Complete Pottery Kiln Builder Career Guide
Pottery kiln builders are specialized artisans and engineers who design, construct, and maintain the high-temperature furnaces essential for transforming raw clay into durable ceramic art and functional ware. This unique craft requires a deep understanding of thermodynamics, material science, and safety protocols, ensuring kilns operate efficiently and reliably. You'll blend traditional techniques with modern innovations, solving complex engineering challenges to bring artistic visions to life, making this a niche yet vital career in the ceramics world.
Key Facts & Statistics
Median Salary
Range: Due to the highly specialized and often freelance nature of this role, salary can vary widely from project-based fees ($5,000 - $50,000+ USD per custom kiln) to hourly rates. Experienced builders with a strong reputation could earn $60k - $150k+ USD annually, depending on project volume and complexity, often operating as independent contractors.
Growth Outlook
Annual Openings
Top Industries
Typical Education
No formal degree is typically required; expertise is gained through extensive apprenticeships, hands-on experience, and self-study in thermodynamics, refractory materials, and kiln design. Engineering or ceramics backgrounds can be advantageous.
What is a Pottery Kiln Builder?
A pottery kiln builder is a highly specialized craftsperson and engineer who designs, constructs, and repairs high-temperature kilns used for firing ceramic and pottery wares. These professionals possess a deep understanding of thermodynamics, material science, and structural engineering to create efficient, safe, and durable firing environments. They transform raw materials into complex heating chambers capable of reaching thousands of degrees Fahrenheit.
Unlike a general contractor or a ceramic artist, a kiln builder focuses exclusively on the intricate structure and functionality of the kiln itself, rather than the building it resides in or the art it produces. They are the architects and masons of the ceramic world's most critical tool, ensuring the precise control of heat necessary for transforming clay into durable ceramic. Their expertise ensures kilns are not only functional but also energy-efficient and compliant with safety regulations.
What does a Pottery Kiln Builder do?
Key Responsibilities
- Design and engineer kiln structures, calculating thermal requirements, material stress points, and fuel efficiency based on client specifications.
- Cut, shape, and lay refractory bricks and insulating materials, ensuring precise alignment and tight joints to prevent heat loss.
- Install and connect heating elements, burners, and exhaust systems, adhering strictly to safety codes and operational standards.
- Construct and reinforce the outer shell of kilns using steel, concrete, or other robust materials, providing structural integrity.
- Test newly built kilns for proper temperature distribution, ventilation, and safety features before handover to clients.
- Perform maintenance, repair, and upgrades on existing kilns, diagnosing issues and replacing worn components.
- Source and manage inventory of specialized refractory materials, insulation, and heating components required for kiln construction and repair projects.
Work Environment
Pottery kiln builders typically work in a variety of environments, ranging from dedicated workshops to client sites, which can include pottery studios, educational institutions, or industrial facilities. The work often involves physical labor, including lifting heavy refractory bricks and working in dusty or confined spaces. Collaboration is common, often involving small teams of skilled technicians or apprentices, and close communication with clients regarding design and progress.
The work schedule can be variable, with project-based timelines dictating hours. While some projects are steady, others may require intensive periods to meet deadlines. Travel to different locations for on-site builds, repairs, and consultations is a regular part of the job, making remote work largely impractical for the hands-on construction aspects.
Tools & Technologies
Pottery kiln builders use a specialized array of tools and technologies. They frequently work with refractory bricks, ceramic fiber insulation, and various high-temperature mortars and cements. Essential hand tools include brick tongs, trowels, levels, and measuring tapes for precise material placement. For cutting and shaping, they utilize refractory saws, angle grinders with diamond blades, and brick splitters.
Technical equipment involves welding gear for structural steel frames, specialized burners (gas, electric, wood-fired), and pyrometers or thermocouples for temperature measurement and calibration. They also work with ventilation systems, flues, and sometimes programmable temperature controllers for automated firing cycles. Understanding material science principles, heat transfer, and combustion dynamics is crucial for effective kiln design and construction.
Pottery Kiln Builder Skills & Qualifications
Building pottery kilns requires a unique blend of engineering principles, material science knowledge, and practical construction skills. Qualifications are highly dependent on the type of kilns being built and the target market. For instance, constructing large industrial kilns demands different expertise than building smaller, artisanal kilns for individual potters or educational institutions.
Formal education is less critical than demonstrated practical experience and a strong portfolio for a Pottery Kiln Builder. Many successful builders learn through apprenticeships or hands-on experience, often starting as assistants to experienced professionals. Certifications in welding, masonry, or specific refractory materials can add significant value, proving a baseline level of competency. The industry values proven ability to design, construct, and troubleshoot kilns that operate safely and efficiently.
