Complete Log Sorter Career Guide
Log sorters play a crucial role at the initial stages of timber processing, ensuring raw logs are accurately categorized by species, size, and quality. Your keen eye and quick decision-making directly impact efficiency and profitability in the forestry and logging industries. This essential work provides a stable entry point into the natural resources sector, with opportunities for growth into equipment operation or supervisory roles.
Key Facts & Statistics
Median Salary
$44,050 USD
(U.S. Bureau of Labor Statistics, May 2023)
Range: $35k - $55k+ USD
Growth Outlook
Annual Openings
Top Industries
Typical Education
High school diploma or equivalent; on-the-job training is common.
What is a Log Sorter?
A log sorter is a specialized professional in the timber industry responsible for evaluating and categorizing raw timber as it arrives at a sawmill, pulp mill, or logging yard. Their primary purpose is to ensure that logs are directed to their most appropriate processing destination based on their species, size, and quality, maximizing the value extracted from each tree. This role is crucial for optimizing mill operations, reducing waste, and ensuring the right raw materials are available for specific products like lumber, plywood, or paper.
This position differs significantly from a general laborer in a timber yard, who might perform general cleanup or assist with manual tasks. A log sorter possesses specific knowledge of timber characteristics and quality grading, and often operates complex heavy machinery. They are distinct from a lumber grader, who evaluates finished wood products, as the log sorter focuses on the raw, unprocessed logs at the initial stages of the timber supply chain, making critical decisions about how each log will be utilized.
What does a Log Sorter do?
Key Responsibilities
- Visually inspect incoming logs for species, diameter, length, and quality defects such as rot or excessive knots.
- Operate heavy machinery, such as forklifts or log loaders, to move and position logs onto designated sorting lines or storage areas.
- Identify and mark logs according to their end-use, separating sawlogs from pulpwood or veneer logs to optimize processing.
- Monitor automated sorting equipment and machinery, troubleshooting minor issues to ensure continuous operation.
- Record log inventory data, including volume and grade, using handheld devices or computer systems.
- Maintain a clean and safe work area around sorting equipment and log piles, adhering to all safety protocols.
- Collaborate with mill operators and inventory managers to ensure a steady supply of logs for processing and to meet production targets.
Work Environment
Log sorters typically work outdoors in log yards or within large, open-sided mill facilities. The environment is often noisy due to heavy machinery and the movement of logs, and can be dusty or muddy depending on weather conditions. This role requires significant physical activity, including standing, climbing, and operating equipment for extended periods. Work schedules often involve shifts, including early mornings, evenings, or weekends, to match mill operating hours. Collaboration is key, as sorters work closely with equipment operators, mill supervisors, and inventory staff. The pace of work is steady and production-driven, requiring constant vigilance for safety and efficiency.
Tools & Technologies
Log sorters primarily operate heavy machinery such as log loaders, excavators with grapples, or specialized forklifts designed for timber handling. They use automated sorting systems that often include sensors, cameras, and computer-controlled gates to direct logs. Handheld devices or ruggedized tablets are common for data entry and inventory tracking. Essential safety equipment includes hard hats, safety glasses, hearing protection, and steel-toed boots. They also work with basic hand tools for minor adjustments or clearing jams, and communication radios for coordinating with other team members.
Log Sorter Skills & Qualifications
Qualifications for a Log Sorter primarily center on practical experience and specific certifications, rather than formal academic degrees. Employers prioritize hands-on familiarity with logging equipment and a strong understanding of timber characteristics. While entry-level positions might accept less experience, senior Log Sorters typically possess several years in the field.
Requirements vary significantly by company size and the type of timber being processed. Large industrial operations often demand more stringent safety certifications and proficiency with automated sorting systems. Smaller, localized operations might focus more on manual sorting techniques and general forestry knowledge. Geographic location also influences requirements due to regional timber types and local safety regulations.
Formal education, such as a college degree, is generally not a prerequisite. Vocational training programs, apprenticeships, and industry-specific certifications hold far greater value. The skill landscape for Log Sorters is evolving with increasing automation in larger mills, requiring some adaptivity to new technologies. However, the core skills of timber identification, quality assessment, and safe equipment operation remain paramount. Certifications in heavy equipment operation, first aid, and specific logging safety protocols are often essential and can significantly enhance employability.
