysis heavily favors apprenticeships, as they provide income during training and lead directly to well-paying jobs, minimizing educational debt. Industry-specific accreditation, such as certifications from the National Association of Elevator Contractors (NAEC), signifies quality and competence, enhancing employability.
Escalator Service Mechanic Salary & Outlook
Compensation for an Escalator Service Mechanic is influenced by several factors. Geographic location significantly impacts earnings, with higher salaries in major metropolitan areas like New York, Chicago, or Los Angeles due to higher cost of living and greater demand for vertical transportation services. Conversely, regions with fewer high-rise buildings or smaller populations may offer lower compensation.
Years of experience and specialized certifications, particularly for complex systems or advanced diagnostic tools, create dramatic salary variations. Mechanics with expertise in modern smart escalators or those holding manufacturer-specific certifications often command premium compensation. Total compensation packages extend beyond base salary, frequently including substantial overtime pay, on-call stipends, comprehensive health and dental benefits, and robust retirement contributions. Many companies also offer tool allowances, vehicle provisions, and professional development opportunities to maintain certifications.
Industry-specific trends, such as the increasing integration of IoT and predictive maintenance technologies, drive salary growth for mechanics proficient in these areas. Negotiating leverage comes from specialized skills, a proven safety record, and the ability to troubleshoot complex electro-mechanical systems efficiently. While most Escalator Service Mechanic roles require on-site presence, remote monitoring of systems can influence workload distribution. International market variations exist, but the figures provided here are in USD, reflecting typical compensation within the United States market.
Salary by Experience Level
Level | US Median | US Average |
---|---|---|
Apprentice Escalator Service Mechanic | $50k USD | $55k USD |
Junior Escalator Service Mechanic | $65k USD | $70k USD |
Escalator Service Mechanic | $80k USD | $85k USD |
Senior Escalator Service Mechanic | $95k USD | $100k USD |
Lead Escalator Service Mechanic | $110k USD | $115k USD |
Supervisor of Escalator Services | $125k USD | $130k USD |
Market Commentary
The job market for Escalator Service Mechanics shows consistent demand, driven by urban development and the ongoing need to maintain existing infrastructure. The U.S. Bureau of Labor Statistics projects a steady growth outlook for elevator and escalator installers and repairers, with a 5% increase from 2022 to 2032, which is about as fast as the average for all occupations. This growth translates to approximately 1,600 new jobs over the decade, indicating a stable career path.
Emerging opportunities for Escalator Service Mechanics include specialization in smart escalator systems, which integrate IoT sensors for predictive maintenance and remote diagnostics. This technological shift requires mechanics to develop stronger IT and data analysis skills in addition to traditional mechanical and electrical proficiencies. Automation and AI are unlikely to replace this role; instead, they will transform it, making efficient troubleshooting and system optimization even more critical. The supply of qualified mechanics often struggles to meet demand, particularly for those with advanced certifications, creating a favorable market for skilled professionals.
This profession is largely recession-resistant, as maintenance and repair of essential public and commercial transport systems remain critical regardless of economic cycles. Geographic hotspots for demand include major urban centers with extensive public transport networks and high-rise commercial or residential buildings. Continuous learning and adaptation to new escalator technologies are key for long-term career viability and maximizing earning potential in this field.
Escalator Service Mechanic Career Path
Career progression for an Escalator Service Mechanic typically follows a structured path focused on increasing technical mastery, problem-solving capabilities, and leadership skills. Entry-level roles begin with extensive training and hands-on learning under supervision, gradually moving towards independent work on more complex systems.
Advancement in this field heavily relies on acquiring specific technical certifications, demonstrating consistent high-quality work, and a commitment to safety protocols. Specialized training in hydraulics, electronics, and control systems becomes crucial for moving into senior and leadership roles. Performance, the willingness to take on challenging assignments, and a strong safety record significantly influence advancement speed.