The skill landscape for kiln builders is evolving with advancements in materials science and energy efficiency. Builders increasingly need to understand insulation technologies, precise temperature control systems, and sustainable building practices. While traditional brick-and-mortar skills remain vital, knowledge of specialized refractory cements, ceramic fiber insulation, and digital control systems is becoming essential. This role requires a balance of broad construction knowledge and deep specialization in thermal dynamics and high-temperature materials.
Education Requirements
Technical Skills
- Refractory material selection and application (bricks, castables, ceramic fiber)
- High-temperature insulation techniques and best practices
- Welding and metal fabrication (for frames, flues, and structural components)
- Masonry and bricklaying for high-temperature environments
- Combustion system design and installation (gas burners, electric elements, wood-firing)
- Ventilation and exhaust system design for safe kiln operation
- Electrical wiring and control panel installation for electric kilns
- Temperature control system (pyrometers, thermocouples, digital controllers) integration
- Blueprint reading and technical drawing interpretation
- Structural engineering principles for load-bearing and thermal expansion
- Tool maintenance and operation (cut-off saws, grinders, mixers)
Soft Skills
- Problem-solving and troubleshooting: Kiln building often involves unexpected challenges requiring creative solutions to material and design issues.
- Attention to detail: Precise measurements and meticulous execution are crucial for kiln safety and optimal firing performance.
- Patience and persistence: Kiln construction is a labor-intensive process that demands sustained effort and careful work over extended periods.
- Safety consciousness: Working with high temperatures, heavy materials, and specialized tools requires a constant focus on safety protocols and risk mitigation.
- Client communication: Understanding client needs, explaining design choices, and setting realistic expectations are vital for custom kiln projects.
- Adaptability: Designs and material choices may need to change based on site conditions or client feedback, requiring flexibility and quick adjustments.
- Time management: Efficiently planning construction phases and managing material delivery ensures projects stay on schedule.
- Resourcefulness: Finding and utilizing specialized materials and tools, often on a project-by-project basis, is critical for success in this niche field.
How to Become a Pottery Kiln Builder
Becoming a Pottery Kiln Builder involves a blend of specialized technical skills, practical experience, and an understanding of material science. Unlike many traditional careers, there isn't a single standardized educational path like a university degree. Instead, entry often combines vocational training, apprenticeships, and extensive self-directed learning.
Realistic timelines vary significantly. A complete beginner might spend 2-3 years acquiring foundational skills and seeking initial apprenticeship opportunities. Someone with a background in construction, welding, or refractory materials could potentially transition in 1-2 years by focusing on kiln-specific knowledge. Geographic location plays a crucial role; opportunities are more concentrated in areas with active pottery communities, ceramic manufacturing, or specialized kiln repair services, such as regions known for ceramics production or art schools.
Misconceptions include believing that only formal engineering degrees are necessary, or that one can quickly master the craft. The field values hands-on proficiency, problem-solving abilities, and a deep respect for safety protocols. Networking within the ceramics community, attending workshops, and connecting with experienced builders are essential. Many builders start by assisting on smaller projects or focusing on maintenance before undertaking full constructions.
Step 1
Step 2
Step 3
Step 4
Step 5
Step 6
Step 7
Education & Training Needed to Become a Pottery Kiln Builder
Becoming a Pottery Kiln Builder involves a unique blend of craftsmanship, engineering principles, and material science. Unlike many modern professions, formal university degrees are less common or directly relevant. Instead, the educational ecosystem centers around hands-on apprenticeships, specialized workshops, and self-directed study of refractory materials and thermal dynamics. This field highly values practical experience over theoretical academic credentials.
Apprenticeships with experienced kiln builders are the most effective and recognized pathway. These can range from 1 to 5 years, depending on the complexity of skills acquired, often involving minimal or no direct cost beyond living expenses, and sometimes even offering a stipend. Specialized workshops, offered by craft centers or individual builders, provide concentrated learning on specific kiln types (e.g., wood-fired, anagama, gas kilns) and typically cost $500-$3,000 for a few days to a few weeks. Self-study, through books on kiln design and refractory materials, complements practical learning, costing $50-$500 for resources. Employers and clients in this niche field prioritize a portfolio of built kilns and direct references from experienced builders over formal certifications.
Continuous learning in this field involves staying updated on new refractory materials, insulation techniques, and safety standards. This often happens through participation in pottery conferences, online forums, and direct communication with material suppliers. The cost-benefit analysis heavily favors practical, experiential learning. While a four-year engineering degree might provide theoretical knowledge, its cost ($40,000-$100,000+) and time commitment do not directly translate to the specific, hands-on skills required for kiln building, making it a less efficient investment compared to direct mentorship. Industry-specific accreditation is virtually non-existent; reputation and a proven track record are paramount.