Education Requirements
Technical Skills
- Log Grading and Species Identification: Accurately identifying different tree species and assessing log quality based on industry standards (e.g., defects, dimensions, rot).
- Heavy Equipment Operation: Proficiency in operating various logging machinery such as log loaders, forklifts, excavators with grapples, or sorting cranes.
- Chainsaw Operation and Maintenance: Safe and effective use of chainsaws for trimming, delimbing, or bucking logs, along with basic maintenance.
- Scaling and Measurement: Accurately measuring log length, diameter, and volume using scaling sticks, calipers, or automated systems.
- Safety Protocols and Procedures: Thorough understanding and strict adherence to logging industry safety regulations, including PPE use and lockout/tagout procedures.
- Basic Equipment Maintenance and Troubleshooting: Performing routine checks, minor repairs, and identifying common issues with sorting equipment.
- Log Handling and Stacking Techniques: Efficiently moving, sorting, and stacking logs to optimize space and prepare for transport or milling.
- Data Entry and Record Keeping (for automated systems): Inputting log data into computer systems for inventory tracking and quality control.
- Radio Communication: Using two-way radios for clear and concise communication with other crew members and equipment operators.
Soft Skills
- Attention to Detail: Log Sorters must accurately identify timber species, assess quality, and recognize defects to ensure proper sorting and maximize value.
- Safety Consciousness: This role involves working with heavy machinery and large logs; a constant awareness of safety protocols and surroundings is critical to prevent accidents.
- Physical Stamina and Endurance: The job often requires long hours, lifting, bending, and standing in various weather conditions, demanding good physical fitness.
- Problem-Solving: Log Sorters frequently encounter irregular logs, equipment malfunctions, or unexpected conditions, requiring quick and effective solutions.
- Teamwork and Collaboration: Sorters often work as part of a larger logging or mill crew, requiring effective communication and coordination with colleagues.
- Adaptability: Weather conditions, log types, and equipment can change, requiring the ability to adjust work methods and priorities quickly.
- Decision-Making: Quickly assessing log characteristics and making sorting decisions under time pressure is a core aspect of the job.
- Reliability: Dependability in attendance and consistent work ethic are crucial for maintaining operational flow in the logging process.
How to Become a Log Sorter
Entering the log sorter field primarily involves practical, on-the-job training rather than extensive formal education. Many individuals begin as general laborers in a sawmill or logging operation and then transition into sorting roles as they gain experience and familiarity with wood types and grading standards. While some vocational programs might touch upon timber handling, direct industry experience is paramount.
The timeline for becoming a proficient log sorter can vary. A complete beginner might spend 3-6 months in general labor before moving into a sorting apprentice role, with full proficiency taking up to a year or more. Career changers with experience in heavy machinery or outdoor labor might accelerate this timeline. Entry strategies are quite consistent across regions, though larger mills might have more structured training programs than smaller, independent operations.
A common misconception is that log sorting is simple manual labor; in reality, it requires keen observation, knowledge of wood defects, and quick decision-making under pressure. Building a network within local logging or sawmill companies is crucial, as many opportunities arise through word-of-mouth or direct contact. Hiring landscapes remain steady for skilled sorters, as timber processing is a continuous industry, but initial entry often relies on proving reliability and a strong work ethic.
Step 1
Step 2
Step 3
Step 4
Step 5
Step 6
Education & Training Needed to Become a Log Sorter
Becoming a Log Sorter primarily involves practical skills and on-the-job training, rather than formal degrees. While no university degree is typically required, vocational training and certifications in heavy equipment operation or forestry safety can significantly enhance employability. These programs often range from a few days to several weeks and cost between $500 and $3,000. Some community colleges offer short courses in logging operations or timber harvesting, which might take 3-6 months and cost $2,000-$5,000.
Employers highly value hands-on experience and a strong understanding of timber characteristics and grading standards. Many log sorters begin in entry-level positions within a sawmill or logging operation, learning directly from experienced professionals. This informal apprenticeship can last from six months to two years, depending on the complexity of the timber types and sorting equipment involved. Industry-specific certifications, such as those for operating forklifts, excavators, or specialized log-handling machinery, are often prerequisites or highly beneficial for this role.
