Complete Doffer Career Guide
Doffers play a crucial role in textile manufacturing, ensuring the continuous, efficient operation of spinning frames by replacing full bobbins with empty ones. This hands-on position is vital to maintaining production flow and quality, making you an essential part of the modern textile industry. It offers a direct entry point into manufacturing, providing tangible skills and a pathway within a foundational sector.
Key Facts & Statistics
Median Salary
$34,220 USD
(U.S. national median, BLS, May 2023)
Range: $28k - $45k+ USD (BLS, May 2023)
Growth Outlook
Annual Openings
≈1,300
openings annually (BLS, 2022-2032)
Top Industries
Typical Education
High school diploma or equivalent; on-the-job training
What is a Doffer?
A Doffer is a specialized production worker in textile manufacturing, primarily responsible for the rapid and efficient removal of full bobbins, cones, or packages of yarn from spinning, winding, or twisting machines. This role ensures the continuous operation of textile machinery by replacing full units with empty ones, preventing production bottlenecks. Doffers are crucial for maintaining the flow of material through the production line, directly impacting output volume.
This position differs from a general textile machine operator, who typically sets up, monitors, and adjusts the machines themselves. A Doffer's focus is almost exclusively on the physical process of changing out finished yarn products and preparing the machines for the next cycle, acting as the vital link between machine output and subsequent processing steps. They must work quickly and precisely to keep the high-speed machinery running without interruption.
What does a Doffer do?
Key Responsibilities
- Remove full bobbins or packages of yarn from spinning, winding, or twisting machines when they reach their specified capacity.
- Replace empty bobbins or tubes onto the spindles swiftly and accurately to ensure continuous machine operation.
- Inspect yarn for breaks, tangles, or quality issues during the doffing process and alert machine operators to problems.
- Transport full bobbins or packages to designated collection areas or subsequent processing stations, often using carts or specialized equipment.
- Clean machines and work areas regularly, including removing lint and waste, to maintain a safe and efficient production environment.
- Monitor machine performance during doffing and report any malfunctions or unusual noises to supervisors or maintenance staff.
Work Environment
Doffers typically work in textile mills or manufacturing plants, which are often loud due to the operating machinery and can be warm and humid. The environment usually has airborne lint and fibers, requiring good ventilation and sometimes respiratory protection. Work is physically demanding, involving repetitive movements, standing for long periods, bending, lifting, and pushing heavy carts. Collaboration with machine operators and supervisors is essential for coordinating doffing schedules and reporting issues. Shifts often run continuously, meaning doffers may work rotating shifts, including nights, weekends, and holidays. The pace of work is fast and continuous, directly tied to machine output.
Tools & Technologies
Doffers primarily work directly with textile machinery such as spinning frames, winding machines, and twisting machines. They use bobbins, tubes, and yarn packages as their primary materials. Essential tools include doffing carts or trolleys for transporting materials, and sometimes specialized lifters or hoists for heavier loads. They also use basic cleaning tools like brushes and air hoses to maintain machine cleanliness. While not highly technical, understanding machine indicators and basic troubleshooting for jams or breaks is crucial for efficient work. Safety equipment like gloves and ear protection are also standard.
Doffer Skills & Qualifications
Becoming a Doffer in a textile manufacturing environment involves a very specific set of skills and qualifications, primarily focused on manual dexterity, attention to detail, and physical endurance. This role is foundational to the production process, directly impacting efficiency and product quality. Unlike many modern roles, formal education plays a minimal role; practical experience and on-the-job training are paramount.
Requirements for a Doffer vary significantly by the type of textile mill and the specific machinery used. Larger, more automated facilities might prioritize individuals who can quickly learn machine interfaces and troubleshoot minor issues, while smaller, traditional mills focus more on speed and precision in manual operations. Seniority for a Doffer often translates to greater speed, fewer errors, and the ability to train new hires, rather than a shift to managerial duties.