Pottery Kiln Builder Salary & Outlook
Compensation for a Pottery Kiln Builder varies significantly based on specialized skills, project complexity, and geographic demand. Expertise in specific kiln types, such as wood-fired, gas, or electric, often commands higher rates. Builders with a reputation for efficiency, durability, and traditional craftsmanship also secure premium pay.
Geographic location profoundly impacts earnings. Urban centers or regions with a strong arts and crafts community, like parts of California, the Pacific Northwest, or the Northeast, tend to offer higher compensation due to increased demand and a higher cost of living. Rural areas, while potentially having a niche market, may offer lower rates. International markets also show variations, with European and Asian countries having different compensation structures compared to the USD figures presented.
Total compensation extends beyond base project fees. Many builders operate as independent contractors, allowing them to set their own rates and manage their business expenses. Performance-based bonuses are rare, but successful project completion often leads to valuable referrals and repeat business. Benefits packages are typically self-funded, requiring careful financial planning.
Years of experience directly correlate with earning potential. Apprentices gain foundational knowledge, while Master Kiln Builders or Kiln Construction Specialists command top rates due to their extensive experience and ability to undertake large, complex, or historically accurate projects. Negotiation leverage comes from a strong portfolio, client testimonials, and unique design or construction methods. Remote work is not applicable for this hands-on role, but travel for projects is common and often includes per diem or travel expense reimbursement.
Salary by Experience Level
Level | US Median | US Average |
---|---|---|
Apprentice Pottery Kiln Builder | $30k USD | $35k USD |
Pottery Kiln Builder | $50k USD | $55k USD |
Senior Pottery Kiln Builder | $70k USD | $75k USD |
Master Kiln Builder | $90k USD | $95k USD |
Kiln Construction Specialist | $105k USD | $110k USD |
Market Commentary
The job market for Pottery Kiln Builders is highly specialized and niche, driven primarily by individual artists, educational institutions, community art centers, and small-scale ceramics manufacturers. Demand remains steady but is not experiencing rapid growth, as new kiln construction is a significant investment for clients. The market is less susceptible to broad economic cycles than other construction trades, but relies on the sustained interest in ceramic arts and pottery.
Current trends show a renewed interest in traditional pottery methods, which can create opportunities for builders specializing in specific historical kiln designs or environmentally sustainable options like wood-fired kilns. There is also a small but growing demand for custom-built, energy-efficient electric kilns that meet modern safety and environmental standards. The supply of highly skilled, experienced kiln builders is relatively low, creating a favorable dynamic for those with proven expertise.
Future-proofing in this profession involves continuous learning about new materials, insulation technologies, and firing processes. Automation and AI have minimal direct impact on the hands-on construction of kilns, but digital tools might assist in design or material sourcing. The role remains highly craft-based and requires significant manual skill and problem-solving abilities on-site.
Geographic hotspots for this role align with areas rich in ceramic arts programs, workshops, and artist communities. While not a high-growth sector, the specialized nature and relatively low supply of master builders ensure stable opportunities for those with the requisite skills. The profession is generally recession-resistant as it serves a dedicated community, though large, new projects may slow during economic downturns.
Pottery Kiln Builder Career Path
Career progression for a Pottery Kiln Builder involves a hands-on journey from assisting to designing and leading complex projects. Advancement typically follows a clear path of increasing skill, specialized knowledge, and project leadership. This field emphasizes practical experience and the mastery of diverse construction techniques and materials.
Individual contributor (IC) tracks are common, focusing on deep technical expertise in kiln construction, repair, and optimization. While management roles are less defined in this niche, a Master Kiln Builder or Kiln Construction Specialist often takes on mentorship and project oversight, functioning as a technical leader. Performance, the complexity of kilns built, and a reputation for durability and efficiency significantly influence advancement speed.
Specialization can involve focusing on specific kiln types like wood-fired, gas, or electric, or materials such as brick, refractory concrete, or insulation. Networking within the ceramics and pottery community, sharing knowledge, and demonstrating successful kiln builds are crucial for career growth. Certifications are less formal, often replaced by a portfolio of successful projects and peer recognition. Lateral moves might involve transitioning into refractory material sales or consulting for pottery studios on kiln maintenance or design.
Apprentice Pottery Kiln Builder
1-2 yearsKey Focus Areas
Pottery Kiln Builder
3-5 years total experienceKey Focus Areas
Senior Pottery Kiln Builder
6-10 years total experienceKey Focus Areas
Master Kiln Builder
10-15 years total experienceKey Focus Areas
Kiln Construction Specialist
15+ years total experienceKey Focus Areas
Apprentice Pottery Kiln Builder
1-2 yearsAssists experienced builders with material preparation, site setup, and basic construction tasks. Works under direct supervision, focusing on learning proper techniques and safety procedures. Responsibilities include moving materials, mixing mortar, and laying simple brick patterns. Has minimal decision-making authority.
