4 Gage Designer Interview Questions and Answers
Gage Designers specialize in creating precision tools and measurement devices used in manufacturing and quality control processes. They design and develop gages to ensure components meet exact specifications and tolerances. Junior designers typically assist in drafting and basic design tasks, while senior and lead designers take on complex projects, oversee teams, and ensure adherence to industry standards. Need to practice for an interview? Try our AI interview practice for free then unlock unlimited access for just $9/month.
Unlimited interview practice for $9 / month
Improve your confidence with an AI mock interviewer.
No credit card required
1. Junior Gage Designer Interview Questions and Answers
1.1. Can you describe a project where you had to create a gage design from scratch?
Introduction
This question assesses your technical skills and creativity in gage design, which are essential for a Junior Gage Designer.
How to answer
- Use the STAR method to structure your response: Situation, Task, Action, Result.
- Briefly describe the project and its requirements.
- Explain the design process you followed, including software and tools used.
- Detail any challenges faced and how you overcame them.
- Highlight the final outcome and any positive feedback received.
What not to say
- Providing a vague description without specifics on tools or processes.
- Focusing too much on challenges without mentioning solutions.
- Neglecting to discuss collaboration with team members.
- Avoiding metrics or results that demonstrate the success of your design.
Example answer
“In my internship at SNC-Lavalin, I was tasked with designing a gage for a new component in a manufacturing process. I started by gathering requirements from the engineering team and then used SolidWorks to create the initial design. The biggest challenge was ensuring accuracy, which I addressed by running multiple simulations. The final design was implemented in production, leading to a 15% increase in efficiency, and I received commendations from my supervisors for my thorough approach.”
Skills tested
Question type
1.2. How do you ensure that your gage designs meet industry standards and regulations?
Introduction
This question evaluates your knowledge of industry standards and your attention to detail, which are crucial for ensuring safety and compliance in gage design.
How to answer
- Discuss specific standards relevant to gage design (e.g., ASME, ISO).
- Explain your process for researching and staying updated on these standards.
- Describe how you incorporate these standards into your design process.
- Share an example where adhering to standards was critical.
- Mention any tools or resources you use for compliance checks.
What not to say
- Claiming that standards are not important in your design process.
- Providing generic answers without demonstrating specific knowledge.
- Failing to mention any examples or experiences related to compliance.
- Overlooking the role of teamwork in ensuring compliance.
Example answer
“In my previous role, I regularly utilized ASME standards for gage design. I kept myself updated by attending webinars and reading industry publications. For a project involving pressure gages, I made sure to follow the relevant ISO regulations, which included conducting rigorous testing to ensure accuracy. This diligence helped us avoid costly redesigns and ensured that our products were compliant right from the start.”
Skills tested
Question type
2. Gage Designer Interview Questions and Answers
2.1. Can you describe a project where you designed a gage that improved production efficiency?
Introduction
This question evaluates your practical experience and ability to create effective gage designs that enhance manufacturing processes, which is crucial for a Gage Designer role.
How to answer
- Start by outlining the context of the project and the production challenge faced
- Describe the design process you followed, including any calculations or software used
- Explain how your gage design addressed the specific issues in production
- Quantify the impact of your design on efficiency or quality metrics
- Discuss any feedback you received from the production team and any iterative improvements made
What not to say
- Providing vague descriptions without specific metrics or outcomes
- Failing to mention collaboration with other teams or departments
- Overlooking the importance of testing and validation of your gage
- Describing a project that didn't lead to measurable improvements
Example answer
“At Rolls-Royce, I designed a gage to measure the tolerances of turbine blades, which were causing production delays. By utilizing CAD software, I created a non-contact measurement gage that reduced set-up times by 30%. Post-implementation, we saw a 20% increase in production efficiency. The production team appreciated the improved accuracy and time savings, leading to further collaboration on future projects.”
Skills tested
Question type
2.2. How do you ensure that your gage designs comply with industry standards and regulations?
Introduction
This question assesses your knowledge of compliance and standards in gage design, which is vital for maintaining quality and safety in manufacturing.
How to answer
- Discuss your familiarity with relevant industry standards such as ISO, ASME, or specific sector regulations
- Explain your approach to integrating these standards into your design process
- Share examples of how you have adapted a design to meet compliance requirements
- Describe any tools or resources you use to stay updated on industry standards
- Mention the importance of documentation and audits in maintaining compliance
What not to say
- Claiming you don't keep up with industry standards
- Focusing solely on your design skills without mentioning compliance
- Suggesting that compliance is not a priority for your work
- Providing examples that show a lack of awareness of relevant regulations
Example answer
“I always start my gage designs by reviewing applicable ISO standards, such as ISO 9001 for quality management. For instance, when I designed a gage for a precision engineering firm, I ensured it met ASME standards by conducting thorough checks during the design phase and documenting all compliance measures. I regularly attend industry seminars and training to keep updated, ensuring that our designs not only meet but exceed compliance requirements.”