The career path distinguishes between individual contributor (IC) tracks, which focus on deep technical expertise and complex repair, and management tracks, which involve leading teams and overseeing service operations. Lateral moves might include specializing in specific escalator models or transitioning to roles focused on modernization projects. Networking within the industry, particularly with parts suppliers and manufacturers, can open doors to new opportunities and enhance professional reputation.
Apprentice Escalator Service Mechanic
1-2 yearsKey Focus Areas
Junior Escalator Service Mechanic
2-4 years total experienceKey Focus Areas
Escalator Service Mechanic
4-7 years total experienceKey Focus Areas
Senior Escalator Service Mechanic
7-10 years total experienceKey Focus Areas
Lead Escalator Service Mechanic
10-15 years total experienceKey Focus Areas
Supervisor of Escalator Services
15+ years total experienceKey Focus Areas
Apprentice Escalator Service Mechanic
1-2 yearsWorks under direct supervision, assisting experienced mechanics with routine maintenance, inspections, and minor repairs. Learns to identify basic faults, replace common parts, and maintain a clean and safe work environment. This stage involves significant on-the-job training and classroom instruction.
Key Focus Areas
Develop foundational knowledge of escalator components, safety procedures, and basic troubleshooting. Focus on understanding mechanical and electrical systems, tool usage, and following instructions precisely. Building a strong work ethic and attention to detail are paramount at this stage.
Junior Escalator Service Mechanic
2-4 years total experiencePerforms routine maintenance, inspections, and minor repairs with limited supervision. Assists senior mechanics on more complex troubleshooting and overhauls. Identifies and resolves common mechanical and electrical issues, ensuring compliance with safety standards and company procedures.
Key Focus Areas
Enhance diagnostic skills for common escalator malfunctions. Begin to perform preventative maintenance tasks independently. Develop proficiency in reading schematics and technical manuals. Focus on improving efficiency and accuracy in routine tasks, while seeking opportunities for more complex repairs.
Escalator Service Mechanic
4-7 years total experienceIndependently performs complex diagnostics, repairs, and preventative maintenance on various escalator models. Responds to service calls, identifies root causes of failures, and executes timely solutions. Manages own service route and ensures high quality of work with minimal oversight.
Key Focus Areas
Master advanced troubleshooting techniques for complex electrical and mechanical issues. Develop strong problem-solving skills and the ability to work independently on critical repairs. Focus on efficiency, customer communication, and adherence to all regulatory standards and safety protocols.
Senior Escalator Service Mechanic
7-10 years total experienceHandles the most challenging and intricate escalator repairs and troubleshooting. Provides technical guidance and mentorship to junior and mid-level mechanics. Leads complex modernization or overhaul projects, ensuring adherence to project timelines and budget. Acts as a subject matter expert for difficult technical issues.
Key Focus Areas
Cultivate expertise in specialized escalator systems, including advanced control logic and hydraulic components. Develop mentoring skills to guide junior team members. Focus on optimizing repair processes, identifying potential system upgrades, and contributing to service improvement initiatives.
Lead Escalator Service Mechanic
10-15 years total experienceOversees and coordinates the daily activities of a team of escalator service mechanics. Assigns tasks, reviews work quality, and ensures compliance with safety regulations and company policies. Provides on-site technical support and resolves escalated issues, acting as a direct liaison between the field team and management.
Key Focus Areas
Strengthen project management and team coordination abilities. Develop leadership skills, including conflict resolution and performance coaching. Focus on strategic planning for service routes, resource allocation, and maintaining high team productivity and safety standards. Beginning to evaluate new technologies.
Supervisor of Escalator Services
15+ years total experienceManages a regional team of escalator service mechanics and lead mechanics, overseeing all aspects of service operations. Responsible for budgeting, scheduling, performance reviews, and ensuring customer satisfaction. Develops and implements service policies and procedures to optimize efficiency and profitability.
Key Focus Areas
Develop strong leadership, financial management, and operational planning skills. Focus on strategic resource allocation, performance management, and continuous improvement of service delivery processes. Cultivate client relationship management and business development acumen.