Continuous learning in this field focuses on staying updated with new sorting technologies, safety protocols, and evolving timber market specifications. While formal education is minimal, practical experience and a commitment to safety and efficiency are paramount. The cost-benefit analysis heavily favors practical training and certifications over expensive, lengthy academic programs for this specific role.
Log Sorter Salary & Outlook
Compensation for a Log Sorter varies significantly based on several factors, extending beyond just base wages. Geographic location plays a crucial role; regions with dense forestry operations and high demand for timber often command higher salaries due to localized industry presence and cost of living. For instance, the Pacific Northwest in the United States typically offers more competitive rates than areas with less logging activity.
Experience and specialized skills also drive earning potential. Log Sorters with years of experience, particularly those proficient with advanced sorting equipment or capable of identifying various timber grades, can secure higher pay. Total compensation packages may include overtime pay, which is common in logging, and sometimes production bonuses linked to efficiency or volume. Benefits like health insurance, retirement contributions, and safety gear allowances are also standard components of the overall package.
Industry-specific trends, such as fluctuating timber prices or increased demand for sustainable forestry products, can influence salary growth. Negotiating leverage often comes from a proven track record of safety, efficiency, and reliability. While remote work is not applicable to this hands-on role, the demand for skilled Log Sorters remains tied to local and national construction and manufacturing sectors. International market variations also exist, but the figures provided here are specific to the USD context.
Salary by Experience Level
Level | US Median | US Average |
---|---|---|
Log Sorter | $36k USD | $38k USD |
Senior Log Sorter | $43k USD | $45k USD |
Lead Log Sorter | $50k USD | $52k USD |
Market Commentary
The job market for Log Sorters remains steady, driven by ongoing demand in the construction, pulp and paper, and manufacturing industries. The U.S. Bureau of Labor Statistics projects stable employment for logging workers, including Log Sorters, over the next decade, with growth largely tied to housing starts and wood product consumption. While not experiencing rapid expansion, the need for skilled individuals to process timber at sawmills and logging sites persists.
Technological advancements, such as automated sorting systems, are gradually being introduced in larger facilities. However, human Log Sorters remain essential for complex grading, quality control, and operating specialized machinery in diverse conditions. This role is generally recession-resistant, as demand for wood products, though cyclical, rarely ceases entirely. The primary challenge is the aging workforce; as experienced sorters retire, opportunities for new entrants increase.
Geographic hotspots for Log Sorters align with major timber-producing regions, including the Pacific Northwest, the Southeast, and parts of the Northeast. There is a consistent supply-demand balance, with employers often seeking reliable candidates willing to work outdoors and in varying weather conditions. Future-proofing this career involves continuous learning on new equipment and understanding sustainable forestry practices. The emphasis on safety protocols and efficient material flow will continue to shape the role.
Log Sorter Career Path
Career progression for a Log Sorter typically involves a clear path focused on increasing efficiency, safety, and operational leadership within timber yards or sawmills. Advancement hinges on demonstrated proficiency, adherence to safety protocols, and the ability to train and supervise others. While individual contributor (IC) tracks emphasize mastery of sorting techniques and equipment operation, leadership tracks involve managing teams and optimizing sorting processes.
Advancement speed depends on several factors, including an individual's performance, the size and operational demands of the mill, and the regional timber industry's health. Specialization might involve expertise in specific timber types or sorting machinery. Lateral movement could include transitioning into quality control, inventory management, or equipment maintenance roles within the same facility. Company size also impacts progression; larger operations may offer more defined leadership roles, while smaller ones might combine responsibilities.
Networking within the timber industry and continuous learning about new sorting technologies or timber grading standards enhance career prospects. Mentorship from experienced sorters is crucial for skill transfer and understanding nuanced operational challenges. Key career milestones include achieving certifications in equipment operation and demonstrating consistent, error-free sorting. Some sorters might pivot into logistics, supply chain management, or even forest operations, leveraging their foundational understanding of timber flow.
Log Sorter
0-2 yearsKey Focus Areas
Senior Log Sorter
2-5 yearsKey Focus Areas
Lead Log Sorter
5-8 years total experienceKey Focus Areas
Log Sorter
0-2 yearsOperate sorting machinery to separate logs based on species, size, quality, and intended use. Work under direct supervision, following instructions to ensure logs are directed to correct processing areas. Maintain a clean and organized work environment. Contribute to overall production targets by efficiently handling timber.