Certifications or licenses are generally not required for Doffers. However, internal safety training and certifications related to machine operation and material handling are crucial. The skill landscape for Doffers has remained relatively stable over time, as the core function of removing full bobbins and replacing them with empty ones remains fundamental. However, an increasing emphasis on lean manufacturing principles means Doffers must also understand their role in overall production flow and waste reduction.
Education Requirements
Technical Skills
- Bobbin Handling Techniques: Proficient and quick removal of full bobbins and precise placement of empty bobbins.
- Yarn Threading: Accurately threading yarn through machine guides and onto bobbins.
- Machine Monitoring: Observing machinery for proper operation, identifying minor irregularities or potential faults.
- Quality Inspection (Basic): Recognizing and reporting yarn defects, tangles, or inconsistencies in winding.
- Safety Procedures: Strict adherence to lockout/tagout procedures and general machine safety guidelines.
- Material Handling: Safe and efficient transport of full and empty bobbins within the production area.
- Production Quota Adherence: Ability to meet daily or hourly doffing targets.
- Basic Machine Cleaning: Performing routine cleaning tasks on doffing mechanisms to prevent buildup and ensure smooth operation.
Soft Skills
- Attention to Detail: Essential for ensuring bobbins are correctly placed and removed, preventing tangles or production errors that can lead to costly downtime.
- Physical Stamina: The role requires standing for long periods, repetitive motions, and frequent lifting of bobbins, demanding good physical condition.
- Manual Dexterity: Critical for quickly and accurately handling bobbins, threading yarn, and performing tasks in a fast-paced environment.
- Time Management: Doffers must work efficiently to keep machines running, minimizing downtime between doffing cycles to maintain production quotas.
- Adherence to Safety Protocols: Strictly following safety procedures is vital to prevent accidents involving fast-moving machinery and heavy loads.
- Team Collaboration: Working effectively with other Doffers and machine operators ensures a smooth workflow across the production line.
- Problem-Solving (Basic): The ability to identify and report minor issues like yarn breaks or machine malfunctions quickly to prevent larger problems.
How to Become a Doffer
Entering the Doffer role primarily involves practical, on-the-job training rather than extensive formal education. Many individuals secure these positions by directly applying to textile mills, yarn manufacturing plants, or carpet factories. While some employers might prefer candidates with a high school diploma or equivalent, this is not always a strict requirement, especially for entry-level positions in regions with high demand for manufacturing labor.
The timeline for becoming a Doffer is relatively short, often ranging from a few days to a couple of weeks of initial training. This differs significantly from roles requiring advanced degrees or certifications. Entry strategies vary by company size; larger corporations might have more structured training programs, while smaller operations may offer more direct, hands-on learning from experienced colleagues. Geographic location also influences opportunities, with most Doffer positions concentrated in areas with a strong textile or manufacturing industry presence.
Common misconceptions include believing that Doffer roles require complex technical skills or prior manufacturing experience. In reality, most of the necessary skills are learned on the job. Networking within local manufacturing communities or even visiting plant open houses can be more beneficial than traditional job fairs. Success in this field relies on reliability, attention to detail, and a willingness to learn repetitive tasks quickly.
Step 1
Step 2
Step 3
Step 4
Step 5
Education & Training Needed to Become a Doffer
The Doffer role, primarily found in textile manufacturing, focuses on removing full bobbins or packages of yarn from spinning or winding machines and replacing them with empty ones. This role typically requires strong manual dexterity, attention to detail, and the ability to work in a fast-paced environment. Formal academic degrees are not generally a prerequisite for becoming a Doffer.
Instead, the educational landscape for Doffers heavily emphasizes on-the-job training and vocational programs. Many textile manufacturers provide in-house training programs that can last from a few days to several weeks, covering machine operation, safety protocols, and quality control. Some community colleges or vocational schools in textile-producing regions may offer short courses or certifications in textile production, which can be beneficial but are not universally required. These programs typically range from 12-24 weeks and cost between $1,000-$5,000. Self-study is not a primary path for this role, as practical, hands-on experience with machinery is essential.
