Complete Combination Machine Tool Operator Career Guide
Combination machine tool operators are the skilled craftspeople who manage and operate multiple types of metalworking machines simultaneously, creating precision parts for everything from automotive components to aerospace systems. This role is crucial in modern manufacturing, blending traditional machining expertise with technological oversight to maximize efficiency and output. You'll master diverse machinery, ensuring quality and driving production in a hands-on, detail-oriented career.
Key Facts & Statistics
Median Salary
$49,080 USD
(U.S. Bureau of Labor Statistics, May 2023)
Range: $34k - $70k+ USD
Growth Outlook
Annual Openings
≈34,700
openings annually (U.S. Bureau of Labor Statistics, 2022-2032)
Top Industries
Typical Education
High school diploma or equivalent; on-the-job training, vocational training, or an apprenticeship are common paths. Some employers prefer postsecondary certificates.
What is a Combination Machine Tool Operator?
A Combination Machine Tool Operator is a highly skilled manufacturing professional who sets up, operates, and maintains a variety of machine tools—such as lathes, mills, grinders, and drill presses—to produce precision parts. Unlike a single-machine operator who specializes in one type of equipment, a combination operator possesses the versatility to work across multiple machinery types, often operating them in sequence or in tandem to complete complex components.
This role is critical for manufacturing efficiency and flexibility, especially in job shops or production environments requiring diverse machining capabilities. They are distinct from CNC programmers, who primarily write the code, as the operator focuses on the physical setup, operation, and troubleshooting of the machines themselves. Their expertise ensures the accurate and efficient transformation of raw materials into finished products according to engineering specifications.
What does a Combination Machine Tool Operator do?
Key Responsibilities
- Set up and operate multiple types of machine tools, such as lathes, milling machines, and grinders, often simultaneously or in sequence to complete parts.
- Read and interpret blueprints, schematics, and engineering drawings to understand part specifications and machining requirements.
- Monitor machine operations, adjusting controls as needed to ensure product quality and adherence to design tolerances.
- Perform routine maintenance on machines, including cleaning, lubricating, and making minor repairs to ensure optimal performance.
- Inspect finished products using precision measuring instruments like calipers, micrometers, and gauges to verify dimensional accuracy.
- Troubleshoot machine malfunctions or production issues, identifying root causes and implementing corrective actions to minimize downtime.
- Document production activities, including completed units, scrap rates, and any machine adjustments or maintenance performed, maintaining accurate records for quality control and process improvement.
Work Environment
Combination Machine Tool Operators typically work in manufacturing plants, machine shops, or production facilities. The environment can be noisy dueating equipment, and may require standing for long periods. Safety is a top priority, with strict adherence to protocols due to the presence of heavy machinery and moving parts.
Collaboration is often with other operators, supervisors, and quality control personnel. Schedules can vary, including day, evening, or night shifts, and sometimes weekends, depending on production demands. The work pace is steady, requiring consistent focus and attention to detail. While largely independent during machine operation, operators must communicate effectively about production progress and potential issues.
Tools & Technologies
Combination Machine Tool Operators use a wide array of specialized equipment, including CNC (Computer Numerical Control) lathes, milling machines, grinding machines, and multi-axis machining centers. They frequently work with precision measuring instruments such as micrometers, calipers, bore gauges, and optical comparators to ensure part accuracy.
Software includes CAD/CAM (Computer-Aided Design/Manufacturing) programs for interpreting designs and sometimes for basic programming or editing of G-code. They also utilize various hand tools for setup and maintenance, and material handling equipment like forklifts or hoists for moving raw materials and finished parts. Adherence to safety protocols and the use of personal protective equipment (PPE) are also fundamental to the role.
Combination Machine Tool Operator Skills & Qualifications
The Combination Machine Tool Operator role demands a specific blend of precision mechanical aptitude and operational knowledge. Qualifications are typically structured around practical experience, with formal education often playing a supportive, rather than primary, role. Entry-level positions may require only a high school diploma and some vocational training, focusing heavily on foundational machine shop principles and safety.
Requirements shift significantly with seniority and the complexity of the machinery involved. Senior operators often possess several years of experience, demonstrating proficiency across multiple machine types, advanced setup procedures, and troubleshooting capabilities. Larger manufacturing firms or those specializing in high-precision components (e.g., aerospace, medical devices) often prioritize candidates with formal apprenticeships or associate degrees in machining technology. Smaller job shops, however, might value direct on-the-job experience and a proven track record over academic credentials.
