5 Precision Lens Centerer and Edger Interview Questions and Answers
Precision Lens Centerers and Edgers are skilled professionals responsible for aligning, shaping, and finishing optical lenses to exact specifications. They work with specialized machinery to ensure lenses meet precise standards for use in eyewear, scientific instruments, or industrial applications. Junior roles focus on learning equipment operation and basic tasks, while senior and lead roles involve overseeing quality control, training others, and managing complex projects. Need to practice for an interview? Try our AI interview practice for free then unlock unlimited access for just $9/month.
Unlimited interview practice for $9 / month
Improve your confidence with an AI mock interviewer.
No credit card required
1. Precision Lens Technician Interview Questions and Answers
1.1. Can you describe a time when you had to troubleshoot an issue with lens fabrication? What steps did you take to identify and resolve the problem?
Introduction
This question is important for assessing your problem-solving skills and technical knowledge in lens fabrication, which are critical for a Precision Lens Technician.
How to answer
- Use the STAR method (Situation, Task, Action, Result) to structure your response.
- Clearly describe the situation and the specific issue you encountered during the lens fabrication process.
- Detail the steps you took to diagnose the problem, including any tools or techniques used.
- Explain the resolution process and any adjustments made to improve the outcome.
- Share the results of your actions, including any metrics or feedback from colleagues or supervisors.
What not to say
- Vague descriptions of problems without specific details.
- Failing to mention the tools or methods you used to troubleshoot.
- Taking sole credit for solving a team issue without acknowledging collaboration.
- Neglecting to discuss the outcome or lessons learned.
Example answer
“At a previous position with Nikon Canada, we faced an issue with lens distortion that affected quality control. I used precision measurement tools to identify the source of the distortion, which turned out to be an incorrect calibration in our grinding machine. I recalibrated the machine and reran the affected batches, which improved the quality by 30%. This experience taught me the importance of meticulous calibration and prompt action in maintaining quality standards.”
Skills tested
Question type
1.2. How do you ensure precision and accuracy when working with optical lenses?
Introduction
This question evaluates your understanding of precision work and the techniques you implement to maintain high standards in optical lens production.
How to answer
- Discuss the specific tools and equipment you use to measure and verify precision.
- Explain your process for quality checks and how you minimize errors.
- Mention any standards or protocols you adhere to for lens fabrication.
- Describe how you handle discrepancies in measurements and what steps you take to correct them.
- Share any relevant certifications or training that enhance your precision work.
What not to say
- Suggesting that you rely solely on intuition without using tools.
- Failing to mention quality control processes.
- Overlooking the importance of documentation and record-keeping.
- Neglecting to emphasize the impact of precision on end-user satisfaction.
Example answer
“I utilize a combination of digital calipers and optical comparators to ensure precision when fabricating lenses. I follow strict quality control protocols that include multiple checks at each stage of production. For instance, I always cross-verify measurements against established standards for each lens type. In my previous role at Essilor, these practices helped us achieve a 98% pass rate in our quality assurance checks, significantly reducing rework costs.”
Skills tested
Question type
2. Junior Precision Lens Centerer and Edger Interview Questions and Answers
2.1. Can you describe a time when you had to troubleshoot a precision lens alignment issue?
Introduction
This question is vital for assessing your problem-solving skills and technical knowledge in precision lens centering, which are essential for a Junior Precision Lens Centerer and Edger.
How to answer
- Use the STAR method to structure your response: Situation, Task, Action, Result.
- Clearly describe the issue you faced in the lens alignment process.
- Explain the steps you took to diagnose and troubleshoot the issue.
- Discuss any tools or techniques you used to resolve the problem.
- Share the outcome and any lessons learned that could be applied in future situations.
What not to say
- Avoid vague descriptions that lack specific detail about the problem.
- Do not focus solely on the technical aspects without discussing your thought process.
- Steer clear of blaming others for the issue without taking responsibility for finding a solution.
- Avoid discussing situations where you did not take initiative or learn from the experience.
Example answer
“During my internship at a local optical lab, I encountered a lens that was consistently misaligned during the edging process. I first checked the machinery for calibration issues and found that the centering device was slightly off. I recalibrated the equipment and re-centered the lens, which resolved the issue. As a result, the quality of finished lenses improved, and I learned the importance of regular equipment checks.”