Employers highly value practical experience and a demonstrated ability to perform tasks efficiently and safely. While a high school diploma or GED is often preferred, some entry-level positions may not even require it. Continuous learning in this field primarily involves staying updated on new machinery and production techniques through ongoing training provided by employers. The return on investment for formal education for a Doffer is low, as the direct impact on earning potential for this specific role is minimal. The focus should be on acquiring practical skills and demonstrating reliability.
Doffer Salary & Outlook
Compensation for a Doffer is primarily influenced by the specific textile mill, geographic location, and years of experience. Mills in regions with higher costs of living or specialized production often offer slightly better wages. While base salary forms the core, some facilities may provide performance incentives for efficiency or safety. Total compensation typically includes standard benefits like health insurance, retirement contributions, and paid time off.
Experience plays a direct role in earning potential, with long-tenured Doffers commanding higher hourly rates. Specialized skills, such as operating specific types of machinery or handling delicate fibers, can also increase value. Remote work is not applicable for this hands-on role. Salary figures presented here are based on the US market, acknowledging that international textile industries have varying pay scales.
Salary by Experience Level
Level | US Median | US Average |
---|---|---|
Doffer | $30k USD | $32k USD |
Market Commentary
The job market for Doffers faces significant shifts due to automation and global manufacturing trends. Demand for Doffers in the US has steadily declined as textile production moves overseas and mills adopt more automated machinery. This trend reduces the need for manual labor in tasks like doffing.
While some domestic mills continue to operate, especially those producing specialized textiles or military uniforms, job growth projections for Doffers are negative. Emerging opportunities within the textile industry lean towards roles in automation maintenance, quality control, or advanced material science, rather than traditional production roles. The supply of labor for these roles often exceeds demand in many regions.
Future-proofing in this profession involves acquiring skills in machine operation, maintenance, or other aspects of modern textile manufacturing. The role is susceptible to further automation, making it less recession-resistant compared to highly skilled technical trades. Geographic hotspots for Doffers are limited to existing textile manufacturing regions, primarily in the Southeast US, but even there, job availability is contracting.
Doffer Career Path
Career progression for a Doffer primarily involves gaining proficiency and demonstrating reliability within textile manufacturing. Advancement often means moving from a junior role to a more experienced Doffer, or specializing in specific machine types. Performance and consistent adherence to safety protocols are key factors influencing advancement speed.
The Doffer role is typically an individual contributor (IC) track position. There is limited formal upward mobility within the Doffer title itself. Instead, progression often involves becoming a lead Doffer, a trainer for new doffers, or transitioning into related textile machine operation or maintenance roles. Lateral movement might involve working with different fiber types or machinery within the mill.
Company size and specific mill operations influence career paths. Larger mills might offer more opportunities for specialization or cross-training on various machines. Continuous learning, especially regarding new machinery or automated doffing systems, is crucial. Networking within the mill and demonstrating a strong work ethic helps doffers become candidates for more responsible roles or machine operator positions when they become available.
Doffer
0-3 yearsKey Focus Areas
Doffer
0-3 yearsA Doffer is responsible for removing full bobbins or packages of yarn from textile machines and replacing them with empty ones. This role requires precision to prevent yarn breaks and maintain production flow. Doffers work under direct supervision, following established protocols for machine operation and material handling.
Key Focus Areas
Develop a strong understanding of different yarn types and their handling requirements. Focus on improving speed and efficiency in doffing while maintaining quality. Learn basic machine troubleshooting for common doffing issues. Prioritize adherence to all safety regulations and mill procedures.