Formal certifications, such as those from the National Institute for Metalworking Skills (NIMS), significantly enhance a candidate's profile, validating specific competencies in areas like measurement, materials, and machining processes. While a degree is not always mandatory, it can accelerate career progression into supervisory or programming roles. The skill landscape for machine tool operators is evolving; traditional manual machining skills remain valuable, but proficiency with Computer Numerical Control (CNC) machines, including basic programming and G-code interpretation, is increasingly crucial for modern manufacturing environments. This role balances hands-on mechanical skill with the ability to interpret technical drawings and work within tight tolerances.
Education Requirements
Technical Skills
- Operation of Manual Lathes (e.g., engine lathes, turret lathes)
- Operation of Manual Milling Machines (e.g., vertical milling, horizontal milling)
- CNC Machine Operation (loading programs, offsets, tool changes)
- Blueprint and Technical Drawing Reading (GD&T interpretation)
- Precision Measurement Tools (calipers, micrometers, height gauges, bore gauges)
- G-code and M-code understanding (basic interpretation and minor edits)
- Material Science (understanding properties of metals like steel, aluminum, brass)
- Tooling Selection and Setup (inserts, end mills, drills, taps)
- Machine Setup and Fixturing (workholding, part alignment)
- Preventative Machine Maintenance (lubrication, cleaning, minor adjustments)
- Quality Control Procedures (in-process inspection, defect identification)
- Safety Protocols (lockout/tagout, machine guarding)
Soft Skills
- Attention to Detail: Critical for producing parts within tight tolerances and identifying subtle machine malfunctions before they cause defects.
- Problem-Solving: Essential for troubleshooting machine errors, adjusting setups, and resolving issues that arise during production.
- Safety Consciousness: Paramount for operating heavy machinery safely and adhering to strict workplace safety protocols.
- Mechanical Aptitude: Important for understanding how machines work, performing basic maintenance, and making precise adjustments.
- Adherence to Procedures: Necessary for consistently following operational guidelines, quality control checks, and safety regulations.
- Time Management: Key for efficiently setting up machines, monitoring production cycles, and meeting production deadlines.
- Adaptability: Valuable for adjusting to different machine types, new materials, and evolving production schedules or specifications.
- Team Collaboration: Important for coordinating with supervisors, quality control, and other operators on production runs and process improvements, especially in a shift environment, to ensure smooth handovers and shared problem-solving for production efficiency and quality control, contributing to overall operational success and a cohesive work environment, as effective communication and mutual support are vital for maintaining continuous production and addressing unforeseen challenges quickly and effectively, preventing downtime and ensuring that production targets are met with minimal disruptions and maximum efficiency.
How to Become a Combination Machine Tool Operator
Entering the field of Combination Machine Tool Operation offers several pathways, from formal training to on-the-job learning. A common route involves completing a vocational program or an associate's degree in machining technology, which provides a strong theoretical and practical foundation. However, many individuals also successfully enter through apprenticeships or entry-level manufacturing roles, gaining skills directly on the factory floor.
The timeline for entry varies significantly based on your starting point. A vocational program typically takes 9-18 months, while an associate's degree may take two years. Apprenticeships can range from 2-4 years, offering paid training. For those with no prior experience, starting in a general production role and demonstrating a keen interest in machine operation can lead to internal training opportunities within 6-12 months.
Geographic considerations also play a role; manufacturing hubs often have more opportunities and established apprenticeship programs. Company size affects entry too; smaller shops might offer broader exposure to different machines, while larger corporations may have more structured training and clear career progression. Regardless of the path, a strong mechanical aptitude, attention to detail, and a commitment to safety are crucial for success in this hands-on field.
Step 1
Step 2
Step 3
Step 4
Step 5
Step 6
Education & Training Needed to Become a Combination Machine Tool Operator
Becoming a Combination Machine Tool Operator requires a blend of practical skills and theoretical knowledge, focusing on operating and maintaining CNC (Computer Numerical Control) and manual machinery. Formal degree programs, like associate degrees in Manufacturing Technology or Machine Tool Technology, typically span two years and can cost between $8,000 and $20,000 at community colleges. These programs provide a strong foundation in machining principles, blueprint reading, and safety protocols. They often include hands-on lab work essential for developing proficiency.
Alternative pathways, such as vocational school certificates or apprenticeships, are highly valued in this field. Certificate programs, lasting 6 to 18 months, often focus intensely on specific machine operations and programming, with costs ranging from $2,000 to $10,000. Apprenticeships, which combine paid on-the-job training with classroom instruction, are an excellent option; they can last 3-5 years and often lead directly to employment upon completion. Employers highly favor candidates with verifiable hands-on experience, often gained through these vocational routes.