Key Focus Areas
Develop foundational skills in bricklaying, mortar mixing, and safely handling refractory materials. Learn about different types of insulation and their applications. Focus on understanding blueprints and following detailed instructions. Begin to grasp safety protocols for construction sites.
Pottery Kiln Builder
3-5 years total experienceIndependently executes specific sections of a kiln build, such as firebox construction or chimney assembly, with general supervision. Takes responsibility for the quality and accuracy of assigned tasks. Participates in site assessments and material estimation. Makes basic on-site adjustments under guidance.
Key Focus Areas
Master precise brick cutting and laying, refractory material application, and flue system construction. Gain proficiency in interpreting complex kiln designs and troubleshooting minor construction issues. Develop a deeper understanding of thermal dynamics and material properties related to heat retention and transfer.
Senior Pottery Kiln Builder
6-10 years total experienceLeads significant portions of a kiln construction project or manages smaller, complete builds from start to finish. Oversees junior builders, ensuring adherence to design specifications and quality standards. Acts as a primary point of contact for clients on site. Makes critical construction decisions and resolves complex technical challenges.
Key Focus Areas
Acquire advanced knowledge of various firing methods (wood, gas, electric) and their impact on kiln design. Develop skills in structural integrity analysis and thermal mapping. Begin to mentor junior builders and lead small teams. Focus on client communication and project planning.
Master Kiln Builder
10-15 years total experienceTakes full ownership of large-scale, complex, or custom kiln projects, from initial client consultation and design to final commissioning. Provides expert consultation on kiln selection, site preparation, and operational efficiency. Mentors senior builders and contributes to industry best practices. Holds ultimate responsibility for project success.
Key Focus Areas
Cultivate expertise in custom kiln design, advanced refractory engineering, and energy efficiency optimization. Develop strong problem-solving skills for unique firing requirements and site constraints. Focus on business development, client relationship management, and industry reputation building through successful, innovative projects.
Kiln Construction Specialist
15+ years total experienceServes as a top-tier expert and consultant for highly specialized or challenging kiln construction projects globally. Engages in strategic planning for large institutions or commercial potteries. May lead R&D initiatives for new kiln technologies or materials. Provides high-level problem-solving and innovative solutions for unique firing needs. Often works independently or leads highly specialized teams.
Key Focus Areas
Specialize in niche areas like historical kiln replication, advanced automation integration, or international consulting. Focus on research and development of new materials or construction techniques. Develop thought leadership through publications, workshops, or industry presentations. Cultivate a global network of clients and collaborators.
Job Application Toolkit
Ace your application with our purpose-built resources:
Pottery Kiln Builder Resume Examples
Proven layouts and keywords hiring managers scan for.
View examplesPottery Kiln Builder Cover Letter Examples
Personalizable templates that showcase your impact.
View examplesTop Pottery Kiln Builder Interview Questions
Practice with the questions asked most often.
View examplesPottery Kiln Builder Job Description Template
Ready-to-use JD for recruiters and hiring teams.
View examplesGlobal Pottery Kiln Builder Opportunities
Pottery Kiln Builders are specialized artisans and engineers, designing and constructing kilns for ceramic production globally. This niche profession sees demand in regions with strong pottery traditions or emerging craft industries.
International opportunities often arise from studio expansions, educational institutions, or cultural heritage projects requiring specific kiln types. Regulatory differences, especially safety and environmental standards, significantly impact design and construction methods across countries. Professionals consider international work for unique projects, skill exchange, and market expansion.
Global Salaries
Salaries for Pottery Kiln Builders vary significantly by region, experience, and project complexity. In North America, experienced builders might earn between USD 60,000 and USD 100,000 annually, or USD 300-600 per day for project-based work, depending on the kiln size and type. Europe shows similar ranges, with Western European countries like Germany or the UK offering EUR 50,000-85,000 (approx. USD 55,000-95,000) for employed specialists. Project rates can be higher.
Asia-Pacific markets, particularly Japan and South Korea, which have deep ceramic traditions, may offer JPY 5,000,000-8,000,000 (approx. USD 35,000-55,000) for skilled builders, though local costs of living are lower. Latin America, such as Mexico or Brazil, might offer USD 25,000-45,000, with local currency equivalents reflecting lower purchasing power but also lower living expenses. These figures often exclude project-specific bonuses or material costs.