Job Application Toolkit
Ace your application with our purpose-built resources:
Global Doffer Opportunities
The doffer role, primarily found in textile manufacturing, involves replacing bobbins or spindles on spinning frames. This profession has a global presence, especially in countries with robust textile industries like China, India, Vietnam, and Turkey. While demand for doffers remains steady in these regions, automation increasingly impacts the role in more developed economies. Cultural and regulatory differences affect labor practices and workplace safety standards across countries.
Doffers might consider international opportunities to access better working conditions, higher wages, or more advanced manufacturing environments. No specific international certifications exist for doffers; on-the-job training and experience are paramount for global mobility.
Global Salaries
Doffer salaries vary significantly based on the country's economic development and textile industry scale. In North America, specifically the United States, doffers earn approximately $25,000 to $35,000 USD annually. This range reflects higher labor costs and often more automated facilities.
In Europe, particularly in countries like Turkey or Portugal with strong textile sectors, doffers can expect to earn between €10,000 and €18,000 annually (approximately $11,000 to $20,000 USD). Western European countries with limited textile production offer fewer opportunities at similar or slightly higher rates.
Asia-Pacific, including major textile hubs like India and Bangladesh, offers lower salary ranges, typically between $3,000 and $7,000 USD per year (250,000 to 580,000 INR in India, or 250,000 to 580,000 BDT in Bangladesh). While these figures seem low, they align with the significantly lower cost of living and purchasing power parity in these nations. For instance, a doffer's salary in India allows for a comparable local lifestyle to a doffer's salary in the US, considering local expenses.
Salary structures also differ internationally. European countries often include more comprehensive healthcare and longer paid vacation as standard benefits. In contrast, benefits might be less extensive in some Asian countries. Tax implications vary widely; some countries have higher income taxes but offer more public services, affecting take-home pay. Experience and education primarily impact compensation within a specific country's pay scale, as international transferability of doffer skills does not typically lead to a higher pay grade without a change in role.
Remote Work
The doffer role, by its very nature, requires physical presence in a textile manufacturing facility. Doffing involves hands-on operation of machinery and direct interaction with textile production lines. Therefore, international remote work opportunities for doffers are non-existent.
The possibility of digital nomad lifestyles or working from a different country while performing doffer duties is not applicable. Employers in this field do not offer global hiring for remote doffer positions because the core functions cannot be performed remotely. Salary expectations are tied to the physical location of the textile plant.
Any considerations for equipment, internet requirements, or workspace setup for remote work do not apply to this profession. The role remains strictly on-site, tied to the specific factory's operational needs and machinery.
Visa & Immigration
Doffers considering international work primarily fall under skilled worker visa categories in many countries, though the specific classification can vary. Popular destination countries for textile workers include Vietnam, Bangladesh, and Turkey, which have significant textile industries. Requirements typically involve a job offer from an employer in the destination country.
Education credential recognition is generally not a major hurdle for doffers, as the role emphasizes practical skills and on-the-job training rather than formal academic qualifications. Professional licensing is not required for doffers.
Visa timelines and application processes vary by country, often taking several weeks to a few months. Employers usually assist with the visa application process. Pathways to permanent residency for doffers are limited and often depend on long-term employment and specific country policies on low-skilled labor immigration. Language requirements are typically minimal for this role, focusing on basic communication for workplace safety and instructions.
There are no profession-specific fast-track immigration programs for doffers. Practical considerations include securing housing near the factory and understanding local transportation. Family visas might be available for dependents, subject to the primary applicant's visa type and the destination country's regulations.
2025 Market Reality for Doffers
Understanding the current market realities for a doffer is crucial for career planning. This role, traditionally central to textile production, faces significant transformation. Market conditions have evolved rapidly, particularly between 2023 and 2025.
Post-pandemic shifts accelerated automation adoption in manufacturing. The ongoing AI revolution further impacts operational efficiency, influencing the need for manual labor. Broader economic factors like global supply chain shifts and consumer demand for textiles directly shape job availability. Market realities for doffers vary significantly by the level of mill modernization, geographic location, and the specific type of textile produced. This analysis provides an honest assessment of these dynamics.