Key Focus Areas
Develop foundational knowledge of different log species, grades, and dimensions. Master safe operation of sorting equipment, including loaders or conveyors. Focus on precision in sorting, minimizing errors, and maintaining a steady workflow. Understand and strictly adhere to all safety regulations and standard operating procedures.
Senior Log Sorter
2-5 yearsIndependently sort logs, making critical decisions on categorization and routing with minimal oversight. Identify and resolve minor equipment malfunctions or sorting bottlenecks. Serve as a go-to resource for complex sorting challenges. Provide informal guidance and training to junior team members, ensuring adherence to quality and safety standards.
Key Focus Areas
Refine expertise in log grading, identifying subtle quality differences, and optimizing sorting speed without compromising accuracy. Begin cross-training on various types of sorting equipment and different log handling procedures. Develop problem-solving skills for minor operational issues and contribute to process improvements. Start mentoring new sorters on best practices.
Lead Log Sorter
5-8 years total experienceOversee a team of Log Sorters, assigning tasks, monitoring performance, and ensuring daily production targets are met. Troubleshoot complex sorting issues and coordinate with maintenance for equipment repairs. Implement and enforce safety protocols across the sorting area. Contribute to scheduling and resource allocation decisions for the sorting operation. Report directly to the yard or mill supervisor.
Key Focus Areas
Cultivate strong leadership and communication skills, effectively delegating tasks and providing constructive feedback. Develop a comprehensive understanding of mill production goals and how sorting impacts downstream processes. Focus on optimizing team performance, implementing new sorting technologies, and enhancing overall operational efficiency. Engage in safety audits and continuous improvement initiatives.
Job Application Toolkit
Ace your application with our purpose-built resources:
Global Log Sorter Opportunities
Log Sorters play a crucial role globally in timber processing and lumber production. This profession involves grading and categorizing logs based on species, size, and quality for various end uses. International demand for skilled Log Sorters remains steady, particularly in countries with significant forestry industries. Regulatory and environmental standards vary by region, influencing sorting criteria and operational practices. Log Sorters often seek international opportunities in regions with abundant natural resources and active timber markets. While no universal certifications exist, practical experience and understanding of international timber standards are highly valued.
Global Salaries
Log Sorter salaries vary significantly by region due to local economic conditions and industry scale. In North America, particularly Canada and the USA, annual salaries range from USD 35,000 to USD 55,000 (CAD 47,000 to CAD 75,000). These figures reflect a higher cost of living and advanced machinery often used in operations. Benefits packages typically include health insurance and retirement plans.
Europe offers diverse salary landscapes. In Scandinavia (e.g., Sweden, Finland), Log Sorters earn between EUR 30,000 and EUR 45,000 (USD 32,000 to USD 48,000) annually, with strong social security benefits and ample vacation time. Eastern European countries like Poland might see wages around EUR 18,000 to EUR 28,000 (USD 19,000 to USD 30,000), where the cost of living is lower, offering comparable purchasing power. Tax rates and social contributions also differ, impacting net pay.
In Asia-Pacific, Australia and New Zealand provide salaries from AUD 50,000 to AUD 70,000 (USD 33,000 to USD 46,000), reflecting a higher cost of living and robust forestry sectors. Latin American countries, such as Brazil or Chile, typically offer lower nominal salaries, ranging from USD 10,000 to USD 20,000, but these provide significant local purchasing power. Experience and specialized knowledge of timber species or grading systems can enhance compensation across all regions.
Remote Work
International remote work opportunities for Log Sorters are extremely limited. This role is inherently hands-on, requiring physical presence at timber yards, sawmills, or logging sites. The core tasks involve direct inspection, measurement, and physical handling of logs. Therefore, digital nomad lifestyles or fully remote arrangements are not feasible for this profession.
Some administrative or supervisory aspects of timber management might involve remote coordination, but actual log sorting cannot be done off-site. Companies in the forestry sector rarely offer international remote hiring for operational roles like Log Sorter. Salary expectations for Log Sorters are tied to the local labor market where the physical work occurs, without geographic arbitrage potential typically associated with remote digital roles. Equipment needs are specific to the physical work environment, including safety gear and specialized tools, not standard remote office setups.
