Complete Assembly Supervisor Career Guide
Assembly supervisors are the linchpin of manufacturing floors, orchestrating production lines to ensure efficiency, quality, and safety. You direct teams, optimize processes, and troubleshoot issues, directly impacting a company's ability to deliver products on time and to specification. This hands-on leadership role offers a direct path to managing critical operations, blending technical oversight with strong interpersonal skills.
Key Facts & Statistics
Median Salary
$68,690 USD
(U.S. Bureau of Labor Statistics, May 2023)
Range: $45k - $95k+ USD
Growth Outlook
3%
as fast as average (U.S. Bureau of Labor Statistics, 2022-2032)
Annual Openings
≈17
.2k openings annually (U.S. Bureau of Labor Statistics, 2022-2032)
Top Industries
Typical Education
High school diploma or equivalent, with significant on-the-job experience; some positions prefer an associate's degree or vocational training in manufacturing or industrial technology.
What is an Assembly Supervisor?
An Assembly Supervisor leads and manages a team of assembly line workers responsible for putting together components to create finished products. This role focuses on the direct oversight of the assembly process, ensuring that production goals are met efficiently, safely, and to specified quality standards. They are critical in translating production plans into tangible output on the factory floor.
Unlike a Production Manager, who handles broader strategic planning and resource allocation across multiple lines or departments, an Assembly Supervisor maintains a more hands-on role with daily operations and direct team management. They are distinct from Quality Control Inspectors, who solely focus on product inspection, as supervisors also address process improvement and team performance. This position ensures the smooth flow of manufacturing, preventing bottlenecks and maintaining high product integrity.
What does an Assembly Supervisor do?
Key Responsibilities
- Oversee and coordinate the daily activities of production line workers, ensuring adherence to safety protocols and quality standards.
- Monitor production schedules and adjust workflow as needed to meet output targets and deadlines.
- Train new assembly technicians on proper procedures, machine operation, and quality control measures.
- Conduct regular inspections of work-in-progress and finished products to identify and resolve any defects or inefficiencies.
- Manage inventory of parts and materials on the assembly line, coordinating with procurement to prevent shortages.
- Implement continuous improvement initiatives to optimize assembly processes and reduce waste.
- Prepare daily production reports, documenting output, downtime, and any issues encountered during shifts.
Work Environment
An Assembly Supervisor primarily works on the manufacturing floor, which can be noisy and fast-paced, often requiring standing for extended periods. They spend significant time overseeing production lines, interacting directly with assembly workers, and troubleshooting issues. The role involves a mix of hands-on problem-solving and administrative tasks in an office or designated workstation.
Collaboration with other supervisors, engineers, and quality control personnel is constant. Work schedules often align with production shifts, which may include evenings, nights, or weekends, depending on the facility's operations. The environment emphasizes efficiency, safety, and continuous improvement, demanding a proactive and adaptable approach.
Tools & Technologies
Assembly supervisors regularly use various tools to manage production and teams. They utilize Manufacturing Execution Systems (MES) or Enterprise Resource Planning (ERP) software like SAP or Oracle to track production orders, inventory, and labor. For quality control, they employ measurement tools such as calipers, micrometers, and gauges, along with statistical process control (SPC) software.
Communication tools like two-way radios, walkie-talkies, and production line display boards are essential for real-time coordination. They also work with various hand and power tools used by their teams, ensuring proper calibration and maintenance. Knowledge of automation equipment and robotics, especially in modern assembly lines, becomes increasingly important for troubleshooting and oversight.
Assembly Supervisor Skills & Qualifications
An Assembly Supervisor oversees production processes and teams on the manufacturing floor. Qualifications for this role prioritize a blend of practical experience, leadership ability, and technical understanding of assembly operations. Entry-level supervisory roles often require significant hands-on experience as an assembler, coupled with demonstrated leadership potential. Senior supervisors, managing larger teams or more complex lines, need proven track records in process optimization and team development.
Requirements vary significantly by industry sector. In aerospace or medical device manufacturing, strict adherence to quality standards and regulatory compliance (e.g., ISO, FDA) is paramount, often demanding specific certifications or extensive training. In consumer electronics or automotive, efficiency, lean manufacturing principles, and rapid production cycles are key. Company size also plays a role; smaller companies might expect a supervisor to be more hands-on with assembly tasks, while larger organizations focus more on pure management and strategic oversight. Geographic location can influence labor laws and safety regulations, which supervisors must understand and enforce.