Current Challenges
Doffers face significant challenges from automation. Many textile mills are investing in robotic doffing systems, directly reducing the need for manual labor. This trend leads to fewer entry-level positions and increased competition for remaining roles.
Economic fluctuations also impact demand. A downturn in consumer spending on textiles can slow production, leading to hiring freezes or layoffs in mills. Additionally, the physically demanding nature of the job, coupled with shift work, contributes to higher turnover but not necessarily more openings due to automation.
Growth Opportunities
Despite automation, niche opportunities for doffers exist in specialized textile production. This includes mills producing custom fabrics, high-performance textiles, or artisan goods where full automation is not yet cost-effective or practical. These roles often require a keen eye for detail and quality control.
Doffers can position themselves advantageously by acquiring basic machine operation and maintenance skills. Understanding automated doffing systems, even at a supervisory level, creates new pathways. Mills value individuals who can assist with setup, monitoring, and minor repairs of robotic equipment, transitioning from manual labor to machine support roles.
Underserved markets might include smaller, independent mills or those focusing on unique, high-value products. These companies may not have the capital for full automation, retaining a need for skilled manual doffers. Strategic career moves involve seeking out roles in such specialized segments or pursuing training in textile machinery operation and maintenance, aligning with the industry's technological shift.
Current Market Trends
The demand for doffers in textile manufacturing continues its decline as of 2025. Modern textile mills prioritize automation to enhance efficiency and reduce labor costs. This shift means fewer manual doffing positions are available, particularly in developed economies.
Generative AI and advanced robotics influence this trend. AI-driven systems optimize production lines, making automated doffing more precise and reliable. Employers seek candidates with a basic understanding of machinery operation and troubleshooting, moving away from purely manual labor requirements. Wage growth for doffers remains stagnant or declines in real terms due to reduced demand and a surplus of available labor.
Geographically, doffing opportunities concentrate in regions with older textile infrastructure or specialized, low-volume production. Remote work is not applicable to this role. Seasonal patterns might exist in some niche textile segments, but overall, the trend points towards consolidation and reduced hiring for manual doffing roles.
Emerging Specializations
The manufacturing landscape continually evolves, driven by rapid technological advancements and shifting industry demands. For a Doffer, understanding these changes is crucial for career progression. New specialization opportunities arise from the integration of automation, advanced materials, and data analytics into textile production.
Positioning oneself early in these emerging areas provides a significant advantage for career advancement beyond 2025. Early adopters often become subject matter experts, commanding premium compensation and experiencing accelerated career growth. While established specializations offer stability, embracing emerging areas unlocks next-generation opportunities.
Most emerging specializations take time to become mainstream, often requiring 3-5 years to develop into areas with significant job opportunities. This timeline allows professionals to acquire necessary skills and gain early experience. Pursuing cutting-edge areas involves a balance of risk and reward; while initial demand might be niche, the long-term potential for impact and leadership is substantial.
Strategic choices about specialization allow Doffers to remain relevant and indispensable in an increasingly automated and data-driven manufacturing environment. These opportunities are not merely about adapting to change but about actively shaping the future of textile production.
Automated Doffing System Monitor
As textile mills integrate more robotics and automated guided vehicles (AGVs) for material handling and doffing operations, a Doffer specializing in automation oversight becomes essential. This role involves monitoring automated systems, troubleshooting minor malfunctions, and ensuring seamless integration with manual processes. It moves beyond physical doffing to managing the automated workflow, ensuring efficiency and minimizing downtime.
Advanced Material Quality Doffer
The rise of advanced textiles, including smart fabrics and technical fibers, requires specialized handling and quality control. A Doffer specializing in advanced material handling understands the unique properties of these new materials, such as conductivity or specific tensile strengths. This specialization focuses on precise doffing and packaging to preserve material integrity, ensuring that high-value yarns meet stringent quality specifications for downstream applications like wearable tech or medical textiles.