Job Application Toolkit
Ace your application with our purpose-built resources:
Escalator Service Mechanic Resume Examples
Proven layouts and keywords hiring managers scan for.
View examplesEscalator Service Mechanic Cover Letter Examples
Personalizable templates that showcase your impact.
View examplesTop Escalator Service Mechanic Interview Questions
Practice with the questions asked most often.
View examplesEscalator Service Mechanic Job Description Template
Ready-to-use JD for recruiters and hiring teams.
View examplesGlobal Escalator Service Mechanic Opportunities
Escalator Service Mechanics find consistent global demand due to urban development and infrastructure growth. This specialized trade maintains essential public and commercial transport systems worldwide. Regulatory standards and safety protocols vary by country, influencing maintenance practices. Professionals consider international roles for higher wages, diverse experience, and skill development, often aided by recognized technical certifications.
Global Salaries
Salaries for Escalator Service Mechanics vary significantly by region and experience. In North America, particularly the USA and Canada, annual salaries range from $60,000 to $95,000 USD, reflecting high demand and a strong union presence. Europe sees ranges from €40,000 to €70,000 EUR (approx. $43,000-$75,000 USD) in countries like Germany and Switzerland, where cost of living is higher but social benefits are robust.
In the Asia-Pacific region, salaries in developed markets like Singapore or Australia can reach $50,000 to $80,000 AUD/SGD (approx. $33,000-$59,000 USD). However, emerging markets like India or Southeast Asia offer lower nominal salaries, often $10,000 to $25,000 USD equivalent, but with significantly lower living costs, leading to comparable purchasing power locally.
Latin American countries typically offer lower salaries, ranging from $15,000 to $35,000 USD equivalent, with variations based on economic stability and infrastructure investment. Salary structures also differ; North America often includes health insurance and retirement plans, while European compensation might feature more vacation time and public healthcare access. Tax implications vary; for instance, high-income earners in Nordic countries face higher tax rates but benefit from extensive public services. International experience and specialized certifications can significantly elevate earning potential across all markets.
Remote Work
International remote work for an Escalator Service Mechanic is generally not feasible. This role requires hands-on diagnostic, repair, and maintenance tasks performed directly on mechanical systems. The nature of the job demands physical presence at specific sites where escalators are installed.
While administrative tasks, such as scheduling or report writing, can be done remotely, the core responsibilities necessitate on-site presence. Digital nomad opportunities do not apply to this trade due to the physical nature of the work. Companies hiring globally for this role expect mechanics to relocate or be locally based. Salary expectations remain tied to the geographic location of the physical work, with no concept of geographic arbitrage for this specific trade.
Visa & Immigration
Escalator Service Mechanics seeking international work typically apply for skilled worker visas. Countries like Canada (Express Entry), Australia (Skilled Nominated Visa), and Germany (EU Blue Card) often list such trades as in-demand. Requirements usually include recognized trade qualifications, several years of experience, and often English or local language proficiency tests.
Credential recognition is crucial; applicants must have their certifications assessed by relevant authorities in the target country. The application process involves submitting educational documents, work experience letters, and often a job offer from a local employer. Processing times vary from a few months to over a year, depending on the country and visa type. Some countries may offer expedited processing for highly skilled trades. Pathways to permanent residency exist in many nations after several years of continuous skilled employment. Family visas for spouses and dependents are typically available alongside the primary applicant's visa.
2025 Market Reality for Escalator Service Mechanics
Understanding current market realities is crucial for any Escalator Service Mechanic. The industry has seen significant evolution, particularly with the integration of advanced electronics and digital diagnostic tools since 2023. These shifts, including post-pandemic operational adjustments and the broader impact of automation, directly influence job availability and required skills.
Economic factors, such as construction cycles and infrastructure investment, also play a vital role. Market conditions vary by experience level, from entry-level apprenticeships to senior technician roles, and by geographic region, with urban centers offering more opportunities. This analysis provides an honest assessment of current hiring conditions.