Formal education, such as an associate's degree in manufacturing technology or industrial management, provides a strong foundation but is not always a strict prerequisite. Practical experience, especially with continuous improvement methodologies like Lean or Six Sigma, often holds more weight. Certifications in these areas, or in production and inventory management (e.g., APICS CPIM), add significant value. The skill landscape is evolving with increasing automation and smart manufacturing; supervisors now need a basic understanding of robotics, IoT, and data analytics to effectively manage modern assembly lines. Balancing deep operational knowledge with broader leadership skills is crucial for career progression in this field.
Education Requirements
Technical Skills
- Lean Manufacturing Principles (5S, Kaizen, Value Stream Mapping)
- Six Sigma Methodologies and Statistical Process Control (SPC)
- Production Planning and Scheduling Software (e.g., ERP systems, MRP)
- Quality Management Systems (e.g., ISO 9001, AS9100, FDA regulations)
- Assembly Process Optimization and Workflow Analysis
- Tooling and Fixturing Selection and Maintenance
- Blueprint and Schematic Reading (mechanical, electrical, hydraulic)
- Inventory Management and Material Handling Techniques
- Safety Regulations and Procedures (OSHA, lockout/tagout)
- Basic Machine Operation and Troubleshooting
- Data Analysis and Reporting (production metrics, OEE)
- Resource Allocation and Capacity Planning
Soft Skills
- Leadership and Motivation: Inspires and guides assembly teams, fosters a positive work environment, and drives performance through effective coaching and feedback.
- Problem-Solving and Decision-Making: Quickly identifies root causes of production issues, implements effective solutions, and makes timely decisions under pressure to maintain production flow.
- Communication and Interpersonal Skills: Clearly conveys instructions, expectations, and feedback to team members, upper management, and other departments; effectively resolves conflicts.
- Adaptability and Flexibility: Adjusts to changing production schedules, material availability, and process improvements; manages unexpected challenges on the shop floor.
- Time Management and Organization: Prioritizes tasks, manages multiple production lines or projects simultaneously, and ensures efficient resource allocation to meet deadlines.
- Safety and Quality Focus: Champions and enforces safety protocols and quality standards, ensuring all products meet specifications and preventing workplace incidents.
- Coaching and Mentoring: Develops team members' skills, provides constructive criticism, and identifies opportunities for individual growth and continuous improvement.
- Team Building and Collaboration: Fosters a cohesive and collaborative team environment, encouraging mutual support and effective communication among assemblers.
How to Become an Assembly Supervisor
Becoming an Assembly Supervisor involves overseeing production teams and ensuring efficiency in manufacturing. Entry typically requires a blend of hands-on experience, leadership potential, and a solid understanding of assembly processes. While a bachelor's degree in engineering or operations management can accelerate entry, many successful supervisors start on the assembly line and advance through internal promotions.
The timeline for becoming an Assembly Supervisor varies significantly based on your starting point. Someone with direct manufacturing experience and proven leadership skills might transition into a supervisory role within 1-2 years. A complete beginner entering as an assembly worker could take 3-5 years to build the necessary experience and demonstrate readiness for promotion. Geographic location and the size of the manufacturing plant also play a role; larger facilities in industrial hubs often have more structured paths and frequent openings.
Overcoming barriers like lack of formal education often involves showcasing exceptional on-the-job performance, taking initiative, and pursuing certifications in lean manufacturing or Six Sigma. Networking within your current company and building relationships with senior management is crucial for identifying opportunities and gaining mentorship. Hiring managers prioritize practical experience, problem-solving abilities, and the capacity to motivate a team over solely academic credentials.
Step 1
Step 2
Step 3
Step 4
Step 5
Step 6
Education & Training Needed to Become an Assembly Supervisor
Becoming an Assembly Supervisor primarily relies on a blend of practical experience and targeted management training, rather than traditional four-year degrees. While a bachelor's degree in operations management or industrial engineering can be beneficial, it is not typically a prerequisite. Many successful supervisors begin as assembly line workers, gaining hands-on experience before moving into leadership roles through internal promotion or specialized certifications. The cost for formal degrees ranges from $40,000 to $100,000+ over four years, while specialized certifications or associate's degrees can cost $5,000 to $20,000, taking 6 months to two years.
Alternative learning paths, such as vocational training, online courses in lean manufacturing, or Six Sigma certifications, offer focused skills development. These options are often more cost-effective, ranging from a few hundred dollars for a single online course to several thousand for a comprehensive certification, with completion times from a few weeks to several months. Employers highly value practical experience and demonstrated leadership abilities. Certifications in areas like Lean Manufacturing, Six Sigma Green Belt, or OSHA safety standards significantly enhance a candidate's profile, showing commitment to quality and safety.
Continuous learning remains vital for Assembly Supervisors, particularly in adapting to new technologies, automation, and evolving production methodologies. Professional development often involves workshops on leadership, team building, and problem-solving. The most effective educational investment for an Assembly Supervisor combines on-the-job experience with targeted training in supervision, quality control, and operational efficiency, ensuring they can effectively manage teams and optimize production processes.