Skills tested
Question type
2.2. How do you ensure quality control in your work when centering and edging lenses?
Introduction
This question evaluates your understanding of quality control processes, which are critical in ensuring that lenses meet specifications and customer satisfaction.
How to answer
- Describe specific quality control measures you follow in the lens centering and edging process.
- Explain how you verify your work against quality standards.
- Discuss any tools or technologies you use for quality assurance.
- Share examples of how you have corrected mistakes or improved processes based on quality checks.
- Highlight the importance of feedback loops in maintaining high-quality standards.
What not to say
- Avoid saying that you do not have a quality control process in place.
- Do not mention quality checks that are not relevant to lens work.
- Steer clear of vague or generic answers that lack specific examples.
- Avoid discussing a lack of understanding of quality control concepts.
Example answer
“In my previous role, I implemented a double-check system where I would verify my work against the specifications before finalizing the lenses. I used calipers and optical comparators to ensure precise measurements. Additionally, I always sought feedback from senior technicians to identify areas for improvement. This process helped reduce rework and increase overall quality.”
Skills tested
Question type
3. Precision Lens Centerer and Edger Interview Questions and Answers
3.1. Can you describe your experience with precision lens centering and edging, including the tools and techniques you have used?
Introduction
This question is crucial as it evaluates your technical expertise and familiarity with the specific equipment and processes necessary for lens centering and edging in optical manufacturing.
How to answer
- Begin with a brief overview of your background in lens centering and edging
- List the specific tools and machinery you have experience with, such as digital edging machines or manual tools
- Explain the techniques you employ to ensure precision and accuracy in your work
- Discuss any relevant certifications or training you have received
- Highlight your understanding of quality control measures in the lens manufacturing process
What not to say
- Vague descriptions without specific tools or techniques
- Overemphasizing theoretical knowledge without practical experience
- Failing to mention any quality control or safety measures
- Not providing examples of problem-solving in past roles
Example answer
“During my time at Essilor, I worked extensively with a digital edging machine, ensuring precision by calibrating the equipment before each batch. I used techniques like the 'three-point alignment' method for centering the lenses accurately. Additionally, I completed a training program in optical lens manufacturing, which deepened my understanding of quality control processes. This hands-on experience taught me the importance of precision and attention to detail in producing high-quality lenses.”
Skills tested
Question type
3.2. Describe a challenging situation you faced while centering or edging lenses and how you resolved it.
Introduction
This question assesses your problem-solving skills and ability to handle challenges in a pressure-driven environment, which is vital in precision optics work.
How to answer
- Use the STAR method (Situation, Task, Action, Result) to structure your response
- Describe the specific challenge you encountered in detail
- Explain the steps you took to resolve the issue, including any collaboration with colleagues
- Highlight the outcome and what you learned from the experience
- Mention any changes you implemented to prevent similar issues in the future
What not to say
- Focusing solely on the problem without discussing the solution
- Failing to demonstrate an understanding of teamwork in solving the issue
- Avoiding personal accountability or learning from the experience
- Providing a resolution that lacks measurable results or improvements
Example answer
“At my previous job with Luxottica, I faced a situation where a batch of lenses was consistently coming out misaligned. I gathered the team to troubleshoot, and we discovered an issue with the calibration of the edging machine. I worked on recalibrating the equipment, and after retesting, we achieved perfect alignment. This experience taught me the importance of teamwork and proactive problem-solving, and I later implemented a more rigorous calibration schedule to avoid future issues.”
Skills tested
Question type
4. Senior Precision Lens Centerer and Edger Interview Questions and Answers
4.1. Can you describe a time when you faced a significant challenge in precision lens centering and how you overcame it?
Introduction
This question assesses your problem-solving abilities and technical expertise specific to precision lens centering, which is critical for ensuring high-quality optical products.
How to answer
- Start by clearly outlining the specific challenge you encountered with lens centering.
- Describe the steps you took to analyze the problem and identify the root cause.
- Explain the solution you implemented and any adjustments made to your process.
- Highlight the outcomes, focusing on improvements in precision and efficiency.