Production Data Analyst (Doffing Focus)
Data analytics increasingly informs every aspect of manufacturing. A Doffer specializing in production data entry and analysis collects and inputs critical doffing cycle times, machine performance metrics, and yarn quality data. They help identify trends, bottlenecks, and areas for improvement directly impacting operational efficiency and waste reduction. This role is pivotal in transforming raw operational data into actionable insights for production managers.
Sustainable Yarn Flow Specialist
Sustainability is a core focus across industries, including textiles. A Doffer specializing in sustainable material flow management understands the lifecycle of raw materials and yarns, focusing on minimizing waste and optimizing resource usage during doffing. This involves implementing practices that reduce material damage, ensure proper segregation for recycling, and contribute to the mill's overall environmental goals. They play a direct role in reducing the carbon footprint of textile production.
Predictive Maintenance Assistant (Doffing Equipment)
The advent of predictive maintenance in textile machinery requires Doffers to play an active role in sensing and reporting potential equipment issues before they cause downtime. A Doffer specializing in sensor-based predictive maintenance identifies unusual machine vibrations, temperature changes, or yarn irregularities indicated by embedded sensors on doffing equipment. They contribute to a proactive maintenance strategy, reducing costly breakdowns and extending machine lifespan.
Pros & Cons of Being a Doffer
Understanding both the advantages and challenges of a career is crucial before making a commitment. Career experiences vary significantly by company culture, industry sector, specific specialization, and individual preferences. The pros and cons of a doffer role may also shift at different career stages, with early experiences focusing on skill acquisition and later stages on efficiency or minor supervisory tasks. What one person considers an advantage, like a predictable routine, another might see as a challenge, such as monotony. This assessment provides an honest, balanced view to help set realistic expectations for anyone considering this type of manufacturing position.
Pros
- The role requires minimal formal education or prior experience, making it an accessible entry point into the manufacturing sector for individuals seeking immediate employment.
- Doffers often find consistent work schedules, with shifts typically set for extended periods, providing a predictable routine and stable income.
- The job involves clear, repetitive tasks that are easy to learn, allowing new employees to quickly become proficient and contribute effectively to the production line.
- Many manufacturing facilities offer on-the-job training for doffers, providing a practical way to learn the necessary skills without incurring educational debt.
- Working as a doffer provides a tangible sense of contribution to the production process, as you directly handle and prepare materials for the next stage of manufacturing.
- The physical nature of the work can be beneficial for individuals who prefer an active job over sedentary office roles, helping to maintain physical fitness during the workday.
- Some manufacturing plants offer opportunities for doffers to cross-train in other basic production roles, potentially broadening their skill set and making them more versatile within the facility.
Cons
- Doffers often work in noisy environments due to machinery, which can lead to hearing fatigue and long-term hearing damage if proper protection is not consistently used.
- The role is physically demanding, requiring constant standing, walking, lifting, and repetitive motions, which can lead to musculoskeletal issues over time.
- Work schedules for doffers frequently involve shift work, including nights, weekends, and holidays, making it challenging to maintain a consistent social life or family routine.
- The job typically offers limited opportunities for career advancement within the manufacturing plant, with few clear pathways to higher-skilled or supervisory roles without further education or training.
- Doffers face exposure to dust, fibers, and airborne particles, which can aggravate respiratory conditions or lead to new ones if ventilation is inadequate or personal protective equipment is not worn.
- The work is highly repetitive and monotonous, involving the same tasks repeatedly throughout a shift, which can lead to boredom and reduced job satisfaction for some individuals.
- Entry-level doffer positions generally offer lower wages compared to more skilled manufacturing roles, and wage progression may be slow without acquiring additional certifications or responsibilities within the plant.
Frequently Asked Questions
Doffers play a crucial role in textile manufacturing, directly impacting production efficiency and quality. Many prospective doffers wonder about the physical demands, the required skills, and the career progression within a factory setting. This FAQ addresses common concerns about entering and succeeding in this specific hands-on role.