Assembly Supervisor Salary & Outlook
Compensation for an Assembly Supervisor varies significantly based on several factors. Geographic location plays a crucial role; areas with higher costs of living or strong manufacturing sectors typically offer higher salaries. For instance, supervisors in automotive or aerospace manufacturing hubs may earn more than those in regions with less specialized industries.
Experience and specific skill sets directly impact earning potential. Supervisors with extensive experience in lean manufacturing, Six Sigma, or advanced automation processes command higher salaries. Total compensation often extends beyond base salary to include performance bonuses tied to production targets, quality metrics, and safety records. Benefits packages, retirement contributions, and professional development allowances also add considerable value.
Company size and industry also influence pay. Larger corporations or those in high-precision manufacturing sectors generally offer more competitive salaries and benefits. Remote work is less common for this hands-on role, but some companies may offer hybrid models for administrative tasks, which can affect local salary expectations. International markets present different pay scales; the figures provided here are specific to the United States Dollar (USD) context, offering a benchmark for global comparisons.
Salary by Experience Level
Level | US Median | US Average |
---|---|---|
Assembly Team Lead | $62k USD | $65k USD |
Assembly Supervisor | $75k USD | $78k USD |
Senior Assembly Supervisor | $88k USD | $92k USD |
Assembly Manager | $105k USD | $110k USD |
Senior Assembly Manager | $128k USD | $135k USD |
Director of Assembly Operations | $160k USD | $170k USD |
Market Commentary
The job market for Assembly Supervisors remains stable with steady demand, driven by ongoing manufacturing activity across various sectors. The Bureau of Labor Statistics projects a moderate growth outlook for first-line supervisors of production and operating workers, which includes Assembly Supervisors, with about 5% growth over the next decade. This growth is slightly below the average for all occupations, reflecting increased automation in some areas.
Emerging opportunities lie in industries adopting advanced manufacturing technologies, such as smart factories and robotic assembly lines. Supervisors proficient in managing automated systems, data analysis, and cross-functional teams are in high demand. The supply of experienced supervisors often meets demand, though specialized industries may face shortages of candidates with specific technical expertise.
Future-proofing this role involves continuous learning in automation, digital tools, and supply chain management. While automation handles repetitive tasks, the need for human oversight, problem-solving, and team leadership remains critical. This role is generally recession-resistant as manufacturing is a foundational economic activity. Geographic hotspots for Assembly Supervisors include states with strong manufacturing bases, such as Michigan, Ohio, Texas, and California, where industrial expansion continues to create new roles.
Assembly Supervisor Career Path
Career progression for an Assembly Supervisor typically involves a blend of technical expertise, leadership development, and operational management. Individuals often begin in hands-on assembly roles, gaining deep practical knowledge before transitioning into supervisory positions. Advancement can follow either an individual contributor (IC) track, focusing on highly specialized technical assembly or process improvement, or a management track, leading teams and overseeing broader operations.
Advancement speed depends on several factors, including individual performance, the complexity of the products assembled, and the company's size and growth trajectory. Larger manufacturing firms often have more structured progression paths with distinct management layers, while smaller companies might offer quicker advancement for high performers willing to take on diverse responsibilities. Specialization in lean manufacturing, automation, or specific product lines enhances career opportunities.
Lateral movement is common, with supervisors often transitioning into roles like production planning, quality assurance, or continuous improvement. Networking within the industry and continuous learning, particularly in new assembly technologies or lean principles, significantly aid career growth. Certifications in Six Sigma or Lean Manufacturing are key milestones that mark professional development and increase promotability.
Assembly Team Lead
2-4 years total experienceKey Focus Areas
Assembly Supervisor
4-7 years total experienceKey Focus Areas
Senior Assembly Supervisor
7-10 years total experienceKey Focus Areas
Assembly Manager
10-15 years total experienceKey Focus Areas
Senior Assembly Manager
15-20 years total experienceKey Focus Areas
Director of Assembly Operations
20+ years total experienceKey Focus Areas
Assembly Team Lead
2-4 years total experienceDirect daily activities for a small team of assembly technicians, ensuring production targets are met. Provide on-the-job training and support to new hires. Address immediate operational issues and escalate complex problems to the supervisor. Maintain adherence to safety and quality standards within the team's work area.
Key Focus Areas
Develop foundational leadership skills, including delegation and conflict resolution. Gain proficiency in production scheduling and basic quality control methods. Focus on improving communication with team members and upper management. Understand safety protocols and ensure team compliance.