Salary structures also differ; North American and European contracts often include health benefits and retirement plans, while project-based work globally may require builders to manage their own insurance. Tax implications vary widely; some countries have higher income taxes but offer more social services. Experience in specific kiln types, like wood-fired or anagama kilns, can command higher rates due to specialized knowledge and demand.
Remote Work
Direct remote work for Pottery Kiln Builders is limited, as the core work involves physical construction. However, significant aspects can be handled remotely. Design, material sourcing, structural calculations, and project management are often conducted from a distance using CAD software and communication tools.
This allows builders to consult internationally or manage projects from their home base, traveling only for critical construction phases. Legal and tax implications for international remote consultation require careful planning. Time zone differences are manageable for design and planning but can impact real-time collaboration during construction.
Digital nomad opportunities exist for the design and consultation phases, with countries like Portugal or Estonia offering specific visas for remote workers. Employers typically cover travel and accommodation during on-site phases. Impact on salary expectations is minimal if the builder charges for their time and expertise, regardless of location for design work. Specialized platforms for architectural or industrial design may feature such roles.
Visa & Immigration
Pottery Kiln Builders pursuing international work typically need skilled worker visas. Countries like Canada, Australia, and Germany often have pathways for tradespeople or specialized technicians. Requirements include demonstrating expertise, often through portfolios of past projects and professional references. Some nations may require skills assessments or trade certifications.
Credential recognition is crucial; some countries may require equivalence assessments for technical education. The visa application process usually involves employer sponsorship, a detailed job offer, and proof of financial stability. Processing times vary from a few weeks to several months. Language proficiency, especially in the destination country's official language, can be a requirement, particularly for client interaction and safety protocols.
For short-term projects, business visas or temporary work permits may suffice. Pathways to permanent residency often exist after several years of skilled employment. Family visas for dependents are usually available alongside the primary applicant's work visa. Specific advantages for this niche profession are rare, but unique skills can strengthen visa applications.
2025 Market Reality for Pottery Kiln Builders
Understanding the current market realities for a Pottery Kiln Builder is crucial for strategic career planning. This niche profession operates outside typical job market dynamics, heavily influenced by specialized demand and artistic community growth. The market has evolved significantly in recent years, moving from a steady, artisan-driven trade to one increasingly shaped by material science advancements and economic shifts impacting discretionary spending on art infrastructure.
The post-pandemic period saw a small boom in home studio setups, but the broader economic climate in 2024-2025 has introduced more caution, affecting large-scale investments. Broader economic factors, such as inflation and interest rates, directly influence the willingness of individuals and institutions to commission new kiln builds. Market realities vary widely by experience level, with seasoned builders commanding premium rates, and by geographic region, concentrating in areas with strong arts scenes. This analysis provides an honest assessment of current hiring conditions.
Current Challenges
Finding consistent, full-time employment remains a significant challenge. Most work comes through project-based contracts, requiring constant networking and self-promotion. Competition for specialized projects is intense, especially for those with limited portfolios.
Economic fluctuations directly impact discretionary spending on custom kilns or studio upgrades. This creates unpredictable demand. The niche nature of the skill also means fewer available positions compared to broader construction trades.
Growth Opportunities
Despite challenges, strong opportunities exist for specialized Pottery Kiln Builders. Demand remains consistent for custom, high-efficiency kilns that meet specific artistic or production needs. Builders who can design and construct advanced wood-fired or soda kilns, known for their unique firing characteristics, find a dedicated client base.
Emerging opportunities lie in retrofitting older kilns with modern insulation and control systems to improve energy efficiency. This appeals to environmentally conscious clients and those seeking to reduce operational costs. Professionals who understand smart home integration or remote monitoring for kilns also gain a competitive edge.
Underserved markets include smaller community art centers or educational institutions looking to upgrade outdated equipment on a budget. Building a strong portfolio showcasing diverse kiln types and emphasizing energy efficiency can position a builder advantageously. Networking within ceramics guilds and art communities is paramount for securing commissions.
Market corrections might lead institutions to invest in long-term infrastructure improvements like kilns, rather than short-term projects. Regions with growing populations and a burgeoning interest in craft arts often present better opportunities. Investing in continuous learning about new refractory materials and digital design tools can provide a significant competitive advantage in this highly specialized field.
Current Market Trends
Demand for skilled pottery kiln builders remains highly specialized and project-based as of 2025. It is not a high-volume hiring market; instead, it relies on individual commissions for custom studio installations, educational institutions, and art centers. The post-pandemic surge in home-based hobbies initially boosted interest in personal studios, but this has somewhat stabilized.
Industry changes largely involve material advancements and energy efficiency. Builders incorporating modern refractory materials and smart temperature controls find more work. AI integration has minimal direct impact on the physical construction of kilns, but AI-powered design tools might influence custom kiln aesthetics or efficiency calculations in the long term.