Current Challenges
Securing an Escalator Service Mechanic position faces several challenges. Competition for experienced technicians remains high, especially for roles in major metropolitan areas. Economic slowdowns can delay new construction projects, reducing the need for new escalator installations, though maintenance demand persists.
The learning curve for complex modern systems, including digital diagnostics and integrated safety protocols, creates a skill gap. Companies seek mechanics with a blend of traditional mechanical expertise and strong digital literacy.
Growth Opportunities
Despite market challenges, strong opportunities exist for Escalator Service Mechanics. The growing complexity of modern escalator systems creates a high demand for technicians skilled in integrated mechanical and digital diagnostics. Specializations in smart escalator systems, predictive maintenance, and cybersecurity for connected units are emerging areas of growth.
Professionals can gain a competitive edge by pursuing certifications in specific manufacturer systems, particularly those from major global escalator companies. Developing strong data analysis skills for interpreting diagnostic outputs, alongside traditional mechanical repair expertise, makes candidates highly attractive. Underserved markets often include older commercial buildings requiring modernization or smaller municipalities upgrading their infrastructure.
Market corrections can create opportunities as companies focus on maintaining existing assets rather than new installations, shifting demand towards skilled repair and modernization specialists. Industries like public transportation, healthcare facilities, and large retail complexes consistently require experienced mechanics. Investing in continuous training on new control systems and safety protocols positions mechanics for long-term career stability and advancement.
Current Market Trends
The market for Escalator Service Mechanics shows stable demand, primarily driven by the ongoing need for maintenance, repair, and modernization of existing units rather than new installations. Urbanization continues to fuel public and commercial building development, ensuring a baseline requirement for skilled technicians.
Hiring patterns emphasize experience. Companies prioritize mechanics with proven diagnostic abilities and a strong safety record. The integration of smart building technologies and IoT into escalator systems means employers increasingly seek candidates proficient in digital diagnostics and software-based troubleshooting. This shift affects hiring criteria significantly, moving beyond purely mechanical skills.
Economic conditions have a nuanced impact; while new construction might slow, the essential nature of escalator maintenance ensures consistent work. Layoffs are rare in this specialized field, as demand for servicing existing equipment remains constant. Salary trends show a steady increase for experienced, multi-skilled mechanics, particularly those comfortable with both legacy and modern systems. Market saturation is low for highly skilled, certified professionals, but entry-level roles can be competitive without specific vocational training.
Geographically, major cities and transportation hubs like airports and subway systems offer the strongest markets due to the high density of escalators. Remote work is not applicable to this hands-on role. Seasonal hiring does not significantly affect this field; demand for maintenance is year-round.
Emerging Specializations
The field of escalator service and maintenance is undergoing a significant transformation driven by technological advancements and the increasing demand for smart infrastructure. Understanding these shifts is crucial for professionals aiming to secure future-proof careers. New specialization opportunities are emerging from the integration of digital technologies, sustainable practices, and advanced diagnostic tools into traditional mechanical work.
Positioning oneself early in these nascent areas offers a distinct advantage for career advancement in 2025 and beyond. Professionals who adapt to these emerging specializations often command premium compensation and experience accelerated career growth, as their unique skill sets are in high demand yet short supply. This strategic choice balances the stability of established maintenance practices with the lucrative potential of cutting-edge fields.
While some emerging areas may initially have fewer immediate openings, they are rapidly gaining momentum and are projected to create significant job opportunities within the next three to five years. The risk of investing in new skills is offset by the substantial rewards of becoming an early expert in a growing niche. Identifying these trends allows escalator service mechanics to proactively shape their professional trajectory.
Smart Escalator IoT & Predictive Maintenance Specialist
This specialization focuses on the installation, maintenance, and troubleshooting of sophisticated sensor networks and IoT devices integrated into modern escalators. These systems monitor performance, predict failures, and optimize energy usage. Mechanics in this area ensure seamless data flow from components to central diagnostic platforms, enabling proactive maintenance and reducing downtime significantly.