Assembly Supervisor
4-7 years total experienceOversee the entire assembly line or a significant production segment, managing multiple teams or shifts. Responsible for meeting daily and weekly production quotas, quality metrics, and cost targets. Conduct performance reviews for team leads and assembly technicians. Implement process improvements and ensure compliance with operational procedures.
Key Focus Areas
Master performance management techniques, including coaching and disciplinary actions. Deepen knowledge of lean manufacturing principles and waste reduction. Cultivate problem-solving abilities for production bottlenecks and quality deviations. Begin cross-functional collaboration with engineering and supply chain teams.
Senior Assembly Supervisor
7-10 years total experienceManage complex assembly operations, often across multiple product lines or shifts, with increased autonomy. Lead continuous improvement projects aimed at enhancing efficiency, reducing defects, and cutting costs. Collaborate extensively with cross-functional departments like R&D, logistics, and maintenance. Play a key role in budget planning and resource optimization for the assembly department.
Key Focus Areas
Develop strategic planning for production capacity and resource allocation. Acquire skills in project management for continuous improvement initiatives. Enhance data analysis capabilities to identify trends and drive operational efficiency. Mentor junior supervisors and contribute to departmental training programs.
Assembly Manager
10-15 years total experienceDirect all assembly operations within a plant or a major business unit, reporting to a senior manager or director. Responsible for the overall performance of assembly lines, including safety, quality, productivity, and cost efficiency. Develop and implement departmental strategies aligned with company goals. Manage a team of supervisors and team leads, fostering their professional growth.
Key Focus Areas
Cultivate strong leadership and team-building skills across multiple supervisory levels. Develop expertise in budget management, cost control, and capital expenditure planning. Master strategic workforce planning and talent development within the assembly function. Engage in supplier relationship management and production forecasting.
Senior Assembly Manager
15-20 years total experienceOversee multiple assembly plants or large-scale, complex assembly divisions, setting operational policies and long-term strategies. Accountable for multi-million dollar budgets and significant capital investments. Lead major organizational initiatives such as new product introductions, plant expansions, or technology upgrades. Mentor and develop a robust pipeline of leadership talent within the assembly function.
Key Focus Areas
Advance strategic leadership skills, influencing broader organizational objectives beyond assembly. Develop expertise in global supply chain dynamics and manufacturing trends. Master complex negotiations and stakeholder management at an executive level. Drive innovation in assembly processes and technology adoption.
Director of Assembly Operations
20+ years total experienceProvide executive leadership for all assembly and related manufacturing operations across the entire organization or a major global region. Responsible for setting the strategic vision for assembly, driving innovation, and ensuring operational excellence at scale. Influence company-wide policies related to production, quality, and supply chain. Represents the assembly function at the executive level, contributing to overall business strategy.
Key Focus Areas
Shape the company's overall manufacturing strategy, integrating assembly operations with business development. Lead organizational change management initiatives across multiple departments. Develop expertise in advanced manufacturing technologies, including automation and Industry 4.0. Build and maintain high-level industry partnerships and external relationships.
Job Application Toolkit
Ace your application with our purpose-built resources:
Assembly Supervisor Resume Examples
Proven layouts and keywords hiring managers scan for.
View examplesAssembly Supervisor Cover Letter Examples
Personalizable templates that showcase your impact.
View examplesTop Assembly Supervisor Interview Questions
Practice with the questions asked most often.
View examplesAssembly Supervisor Job Description Template
Ready-to-use JD for recruiters and hiring teams.
View examplesGlobal Assembly Supervisor Opportunities
Assembly Supervisors manage production lines globally, ensuring efficiency and quality. This role sees consistent international demand, particularly in manufacturing hubs across Asia, Europe, and North America. Regulatory differences in safety and labor laws impact operations. Professionals seek international roles for career advancement, exposure to diverse manufacturing techniques, and higher earning potential. No specific international certifications are broadly mandatory, but lean manufacturing or Six Sigma qualifications enhance global mobility.
Global Salaries
Salaries for Assembly Supervisors vary significantly by region and industrial sector. In North America, particularly the U.S. and Canada, supervisors earn between $55,000 and $80,000 USD annually. This range reflects higher purchasing power and robust benefit packages, including health insurance and retirement plans. European nations like Germany or the UK offer salaries from €45,000 to €65,000 (approximately $48,000-$70,000 USD), often with strong social security contributions and generous vacation allowances. While base salaries might seem lower, the cost of living in many parts of Europe can be higher than in some U.S. states.