Skills tested
Question type
3. Senior Gage Designer Interview Questions and Answers
3.1. Can you describe a project where you had to design a gage for a complex component? What challenges did you face?
Introduction
This question assesses your technical expertise in gage design and your problem-solving abilities when faced with complex requirements.
How to answer
- Use the STAR method to structure your response: Situation, Task, Action, Result.
- Clearly define the project requirements and the complexity of the component.
- Discuss the specific challenges encountered, such as geometric constraints or material properties.
- Explain the design process you followed, including tools and software used.
- Quantify the results, such as improvements in accuracy or reductions in production time.
What not to say
- Focusing only on the challenges without discussing the solutions.
- Neglecting to mention the tools or techniques used in the design process.
- Providing vague responses without specific examples.
- Failing to highlight lessons learned or improvements made.
Example answer
“In my role at Tata Technologies, I was tasked with designing a gage for a complex automotive component with tight tolerances. The challenge was to ensure the gage could accurately measure multiple features simultaneously. I utilized 3D CAD software to create a modular design that addressed these complexities, and through prototyping, we achieved a 30% reduction in assembly time. This project not only improved our measurement accuracy but also enhanced the overall production efficiency.”
Skills tested
Question type
3.2. How do you stay updated with the latest trends and technologies in gage design?
Introduction
This question seeks to understand your commitment to continuous learning and professional development in a rapidly evolving field.
How to answer
- Mention specific resources you use, such as industry journals, online courses, or professional organizations.
- Discuss attending workshops, webinars, or conferences relevant to gage design.
- Share examples of how you have applied new knowledge to your work.
- Explain the importance of staying current for the quality and innovation in your designs.
- Express a genuine passion for the field and a desire to leverage new technologies.
What not to say
- Indicating you do not engage in any form of continuous learning.
- Providing generic answers about using the internet without specifics.
- Failing to mention any practical application of new knowledge.
- Showing disinterest in industry advancements.
Example answer
“I regularly read industry publications like 'Quality Magazine' and am a member of the American Society for Quality. I also attend annual conferences focused on metrology and gage design, which allow me to network and learn about emerging technologies. For instance, after attending a recent webinar on digital gaging technologies, I implemented a new digital measuring tool that increased our measurement efficiency by 25%.”
Skills tested
Question type
4. Lead Gage Designer Interview Questions and Answers
4.1. Can you describe a complex gage design project you led from concept to completion?
Introduction
This question is important for evaluating your technical expertise, project management skills, and ability to deliver results in gage design, which is critical for ensuring precision in manufacturing processes.
How to answer
- Start by outlining the project's scope and objectives
- Detail your approach to the design process, including any software or tools used
- Discuss the collaboration with cross-functional teams, such as engineering and quality assurance
- Highlight challenges faced during the project and how you overcame them
- Conclude with the project's impact on the organization, including any metrics or feedback received
What not to say
- Failing to provide specifics about the project or your role
- Overemphasizing technical jargon without explaining their relevance
- Not mentioning team collaboration or contributions from others
- Ignoring the project outcomes or learnings
Example answer
“At Toyota, I led the design of a new gage system for measuring engine components. I started by gathering requirements from production engineers and using SolidWorks for the design. Throughout the project, I coordinated with the QA team to ensure compliance with ISO standards. A key challenge was refining the design for better accuracy, which we solved through iterative testing. Ultimately, the new gage reduced measurement errors by 30%, significantly enhancing production efficiency. This project reinforced my belief in the importance of teamwork and continuous improvement.”
Skills tested
Question type
4.2. How do you ensure that your gage designs meet industry standards and customer specifications?
Introduction
This question assesses your knowledge of industry standards, attention to detail, and your methodology for ensuring compliance in your designs, which is essential for maintaining quality and customer satisfaction.
How to answer
- Explain your familiarity with relevant industry standards (e.g., ISO, ASME)
- Describe your process for reviewing customer specifications and integrating feedback
- Discuss any quality control measures you implement during the design phase
- Share examples of how you have adapted designs based on standards or client feedback
- Mention any tools or software that assist you in ensuring compliance
What not to say
- Indicating that standards are not a priority in your design process
- Providing vague responses without specific examples or processes
- Ignoring customer specifications or feedback
- Failing to mention any quality assurance practices
Example answer
“In my role at Mitsubishi, I make it a priority to stay updated on ISO standards applicable to gage design. I start every project by closely reviewing customer specifications and ensuring they align with these standards. During the design phase, I perform regular checks and utilize software like CAD to simulate compliance. For instance, when a customer requested a modification to a gage for a new product line, I quickly adapted our design, ensuring it met both their needs and the relevant standards. This proactive approach has helped maintain a 98% customer satisfaction rate in my projects.”