Visa & Immigration
Log Sorters considering international work typically pursue skilled worker visas. Countries with large forestry industries, such as Canada, Australia, New Zealand, Sweden, and Finland, are common destinations. Specific requirements for this role often include a job offer from an employer, relevant experience, and sometimes vocational training or certifications recognized by the host country's industry standards. Education credential recognition is less critical than practical experience for this trade.
Visa application timelines vary, generally taking several months, and involve submitting detailed employment contracts and personal documentation. Some countries may require language proficiency tests, especially for permanent residency pathways. While not a fast-track profession, a consistent work history in this field can support long-term residency applications in many nations. Dependents usually qualify for accompanying visas. Understanding specific national labor market needs and any existing shortages in the forestry sector can improve immigration prospects for Log Sorters.
2025 Market Reality for Log Sorters
Understanding the current market realities for log sorters is crucial. The timber industry, while foundational, is undergoing significant transformation. Post-pandemic shifts, global supply chain adjustments, and technological advancements, particularly in automation, reshape daily operations.
Economic factors, like housing market fluctuations and interest rates, directly impact timber demand and, by extension, the need for log sorters. Market realities vary by region, influenced by local forestry regulations and the scale of processing facilities. Larger mills often lead in automation, affecting job availability more profoundly than smaller, specialized operations. This analysis provides an honest assessment to help log sorters navigate these evolving conditions.
Current Challenges
Log sorters face significant competition from automation. Sawmills invest heavily in optical scanners and robotic arms, reducing the need for manual sorting. Economic downturns decrease construction demand, directly impacting timber harvesting and processing volumes. This leads to fewer available positions and increased pressure on existing crews. Remaining roles often require higher efficiency and adaptability to new technologies.
Growth Opportunities
Opportunities for log sorters lie in adapting to the evolving technological landscape. Roles requiring oversight of automated sorting systems, basic maintenance of optical scanners, or quality control checks on machine outputs are emerging. These positions demand a blend of traditional log knowledge and technical skills.
Smaller, specialized mills or those focusing on niche wood products might retain more manual sorting roles where precision and specific grading knowledge are paramount. These operations often cannot justify the high capital investment in full automation. Geographically, remote logging regions or areas with less developed infrastructure may still have a higher demand for manual labor. Professionals who gain certifications in heavy equipment operation or basic industrial automation will find themselves more competitive. Upskilling in data entry for inventory systems or basic troubleshooting of sorting machinery creates a distinct advantage. While the overall trend favors automation, strategic skill development opens new pathways within the timber processing sector.
Current Market Trends
The demand for log sorters shows a steady decline as of 2025. Automation in sawmills and processing plants continues to replace manual labor. Optical scanners and AI-driven sorting systems handle log grading and categorization with greater speed and accuracy than human workers. This shift impacts job availability across North America and Europe, where large-scale timber operations prioritize efficiency gains.
Economic conditions significantly influence the timber industry. High interest rates in 2023-2024 cooled the housing market, directly reducing demand for lumber and related products. This led to reduced logging output and subsequent cuts in processing plant staff, including log sorters. Layoffs in the forestry sector have occurred, reflecting this market correction. While some recovery is anticipated, the underlying trend towards automation persists.
Employer requirements for log sorters increasingly favor individuals capable of operating and monitoring machinery, not just manual sorting. Basic computer literacy for data input or system oversight becomes an advantage. Salary trends for manual sorters remain stagnant or show slight decreases, while roles involving equipment operation might see modest increases. Market saturation is evident in traditional manual sorting roles, particularly in regions with established timber industries. Remote work is not applicable to this hands-on profession.
Emerging Specializations
The field of log sorting, traditionally reliant on manual labor and basic machinery, is undergoing a significant transformation. Advanced technologies like AI, robotics, and sophisticated sensor systems are creating entirely new specialization opportunities. Understanding these shifts and positioning oneself early in these emerging areas is crucial for career advancement in 2025 and beyond.
Early adoption of these next-generation skills often leads to premium compensation and accelerated career growth. Professionals who develop expertise in cutting-edge log sorting technologies will find themselves highly sought after. While established sorting methods remain important, focusing on emerging areas offers a strategic advantage, opening doors to leadership roles and innovative projects.