In Asia-Pacific, countries like Japan and South Korea see supervisors earning ¥4.5 million to ¥7 million (approximately $30,000-$47,000 USD) and ₩40 million to ₩60 million (approximately $29,000-$43,000 USD) respectively. These figures consider a lower cost of living and different tax structures, often resulting in comparable take-home pay relative to local expenses. Latin American countries, such as Mexico or Brazil, typically offer $25,000 to $40,000 USD, reflecting a lower cost of living and often less comprehensive benefits. Experience and specialized industry knowledge, like in automotive or aerospace, significantly influence compensation across all regions. International pay scales are not standardized, but global corporations often have internal frameworks that adjust for local market conditions and cost of living.
Remote Work
International remote work opportunities for Assembly Supervisors are very limited. This role requires direct, on-site presence to manage production lines, oversee staff, and ensure quality control. While some administrative tasks, like scheduling or reporting, can be done remotely, the core functions demand physical supervision. Digital nomad visas are generally not applicable, as this role is not location-independent. Employers typically do not hire Assembly Supervisors for fully remote international positions.
Any 'remote' aspect would likely involve managing multiple local sites within a country or region, not across international borders. Companies might use virtual tools for inter-facility coordination, but the supervisor remains based at a physical plant. Salary expectations for this role are tied to the local industrial wage structure, with no significant geographic arbitrage potential from international remote work.
Visa & Immigration
Assembly Supervisors seeking international roles typically require skilled worker visas. Popular destinations include Germany, Canada, and Australia, which have robust manufacturing sectors. Germany's 'Blue Card' or skilled worker visas often require a recognized degree and a job offer meeting a salary threshold. Canada's Express Entry system assesses points for age, education, language proficiency, and work experience, often requiring an Educational Credential Assessment. Australia's Skilled Migration program also uses a points-based system, with specific occupations listed.
Professional licensing is not common for this role, but educational credential recognition is crucial. Visa timelines vary from a few months to over a year, depending on the country and application backlog. Pathways to permanent residency exist in many nations after several years of skilled employment. Language requirements, such as German for Germany or English for Canada/Australia, are often necessary for visa applications and workplace integration. Some countries may offer expedited processing for in-demand manufacturing roles. Family visas for dependents are usually available alongside the primary applicant's visa.
2025 Market Reality for Assembly Supervisors
Understanding current market conditions is crucial for Assembly Supervisors navigating career growth and job searches. The manufacturing landscape has undergone significant transformation from 2023 to 2025, driven by post-pandemic reshoring initiatives and the rapid integration of automation and AI. Broader economic factors, such as inflation and supply chain stability, directly influence production volumes and, consequently, hiring needs.
Market realities for Assembly Supervisors vary considerably by experience level, with senior roles commanding more demand due to their expertise in complex systems. Geographic regions with strong manufacturing bases, particularly those adopting advanced technologies, offer more opportunities. Company size also matters; larger enterprises often have more structured career paths and integrated AI systems, while smaller firms might offer broader responsibilities. This analysis provides an honest assessment of current hiring conditions and strategic considerations for this role.
Current Challenges
Supervisors face increased pressure to integrate automation and AI-driven tools into assembly processes, which demands new technical proficiencies. Competition for roles requiring advanced automation expertise is growing, as companies prioritize efficiency gains. Economic shifts and supply chain volatility can lead to unpredictable production schedules, challenging stable employment.
Entry-level saturation remains a concern in some areas, but experienced supervisors with adaptability stand out. Job searches for these specialized roles may extend for several months, particularly for those targeting specific industries or highly automated facilities.
Growth Opportunities
Despite challenges, strong demand exists for Assembly Supervisors adept at managing highly automated lines and integrating new technologies. Emerging opportunities lie in facilities focusing on advanced manufacturing, such as electric vehicle production, medical devices, and specialized electronics, where precision and efficiency are paramount. Supervisors with a proven track record in lean manufacturing principles and Six Sigma methodologies are highly sought after.
Professionals can gain an advantage by pursuing certifications in robotics operation, industrial automation, and data analytics for production optimization. Underserved markets often include regions with a growing need for domestic manufacturing capabilities, particularly in areas receiving government investment for infrastructure or green energy projects. Expertise in predictive maintenance systems and AI-driven quality control offers a significant competitive edge.
Market corrections, while disruptive, can create opportunities as companies restructure and invest in more efficient leadership for their assembly operations. Sectors that remain strong include defense, aerospace, and specialized industrial components, which prioritize resilience and high-quality output. Strategic career moves now involve upskilling in automation management and understanding how to leverage data for improved team performance and production flow.
Current Market Trends
Demand for Assembly Supervisors shows a mixed picture in 2025. While manufacturing output remains robust in many sectors, the increasing adoption of automation and robotics within assembly lines is reshaping the role. Companies seek supervisors who can manage both human teams and advanced machinery, shifting requirements from purely manual oversight to technological integration and optimization.