Self-study, using online courses or free resources, can supplement formal training but rarely suffices on its own for entry-level positions without practical experience. Continuous learning is vital, as machine technologies evolve rapidly. Operators need to stay updated on new software, tooling, and automation trends through short courses or manufacturer-specific training. The cost-benefit analysis often favors vocational training or apprenticeships due to their direct applicability and quicker entry into the workforce, compared to a longer, more expensive associate degree, though the latter may offer broader career mobility.
Combination Machine Tool Operator Salary & Outlook
Compensation for a Combination Machine Tool Operator varies significantly based on several factors. Geographic location plays a crucial role; areas with a high concentration of manufacturing industries or higher costs of living typically offer elevated wages. For instance, operators in industrial hubs may earn more than those in rural regions, reflecting local demand and economic conditions.
Experience levels, specialized skills, and certifications directly influence earning potential. Junior operators start at foundational rates, while senior and lead operators command higher salaries due to their advanced expertise in complex machinery, precision operations, and problem-solving. Mastery of CNC programming, advanced tooling, or multi-axis machines can lead to premium compensation.
Total compensation extends beyond base salary to include overtime pay, production bonuses, and shift differentials, especially for night or weekend shifts. Benefits packages often cover health insurance, retirement plans like 401(k)s, and paid time off. Some companies also invest in professional development or offer tuition reimbursement for advanced certifications, enhancing an operator's long-term earning capacity.
Industry sector also impacts pay; aerospace, automotive, or medical device manufacturing often provide higher wages than general fabrication due to precision requirements and product value. Remote work is not applicable for this hands-on role. While these figures are in USD, international markets present different pay scales influenced by local labor laws, economic conditions, and industrial output.
Salary by Experience Level
Level | US Median | US Average |
---|---|---|
Junior Machine Tool Operator | $42k USD | $45k USD |
Machine Tool Operator | $55k USD | $58k USD |
Senior Machine Tool Operator | $68k USD | $70k USD |
Lead Machine Tool Operator | $79k USD | $82k USD |
Machine Tool Supervisor | $92k USD | $95k USD |
Market Commentary
The job market for Combination Machine Tool Operators shows a stable outlook, driven by ongoing demand in manufacturing and the need for skilled labor to operate complex machinery. The Bureau of Labor Statistics projects a modest growth for machinists and tool and die makers, which includes combination machine tool operators, around 2% from 2022 to 2032. This growth reflects the continuous need for fabricated metal products, machinery, and transportation equipment.
Technological advancements, particularly in automation and Computer Numerical Control (CNC) systems, are reshaping the role. Operators increasingly need skills in programming, troubleshooting, and maintaining automated systems, moving beyond purely manual operation. This shift creates a demand for operators who can adapt to new technologies and integrate digital tools into their work processes.
The supply of skilled operators often lags behind demand, particularly for those proficient in advanced CNC machining and specialized materials. This imbalance can lead to competitive wages and job security for highly qualified individuals. Geographic hotspots for this role include states with strong manufacturing bases, such as Michigan, Ohio, Texas, and California.
Future-proofing in this career involves continuous learning in new software, advanced materials, and automation technologies. While AI and automation enhance efficiency, they also elevate the operator's role to one of oversight, programming, and maintenance, rather than outright replacement. This profession remains relatively recession-resistant due to its foundational role in essential manufacturing sectors.
Combination Machine Tool Operator Career Path
Career progression for a Combination Machine Tool Operator typically unfolds through increasing mastery of complex machinery, precision, and operational efficiency. Advancement often involves a transition from supervised tasks to independent operation, then to leadership roles overseeing others. Both individual contributor (IC) and management tracks exist; an IC track focuses on becoming a highly specialized expert, while the management track involves leading teams and production processes.
Advancement speed is influenced by consistent high performance, the ability to maintain tight tolerances, and proactive learning of new machine technologies and materials. Company size and industry sector also play a role; larger manufacturing firms may offer more structured progression paths, while smaller shops might allow for quicker cross-training and broader skill development. Lateral moves could involve specializing in CNC programming or quality control within the same manufacturing environment.
Networking within the plant and with equipment vendors helps in understanding new technologies and best practices. Mentorship from experienced operators and supervisors is crucial for skill transfer and problem-solving. Achieving certifications in specific machine types or safety protocols marks significant progression. Continuous learning, adaptability to automation, and a strong commitment to quality are vital for sustained career growth in this field.