What qualifications or experience do I need to become a doffer?
Most doffer positions do not require specific formal education beyond a high school diploma or equivalent. Employers prioritize physical stamina, attention to detail, and the ability to follow instructions. Many factories provide on-the-job training, allowing new doffers to learn the necessary skills directly on the production floor. Previous experience in a manufacturing or physically demanding role can be beneficial but is not always required.
How physically demanding is the doffer job, and what is the typical work environment like?
A doffer's work involves repetitive tasks and can be physically demanding. You will stand for long periods, lift and carry full bobbins, and move quickly between machines. The environment can be noisy and warm due to machinery. While challenging, individuals with good physical condition and a strong work ethic adapt well to the demands. Safety protocols are always in place to minimize risks.
What are the typical salary expectations and benefits for a doffer?
Entry-level doffer salaries vary by region and company, but they generally reflect hourly wages for production roles. Most positions offer competitive benefits, including health insurance and retirement plans. Opportunities for overtime are often available, which can significantly increase earning potential. As you gain experience and demonstrate reliability, there may be opportunities for pay increases.
What is the typical work schedule and how does it affect work-life balance?
The work schedule for a doffer often involves shift work, including nights, weekends, and holidays, as textile factories operate continuously. This schedule allows for consistent production but requires adaptability. While the work is continuous, doffers typically have scheduled breaks and meal times. The consistent nature of the work means a predictable routine, but it might impact social life depending on the shift.
Are there opportunities for career advancement or growth from a doffer position?
While doffer is an entry-level role, it can be a stepping stone within a textile manufacturing plant. With experience and a good performance record, doffers can advance to positions like machine operator, quality control technician, or even supervisory roles. Many companies offer internal training programs to help employees develop new skills and move up the career ladder. Demonstrating reliability and a willingness to learn new tasks is key to advancement.
Is the doffer role a secure job, or is it at risk from automation or industry changes?
The demand for doffers is tied to the health of the textile manufacturing industry. While some textile production has shifted overseas, domestic factories continue to operate, creating a steady need for skilled production workers. Automation can impact some roles, but the hands-on nature of doffing often requires human dexterity. Job security often depends on the specific company and its market position.
What are the most important skills a successful doffer needs to have?
A doffer needs to be highly detail-oriented to ensure bobbins are correctly replaced and machines run efficiently. Speed and efficiency are also crucial, as production lines depend on quick changeovers. Additionally, good communication skills are important for coordinating with other team members and supervisors. The ability to work consistently and reliably in a fast-paced environment is also essential.
Related Careers
Explore similar roles that might align with your interests and skills:
Chain Offbearer
A growing field with similar skill requirements and career progression opportunities.
Explore career guideCotton Ginner
A growing field with similar skill requirements and career progression opportunities.
Explore career guideLoom Fixer
A growing field with similar skill requirements and career progression opportunities.
Explore career guideOffbearer
A growing field with similar skill requirements and career progression opportunities.
Explore career guideSpinning Doffer
A growing field with similar skill requirements and career progression opportunities.
Explore career guideAssess your Doffer readiness
Understanding where you stand today is the first step toward your career goals. Our Career Coach helps identify skill gaps and create personalized plans.
Skills Gap Analysis
Get a detailed assessment of your current skills versus Doffer requirements. Our AI Career Coach identifies specific areas for improvement with personalized recommendations.
See your skills gapCareer Readiness Assessment
Evaluate your overall readiness for Doffer roles with our AI Career Coach. Receive personalized recommendations for education, projects, and experience to boost your competitiveness.
Assess your readinessSimple pricing, powerful features
Upgrade to Himalayas Plus and turbocharge your job search.
Himalayas
Himalayas Plus
Himalayas Max
Find your dream job
Sign up now and join over 100,000 remote workers who receive personalized job alerts, curated job matches, and more for free!