Economic conditions influence hiring, with some industries like automotive and electronics experiencing strong growth, while others tied to discretionary consumer spending face slight contractions. Layoffs have occurred in firms slow to adapt to new production methodologies, but those investing in smart manufacturing continue hiring. Generative AI impacts planning and predictive maintenance more than direct supervision, but supervisors need to understand its output.
Employers now prioritize supervisors with lean manufacturing certifications, robotics experience, and data analysis skills, beyond traditional leadership qualities. Salary trends are stable for experienced supervisors, but entry-level roles face more pressure from automation, leading to a flatter growth curve. Market saturation varies; highly automated facilities often struggle to find qualified candidates, while regions with older manufacturing infrastructure might see more competition. Remote work is generally not applicable, as the role requires on-site presence. Seasonal hiring patterns are less pronounced than cyclical industry demands.
Emerging Specializations
The manufacturing landscape transforms rapidly, driven by automation, artificial intelligence, and new material science. These advancements create new specialization opportunities for Assembly Supervisors. Understanding these future-oriented paths helps professionals strategically position themselves for next-generation roles.
Early positioning in emerging areas often commands premium compensation and accelerated career growth. Leaders in these specialized fields become indispensable as industries integrate advanced technologies. This strategic focus ensures relevance and competitive advantage in 2025 and beyond.
While established specializations remain vital, emerging areas offer significant upside. Many cutting-edge specializations are poised to become mainstream within the next three to five years, leading to a substantial increase in job opportunities. Pursuing these areas involves a calculated risk, but the potential rewards in career progression and impact are considerable for those who adapt and innovate.
Automated Assembly & Cobot Integration Supervisor
This specialization focuses on overseeing assembly lines integrated with advanced robotics and collaborative robots (cobots). The supervisor ensures seamless interaction between human workers and automated systems, optimizing workflows and troubleshooting complex robotic processes. This role is crucial as more manufacturers adopt lights-out or highly automated facilities.
Additive Manufacturing Assembly Supervisor
This area involves supervising the assembly of products using advanced additive manufacturing techniques, such as 3D printing for components or final products. The supervisor manages quality control, material handling for specialized filaments or powders, and post-processing for these unique manufacturing methods. This is vital for customized production and rapid prototyping.
AR/VR Guided Assembly Supervisor
This specialization focuses on leading assembly teams in environments that leverage Augmented Reality (AR) or Virtual Reality (VR) for training, guidance, and quality inspection. The supervisor manages the deployment of AR/VR tools, interprets data from these systems, and ensures their effective use to enhance assembly precision and efficiency. This improves complex assembly tasks.
Smart Product & IoT Assembly Supervisor
This role centers on supervising assembly operations for products incorporating advanced sensor technologies, IoT devices, or embedded intelligence. The supervisor ensures the precise integration and calibration of these smart components, managing complex wiring, software flashing, and initial functional testing for connected devices. This is essential for smart products.
Sustainable & Circular Assembly Supervisor
This specialization involves overseeing assembly lines with a strong emphasis on sustainable practices, including minimizing waste, optimizing energy consumption, and integrating recycled or sustainable materials. The supervisor manages processes for disassembly, repair, and circular economy principles within the assembly process, extending product lifecycle. This is critical for environmental compliance.
Pros & Cons of Being an Assembly Supervisor
Making informed career decisions requires a clear understanding of both the benefits and challenges associated with a role. The experience of an Assembly Supervisor can vary significantly based on the specific industry, company size, production complexity, and the supervisor's individual management style. What one person views as a benefit, such as a fast-paced environment, another might see as a challenge. These factors also influence the day-to-day realities and long-term career progression. This assessment provides an honest look at the advantages and disadvantages of this specific role, helping aspiring supervisors set realistic expectations at different stages of their careers.
Pros
- Assembly Supervisors gain valuable leadership and team management experience, overseeing diverse groups of workers and developing skills in motivation, training, and performance evaluation.
- This role offers strong job stability and consistent demand across various manufacturing sectors, as companies always need skilled individuals to ensure efficient production lines.
- Supervisors play a direct role in product quality and operational efficiency, providing a sense of accomplishment and immediate feedback on their contributions to the manufacturing process.
- The position often comes with competitive hourly wages or salaries, along with benefits packages, reflecting the responsibility and critical nature of overseeing production.
- There are frequent opportunities for problem-solving, as supervisors troubleshoot production bottlenecks, equipment issues, and quality control challenges, which keeps the work engaging and intellectually stimulating.
- Assembly Supervisors build practical knowledge of manufacturing processes, lean principles, and supply chain dynamics, which are highly transferable skills applicable to other operational roles.