Junior Machine Tool Operator
0-2 yearsKey Focus Areas
Machine Tool Operator
2-5 yearsKey Focus Areas
Senior Machine Tool Operator
5-8 yearsKey Focus Areas
Lead Machine Tool Operator
8-12 yearsKey Focus Areas
Machine Tool Supervisor
12+ yearsKey Focus Areas
Junior Machine Tool Operator
0-2 yearsOperates basic machine tools under direct supervision, performing routine tasks such as loading materials, initiating cycles, and deburring finished parts. Learns machine setup and adjustment procedures. Responsibilities include maintaining a clean and safe workspace and reporting any machine malfunctions or quality issues to a senior operator.
Key Focus Areas
Develop foundational knowledge of machine operation, safety protocols, and basic blueprint reading. Focus on understanding material properties and tool selection. Practice precision measurement techniques and routine machine maintenance. Build a strong work ethic and attention to detail.
Machine Tool Operator
2-5 yearsOperates a variety of combination machine tools independently, setting up machines, selecting tools, and performing routine quality checks. Produces parts to specified tolerances with minimal supervision. Identifies and resolves operational issues, ensuring production efficiency and product quality. May assist in training junior operators.
Key Focus Areas
Master advanced machine setup, including tool offsets and fixture adjustments. Develop proficiency in interpreting complex blueprints and G-code. Troubleshoot common machine errors and perform preventative maintenance. Begin cross-training on different machine types or control systems.
Senior Machine Tool Operator
5-8 yearsServes as a subject matter expert for complex machine operations, capable of setting up and operating highly specialized or custom combination machine tools. Takes ownership of critical production runs, ensuring precision and quality for challenging parts. Provides technical guidance to other operators and assists in process improvement initiatives.
Key Focus Areas
Specialize in complex machining processes, such as multi-axis operations or exotic materials. Optimize machine programs for efficiency and reduced cycle times. Develop strong problem-solving skills for intricate production challenges. Mentor and guide less experienced operators on best practices and safety.
Lead Machine Tool Operator
8-12 yearsDirects the daily operations of a group of machine tools or a specific production cell, ensuring production targets, quality standards, and safety protocols are met. Assigns tasks, oversees setups, and troubleshoots complex issues. Acts as the primary point of contact for technical questions and coordinates with maintenance and quality control teams.
Key Focus Areas
Lead and organize daily production schedules for a specific machine or cell. Develop team leadership skills, including effective communication and conflict resolution. Contribute to process optimization and lean manufacturing initiatives. Train new operators and provide ongoing performance feedback.
Machine Tool Supervisor
12+ yearsOversees the entire machine tool operation department, managing a team of operators and leads. Responsible for production planning, budgeting, and ensuring all safety and quality regulations are adhered to. Evaluates new technologies and implements efficiency improvements. Manages performance, training, and development for the machine shop personnel.
Key Focus Areas
Manage overall machine shop operations, including staffing, scheduling, and resource allocation. Develop strategic planning skills for production capacity and equipment upgrades. Implement quality management systems and continuous improvement programs. Foster a strong safety culture and provide leadership for the entire team.
Job Application Toolkit
Ace your application with our purpose-built resources:
Combination Machine Tool Operator Resume Examples
Proven layouts and keywords hiring managers scan for.
View examplesCombination Machine Tool Operator Cover Letter Examples
Personalizable templates that showcase your impact.
View examplesTop Combination Machine Tool Operator Interview Questions
Practice with the questions asked most often.
View examplesCombination Machine Tool Operator Job Description Template
Ready-to-use JD for recruiters and hiring teams.
View examplesGlobal Combination Machine Tool Operator Opportunities
Combination Machine Tool Operators find global demand in manufacturing hubs. This role involves setting up and operating multiple machine types, crucial for precision production across industries like automotive, aerospace, and medical devices. International opportunities exist due to specialized skill requirements and ongoing industrialization. Cultural differences impact workplace safety standards and training methodologies.
Regulatory frameworks vary, influencing machine operation and product quality. Professionals consider international moves for higher wages, advanced technology exposure, or better work-life balance. No universal international certifications exist, but vocational training and experience gained in one country often transfer well.
Global Salaries
Salaries for Combination Machine Tool Operators vary significantly by region. In North America, particularly the United States, annual salaries range from $45,000 to $70,000 USD, with higher figures in regions with strong manufacturing sectors like the Midwest. Canadian operators earn between $40,000 and $60,000 CAD (approximately $30,000-$45,000 USD).