Many emerging areas, while still developing, are rapidly moving towards mainstream adoption, creating significant job opportunities within the next three to five years. Pursuing these specializations involves a balance of risk and reward; while initial investment in new skills may be higher, the potential for long-term career stability and higher earning potential is substantial. This strategic choice helps professionals future-proof their careers.
Automated Log Sorting System Operator
This specialization focuses on operating and managing autonomous sorting systems that utilize AI and machine learning to identify, grade, and direct logs with minimal human intervention. These systems can process logs faster and more accurately than traditional methods, adapting to varying wood types and quality standards. This role involves overseeing automated processes, troubleshooting system errors, and optimizing AI algorithms for peak performance and efficiency in complex logging operations.
Drone-Assisted Log Inventory Analyst
This area involves using drone technology equipped with advanced cameras and LiDAR sensors to conduct aerial surveys of log piles, assess volume, identify species, and detect defects before logs even reach the sorter. This improves inventory management, reduces waste, and enhances safety by minimizing human exposure to hazardous environments. Specialists analyze drone data to provide actionable insights for optimizing the sorting process and supply chain logistics.
Smart Sensor Integration Specialist
This specialization deals with integrating and managing sensor networks that provide real-time data on log characteristics such as density, moisture content, internal defects, and species identification. These sensors, often using near-infrared or X-ray technology, allow for highly precise sorting decisions, optimizing material utilization and product quality. The role requires interpreting complex sensor data and maintaining system accuracy.
Sustainable Resource Sorting Coordinator
This role focuses on developing and implementing sorting strategies that prioritize environmental sustainability and resource efficiency. This includes optimizing log utilization to minimize waste, identifying logs for bioenergy production, and ensuring compliance with sustainable forestry certifications. Professionals in this area work to reduce the ecological footprint of log processing, often involving circular economy principles.
Digital Logistics & Traceability Manager
This specialization involves managing the digital flow of information from log harvesting through the sorting process to final distribution. It includes implementing and maintaining digital tracking systems, ensuring data integrity, and using analytics to improve workflow efficiency and traceability. This role is critical for supply chain transparency and optimizing operational logistics within a digitized forestry industry.
Pros & Cons of Being a Log Sorter
Choosing a career path requires a clear understanding of both its appealing aspects and its inherent difficulties. For log sorters, daily experiences can vary greatly depending on the specific mill, logging operation, or geographic location. The advantages and challenges might also shift as an individual gains more experience or moves into different roles within the timber industry. What one person finds rewarding, another might find challenging, largely based on personal preferences, physical aptitude, and career aspirations. This assessment aims to provide a realistic overview of the log sorter profession, helping prospective workers set appropriate expectations for this demanding but essential role.
Pros
Log sorter positions are often in high demand, particularly in regions with active forestry and timber industries, offering relatively stable employment opportunities.
This role provides an excellent opportunity to work outdoors and engage in physical labor, which can appeal to individuals who prefer an active job over desk-bound work.
The job typically offers a clear sense of accomplishment, as you directly contribute to the initial processing of raw timber, seeing tangible results of your efforts daily.
Entry into this field often requires minimal formal education; many companies provide on-the-job training, making it accessible to a wide range of job seekers without extensive prior experience.
Log sorters often work as part of a team, fostering camaraderie and a sense of shared purpose among colleagues who face similar physical demands and environmental conditions.
There is often a straightforward path for advancement into roles like heavy equipment operator, quality control, or supervisory positions within the same logging or mill operation for motivated individuals.
Cons
Log sorters often work in outdoor environments, exposing them to various weather conditions like rain, snow, extreme heat, or cold, which can be physically demanding and uncomfortable.
The work involves repetitive physical tasks such as lifting, pushing, pulling, and bending, which can lead to musculoskeletal strain or injuries over time.
Working in a log yard or mill involves significant noise from machinery, heavy equipment, and falling logs, necessitating hearing protection and potentially contributing to long-term hearing issues.
There is a constant risk of accidents due to heavy machinery, unstable log piles, falling timber, and sharp objects, requiring high vigilance and strict adherence to safety protocols.
Entry-level wages for log sorters may be modest, and while there can be opportunities for slight increases with experience, the earning potential might be limited compared to other skilled trades.