Skills tested
Question type
Similar Interview Questions and Sample Answers
Simple pricing, powerful features
Upgrade to Himalayas Plus and turbocharge your job search.
Himalayas
Himalayas Plus
Himalayas Max
Find your dream job
Sign up now and join over 100,000 remote workers who receive personalized job alerts, curated job matches, and more for free!
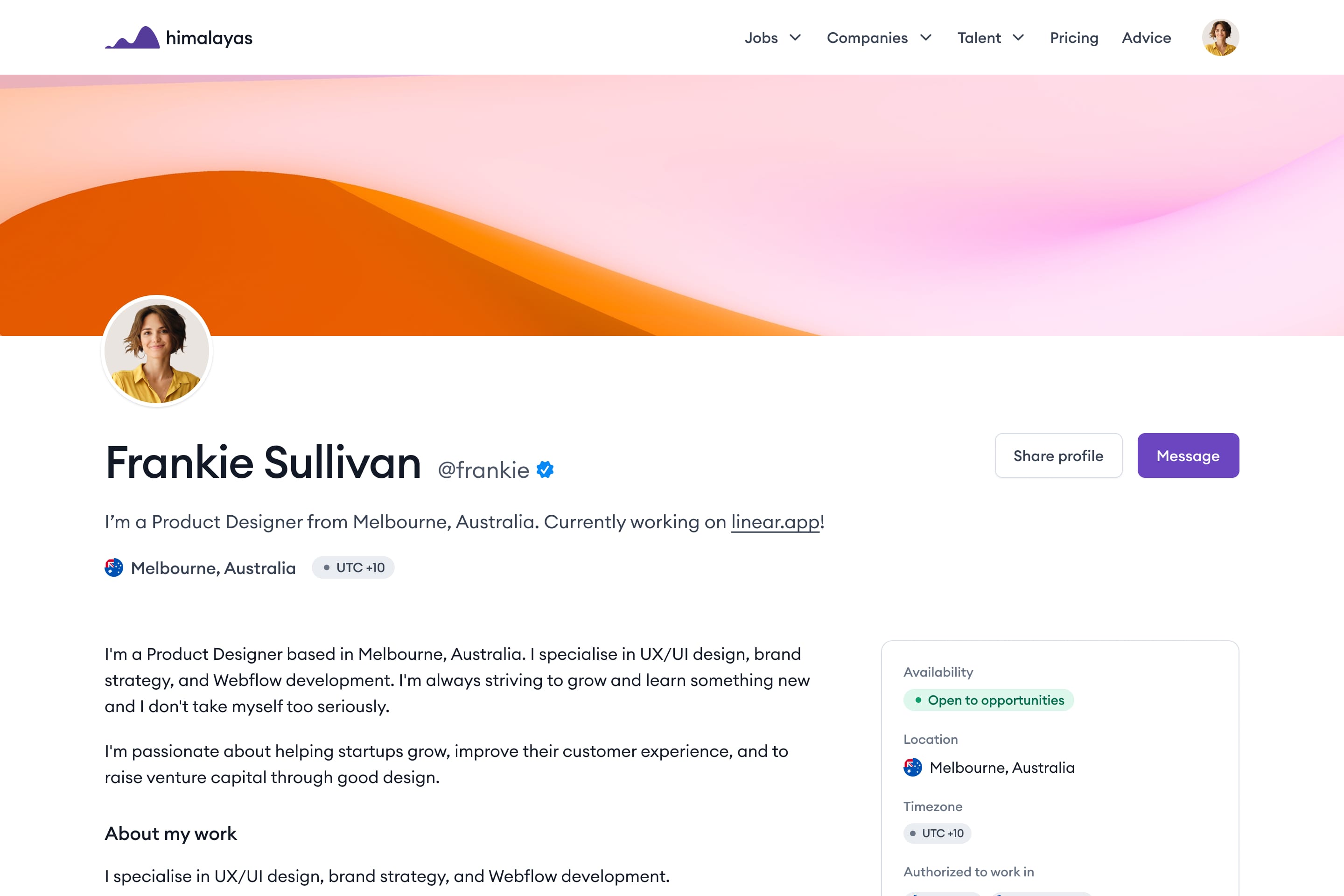