Europe offers diverse compensation. German operators can expect €35,000 to €55,000 (about $38,000-$60,000 USD) annually, reflecting a higher cost of living and robust manufacturing. In Eastern Europe, such as Poland or the Czech Republic, salaries are lower, typically €15,000 to €25,000 (about $16,000-$27,000 USD), but offer higher purchasing power locally. The UK sees salaries from £28,000 to £45,000 (around $35,000-$57,000 USD).
Asia-Pacific markets like Japan or South Korea provide competitive wages, often ranging from ¥3.5 million to ¥5.5 million (approximately $25,000-$37,000 USD) or ₩35 million to ₩55 million (about $26,000-$41,000 USD) respectively, though cost of living in major cities is high. In developing economies, compensation might be lower but still attractive relative to local standards.
Salary structures also differ; European countries often include more robust benefits like extended vacation and public healthcare, impacting take-home pay differently than in North America. Tax implications vary by country; understanding net pay requires local tax knowledge. Experience and specialized training generally lead to higher compensation globally. Some larger international manufacturing firms may have standardized pay scales for similar roles across their global operations.
Remote Work
Remote work potential for Combination Machine Tool Operators is extremely limited. This role is inherently hands-on, requiring direct interaction with physical machinery on a factory floor. Operators must be present to set up, monitor, and troubleshoot equipment.
While some administrative tasks, like scheduling or data entry, could theoretically be done remotely, these form a minor part of the job. Core operational duties demand on-site presence. Digital nomad opportunities do not apply to this profession.
Employers do not typically offer international remote work for this role due to its physical nature. Salary expectations are tied to the local labor market where the manufacturing plant is located. Equipment requirements are specific to the factory environment, including heavy machinery and specialized tools, not a home office setup. Internet requirements are minimal for the operational aspects of the job, but high-speed connectivity is crucial for any remote administrative support or training.
Visa & Immigration
Combination Machine Tool Operators seeking international work often utilize skilled worker visas. Countries like Canada (through Express Entry), Australia (Skilled Nominated Visa), and Germany (Skilled Immigration Act) have pathways for skilled trades. Requirements typically include an employer sponsor, relevant vocational qualifications, and several years of experience.
Educational credential recognition is crucial; applicants often need to demonstrate equivalence of their training to the host country's standards. Professional licensing is not common for this specific role, but some countries may require specific safety certifications. The typical visa timeline ranges from 6 to 18 months, depending on the country and application backlog.
Pathways to permanent residency can exist after several years of skilled employment. Language requirements, particularly English or German, are common for integration and workplace communication. Family visas allow dependents to accompany the primary applicant. Some countries prioritize skilled trades, potentially offering faster processing or more favorable conditions for experienced operators in high-demand sectors.
2025 Market Reality for Combination Machine Tool Operators
Understanding current market conditions is vital for combination machine tool operators to navigate career paths effectively. The manufacturing landscape has transformed significantly between 2023 and 2025, influenced by post-pandemic supply chain adjustments and the accelerating integration of automation and AI.
Broader economic factors, such as inflation and industrial output, directly impact job availability and compensation in this field. Market realities also vary greatly by an operator's experience level, the specific industry (e.g., aerospace vs. general fabrication), geographic location, and the size of the manufacturing facility. This analysis provides an honest assessment to help set realistic expectations.
Current Challenges
Combination machine tool operators face increased competition for advanced roles, as many companies prioritize automation for simpler tasks. Economic slowdowns directly impact manufacturing output, reducing demand for new hires. The need for continuous upskilling in digital controls and programming creates a challenge for some.
Entry-level saturation is also a concern due to vocational training programs. Job search timelines can extend from 3 to 6 months for specialized positions.
Growth Opportunities
Despite challenges, strong demand persists for combination machine tool operators proficient in advanced CNC programming and multi-axis machining. Roles requiring expertise in subtractive and additive manufacturing processes are particularly sought after, especially in precision industries like medical devices and aerospace.
Operators who can integrate robotics or automated material handling systems with their machines hold a significant advantage. Pursuing certifications in advanced CNC controls (e.g., Fanuc, Siemens) or specialized software (e.g., Mastercam, SolidWorks CAM) opens doors to higher-paying positions. Underserved markets often include smaller, custom fabrication shops needing versatile operators.