Log sorters typically work fixed shifts, often including early mornings, late nights, or weekends, which can make it challenging to maintain a consistent social life or family schedule.
Frequently Asked Questions
Log Sorters face distinct challenges around physical demands, safety, and the seasonal nature of work. This section addresses common questions about entering this role, from training requirements to understanding daily tasks and career progression in the timber industry.
What are the basic educational or certification requirements to become a Log Sorter?
Entry into a Log Sorter role typically does not require a formal degree, but a high school diploma or GED is often preferred. Employers prioritize practical skills and a strong work ethic. Many learn through on-the-job training or apprenticeships, focusing on equipment operation, safety protocols, and timber grading. Certifications in heavy equipment operation, first aid, or specific log scaling techniques can significantly boost your prospects.
How long does it take to become job-ready as a Log Sorter if I'm starting without experience?
The timeline to become a proficient Log Sorter varies, but most entry-level positions offer on-the-job training that can last from a few weeks to several months. Within 6-12 months, new sorters can become competent in core tasks like identifying timber types, operating sorting equipment, and maintaining safety. Full expertise in grading and maximizing timber value takes longer, often 2-3 years of consistent experience.
What are the typical salary expectations for a Log Sorter, both entry-level and experienced?
Log Sorter salaries vary based on location, experience, and the specific company. Entry-level positions typically start around $30,000 to $40,000 annually. Experienced sorters with specialized skills or leadership responsibilities can earn $45,000 to $60,000 or more. Overtime pay is common due to seasonal demands, which can significantly increase overall earnings.
What is the typical work-life balance like, considering the physical demands and industry seasonality?
The work-life balance for a Log Sorter is often influenced by the timber industry's seasonal nature. During peak harvesting seasons, long hours, including weekends, are common due to production demands. Off-season periods may offer more regular hours or potential for layoffs, though many companies strive for consistent employment. The work is physically demanding, requiring good stamina and resilience.
Is the Log Sorter role a secure job in the long term, or is it at risk from automation or industry changes?
Job security for Log Sorters generally remains stable due to the continuous demand for timber products in construction, paper, and other industries. While economic downturns can affect demand, the need for skilled sorters to process raw materials persists. Automation is a factor, but human expertise is still critical for nuanced grading and equipment maintenance, providing a degree of job security.
What are the potential career advancement opportunities for a Log Sorter?
Career growth for a Log Sorter can lead to various specialized roles within the timber industry. Experienced sorters might advance to lead hand or supervisory positions, overseeing sorting crews and operations. Opportunities also exist in quality control, timber grading, or becoming a heavy equipment operator. Further training can open doors to roles in mill management or logistics within the supply chain.
What are the biggest challenges or specific difficulties unique to working as a Log Sorter?
The primary challenges in this role involve the physically demanding nature of the work, often outdoors in varying weather conditions. Safety is paramount, requiring constant vigilance around heavy machinery and moving logs. Additionally, accurately identifying and grading different timber species requires keen attention to detail and ongoing learning. Adapting to seasonal work fluctuations can also be a challenge.
Is remote work or location flexibility an option for Log Sorters?
Log Sorter positions are almost exclusively on-site, as the work involves direct handling and processing of timber at sawmills, log yards, or harvesting sites. Remote work is not an option for this hands-on role. Location flexibility is limited to areas with active timber harvesting and processing operations, which are typically rural or semi-rural rather than urban centers.
Related Careers
Explore similar roles that might align with your interests and skills:
Log Check Scaler
A growing field with similar skill requirements and career progression opportunities.
Explore career guideLog Cutter
A growing field with similar skill requirements and career progression opportunities.
Explore career guideLog Grader
A growing field with similar skill requirements and career progression opportunities.
Explore career guideLog Processor Operator
A growing field with similar skill requirements and career progression opportunities.
Explore career guideLog Stacker Operator
A growing field with similar skill requirements and career progression opportunities.
Explore career guideAssess your Log Sorter readiness
Understanding where you stand today is the first step toward your career goals. Our Career Coach helps identify skill gaps and create personalized plans.
Skills Gap Analysis
Get a detailed assessment of your current skills versus Log Sorter requirements. Our AI Career Coach identifies specific areas for improvement with personalized recommendations.