- Many companies offer internal training and development programs for supervisors, providing pathways for skill enhancement and potential advancement into higher-level management or operations roles.
Cons
- Assembly Supervisors often work in noisy, fast-paced factory environments, which can be physically demanding and expose them to repetitive tasks or standing for long periods.
- Managing a diverse team of assembly line workers requires strong conflict resolution and motivational skills, as supervisors frequently deal with interpersonal issues, performance discrepancies, and morale challenges.
- Supervisors are directly responsible for meeting production quotas and deadlines, leading to high-pressure situations, especially when facing equipment breakdowns, material shortages, or staffing issues.
- The role often demands irregular hours, including early mornings, late nights, or weekend shifts, particularly during peak production periods or when troubleshooting critical operational problems.
- Career advancement opportunities may be limited within the same company without further education or transitioning into broader operations management or quality control roles.
- Assembly Supervisors must enforce safety protocols and quality standards rigorously, which can be challenging when balancing efficiency targets with compliance, potentially leading to difficult disciplinary conversations.
- The job requires continuous learning and adaptation to new assembly techniques, machinery, and product designs, demanding ongoing training and a willingness to embrace change in manufacturing processes.
Frequently Asked Questions
Assembly Supervisors face unique challenges in balancing production targets with team leadership and quality control. This section addresses key questions about transitioning into this role, from managing diverse teams to optimizing production lines and maintaining safety standards effectively.
What are the typical entry requirements and prior experience needed to become an Assembly Supervisor?
Most Assembly Supervisors gain experience by working in assembly roles first, often for 3-5 years, before moving into a supervisory position. Some companies prefer candidates with a technical degree or certification in manufacturing, but practical experience and demonstrated leadership skills are often more critical. Strong communication and problem-solving abilities are essential for success.
How long does it typically take to transition into an Assembly Supervisor role?
The timeline to become an Assembly Supervisor varies significantly based on individual experience and company structure. An internal promotion from an assembly line worker might take 3-7 years, while an external candidate with relevant leadership experience could secure a role faster. Developing strong leadership qualities and a deep understanding of production processes can accelerate this path.
What are the salary expectations and potential for financial growth as an Assembly Supervisor?
Salary expectations for Assembly Supervisors vary widely by industry, location, and company size. Entry-level supervisors might expect to earn between $45,000 and $60,000 annually, while experienced supervisors in high-demand sectors or with specialized skills could earn $70,000 or more. Overtime pay can also significantly increase earnings due to production demands.
What is the typical work-life balance like for an Assembly Supervisor, considering shift work and production demands?
Work-life balance as an Assembly Supervisor can be challenging, often involving long hours, especially during peak production periods or when addressing unexpected issues. Many roles require working shifts, including nights or weekends, to oversee continuous operations. The role demands constant attention to production flow, quality, and team dynamics, which can impact personal time.
Is the Assembly Supervisor role a secure career path, and what is the market demand for this position?
Job security for Assembly Supervisors is generally stable, as manufacturing and assembly operations remain critical to many industries. The demand for skilled supervisors who can optimize production and manage teams effectively is consistent. However, economic downturns or automation advancements could influence the number and nature of available positions.
What are the potential career growth opportunities and advancement paths for an Assembly Supervisor?
Career growth for an Assembly Supervisor often includes advancement to Production Manager, Operations Manager, or even Plant Manager roles within a manufacturing facility. Specialized training in lean manufacturing, Six Sigma, or supply chain management can open doors to higher-level positions. Some supervisors also transition into training or quality assurance management.
What are the most significant challenges or stressors unique to the Assembly Supervisor role?
The biggest challenge for Assembly Supervisors often involves managing diverse teams, ensuring consistent quality, and meeting tight production deadlines. They must also handle equipment malfunctions, supply chain disruptions, and maintain strict safety protocols. Balancing these responsibilities while motivating a team requires strong leadership and problem-solving skills.
Does the Assembly Supervisor role offer any remote work flexibility or opportunities for travel?
Assembly Supervisor roles are almost exclusively on-site, as they require direct oversight of production lines, equipment, and personnel. Remote work is generally not feasible for this position due to the hands-on nature of managing assembly operations. Travel is typically limited to occasional visits to other plant locations or supplier sites.
Related Careers
Explore similar roles that might align with your interests and skills:
Assembler
A growing field with similar skill requirements and career progression opportunities.
Explore career guideAssembly Operator
A growing field with similar skill requirements and career progression opportunities.
Explore career guideAssembly Technician
A growing field with similar skill requirements and career progression opportunities.
Explore career guideManufacturing Supervisor
A growing field with similar skill requirements and career progression opportunities.
Explore career guideProduction Supervisor
A growing field with similar skill requirements and career progression opportunities.