The shift towards localized manufacturing and reshoring initiatives also creates opportunities for skilled operators in regions previously experiencing decline. Market corrections might lead companies to upgrade older equipment, creating demand for operators familiar with new technologies. Strategic timing for educational investments in robotics or specific material processing can yield significant career growth.
Current Market Trends
Hiring for combination machine tool operators shows a stable but evolving demand as of 2025. Many manufacturers are investing in advanced CNC machinery that requires operators with programming and troubleshooting skills, shifting away from purely manual operations. This trend means less demand for basic setup roles and more for highly skilled operators.
Economic conditions, while showing signs of recovery, still influence manufacturing capacity. Some sectors, like automotive and aerospace, maintain consistent demand, while others, such as general fabrication, experience fluctuations. Generative AI is starting to impact machine design and simulation, but its direct impact on the operator's daily tasks is limited to more intuitive machine interfaces and predictive maintenance alerts.
Employer requirements now frequently include certifications in specific CNC languages, a strong understanding of CAD/CAM software, and a proven ability to perform complex setups. Companies prioritize operators who can manage multiple machines or integrate automated systems. Salary trends are seeing modest increases for skilled operators, especially those with multi-axis CNC experience, while basic manual machine operation wages remain stagnant.
Geographically, demand remains strongest in industrial hubs like the Midwest and Southeast United States, and parts of Germany and China. Remote work is not applicable for this hands-on role. Seasonal hiring patterns are less pronounced, but capital expenditure cycles in manufacturing can lead to hiring surges or slowdowns.
Emerging Specializations
Technological advancements, particularly in automation and digital manufacturing, are profoundly reshaping the landscape for Combination Machine Tool Operators. These shifts create new specialization opportunities that move beyond traditional operational roles. Understanding these future-oriented paths allows operators to position themselves strategically for career advancement and increased earning potential from 2025 onwards.
Early positioning in emerging areas often commands premium compensation and offers accelerated career growth. While established specializations remain stable, focusing on cutting-edge fields ensures relevance and demand in an evolving industry. The balance lies in building a strong foundational skill set while incrementally adding expertise in these nascent, high-growth areas.
Many emerging areas, driven by advancements in AI, robotics, and advanced materials, are transitioning from niche applications to mainstream adoption. This progression typically takes three to five years, creating significant job opportunities as industries integrate new technologies. Specializing in these areas involves a calculated risk, as some technologies may evolve differently than expected. However, the reward for early adopters often includes leadership roles and influence in shaping the future of manufacturing operations.
Robotic Cell Integration Operator
Hybrid Manufacturing Machine Operator
Smart Machine Data Analyst Operator
Advanced Materials Machining Specialist
Pros & Cons of Being a Combination Machine Tool Operator
Understanding both the advantages and challenges of any career is essential for making informed decisions. Career experiences can vary significantly based on company culture, industry sector, specific specialization, and individual preferences. What one person considers a benefit, another might see as a drawback, depending on their values and lifestyle. Furthermore, the pros and cons may shift at different stages of a career, from entry-level positions to more senior roles. This assessment provides an honest, balanced view of the Combination Machine Tool Operator role to help you set appropriate expectations and determine if this path aligns with your aspirations.
Pros
Combination machine tool operators are consistently in demand across various manufacturing sectors, including automotive, aerospace, and medical devices, providing strong job security.
The role requires precision and technical skill in setting up and operating complex machinery, offering a sense of accomplishment from producing high-quality components.
Many entry-level positions require only a high school diploma and vocational training or an apprenticeship, making it accessible without a four-year college degree and offering a direct path to employment.
Operators gain hands-on experience with advanced manufacturing technologies, which can serve as a foundation for further specialization in CNC programming, quality assurance, or automation.
The work environment is typically stable and predictable, often involving consistent shift schedules, which can be beneficial for maintaining a work-life balance compared to more volatile industries.
Wages for experienced combination machine tool operators are competitive, often offering good hourly rates and opportunities for overtime pay, providing a stable income.
Cons
The work environment often involves exposure to noise, vibrations, and coolants, which can be physically demanding and potentially lead to long-term health issues if proper safety measures are not consistently followed.
Operators frequently stand for long periods, perform repetitive motions, and lift heavy materials, leading to physical fatigue and an increased risk of musculoskeletal injuries over time.
The job can be monotonous, as it often involves repeating the same set of tasks for extended shifts, which may not appeal to individuals who prefer varied or highly interactive work.
Operators must strictly adhere to safety protocols, and even minor errors can result in significant material waste, machine damage, or severe personal injury, leading to constant pressure to maintain precision and vigilance.