Economic conditions influence this market significantly. When disposable income tightens, large investments in pottery equipment or new studio builds slow down. This creates a cyclical demand pattern. Layoffs in broader economic sectors mean fewer individuals pursuing new artistic ventures requiring custom kilns.
Employer requirements often prioritize a proven portfolio of diverse kiln types—electric, gas, wood-fired, soda, or raku. Knowledge of local building codes and ventilation systems is critical. Salary trends are highly variable, based on project complexity and the builder's reputation, rather than standardized rates. Market saturation is low for highly skilled, experienced builders, but new entrants face a steep learning curve and need to build a reputation.
Geographically, demand is strongest in areas with established arts communities, universities with ceramics programs, or regions with a high concentration of professional potters. Remote work is not applicable to the physical construction, but consultation and design work can be done remotely. There are no significant seasonal hiring patterns, as projects arise throughout the year based on client needs.
Emerging Specializations
The field of pottery kiln building, while rooted in ancient traditions, is experiencing significant evolution driven by advancements in material science, energy efficiency, and digital fabrication. Understanding these shifts creates new specialization opportunities for professionals. Early positioning in these emerging areas is crucial for career advancement, especially when looking towards 2025 and beyond.
Specializing in cutting-edge kiln technologies often commands premium compensation and offers substantial career growth. These niche areas are less saturated than established kiln building practices, providing a competitive advantage. While balancing the pursuit of emerging areas with established specializations is wise, focusing on future-oriented skills can unlock next-generation opportunities.
Emerging areas typically take time to transition from novel concepts to mainstream practices, creating significant job opportunities. For kiln builders, this timeline is accelerating due to urgent demands for sustainable and precise firing solutions. Investing in these new skills involves a thoughtful risk-reward assessment; however, the potential for innovation and market leadership in a transforming industry is considerable.
Sustainable Kiln Engineering
This specialization focuses on designing and constructing kilns that minimize energy consumption and environmental impact. It involves integrating advanced insulation materials, heat recovery systems, and alternative fuel sources like biomass or hydrogen. As global regulations tighten and sustainability becomes a core industry value, demand for eco-friendly firing solutions will increase significantly, moving beyond traditional gas or electric designs.
Automated & Smart Kiln Systems
This area involves the integration of sensors, microcontrollers, and software to create kilns that offer precise temperature control, automated firing schedules, and remote monitoring capabilities. These smart kilns can optimize firing curves, reduce human error, and provide data analytics for consistent results. This specialization moves the craft of kiln building into the realm of industrial automation and IoT.
Advanced Material Kiln Design
Specializing in the construction of kilns designed for very specific, high-performance ceramic materials, such as advanced technical ceramics or high-temperature composites, is a growing niche. These materials often require extremely precise firing environments, unique atmospheres, or rapid thermal cycling. This includes kilns for industrial applications beyond traditional pottery, requiring specialized material handling and atmospheric control.
Modular & Portable Kiln Construction
This specialization focuses on designing and building kilns that can be easily transported, assembled, and disassembled for workshops, educational programs, or remote firing locations. This often involves modular construction techniques, lightweight but durable materials, and efficient heating systems suitable for varied environments. The demand for flexible and accessible firing solutions is expanding beyond fixed studio setups.
Robotic & Additive Kiln Fabrication
This area explores the application of additive manufacturing (3D printing) and robotic fabrication techniques in creating kiln components or even entire kiln structures. It allows for highly complex geometries, optimized heat flow paths, and customized designs that are difficult to achieve with traditional construction methods. This pushes the boundaries of kiln design and manufacturing efficiency.
Pros & Cons of Being a Pottery Kiln Builder
Making an informed career decision requires understanding both the positive and challenging aspects of a profession. The experience of a Pottery Kiln Builder can vary significantly depending on the client's needs, the type of kiln being constructed, and the specific materials involved. What one builder finds rewarding, another might find challenging, reflecting personal preferences and work styles. For instance, the physical demands might be a pro for someone who enjoys manual labor, but a con for others. Pros and cons can also shift as a builder gains more experience and takes on larger, more complex projects. This assessment offers an honest look at the realities of building pottery kilns, helping individuals set realistic expectations for this specialized trade.
Pros
- Pottery kiln builders gain deep satisfaction from creating essential tools for artists, directly enabling their creative work and contributing to the ceramics community.
- This niche skill is highly specialized, leading to strong demand for experienced builders as few individuals possess the expertise required for custom kiln construction.
- There is significant intellectual stimulation involved in designing and engineering kilns to meet specific firing needs, balancing thermal efficiency with structural integrity.