- Mention any lessons learned that could help in future situations.
What not to say
- Neglecting to explain the context or technical details of the challenge.
- Focusing solely on the technical aspects without discussing your thought process.
- Failing to mention measurable results or improvements post-solution.
- Avoiding discussion of teamwork or collaboration if applicable.
Example answer
“At Zeiss, I encountered a significant issue with the alignment of lenses, resulting in a high rejection rate. After thorough analysis, I discovered the calibration of our centering equipment was off. I recalibrated the machines and implemented a new routine for regular checks. This reduced our rejection rate by 30% and improved overall production efficiency. This experience taught me the importance of meticulous equipment maintenance and proactive problem-solving.”
Skills tested
Question type
4.2. How do you ensure quality control throughout the lens edging process?
Introduction
This question evaluates your understanding of quality control measures and your ability to maintain high standards in lens production, which is vital for customer satisfaction.
How to answer
- Describe your approach to establishing quality control checkpoints during the edging process.
- Discuss specific tools or technologies you use for quality assessment.
- Explain how you train and guide your team to adhere to quality standards.
- Share examples of how you have responded to quality issues in the past.
- Highlight the importance of continuous improvement and feedback loops.
What not to say
- Providing vague answers without specific quality control methods.
- Ignoring the role of teamwork in maintaining quality standards.
- Failing to mention any tools or technologies used in the process.
- Neglecting the importance of customer feedback in quality assurance.
Example answer
“In my previous role at Essilor, I implemented a multi-step quality control process that included both visual inspection and automated measurements at each stage of lens edging. I also trained my team on the importance of meticulous checks and encouraged them to report any discrepancies immediately. This proactive approach resulted in a 20% decrease in post-production errors and improved customer satisfaction ratings significantly.”
Skills tested
Question type
5. Lead Precision Lens Technician Interview Questions and Answers
5.1. Can you describe a complex lens calibration project you worked on and how you ensured precision throughout the process?
Introduction
This question assesses your technical expertise in lens calibration, attention to detail, and problem-solving skills, which are crucial for a lead technician role.
How to answer
- Start by detailing the specifics of the calibration project, including the type of lenses and the precision requirements.
- Explain the tools and technology you used for calibration and why they were appropriate for the task.
- Describe the steps you took to ensure accuracy and precision during the calibration process.
- Discuss any challenges you faced and how you overcame them.
- Quantify your results, such as improvements in lens performance or reductions in error rates.
What not to say
- Providing vague descriptions without technical details.
- Failing to mention the tools or methods used in the calibration process.
- Overlooking the importance of precision or quality control in your response.
- Not acknowledging any challenges faced or lessons learned.
Example answer
“At a previous role with a lens manufacturing company, I led a project to calibrate high-precision optical lenses for medical equipment. Utilizing advanced calibration tools, I implemented a multi-step process that included laser interferometry to ensure accuracy. Despite initial discrepancies in measurements, I conducted a thorough analysis and adjusted our calibration methods, leading to a 30% reduction in error margins and ensuring compliance with medical standards.”
Skills tested
Question type
5.2. How do you approach training and mentoring junior technicians in precision lens technology?
Introduction
This question evaluates your leadership and mentorship capabilities, which are essential for a lead position in any technical field.
How to answer
- Describe your approach to mentorship and how you customize it for each mentee.
- Share specific examples of training programs or initiatives you have implemented.
- Explain how you assess the progress of junior technicians and provide constructive feedback.
- Discuss the importance of hands-on experience and how you incorporate it into training.
- Highlight any measurable outcomes from your mentorship efforts, such as improved performance or reduced error rates.
What not to say
- Implying that mentoring is not part of your role.
- Providing vague examples without concrete impacts on mentees.
- Focusing only on technical skills without addressing soft skills.
- Neglecting to mention how you adapt your mentoring style to different learning paces.
Example answer
“In my previous position at a precision optics firm, I developed a structured training program for junior technicians that combined theoretical learning with practical, hands-on experience on calibration equipment. I scheduled regular feedback sessions to assess their progress, which led to a 20% increase in their calibration accuracy within three months. I believe that fostering an open environment encourages questions and builds confidence in their skills.”