Sustainable Escalator Energy Optimization Technician
As sustainability becomes a core focus, this specialization involves optimizing escalator systems for energy efficiency and environmental impact. This includes implementing variable frequency drives, regenerative braking systems, and advanced power management solutions. Mechanics also work with eco-friendly lubricants and materials, ensuring compliance with green building standards and reducing operational carbon footprints.
Automated System & Robotics Integration Mechanic
With the rise of automation, escalators are incorporating more complex robotic elements for cleaning, inspection, and even component replacement. This specialization requires mechanics to maintain, calibrate, and repair these automated systems. It involves working with robotic arms, automated guided vehicles (AGVs), and specialized software for robotic control and task execution within escalator environments.
Remote Diagnostics & Augmented Reality Service Engineer
This area focuses on the implementation and upkeep of advanced remote monitoring and diagnostic systems for escalators. Mechanics utilize augmented reality (AR) tools for virtual inspections, troubleshoot issues remotely using real-time data, and guide on-site personnel through complex repairs. This specialization minimizes physical travel and speeds up resolution times, enhancing service efficiency.
Escalator System Cybersecurity Specialist
Cybersecurity is becoming critical for networked escalator systems that transmit sensitive operational data. This specialization involves securing these systems from unauthorized access, data breaches, and malicious attacks. Mechanics must understand network security protocols, identify vulnerabilities, and implement protective measures to ensure the integrity and safety of smart escalator infrastructure.
Pros & Cons of Being an Escalator Service Mechanic
Making informed career decisions requires understanding both the benefits and challenges of a profession. While some roles offer clear advantages, they also come with specific demands and potential drawbacks. Career experiences can vary significantly based on the company culture, the specific industry sector, the specialization within the field, and individual preferences. Moreover, the pros and cons might shift at different stages of one's career, from an entry-level position to a senior role. What one person views as a benefit, another might see as a challenge, depending on their personal values and lifestyle priorities. This assessment provides an honest, balanced view to help you set appropriate expectations for this career path.
Pros
- There is high demand for skilled Escalator Service Mechanics, ensuring strong job security and consistent employment opportunities across various industries and locations.
- The role offers competitive wages and benefit packages, reflecting the specialized skills and critical nature of maintaining public transportation systems, often including overtime pay.
- Work involves hands-on problem-solving, providing intellectual stimulation as you diagnose and repair complex mechanical and electrical systems.
- This career offers a sense of purpose and direct impact, as you ensure the safe and efficient operation of essential public infrastructure, contributing to community mobility.
- Opportunities for continuous learning exist through manufacturer training and new technology integration, allowing for skill development and career growth within the field.
- The job often provides a degree of independence, as mechanics frequently work alone or in small teams, managing their own tasks and schedules once on-site.
- Escalator Service Mechanics gain a unique and specialized skillset that is highly valued and not easily automated, making them indispensable in the urban landscape.
Cons
- The work environment often involves tight, confined spaces within escalator mechanisms, which can be physically demanding and uncomfortable for extended periods.
- This role requires working at heights, often on scaffolding or lifts, which poses inherent safety risks and can be challenging for those uncomfortable with elevated work.
- Emergency call-outs are common for breakdowns, leading to irregular hours, overtime, and disruption to personal plans, especially during peak operation times.
- The job involves exposure to grease, oil, dust, and electrical components, necessitating strict adherence to safety protocols and regular cleaning.
- A significant physical toll results from repetitive lifting, bending, kneeling, and working in awkward positions, potentially leading to long-term musculoskeletal issues.
- Continuous training is essential to keep up with evolving escalator technologies and safety standards, requiring ongoing commitment to learning even after certification.
- Troubleshooting complex mechanical and electrical issues under pressure can be mentally taxing, especially when an escalator is out of service at a busy location, impacting many people.
Frequently Asked Questions
Escalator Service Mechanics face distinct challenges balancing mechanical aptitude with safety regulations and on-call demands. This section addresses common questions about entering this specialized trade, from required training and physical demands to career stability and growth opportunities in a niche but essential field.