While some combination machine tools are highly automated, troubleshooting and minor maintenance often fall to the operator, requiring quick thinking and problem-solving skills under pressure to minimize downtime.
Career advancement can be limited without additional certifications or specialized training in areas like CNC programming, quality control, or supervisory roles, as the operator role itself has a defined scope.
Frequently Asked Questions
Combination Machine Tool Operators face unique challenges balancing precision with efficiency across multiple machine types. This section addresses the most common questions about entering this specialized role, from mastering diverse machinery to understanding safety protocols and career progression within manufacturing.
What are the typical entry requirements and qualifications for a Combination Machine Tool Operator?
Many Combination Machine Tool Operator roles require a high school diploma or GED, along with vocational training or an apprenticeship. Some employers prefer candidates with an associate's degree in machine tool technology. Practical experience operating various CNC and manual machines is highly valued, and certifications in specific machine operations or safety can significantly enhance your qualifications.
How long does it typically take to become a skilled Combination Machine Tool Operator from scratch?
Becoming proficient as a Combination Machine Tool Operator can take 1-3 years, depending on your starting experience. If you begin with vocational training, it usually lasts 6-12 months, followed by 1-2 years of on-the-job experience to master different machine types and materials. Apprenticeships typically last 3-4 years, providing comprehensive hands-on training across various machines and processes.
What are the salary expectations for a Combination Machine Tool Operator, both entry-level and experienced?
Entry-level Combination Machine Tool Operators can expect to earn around $35,000 to $45,000 annually. With 3-5 years of experience and proficiency in a wider range of machines, salaries can rise to $45,000 to $60,000. Highly skilled and experienced operators, especially those with programming knowledge or supervisory responsibilities, can earn upwards of $60,000 to $75,000 or more.
What is the typical work-life balance like for someone in this role, considering shifts and overtime?
The work-life balance for a Combination Machine Tool Operator often depends on the specific manufacturing environment. Many roles involve standard 8-hour shifts, but some facilities operate 24/7, requiring evening, night, or weekend shifts. Overtime can be common, especially during peak production periods. The work is physically demanding, requiring standing for long periods and lifting, which can impact personal time if not managed well.
Is the job of a Combination Machine Tool Operator secure, or is it at risk due to automation?
Job security for Combination Machine Tool Operators remains strong due to ongoing demand in manufacturing. While automation changes some aspects of the job, the need for skilled operators who can set up, troubleshoot, and maintain complex machinery across different functions is consistent. Operators with diverse skills across both manual and CNC machines are particularly valuable and in demand.
What are the typical career growth paths and advancement opportunities for a Combination Machine Tool Operator?
Career growth for Combination Machine Tool Operators can lead to several advanced roles. You can specialize in CNC programming, becoming a CNC Programmer or Machinist. Opportunities also exist to move into quality control, becoming a Quality Inspector, or into maintenance as a Machine Maintenance Technician. With leadership skills, you might advance to a Lead Operator, Shop Foreman, or Production Supervisor position.
What are the biggest challenges or common difficulties specific to being a Combination Machine Tool Operator?
The primary challenges include mastering a wide array of machine types and their specific programming or setup requirements, maintaining extreme precision to meet tight tolerances, and adhering to strict safety protocols. Operators must also be adept at troubleshooting machine malfunctions and adapting to new technologies. The work can be repetitive, but the need for continuous learning keeps it engaging.
Can Combination Machine Tool Operators work remotely, or is it strictly an on-site role?
Combination Machine Tool Operator roles are primarily on-site due to the nature of operating heavy machinery. Remote work is not feasible for the direct operational aspects of the job. However, some administrative or planning tasks, such as reviewing blueprints or scheduling, might occasionally be done remotely in a supervisory capacity, but the core work requires physical presence in a manufacturing facility.
Related Careers
Explore similar roles that might align with your interests and skills:
CNC Machine Operator
A growing field with similar skill requirements and career progression opportunities.
Explore career guideCnc Operator
A growing field with similar skill requirements and career progression opportunities.
Explore career guideMachine Operator
A growing field with similar skill requirements and career progression opportunities.
Explore career guideManufacturing Operator
A growing field with similar skill requirements and career progression opportunities.
Explore career guideProduction Machinist
A growing field with similar skill requirements and career progression opportunities.
Explore career guideAssess your Combination Machine Tool Operator readiness
Understanding where you stand today is the first step toward your career goals. Our Career Coach helps identify skill gaps and create personalized plans.