- The work offers substantial autonomy, as builders often manage projects from initial consultation to final completion, making key decisions throughout the process.
- Each kiln build presents unique challenges and opportunities, ensuring that the work rarely becomes monotonous and continuously tests problem-solving abilities.
- This profession allows for a tangible sense of accomplishment, as builders can see and test the functional, durable structures they have created, often for years to come.
- Networking within the ceramics and art communities is a natural part of the job, opening doors to new projects, collaborations, and a supportive professional environment.
Cons
- Building a pottery kiln involves significant physical labor, including lifting heavy bricks and materials, which can lead to back strain or other injuries over time.
- The work environment can be hot, dusty, and noisy, particularly when cutting bricks or operating machinery, requiring constant use of personal protective equipment.
- Projects often have tight deadlines, especially when a studio or artist needs a kiln operational quickly, leading to periods of intense, prolonged work.
- Specialized knowledge of refractory materials, thermodynamics, and structural engineering is crucial, requiring continuous learning as new materials and techniques emerge.
- Finding consistent work can be challenging as demand for custom kiln builds is project-based rather than continuous, leading to potential income fluctuations.
- Mistakes in construction can be costly, as faulty insulation or structural weaknesses can lead to inefficient firing, kiln failure, or safety hazards, requiring meticulous attention to detail.
- Travel is frequently required to client sites, which can be in remote locations, impacting personal time and increasing logistical complexities for each build.
Frequently Asked Questions
Pottery Kiln Builders face distinct challenges around specialized construction techniques, material sourcing, and safety regulations. This section addresses the most common questions about entering this niche trade, from mastering refractory materials to understanding the demand for custom kilns.
How long does it take to become a skilled Pottery Kiln Builder if I'm starting from scratch?
Becoming a proficient Pottery Kiln Builder typically takes 2-5 years of dedicated learning and hands-on experience. This includes mastering various construction methods, understanding refractory materials, and gaining expertise in electrical or gas systems. Many start by assisting experienced builders, attending specialized workshops, or working in related trades like masonry before focusing on kilns.
Do I need a specific degree or certification to become a Pottery Kiln Builder?
Formal education is not strictly required, but practical skills are essential. Many successful builders learn through apprenticeships with established kiln builders, vocational training in masonry or ceramics, or extensive self-study and hands-on projects. Demonstrating a strong understanding of thermodynamics, material science, and safety protocols is more important than a degree.
What are the typical salary expectations or project earnings for a Pottery Kiln Builder?
Entry-level builders assisting established professionals might earn hourly wages comparable to skilled trades, while experienced, independent builders can command higher fees for custom projects. Income varies significantly based on project complexity, regional demand, and reputation. Custom kiln builds can range from a few thousand to tens of thousands of dollars, depending on size and features.
What is the typical work-life balance and lifestyle for a Pottery Kiln Builder?
The work-life balance can be variable. Project-based work might involve intense periods of construction, followed by slower periods for material sourcing or client acquisition. Travel is often required for on-site builds. While physical demands are significant, the satisfaction of creating a functional, specialized piece of equipment can be very rewarding.
Is there a stable job market for Pottery Kiln Builders, or is it a very niche field?
The demand for custom-built kilns remains steady within the ceramics community, especially for potters and artists seeking specific firing capabilities. While it's a niche market, skilled builders are always in demand. Job security often comes from a strong reputation, word-of-mouth referrals, and the ability to adapt to new technologies or materials in kiln design.
What are the career growth and advancement opportunities for a Pottery Kiln Builder?
Career growth involves specializing in advanced kiln types, such as wood-fired or salt kilns, or moving into design and consultation. You can also expand into kiln repair, maintenance, and refractory material sales. Building a strong portfolio of diverse projects and developing a unique building style can open doors to higher-paying custom work.
What are the biggest challenges or common pitfalls for a Pottery Kiln Builder?
The primary challenges include sourcing specialized refractory materials, ensuring precise temperature control and structural integrity, and adhering to strict safety codes for gas and electrical systems. Each custom build presents unique design challenges, requiring strong problem-solving skills and meticulous attention to detail to prevent failures and ensure longevity.
Related Careers
Explore similar roles that might align with your interests and skills:
Ceramic Painter
A growing field with similar skill requirements and career progression opportunities.
Explore career guideFirebrick Layer
A growing field with similar skill requirements and career progression opportunities.
Explore career guideFurnace Mason
A growing field with similar skill requirements and career progression opportunities.
Explore career guideRefractory Bricklayer
A growing field with similar skill requirements and career progression opportunities.
Explore career guideRefractory Tile Helper
A growing field with similar skill requirements and career progression opportunities.