What are the essential training and certification requirements to become an Escalator Service Mechanic?
Becoming an Escalator Service Mechanic typically requires completing a specialized apprenticeship program, which can last 4-5 years. These programs combine on-the-job training with classroom instruction covering electrical systems, mechanical principles, and safety protocols specific to escalators and elevators. Some entrants may start with a vocational degree in mechanics or electronics, but the apprenticeship is usually essential for certification.
What is the typical salary range for an Escalator Service Mechanic, from entry-level to experienced?
Entry-level Escalator Service Mechanics can expect to earn a competitive wage, often starting around $25-$35 per hour during an apprenticeship, which increases significantly upon becoming a journeyman. Experienced mechanics, especially those with specialized skills or on-call responsibilities, can earn upwards of $40-$60 per hour, plus benefits and overtime. Geographic location and union affiliation also play a role in salary variations.
How physically demanding is the job, and what are the typical working conditions?
The job involves significant physical demands. You will frequently lift heavy components, work in confined spaces, climb ladders, and stand or kneel for extended periods. Good manual dexterity and physical stamina are crucial for troubleshooting and repairing complex mechanical and electrical systems. You must also be comfortable working at heights and in various environmental conditions, including noisy or dusty areas.
What is the job security like for an Escalator Service Mechanic, and is the field growing?
Job security for Escalator Service Mechanics is generally very high due to the critical nature of the equipment and the specialized skills required. Escalators and elevators are essential in urban environments, and they require continuous maintenance, repair, and modernization. The demand for skilled technicians remains consistent, as the infrastructure ages and new installations occur. This is a stable trade with a strong outlook.
What is the typical work-life balance for this role, considering potential on-call duties?
Work-life balance can vary. While you typically work standard hours, emergency repairs or routine maintenance often require working evenings, weekends, or being on-call. This can lead to irregular schedules and overtime. However, many mechanics find the direct impact of their work and the problem-solving aspects rewarding. It's a trade that demands flexibility but offers a clear sense of accomplishment.
What are the career advancement opportunities and potential specializations within this field?
Career growth paths include becoming a lead mechanic, a supervisor, or moving into management roles within an escalator or elevator company. Some experienced mechanics specialize in modernization projects, diagnostics, or safety inspections. Further training and certifications in advanced control systems or specific manufacturer equipment can also open up new opportunities and increase earning potential.
What key skills and personality traits are most important for success as an Escalator Service Mechanic?
Success in this field requires strong mechanical aptitude, excellent problem-solving skills, and attention to detail. You need to be comfortable working with complex electrical schematics and diagnostic tools. Good communication skills are also important for interacting with clients and team members. A commitment to safety protocols and continuous learning about new technologies is essential.
Related Careers
Explore similar roles that might align with your interests and skills:
Elevator Mechanic
A growing field with similar skill requirements and career progression opportunities.
Explore career guideElevator Repair and Maintenance Technician
A growing field with similar skill requirements and career progression opportunities.
Explore career guideElevator Service Technician
A growing field with similar skill requirements and career progression opportunities.
Explore career guideEscalator Installer
A growing field with similar skill requirements and career progression opportunities.
Explore career guideEscalator Mechanic
A growing field with similar skill requirements and career progression opportunities.
Explore career guideAssess your Escalator Service Mechanic readiness
Understanding where you stand today is the first step toward your career goals. Our Career Coach helps identify skill gaps and create personalized plans.
Skills Gap Analysis
Get a detailed assessment of your current skills versus Escalator Service Mechanic requirements. Our AI Career Coach identifies specific areas for improvement with personalized recommendations.
See your skills gapCareer Readiness Assessment
Evaluate your overall readiness for Escalator Service Mechanic roles with our AI Career Coach. Receive personalized recommendations for education, projects, and experience to boost your competitiveness.
Assess your readinessSimple pricing, powerful features
Upgrade to Himalayas Plus and turbocharge your job search.