Skills tested
Question type
Similar Interview Questions and Sample Answers
Simple pricing, powerful features
Upgrade to Himalayas Plus and turbocharge your job search.
Himalayas
Himalayas Plus
Himalayas Max
Find your dream job
Sign up now and join over 100,000 remote workers who receive personalized job alerts, curated job matches, and more for free!
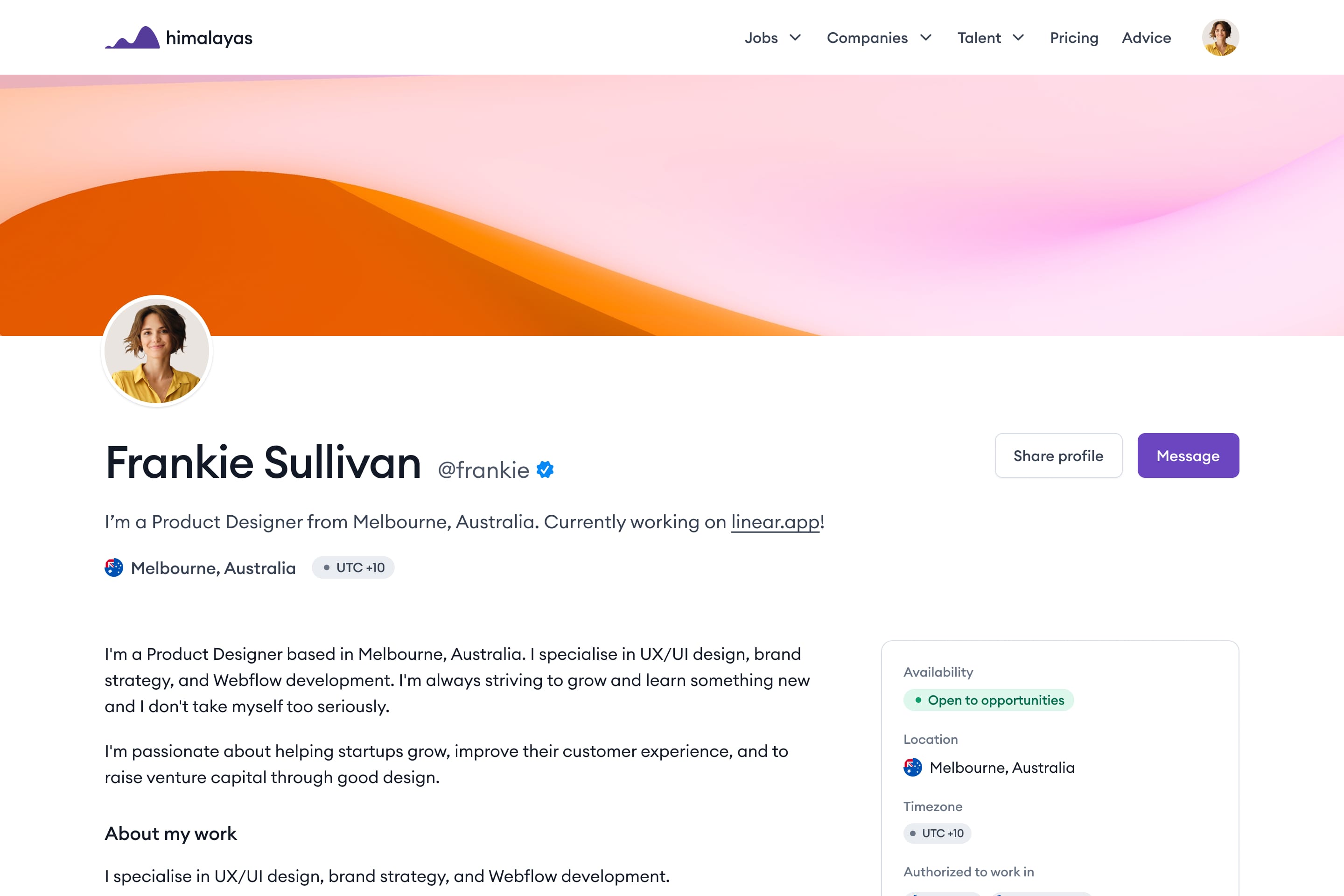