Explore career guideAssess your Pottery Kiln Builder readiness
Understanding where you stand today is the first step toward your career goals. Our Career Coach helps identify skill gaps and create personalized plans.
Skills Gap Analysis
Get a detailed assessment of your current skills versus Pottery Kiln Builder requirements. Our AI Career Coach identifies specific areas for improvement with personalized recommendations.
See your skills gapCareer Readiness Assessment
Evaluate your overall readiness for Pottery Kiln Builder roles with our AI Career Coach. Receive personalized recommendations for education, projects, and experience to boost your competitiveness.
Assess your readinessSimple pricing, powerful features
Upgrade to Himalayas Plus and turbocharge your job search.
Himalayas
Himalayas Plus
Himalayas Max
Find your dream job
Sign up now and join over 100,000 remote workers who receive personalized job alerts, curated job matches, and more for free!
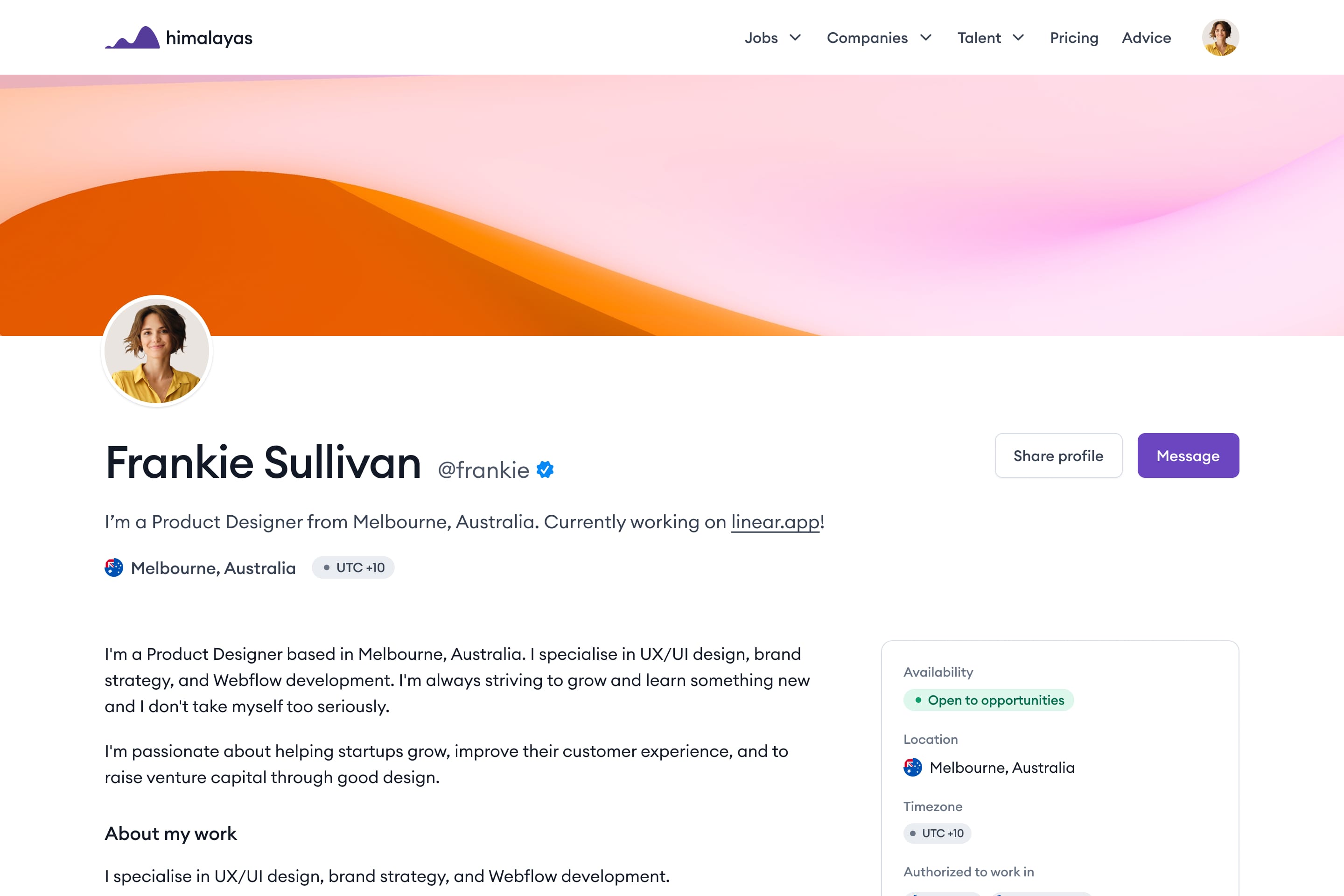