See your skills gapCareer Readiness Assessment
Evaluate your overall readiness for Log Sorter roles with our AI Career Coach. Receive personalized recommendations for education, projects, and experience to boost your competitiveness.
Assess your readinessSimple pricing, powerful features
Upgrade to Himalayas Plus and turbocharge your job search.
Himalayas
Himalayas Plus
Himalayas Max
Find your dream job
Sign up now and join over 100,000 remote workers who receive personalized job alerts, curated job matches, and more for free!
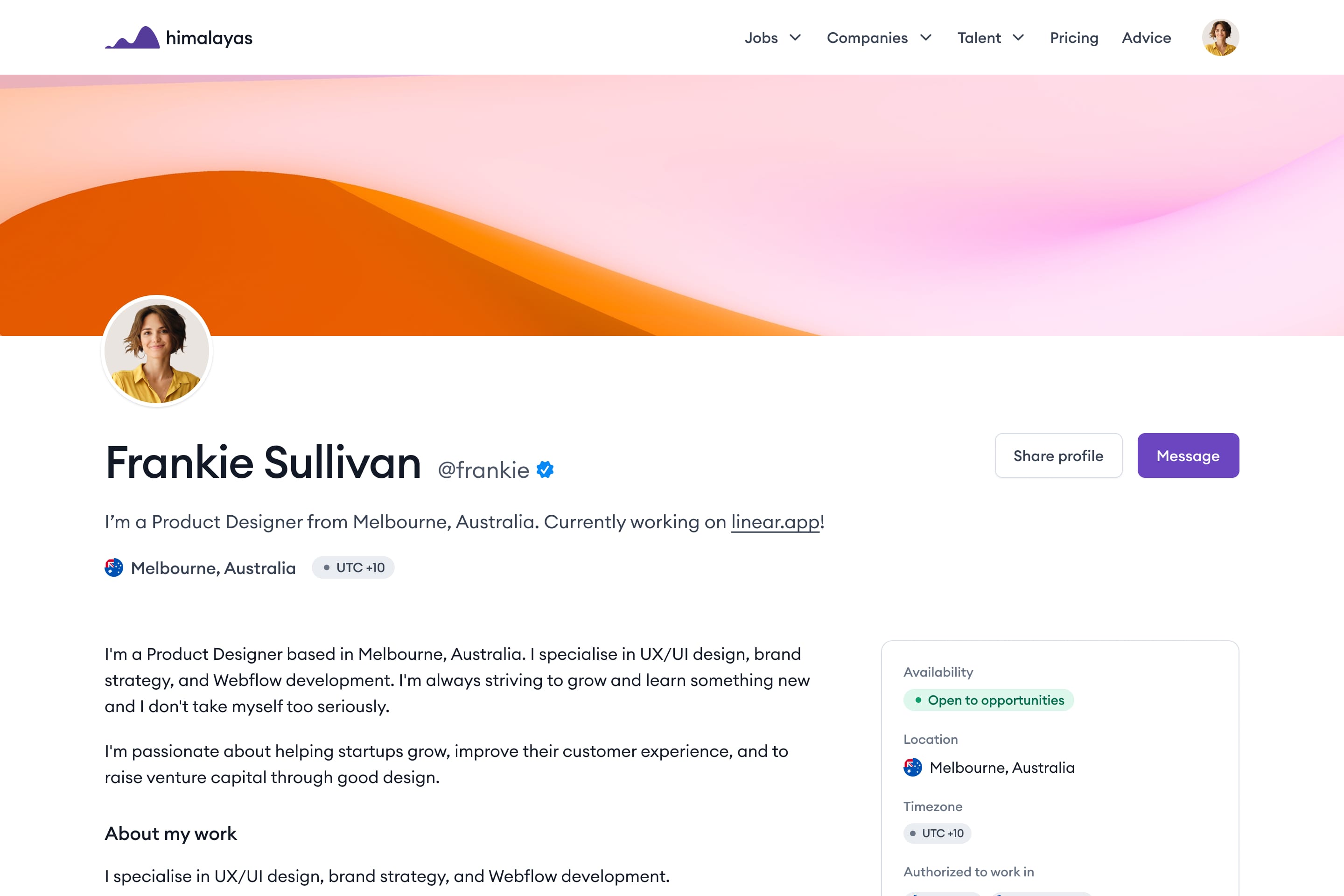