Explore career guideAssess your Assembly Supervisor readiness
Understanding where you stand today is the first step toward your career goals. Our Career Coach helps identify skill gaps and create personalized plans.
Skills Gap Analysis
Get a detailed assessment of your current skills versus Assembly Supervisor requirements. Our AI Career Coach identifies specific areas for improvement with personalized recommendations.
See your skills gapCareer Readiness Assessment
Evaluate your overall readiness for Assembly Supervisor roles with our AI Career Coach. Receive personalized recommendations for education, projects, and experience to boost your competitiveness.
Assess your readinessSimple pricing, powerful features
Upgrade to Himalayas Plus and turbocharge your job search.
Himalayas
Himalayas Plus
Himalayas Max
Find your dream job
Sign up now and join over 100,000 remote workers who receive personalized job alerts, curated job matches, and more for free!
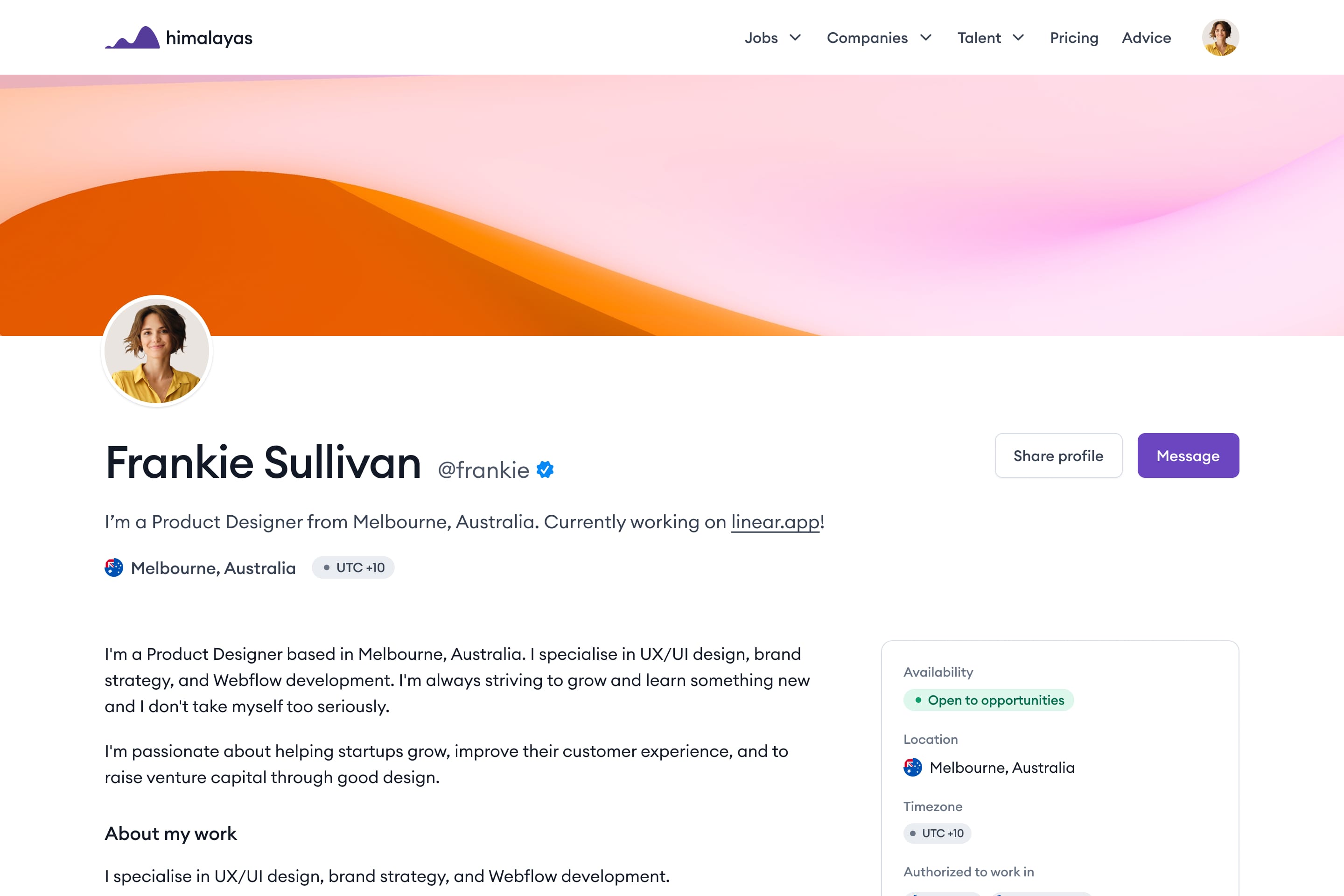