Skills Gap Analysis
Get a detailed assessment of your current skills versus Combination Machine Tool Operator requirements. Our AI Career Coach identifies specific areas for improvement with personalized recommendations.
See your skills gapCareer Readiness Assessment
Evaluate your overall readiness for Combination Machine Tool Operator roles with our AI Career Coach. Receive personalized recommendations for education, projects, and experience to boost your competitiveness.
Assess your readinessSimple pricing, powerful features
Upgrade to Himalayas Plus and turbocharge your job search.
Himalayas
Himalayas Plus
Himalayas Max
Find your dream job
Sign up now and join over 100,000 remote workers who receive personalized job alerts, curated job matches, and more for free!
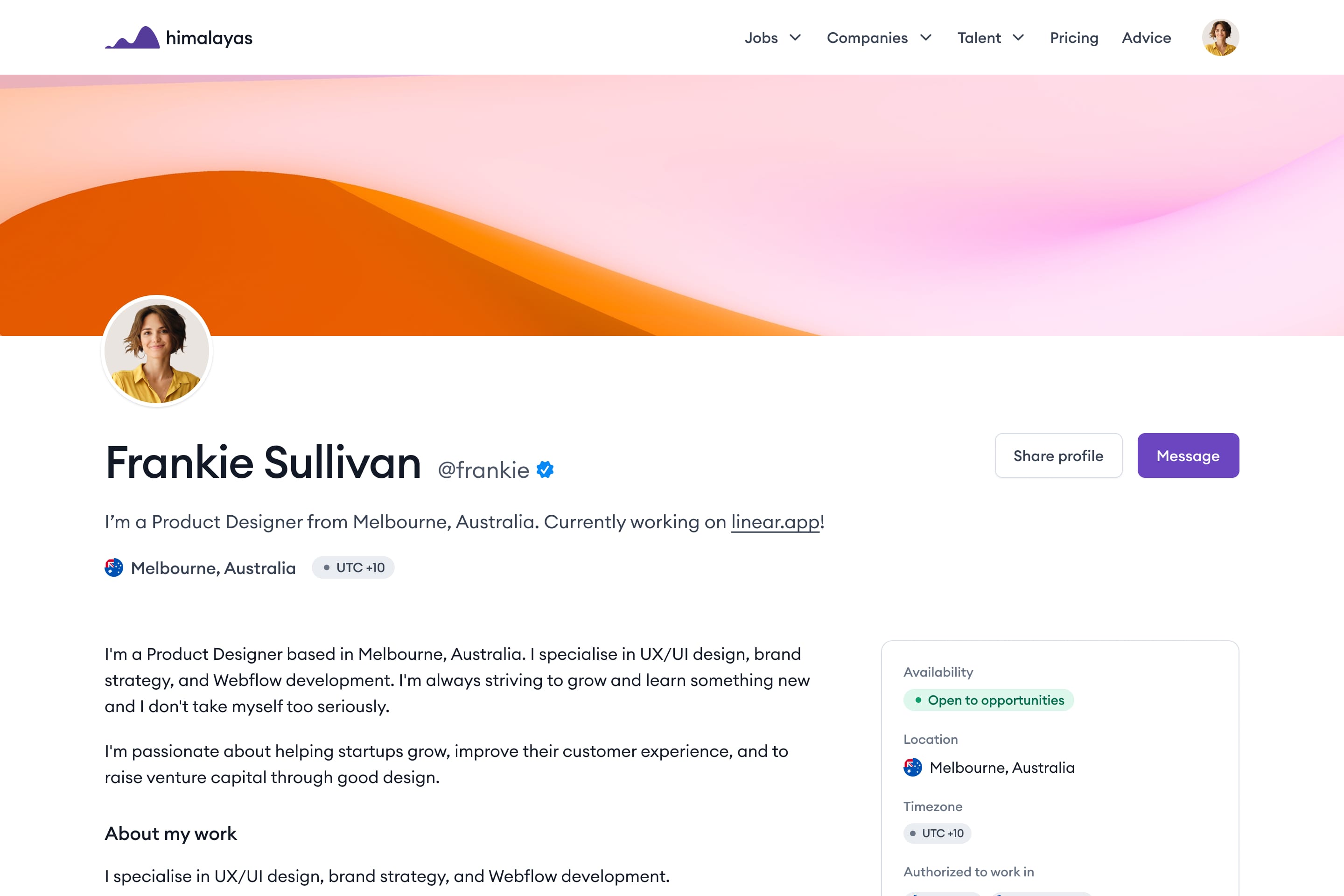