Himalayas
Himalayas Plus
Himalayas Max
Find your dream job
Sign up now and join over 100,000 remote workers who receive personalized job alerts, curated job matches, and more for free!
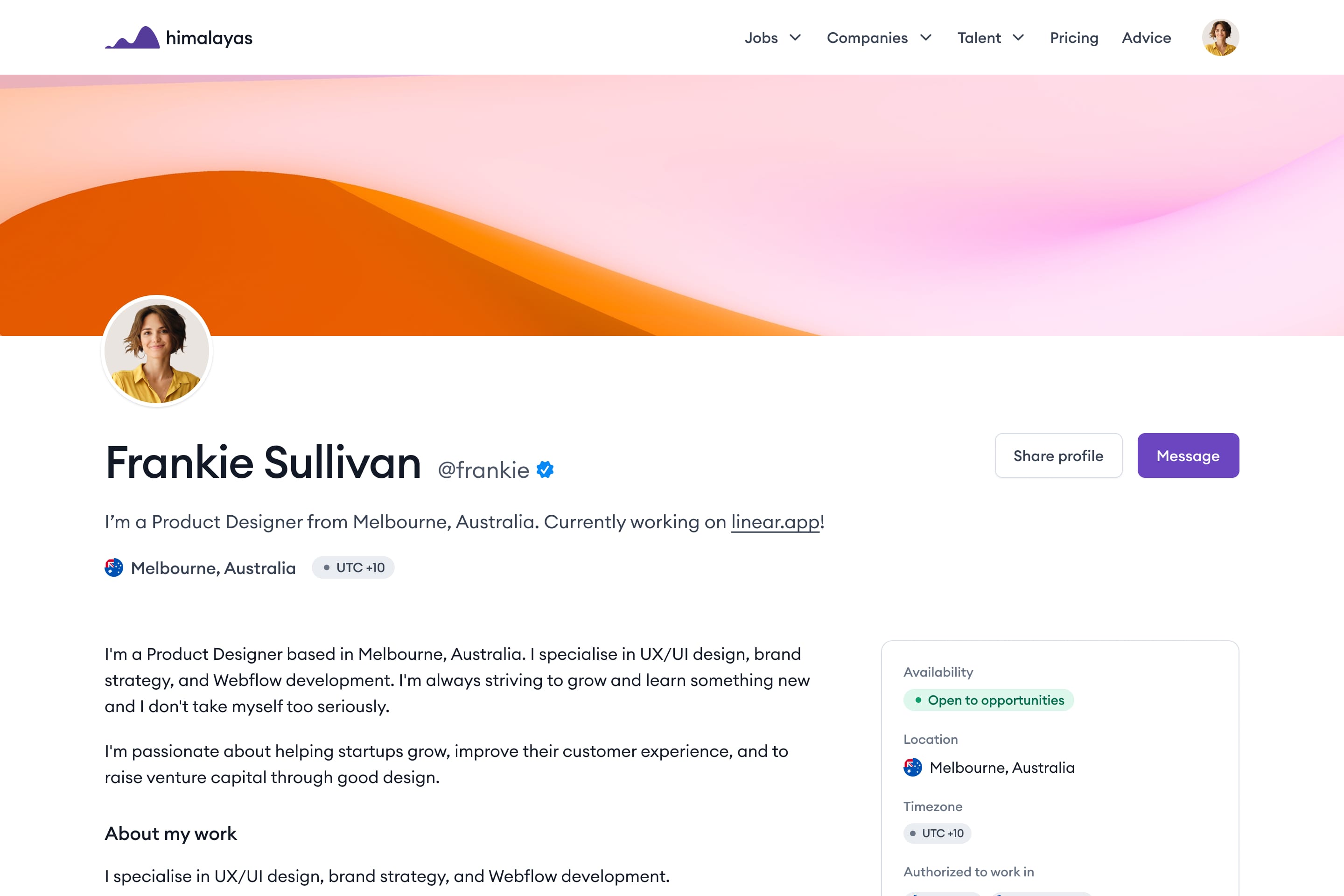