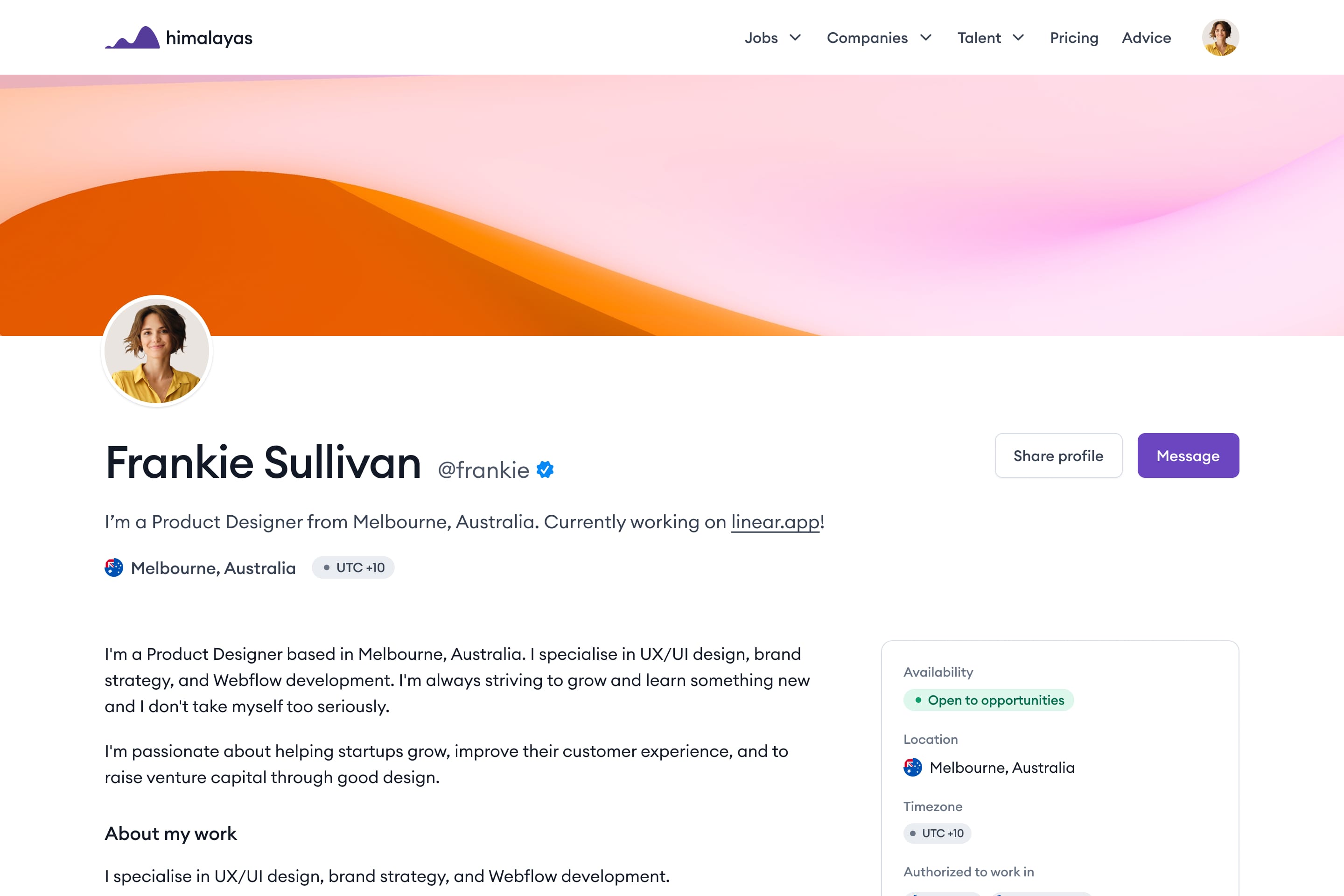